Excessive Weld Reinforcement
Introduction
Welding is a crucial process in various industries, from construction to manufacturing. It involves joining metals together using heat, pressure, or a combination of both. However, achieving the perfect weld isn’t always straightforward. One common issue that welders encounter is excessive weld reinforcement.
Definition of Excessive Weld Reinforcement
Excessive weld reinforcement refers to an overbuildup of weld material beyond the required specifications. In simpler terms, it’s when more weld material is deposited than necessary for the intended application. This can lead to several issues, including compromised structural integrity and aesthetic concerns.
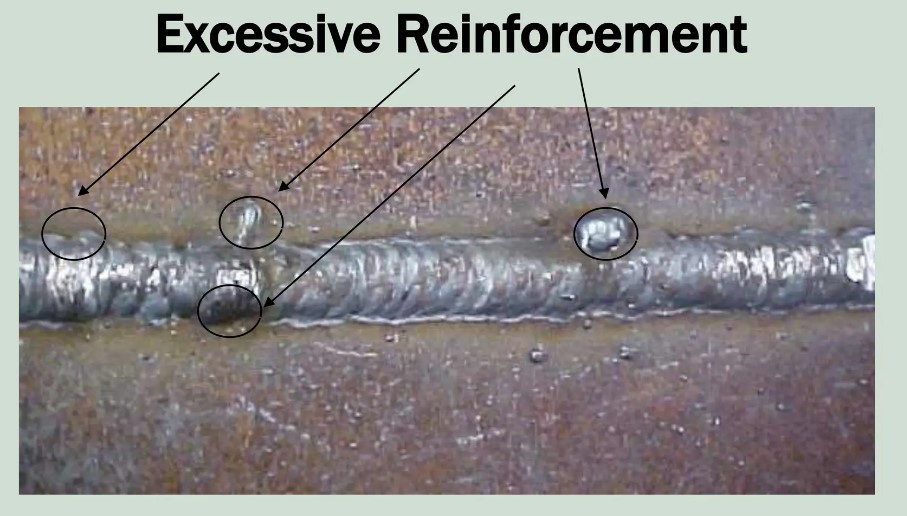
Causes of Excessive Weld Reinforcement
Excessive weld reinforcement can stem from various factors related to the welding process and the materials being welded. Understanding these causes is essential for welders to identify and rectify issues before they compromise the integrity of the weld.
Welding Process Factors
- Welding Technique: The welding technique employed plays a significant role in determining the amount of weld reinforcement. Certain welding processes, such as flux-cored arc welding (FCAW) or gas metal arc welding (GMAW), may inherently produce more weld metal deposition than others. Additionally, the skill and experience level of the welder can influence the consistency and quality of the weld bead, potentially leading to excessive reinforcement.
- Welding Parameters: Welding parameters, including voltage, current, travel speed, and wire feed rate, directly impact the amount of weld metal deposited. Incorrect parameter settings, such as excessive heat or wire feed speed, can result in excessive weld reinforcement. Conversely, insufficient parameters may lead to inadequate fusion and weaker welds, prompting welders to add more material to compensate.
Material Considerations
- Type of Metal: Different metals have varying thermal conductivities, melting points, and metallurgical properties, which can affect weld bead shape and size. Some metals, such as aluminum, require specific welding techniques and filler materials to achieve optimal results. Improper selection of welding processes or consumables for the metal being welded can contribute to excessive reinforcement.
- Thickness of the Material: The thickness of the base material being welded influences the amount of weld metal required to achieve adequate penetration and strength. Thicker materials may necessitate higher welding currents and deposition rates to ensure proper fusion, potentially leading to excessive reinforcement if not carefully controlled. Conversely, welding thin materials may require precise control to avoid burn-through and excessive buildup.
Consequences of Excessive Weld Reinforcement
Excessive weld reinforcement can have significant repercussions on the performance, appearance, and cost-effectiveness of welded structures. Understanding these consequences is paramount for welders and fabricators to mitigate potential risks and ensure the quality of their work.
Structural Integrity Issues
Excessive weld reinforcement can compromise the structural integrity of welded joints in several ways:
- Stress Concentrations: Excessive buildup of weld metal can create stress concentrations, particularly at the weld toe or root. These stress concentrations can lead to fatigue cracking, especially under cyclic loading conditions, reducing the fatigue life of the welded structure.
- Reduced Toughness: Weld metal deposited beyond the required specifications may alter the material properties, such as hardness and toughness, in the heat-affected zone (HAZ). This can weaken the joint and make it more susceptible to fracture, particularly in high-stress applications.
- Distortion and Warping: Excessive weld reinforcement can cause distortion and warping of the welded components, affecting dimensional accuracy and fit-up. This can pose challenges during assembly and may require additional corrective measures to align the components properly.
