Differences Between Water-tube and Fire-tube Boilers
Introduction
Boilers are central to energy generation and industrial heating processes, and understanding their design is critical for optimal performance. For a boiler engineer, the distinctions between water-tube and fire-tube boilers go beyond basic operation—they influence efficiency, safety, and application suitability. Let’s explore their differences in detail.
What Are Boilers and Why Are They Important?
Boilers are closed vessels where water is heated to generate steam or hot water, serving as a fundamental component of heating systems and power generation. In industries, they are the backbone of operations, converting chemical or fossil energy into thermal energy, which then drives mechanical processes. Whether it’s a refinery or a textile plant, boilers are indispensable.
Overview of Water-tube and Fire-tube Boilers
The primary distinction between water-tube and fire-tube boilers lies in their structure:
- In water-tube boilers, water circulates within the tubes, while hot gases flow around them.
- In fire-tube boilers, hot gases pass through tubes submerged in water.
This fundamental difference dictates their performance, efficiency, and application.
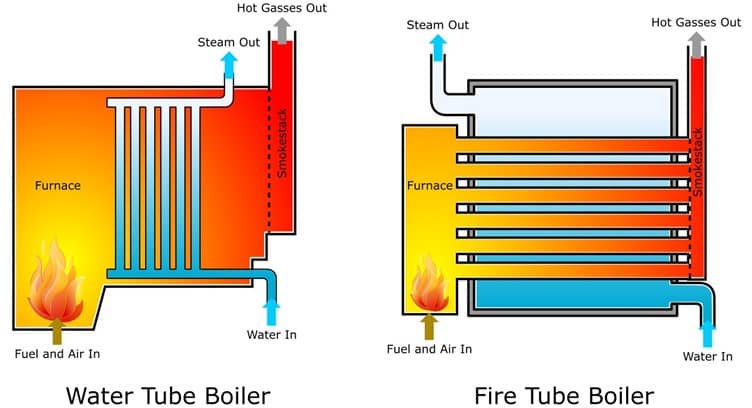
Basics of Boiler Operation
The Role of Boilers in Industries
In industrial environments, boilers are used for:
- Power generation: Producing steam for turbines.
- Process heating: Supplying consistent heat for manufacturing processes like distillation or drying.
- Comfort heating: Providing hot water or steam for building HVAC systems.
Each application demands specific characteristics, and the choice of boiler type directly impacts operational efficiency.
How Water-tube Boilers Work
Water-tube boilers are designed for high-pressure applications. Water is pumped through narrow tubes exposed to high-temperature gases. The heat causes the water to quickly convert to steam. These boilers are capable of generating steam at very high pressures (above 2,000 psi) and temperatures (up to 650°C), making them ideal for power plants and large-scale industrial operations.
- Circulation: Water circulates naturally or via pumps in the tubes, ensuring high heat transfer rates.
- Heat Source: Combustion occurs in a furnace, and the heat is transferred to water via radiant and convective mechanisms.
- Steam Quality: The rapid heating produces superheated steam, essential for high-efficiency turbine operations.
How Fire-tube Boilers Work
Fire-tube boilers are simpler in design, making them suitable for low to medium-pressure applications. Hot gases generated by combustion pass through tubes surrounded by water. Heat transfer occurs as the hot gases lose energy to the water, turning it into steam.
- Heat Pathway: The gases make multiple passes through the tubes, increasing heat transfer efficiency.
- Pressure Levels: Operating pressure rarely exceeds 250 psi, limiting their use in high-demand settings.
- Applications: Fire-tube boilers are prevalent in smaller plants, schools, and commercial heating systems.
Key Differences
Structural Design
Tube Arrangement
Water-tube boilers feature an intricate arrangement of narrow tubes, increasing the surface area for heat transfer. In contrast, fire-tube boilers use fewer, larger tubes, which simplifies their design but limits heat transfer efficiency.
Material Used
Water-tube boilers are built with high-strength materials such as steel alloys, designed to endure extreme pressure and temperature. Fire-tube boilers use less advanced materials, making them cost-effective but less durable under high-stress conditions.
