Controlling Warpage in Welding of Sheet Metal
Introduction
Welding is a critical process in the fabrication of sheet metal structures. However, one of the most significant challenges faced by welders and engineers is controlling warpage. Warpage occurs due to the uneven heating and cooling of the metal, leading to distortions that can affect the quality and precision of the final product. This article delves into the various techniques and best practices for controlling warpage in the welding of sheet metal, ensuring high-quality results.
Understanding Warpage in Welding
Warpage in welding primarily results from the thermal expansion and contraction of the metal. When the metal is heated, it expands, and as it cools, it contracts. Uneven heating causes differential expansion and contraction, leading to distortions. The degree of warpage depends on several factors, including the type of metal, thickness of the sheet, welding technique, and the amount of heat applied.
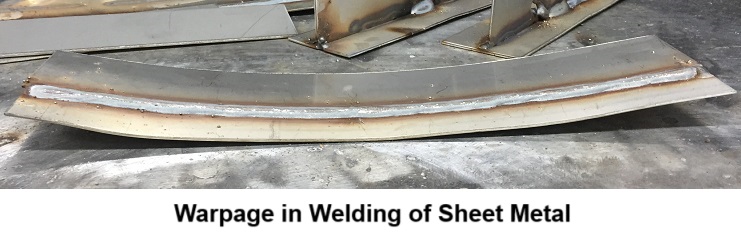
Types of Warpage
There are various types of warpage, such as:
- Longitudinal Warpage: Bending along the length of the weld.
- Transverse Warpage: Bending across the weld.
- Angular Warpage: Formation of angles between different parts of the weld.
- Bowing and Buckling: Overall distortion of the sheet metal.
Factors Affecting Warpage
- Material Type: Different metals have varying thermal expansion coefficients. For instance, aluminum expands more than steel when heated, making it more prone to warpage.
- Sheet Thickness: Thinner sheets are more susceptible to warpage compared to thicker ones due to their lower resistance to thermal expansion and contraction.
- Welding Technique: The choice of welding technique, such as MIG, TIG, or spot welding, significantly impacts the extent of warpage.
- Heat Input: The amount of heat applied during welding plays a crucial role. Excessive heat can cause severe warpage, while insufficient heat may result in weak welds.
Techniques to Control Warpage
Preheating the Metal
Preheating the metal before welding helps in reducing the temperature differential between the welding arc and the surrounding metal. This process minimizes the thermal gradient, leading to reduced warpage. Preheating is especially useful for thicker sheets and high-carbon steels.
Proper Clamping and Fixturing
Using clamps and fixtures to hold the sheet metal in place during welding helps in maintaining the alignment and reducing distortions. Proper clamping ensures even distribution of heat and prevents the metal from moving or warping excessively.
Backstepping Technique
The backstepping technique involves welding in short, staggered steps rather than a continuous line. This method allows the metal to cool slightly between welds, reducing the buildup of excessive heat and minimizing warpage.
Intermittent Welding
Intermittent welding, also known as skip welding, involves welding short sections at intervals along the seam. This technique reduces the amount of heat concentrated in one area, thereby decreasing the likelihood of warpage.
Controlled Cooling
Controlling the cooling rate after welding is crucial in preventing warpage. Slow cooling allows the metal to contract uniformly, reducing the risk of distortions. This can be achieved by using insulation blankets or gradually reducing the heat input.
Best Practices for Minimizing Warpage
Optimize Welding Parameters
Setting the correct welding parameters, such as current, voltage, and travel speed, is essential in controlling warpage. Optimal parameters ensure consistent heat input and reduce the chances of excessive thermal expansion and contraction.
Use of Chill Bars
Chill bars, also known as heat sinks, are metal bars placed adjacent to the weld area. They absorb excess heat during welding, preventing overheating and subsequent warpage. Chill bars are particularly effective for welding thin sheets and aluminum alloys.
Symmetrical Welding
Symmetrical welding involves welding from the center outwards or from alternating sides. This approach balances the heat distribution and minimizes the distortion caused by differential thermal expansion.
Proper Joint Design
Designing joints with minimal gaps and proper fit-up reduces the need for excessive heat input. Well-designed joints ensure even distribution of stress and reduce the risk of warpage.
Post-Weld Treatments
Post-weld treatments, such as stress-relief annealing or heat treatment, help in reducing residual stresses and warpage. These treatments allow the metal to relax and return to its original shape, improving the overall quality of the weld.
Advanced Techniques for Warpage Control
Laser Welding
Laser welding is a precision welding technique that uses a focused laser beam to weld metals. The high energy density of the laser allows for precise control of the heat input, reducing the risk of warpage. Laser welding is ideal for thin sheets and high-precision applications.
Electron Beam Welding
Electron beam welding (EBW) is another advanced technique that uses a beam of high-velocity electrons to weld metals. EBW provides excellent control over the heat input, resulting in minimal warpage. It is suitable for welding thick sections and complex geometries.
Friction Stir Welding
Friction stir welding (FSW) is a solid-state welding process that joins metals without melting them. FSW generates heat through friction, resulting in minimal thermal distortion and warpage. This technique is particularly effective for aluminum and other non-ferrous metals.
FAQs
How does warpage affect the strength of the weld?
Warpage can weaken the weld by introducing residual stresses and causing misalignment, which can compromise the structural integrity of the welded assembly.
Can warpage be completely eliminated?
While it is challenging to eliminate warpage entirely, it can be significantly minimized through careful planning, proper techniques, and advanced equipment.
What are the best materials to minimize warpage?
Materials with low thermal expansion coefficients and high thermal conductivity, such as aluminum and stainless steel, are less prone to warpage.
How can I measure warpage accurately?
Accurate measurement tools like laser scanners, dial indicators, and 3D measurement systems can help detect and quantify warpage precisely.
Are there any software tools to predict warpage?
Yes, several software tools, such as finite element analysis (FEA) programs, can simulate the welding process and predict potential warpage, helping in planning and mitigating distortion.
Conclusion
Controlling warpage in the welding of sheet metal is a critical aspect of ensuring high-quality and precise welds. By understanding the factors that contribute to warpage and implementing the techniques and best practices discussed in this article, welders and engineers can significantly reduce distortions and achieve superior results. From preheating and proper clamping to advanced techniques like laser welding, there are various methods available to control warpage and improve the overall quality of welded structures.