Aesthetic Concerns
In addition to structural issues, excessive weld reinforcement can impact the visual appearance of welded structures:
- Surface Irregularities: Overly protruding weld beads or excessive reinforcement can create surface irregularities and discontinuities, detracting from the overall aesthetics of the welded joint. This is particularly problematic in applications where appearance is important, such as architectural or automotive welding.
- Surface Finish: Excessive weld reinforcement may require extensive grinding or surface finishing to achieve the desired smoothness and contour, adding extra labor and cost to the fabrication process. This can result in a less visually appealing finish and may compromise the weld’s cosmetic quality.
Cost Implications
Excessive weld reinforcement can also have cost implications for welding projects:
- Material Waste: Depositing more weld metal than necessary results in material wastage, increasing material costs and reducing cost-efficiency. This is particularly significant for expensive filler materials or alloys used in specialized welding applications.
- Rework and Repair: Addressing excessive weld reinforcement often requires additional rework or repair, such as grinding or gouging, to correct the defects and bring the weld into compliance with specifications. This adds labor costs and extends project timelines, impacting overall project profitability.
Identifying Excessive Weld Reinforcement
Detecting excessive weld reinforcement is crucial for ensuring the quality and integrity of welded joints. Welders and inspectors employ various methods to identify and assess the extent of weld buildup accurately.
Visual Inspection
Visual inspection is often the first and most straightforward method used to identify excessive weld reinforcement:
- Visual Criteria: Inspectors visually examine the weld bead and surrounding area to assess its size, shape, and profile. Excessive weld reinforcement typically manifests as an overly pronounced weld bead that extends beyond the specified dimensions.
- Comparison to Standards: Weld specifications and industry standards provide guidelines for acceptable weld profiles and reinforcement. Inspectors compare the observed weld profile to these standards to determine compliance and identify any deviations indicative of excessive reinforcement.
- Surface Smoothness: Excessive weld reinforcement may result in surface irregularities, such as bumps, ridges, or protrusions. Visual inspection involves assessing the surface smoothness and contour of the weld to identify any abnormalities that may indicate excessive buildup.
- Dimensional Measurements: Inspectors may use calibrated tools, such as weld gauges or calipers, to measure the dimensions of the weld bead and compare them to the specified requirements. Deviations from the specified dimensions may indicate excessive reinforcement.
Non-Destructive Testing Methods
Non-destructive testing (NDT) methods provide more detailed and quantitative assessment of weld quality, including weld reinforcement:
- Ultrasonic Testing (UT): UT utilizes high-frequency sound waves to detect internal defects, including excessive weld reinforcement. By analyzing the reflections of sound waves from the weld interface, inspectors can assess the thickness and uniformity of the weld reinforcement.
- Radiographic Testing (RT): RT involves exposing the weld to X-rays or gamma rays and capturing radiographic images of the internal weld structure. Excessive weld reinforcement appears as a denser region on the radiograph, indicating higher weld metal deposition.
- Magnetic Particle Testing (MT): MT is used to detect surface and near-surface defects, including excessive reinforcement. A magnetic field is applied to the weld surface, and iron particles are applied. Any magnetic leakage caused by irregularities in the surface, such as excessive weld reinforcement, will attract the iron particles, indicating the presence of defects.
- Visual Examination with Magnification: In some cases, visual inspection may be enhanced by using magnifying devices, such as magnifying glasses or microscopes, to examine the weld surface in greater detail. This can help inspectors identify subtle irregularities or discontinuities associated with excessive reinforcement.
Preventive Measures for Excessive Weld Reinforcement
Addressing excessive weld reinforcement requires a proactive approach that focuses on preventive measures to ensure weld quality and integrity. Implementing robust training, quality control procedures, and proper welding techniques is essential for minimizing the risk of excessive reinforcement and optimizing weld performance.
Training and Education
- Welder Training Programs: Providing comprehensive training programs for welders is crucial for equipping them with the knowledge and skills necessary to produce high-quality welds. Training should cover welding fundamentals, techniques, and best practices, emphasizing the importance of proper reinforcement control.
- Continuing Education: Continuous learning and skills development are essential for welders to stay updated on the latest advancements in welding technology and techniques. Offering ongoing education opportunities, such as workshops, seminars, and certifications, ensures that welders remain proficient in controlling weld reinforcement and adhering to industry standards.
- Quality Awareness: Educating welders about the significance of weld quality and its impact on structural integrity and performance fosters a culture of quality consciousness. Emphasizing the importance of adhering to welding specifications and standards encourages welders to take ownership of their work and strive for excellence.
Quality Control Procedures
- Welding Procedure Specifications (WPS): Developing and adhering to well-defined welding procedure specifications is essential for ensuring consistency and reproducibility in weld quality. WPS documents outline the welding parameters, techniques, and acceptance criteria for each welding procedure, including control measures for weld reinforcement.
- In-process Inspection: Implementing regular in-process inspections during welding operations allows for timely detection and correction of any deviations from the specified weld parameters and reinforcement requirements. Inspectors monitor weld profiles, dimensions, and surface characteristics to identify and address excessive reinforcement promptly.