Heat Transfer Process
The heat transfer efficiency of water-tube boilers is superior due to their large heat exchange area. Additionally, their design minimizes thermal resistance, allowing for quicker steam generation. Fire-tube boilers, while efficient for small-scale applications, experience slower heat transfer due to their lower surface area.
Efficiency and Performance
Water-tube boilers outperform fire-tube boilers in:
- Efficiency: Higher heat transfer rates result in less fuel consumption.
- Steam Generation: Faster startup times and the ability to maintain higher steam quality.
Fire-tube boilers, while less efficient, are reliable and better suited for steady, low-pressure applications.
Applications of Each Boiler Type
Industries That Prefer Water-tube Boilers
Water-tube boilers dominate industries requiring high-capacity steam:
- Power Plants: For electricity generation via steam turbines.
- Chemical Plants: Where precise temperature and pressure control are essential.
- Petrochemical Refineries: Supporting large-scale distillation processes.
Fire-tube Boilers in Everyday Applications
Fire-tube boilers find use in smaller, less demanding settings:
- Commercial Buildings: Heating systems for offices and schools.
- Food Processing: Steam generation for cooking and sterilization.
- Residential Applications: Domestic hot water production.
Pros and Cons of Water-tube Boilers
Advantages
- High Efficiency: Optimized for rapid heat transfer and minimal fuel waste.
- High Pressure and Temperature: Essential for critical industrial applications.
- Compact Design: Despite their complexity, water-tube boilers occupy less space per output unit.
Limitations
- Complex Construction: Requires skilled engineering and precision manufacturing.
- Maintenance Challenges: Routine inspections and repairs are more demanding due to intricate designs.
Pros and Cons of Fire-tube Boilers
Advantages
- Ease of Operation: Simple controls and less training required for operators.
- Cost-Effective: Lower initial costs make them attractive for small-scale use.
- Robust Design: Durable and reliable for steady, long-term use.
Limitations
- Lower Efficiency: Suboptimal for high-pressure and high-temperature requirements.
- Slower Steam Generation: Not suitable for processes demanding rapid response times.
Safety Considerations
Common Risks in Water-tube Boilers
- Tube Ruptures: Caused by thermal stresses or corrosion.
- Pressure Failures: Overpressurization leading to catastrophic failures.
Common Risks in Fire-tube Boilers
- Overheating: Resulting from insufficient water levels.
- Scaling: Reduces heat transfer and increases the risk of tube failure.
Preventive Measures and Maintenance
- Regular inspection of pressure and temperature controls.
- Water quality monitoring to prevent scaling and corrosion.
- Periodic cleaning of tubes to ensure optimal heat transfer.
Cost Comparison
Initial Costs
Water-tube boilers are significantly more expensive upfront due to their advanced materials and intricate design. Fire-tube boilers are budget-friendly for smaller operations.
Operating and Maintenance Costs
Water-tube boilers, while efficient, have higher maintenance costs due to their complexity. Fire-tube boilers are cheaper to operate but less efficient in the long term.
FAQs
What Is the Lifespan of Each Boiler Type?
Water-tube boilers often last over 25 years with proper maintenance, while fire-tube boilers average 15–20 years.
Which Boiler Type Is Easier to Maintain?
Fire-tube boilers are simpler and cheaper to maintain, making them a favorite in less technical environments.
Are Water-tube Boilers Safer Than Fire-tube Boilers?
Water-tube boilers handle high pressures better, making them safer in demanding industrial settings.
Which Boiler Is More Energy Efficient?
Water-tube boilers are generally more energy-efficient due to their superior heat transfer mechanisms.
Can Both Types Be Used for Domestic Purposes?
Fire-tube boilers are more suitable for domestic purposes, while water-tube boilers are designed for industrial-scale operations.
Conclusion
Choosing between a water-tube and fire-tube boiler depends on your specific operational needs. For high-pressure, large-scale applications, water-tube boilers offer unmatched efficiency and performance. On the other hand, fire-tube boilers provide reliability and cost-effectiveness for simpler heating needs.