Types of Welding Process
Introduction
Welding is a fundamental process used across various industries to join two or more pieces of metal together. It plays a vital role in the construction, manufacturing, and maintenance of structures and products. However, welding is not a one-size-fits-all technique. There are different types of welding processes, each with its own unique characteristics and applications. In this article, we will explore two main categories of welding: fusion welding and non-fusion welding.
Fusion welding is a type of welding, that involve joining of two or more materials using heat. This welding is called fusion welding as it is not compulsory to use filler material or not, also it doesn’t require external pressure to be applied. In fusion welding, if the two parts of similar materials are to be joined together, they are kept close to each other and heat from external source is used to melt the surfaces of both to fuse or join them together.
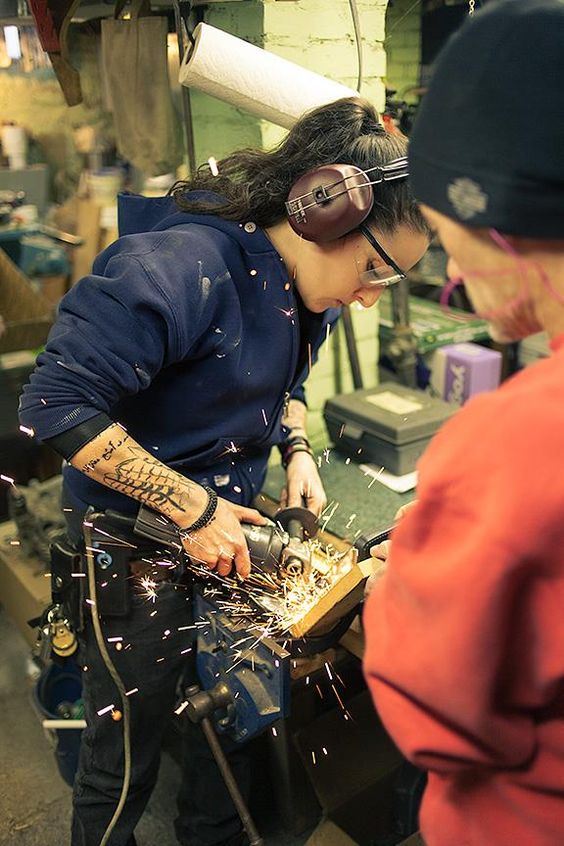
Fusion Welding and Non-Fusion Welding
Fusion welding involves melting the joining materials to be welded to the melting point. And non- fusion does not involve the melting of materials, it can also occur at low heat intensity. Examples of fusion welding are; shielded metal arc welding, gas metal arc welding, tungsten inert gas welding, submerged arc welding, and flux cored arc welding. Non-fusion welding does not require filler material while joining. There are many examples of non-fusion welding e.g., soldering, brazing, and pressure welding.
Fusion Welding Working
In fusion welding, when two different materials are involved, their edges are heated to a melting point. In some cases, a filler material is also used if there are gaps in the joint under welding. Fusion welding takes place when the molted base materials join with the molten fillers used. The same heat can be used for joining the material or it can be used externally.
Types of Fusion Welding
There are many types of fusion welding based on heat sources involved in heating.
1- Arc Welding Process
Arc welding is the best example of fusion welding. Arc welding uses an electric arc that generates heat reaching temperature up to 6000 degrees Fahrenheit. High temperature is involved in melting and fusing the materials. Fusion arc welding has another advantage that it can be used underwater. There are many types of arc welding processes based on their applications:
- Shielded Metal Arc Welding: SMAW is a type of arc welding that uses a flux-coated, consumable electrode to create an arc between an electrode and the workpiece. It is used in all applications of non-ferrous and ferrous materials.
- Metal Gas Arc Welding: Metal gas arc welding is a type of welding in which an electric arc is formed between the welding material and consumable wire electrode, and is melted for fusing. In this type, shielding gas is used to avoid contamination from the atmosphere. It is used to weld all commercial metals.
- Tungsten Inert Gas Welding: TIG welding is a type in which a non-consumable tungsten electrode is used that provides the required current to the welding electrode. In TIG welding, shielding through inert gas is done to avoid any oxidation and atmospheric contamination. It is used to weld steel, stainless steel, aluminum, and even gold.
- Plasma Arc Welding: In this type of welding, an electric arc is formed between the plasma torch nozzle and electrode. In this type electric arc is used to ionize the argon gas or plasma. It is used to weld pipes and tubes.