- Documentation and Recordkeeping: Maintaining detailed records of welding procedures, inspections, and quality control activities provides a traceable history of weld performance and compliance. Documentation facilitates process audits, root cause analysis, and continuous improvement initiatives, ensuring accountability and transparency in weld quality management.
Proper Welding Techniques
- Parameter Optimization: Optimizing welding parameters, including voltage, current, travel speed, and wire feed rate, is critical for controlling weld deposition and minimizing excessive reinforcement. Welders should carefully adjust parameters based on the material type, thickness, and joint configuration to achieve optimal penetration and fusion without excessive buildup.
- Welding Sequence: Proper sequencing of welding passes and techniques, such as weave patterns and oscillation, helps distribute weld metal evenly and minimize reinforcement buildup. Following recommended welding sequences and techniques specified in WPS documents ensures uniform weld profiles and adequate reinforcement control.
- Post-Weld Treatment: Implementing post-weld treatment processes, such as grinding or machining, to remove excess reinforcement and achieve the desired weld profile is essential for maintaining weld quality. Proper surface preparation and finishing techniques enhance the aesthetics and functionality of welded joints while eliminating potential stress concentrations.
Remedial Actions for Excessive Weld Reinforcement
When excessive weld reinforcement is identified, prompt remedial actions are necessary to rectify the issue and restore the integrity and appearance of the welded joint. Implementing effective grinding techniques and weld reinforcement removal methods is essential for achieving the desired weld profile and quality.
Grinding Techniques
- Grinding Equipment Selection: Selecting the appropriate grinding equipment is crucial for effectively removing excess weld reinforcement while minimizing material removal and heat buildup. Choose grinding tools, such as angle grinders or die grinders, with suitable abrasive discs or wheels designed for metal grinding applications.
- Grinding Angle and Pressure: Maintain a consistent grinding angle and apply moderate pressure to the grinding tool to achieve uniform material removal and contour blending. Avoid excessive pressure or aggressive grinding, as it may result in surface gouging, distortion, or overheating of the base material.
- Progressive Grinding Approach: Adopt a progressive grinding approach by starting with coarse-grit abrasive discs to remove bulk weld metal and gradually transitioning to finer-grit discs for smoothing and blending. This sequential grinding process ensures controlled material removal and facilitates the achievement of the desired weld profile.
- Surface Preparation: Prioritize surface preparation by cleaning the weld area of any contaminants, such as slag, spatter, or debris, before initiating grinding. A clean surface improves grinding efficiency and prevents contamination of the weld zone, ensuring optimal weld quality and appearance.
Weld Reinforcement Removal Methods
- Gouging: Gouging involves using specialized gouging electrodes or carbon arc gouging equipment to remove excess weld reinforcement by melting and evacuating the unwanted material. Gouging is particularly effective for thick weld deposits and hard-to-reach areas where grinding may be challenging.
- Machining: Machining methods, such as milling or turning, can be employed to remove excessive weld reinforcement, especially in precision welding applications requiring tight dimensional tolerances. CNC machining centers equipped with cutting tools can precisely remove weld metal while maintaining dimensional accuracy and surface finish.
- Plasma Cutting: Plasma cutting systems equipped with fine-cutting consumables can be utilized to trim excess weld reinforcement, particularly in thicker materials or structural components. Plasma cutting offers high cutting precision and speed, allowing for efficient removal of unwanted weld metal while minimizing heat-affected zones.
- Chemical Etching: Chemical etching processes involve applying chemical solutions or etchants to selectively dissolve and remove excess weld reinforcement without affecting the base material. This method is suitable for delicate or intricate weld geometries where mechanical removal techniques may be impractical or undesirable.
FAQs
What are the common signs of excessive weld reinforcement?
Excessive weld reinforcement often manifests as protrusions or uneven weld beads on the surface of welded components. Visual inspections can help identify these issues.
How can welders prevent excessive weld reinforcement?
Welders can prevent excessive reinforcement by adhering to proper welding techniques, monitoring welding parameters, and implementing quality control measures.
Why is quality control important in welding?
Quality control is essential in welding to ensure the integrity, reliability, and safety of welded structures. It helps detect defects early on and prevents costly rework or repairs.
What are the potential consequences of ignoring excessive weld reinforcement?
Ignoring excessive weld reinforcement can lead to structural failures, aesthetic issues, and increased production costs due to material waste and rework.
How can manufacturers improve weld quality and consistency?
Manufacturers can improve weld quality and consistency by investing in welder training,
Conclusion
In conclusion, excessive weld reinforcement poses significant challenges to weld quality, structural integrity, and overall project success. Through proactive measures and remedial actions, welders and fabricators can effectively manage and mitigate the risks associated with excessive reinforcement, ensuring the production of high-quality welds that meet performance requirements and industry standards.