Can You Weld Cast Iron?
Cast iron is a material commonly found in various industries due to its strength, durability, and versatility. It’s used in everything from engine blocks to cookware. However, when it comes to repairing or modifying cast iron components, many people wonder, “Can you weld cast iron?” The answer isn’t always straightforward, as there are multiple factors to consider, including the type of cast iron, the method used, and the challenges involved in welding this material.
What is Cast Iron?
Cast iron is a group of iron-carbon alloys, typically containing 2-4% carbon, along with varying amounts of other elements like silicon. It’s known for its excellent castability, meaning it can be easily molded into complex shapes. Cast iron is typically divided into several categories:
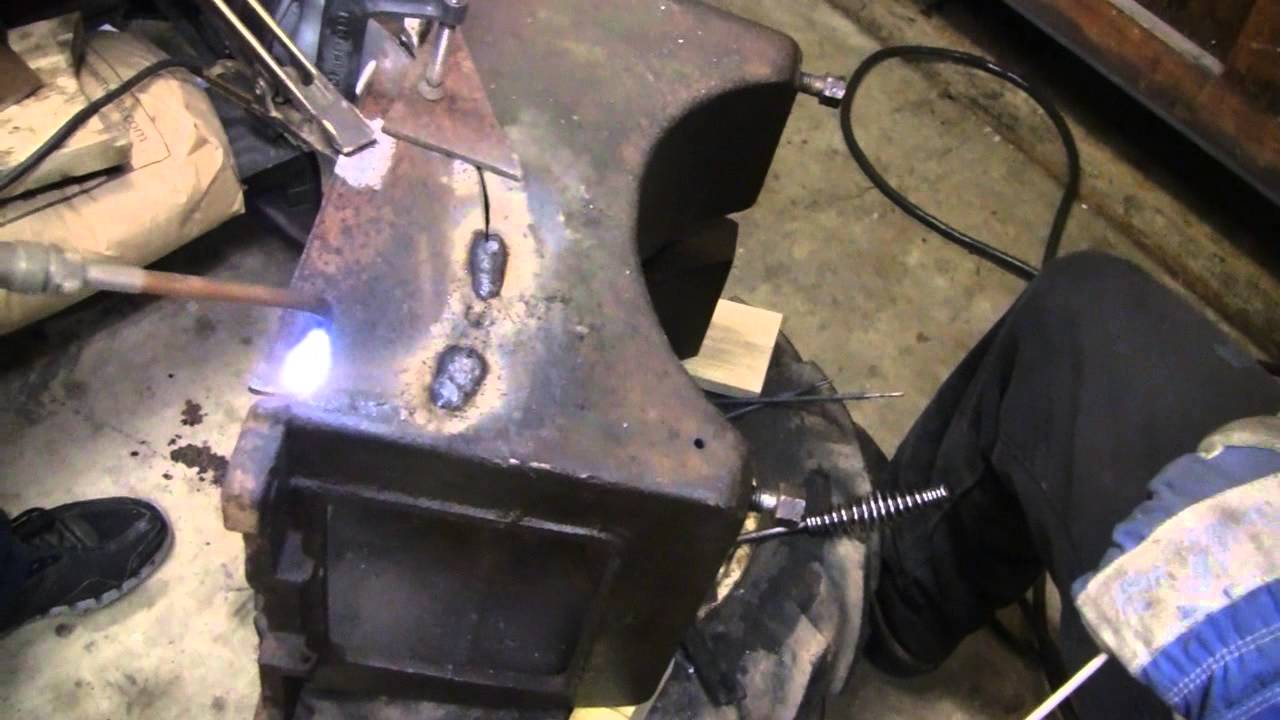
- Gray Cast Iron: Known for its excellent machinability, this is the most common type of cast iron.
- White Cast Iron: Hard and brittle, making it more challenging to weld.
- Malleable Cast Iron: A type of cast iron that’s been heat-treated to increase its ductility.
- Ductile Cast Iron: Stronger and more flexible than regular gray cast iron, making it easier to weld.
Each type of cast iron has unique characteristics that affect its weldability. Some are easier to weld than others, and understanding these differences is key to successful welding.
Can You Weld Cast Iron?
Yes, you can weld cast iron, but it’s not always a simple task. Cast iron is notoriously difficult to weld due to its brittleness, porosity, and tendency to crack. However, with the right technique, equipment, and preparation, welding cast iron can be done successfully.
The main challenges in welding cast iron come from its high carbon content and the fact that it doesn’t behave like more ductile metals such as steel. The welding process must be done carefully to avoid cracking or warping the material.
The Challenges of Welding Cast Iron
Welding cast iron isn’t as straightforward as welding other metals, mainly due to the following challenges:
- Brittleness: Cast iron is more brittle compared to steel, making it prone to cracking during the welding process.