- Submerged Arc Welding: Submerged arc welding is a type of welding that involves the formation of an arc between a continuously fed consumable electrode and the workpiece. It is used to weld carbon steel, alloys, and steel.
- Flux Cored Arc Welding: Flux core arc welding is a type of welding that involves the arc between continuously fed consumable electrodes with flux. It is best for welding dirty, rusted, or contaminated metals easily.
2- Laser Beam Welding
Laser beam welding is a type of fusion welding process. Laser beam welding uses a focused laser beam as the energy source required for welding purposes. This process uses light energy to generate heat; this heat is very useful for joining metals and polymers. A laser beam provides a concentrated heat source that is used to join two metal pieces together. Laser beam welding is an advanced welding method and has many useful applications. It is mostly used in the automotive industry. It is very useful for welding carbon steel and stainless steel.
3- Electronic Beam Welding
The eprocess involves high-velocity electrons to join workpieces together. The electrons produce intense heat that enters the materials changing their solid state to molten. EBW welds are deep and thin and can only be achieved under specific atmospheric conditions.
4- Friction Welding
Friction welding is a type of fusion welding that generates heat through mechanical friction. There are various ways to perform mechanical friction on aluminum, steel, and sometimes wood materials. Mechanical friction is the force resisting the relative motion of solid surfaces or material elements sliding against each other. There are many possibilities or types of mechanical friction based on the type of joints. For example; one material can be stationary or another is moving. Examples of mechanical friction are friction stir welding, rotary friction welding, friction stir spot welding, and linear friction welding. Mechanical friction generates heat that is used for softening the material and also helps in making bonds and cooling it. Friction welding has the advantage that it does not require any filler metal like shielding gas or flux. The process has applications in automotive, aerospace, and industrial tubes and shafts.
5- Resistance Welding Processes
Resistance welding is considered as fastest welding process among other fusion welding methods. Resistance welding is considered a cheap welding process as it does not require any other material for bonding purposes. In resistance welding heat is produced through the resistance of the work to the flow of electric current in a circuit and by the application of pressure. It is preferred in the automotive industry, aerospace, tubing, and electrical appliances. There are two main types of resistance welding: resistance spot welding and resistance seam welding.
Non-Fusion Welding
Non-fusion welding is a type of welding which do not involve heating compared to fusion welding. It can occur under low heat intensity as it doesn’t require melting. Another main difference is that it does not need any filler metal. It requires adequate pressure to be applied to complete the joint and metal pieces are heated to forging temperature. The heating is provided by oxyfuel flame or electric resistance then an adequate amount of pressure is applied to heated pieces by a mechanical source. It can be any hammer, hydraulic press, or mechanical lever based on the requirements of the project.
Types of Non-Fusion Welding
There are 5 main types of non-fusion welding.
- Forge Welding
- Resistance Butt Welding
- Flash Welding
- Spot Welding
- Resistance Seam welding
1- Forge Welding– Forge welding is a type of solid-state welding that involves heating two metal pieces to high temperature before applying any pressure i.e., hammering, hydraulic pressing, or rolling. This pressure causes the plastic deformation of metal pieces. This is the most ancient and simplest process of joining. Forge welding is versatile in its functionality and it has applications in steel and ironworks. With the industrial revolution manual forge welding is replaced by automated forge welding in all manufacturing processes.
It is a type of solid-state welding process in which heat is produced through electrical resistance by passing an electric current through the parts under preset force. After heating, the force across the interface helps in joining the metal pieces to a weld. It is used to join the components with the same cross-sectional areas through a single operation. It has applications in narrow strip joints like automobile road wheel rims.
3- Flash Welding
It is a type of welding in which the two metal pieces that are to be joined are pressed together. First of all the metal pieces are set apart at a predetermined distance and current is applied to the metal, and the gap between the two pieces creates resistance and produces the arc that melts the metal. When the metal pieces reach the required temperature then they are pressed together resulting in forging pieces to create a weld. It is used to weld heavy anchor chains, rails, and pipes.
4- Spot Welding
Spot welding sometimes known as resistance spot welding is basically a resistance welding process. This welding process involves welding metal sheets together by applying pressure and heat from an electric current to the weld area. The process is done through copper ally electrodes which pass the electrical current through the weld pieces. This melted the metal pieces and through applied pressure, they are joined together. It is used to weld wire mesh.
5- Seam welding – Seam welding is a type of welding that involves the joining of two or more workpieces of similar or dissimilar materials having a continuous seam. There are two main categories of seam welding resistance seam welding and friction seam welding. It is used in manufacturing tin cans, radiators, and steel drums.