Shielded Metal Arc Welding
Introduction
Shielded Metal Arc Welding (SMAW), also known as stick welding or manual metal arc welding, is a manual welding process that has been used for over 100 years. It is a versatile process that can be used to weld a wide range of metals, including mild steel, high-strength steel, and stainless steel. In SMAW, an electric arc is formed between a consumable electrode coated in flux and the workpiece. The flux coating on the electrode protects the weld pool from contamination and helps to stabilize the arc. SMAW is a popular choice for welding in many industries due to its simplicity, versatility, and relatively low cost. In this article, we will delve deeper into the shielded metal arc welding process, including its history, equipment, and applications.
Definition SMAW
Shielded metal arc welding, also known as stick welding or manual metal arc welding, is a manual arc welding process that uses a consumable electrode coated in flux to lay the weld. The flux coating on the electrode protects the weld pool from contamination and helps to stabilize the arc. SMAW is a versatile process that can be used to weld a wide range of metals, including mild steel, high-strength steel, and stainless steel.
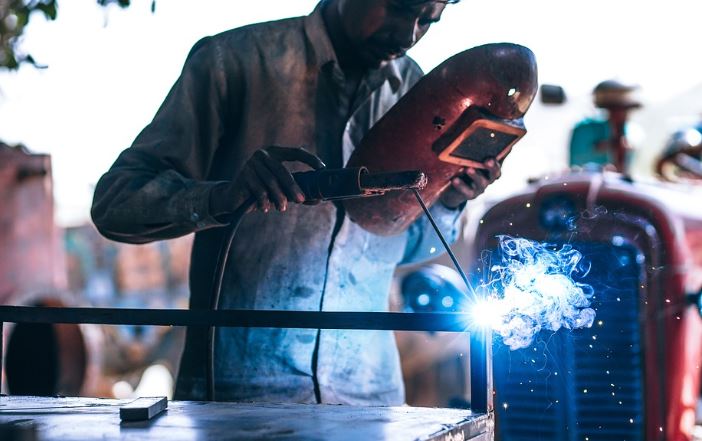
Brief history of SMAW
Shielded metal arc welding has been around for over 100 years and is one of the oldest welding processes in existence. The process was developed in Russia in the late 1800s and was later introduced to the United States in the early 1900s. In the decades following its introduction, SMAW became a popular choice for welding in many industries, including construction, shipbuilding, and manufacturing. Today, it remains a widely used welding process due to its simplicity, versatility, and relatively low cost.
What is Shielding in SMAW
In SMAW, the term “shielding” refers to the protection of the weld pool from contamination by atmospheric gases, such as oxygen and nitrogen. This is achieved by using a consumable electrode coated in a layer of flux, which produces a gas as it burns that surrounds the weld pool and protects it from the atmosphere.
The flux coating on the electrode is made up of a mixture of various materials, including various types of salts, minerals, and metals. When the electrode is burned, the flux coating decomposes and produces a shielding gas that surrounds the weld pool. This shielding gas helps to stabilize the arc and prevents the weld pool from being contaminated by atmospheric gases, which can weaken the weld.
In addition to providing shielding, the flux coating on the electrode also helps to clean the base metal and improve the quality of the weld. It removes any surface contaminants, such as rust or paint, and helps to reduce the formation of weld defects, such as porosity or slag inclusion.
Types of materials that can be welded with
Shielded metal arc welding (SMAW) is a welding process that can be used on a variety of materials, including carbon steel, low alloy steel, stainless steel, and cast iron. It can also be used on some non-ferrous metals, such as aluminum and copper, with the use of special electrodes.
What is SMAW used for?
SMAW is used in a variety of industries, including construction, shipbuilding, manufacturing, and automotive repair. It is often used in the maintenance and repair of heavy equipment and machinery, as well as in the fabrication of structural steel. SMAW is also commonly used in the pipeline industry, as it is well-suited for welding in remote locations where other welding processes may not be practical.
Explanation of the SMAW process
SMAW is a manual welding process that involves the use of a consumable electrode coated in flux to lay the weld. The flux coating on the electrode melts and forms a gas that shields the weld area from contaminants in the air. An electric current is used to create an arc between the electrode and the workpiece. As the electrode is consumed, the welder must periodically stop welding to replace it.
Equipment and supplies needed for SMAW
- Welding power source
- Welding cables
- Electrode holder
- Ground clamp
- Electrodes
- Flux
- Protective gear (helmet, gloves, etc.)
Advantages and disadvantages of SMAW
Advantages:
- SMAW is a versatile process that can be used on a variety of metals and alloys.
- It is a relatively simple process that requires minimal equipment.
- SMAW is a portable welding process that can be used in a variety of locations.
Disadvantages:
- SMAW can produce a lot of slag, which must be chipped or ground off after welding.
- It can be a slow process compared to other welding methods.
- The welder must manually feed the electrode, which can be tiring.
- The welds may not be as aesthetically pleasing as those produced by other methods.
Positions for Shielded metal arc welding
Shielded metal arc welding can be performed in all positions, including flat, horizontal, vertical, and overhead.
- In the flat position, the weld is made on a horizontal plane and the electrode is held in a vertical position. This is the most common position for SMAW and is typically the easiest for beginners to learn.
- In the horizontal position, the weld is made on a horizontal plane and the electrode is held in a horizontal position. This position is often used for welding the sides of beams or plates.
- In the vertical position, the weld is made on a vertical plane and the electrode is held in a vertical position. This position is often used for welding the edges of plates or for making vertical welds on structures.
- In the overhead position, the weld is made on a horizontal or vertical plane above the head of the welder. This position is often used for welding pipes or for making welds in hard-to-reach areas.
It’s important to note that while SMAW can be performed in all positions, it may be more difficult to achieve good weld quality in certain positions, such as overhead, due to the gravity-assisted flow of the weld pool.
Future Developments in SMAW Technology
Potential future developments in SMAW technology:
- Some possible future developments in SMAW technology include the development of new flux coatings that improve the performance and efficiency of the process.
- There may also be efforts to automate certain aspects of the SMAW process, such as the feeding of the electrode, to make the process faster and less physically demanding for the welder.
- Another area of focus for future development could be the development of new electrodes and alloys that expand the range of materials that can be welded using SMAW.
- There may also be efforts to improve the aesthetics of SMAW welds and make the process more suitable for use in applications where appearance is important.
FAQs
In conclusion, SMAW is a manual welding process that uses a consumable electrode coated in flux to lay the weld. The flux coating on the electrode creates a gas shield to protect the weld area from contaminants in the air. SMAW is a versatile process that can be used on a variety of metals and alloys, and it is relatively simple to perform, requiring minimal equipment. However, SMAW can be a slow process and produce a lot of slag. It is also a portable welding process that can be used in a variety of locations. In the future, there may be developments in SMAW technology that improve the performance and efficiency of the process, such as the development of new flux coatings, automation of certain aspects of the process, and the development of new electrodes and alloys. There may also be efforts to improve the aesthetics of SMAW welds and make the process more suitable for use in applications where appearance is important.