- Porosity: Cast iron often has small holes or pores that can cause problems with the integrity of the weld.
- Thermal Expansion: Cast iron expands and contracts with heat in ways that can create stress in the weld area.
- Cracking: The thermal shock and cooling of cast iron can cause cracks, especially if the material is not properly preheated.
Types of Cast Iron That Can Be Welded
Different types of cast iron require different welding approaches. The main types of cast iron you may encounter include:
- Gray Cast Iron: This is the most common form of cast iron, and it is generally easier to weld compared to other types. It is softer and has better machinability.
- White Cast Iron: Due to its hardness and brittleness, white cast iron is much harder to weld. It often requires special techniques and preheating.
- Malleable Cast Iron: Malleable cast iron is more ductile, making it easier to weld compared to gray and white cast iron.
- Ductile Cast Iron: Ductile iron is also easier to weld, as it has better strength and flexibility.
Different Type of Cast Iron ?
Each type of cast iron has different characteristics:
- Gray Cast Iron: High carbon content and graphite flakes make it easy to machine but prone to cracking.
- White Cast Iron: Has a much higher brittleness due to its lack of graphite, making it the most challenging to weld.
- Malleable Cast Iron: With its heat-treated properties, this type is more ductile, making it better suited for welding.
- Ductile Cast Iron: Contains nodular graphite, which gives it more flexibility, making it more weld-friendly than other types.
Methods for Welding Cast Iron
Welding cast iron requires specialized methods. Some of the most common techniques include:
- Oxy-Acetylene Welding: Often used for repairing cast iron, this method involves using an oxy-acetylene torch to melt the filler rod and the base material.
- Stick Welding (MMA): Shielded Metal Arc Welding (SMAW) is another popular option for cast iron, particularly when dealing with thicker components.
- TIG Welding: Tungsten Inert Gas welding is a precise method for welding cast iron, particularly useful for thin sections.
- MIG Welding: While MIG welding is generally not recommended for cast iron, it can be used with the right settings and filler material.
- Induction Welding: A more modern technique where high-frequency current is used to heat the material and create a strong bond.
Right Welding Method for Cast Iron
Choosing the right welding method depends on several factors, including the type of cast iron, the thickness of the material, and the location of the crack or damage. Here’s a quick rundown:
- Oxy-Acetylene Welding: Best for repair work and thinner cast iron pieces.
- Stick Welding: Good for thicker parts, but requires high skill to avoid cracking.
- TIG Welding: Excellent for precision and thinner materials.
- MIG Welding: Can be used for cast iron but requires careful adjustments to prevent poor weld quality.
Preparation & Post-Welding
Before you start welding, you need to properly prepare the cast iron:
- Clean the Surface: Remove any oil, dirt, rust, and other contaminants.
- Preheat the Cast Iron: Preheating reduces thermal stress and prevents cracking during welding.
- Choose the Right Filler Material: Use a filler material that is compatible with the type of cast iron you are welding.
Why Preheating is Essential
Preheating the cast iron is one of the most critical steps in the welding process. By heating the material gradually before welding, you reduce the likelihood of cracking due to the rapid cooling of the material. Preheating helps to stabilize the temperature and ensure a smoother weld.
Post-Welding Considerations
After welding, cast iron needs to be treated carefully to prevent further cracking. Cooling the material slowly and stress-relieving it through heat treatment helps ensure the integrity of the weld.
How to Prevent Cracking After Welding
To avoid cracking, follow these tips:
- Cool Slowly: Allow the cast iron to cool slowly to prevent thermal shock.
- Use Stress-Relief Treatment: Apply heat treatment to relieve the stress caused by welding.
FAQs
Can I weld cast iron with a MIG welder?
While MIG welding can be used on cast iron, it’s generally not recommended due to the potential for weak welds. TIG or stick welding is often preferred.
Why is cast iron so hard to weld?
Cast iron is difficult to weld because of its high carbon content, which makes it brittle and prone to cracking.
Can I weld cast iron without preheating?
Preheating is recommended to reduce the risk of cracking and to ensure a successful weld.
What’s the best welding rod for cast iron?
The best welding rod depends on the type of cast iron. For gray cast iron, a nickel-based electrode is often recommended.
How do I fix a crack in cast iron?
Cracks in cast iron can be repaired through welding, but it’s important to choose the right welding method, preheat the material, and use the correct filler material.
Conclusion
Welding cast iron is possible, but it comes with a unique set of challenges. Understanding the type of cast iron you are working with, choosing the right welding method, and properly preparing the material are crucial steps to ensure a successful weld. By taking the time to follow these steps, you can effectively repair or modify cast iron components, making it a valuable skill in various industries.