Comprehensive Guide to Valves: Types, Purposes, and Applications
Valves are crucial components in various industries, serving as the control points for regulating the flow of liquids, gases, and other substances within a system. They are designed to start, stop, throttle, or direct the flow, ensuring the proper functioning of pipelines, machinery, and other complex systems. Below is a detailed exploration of the different types of valves, their purposes, and their applications.
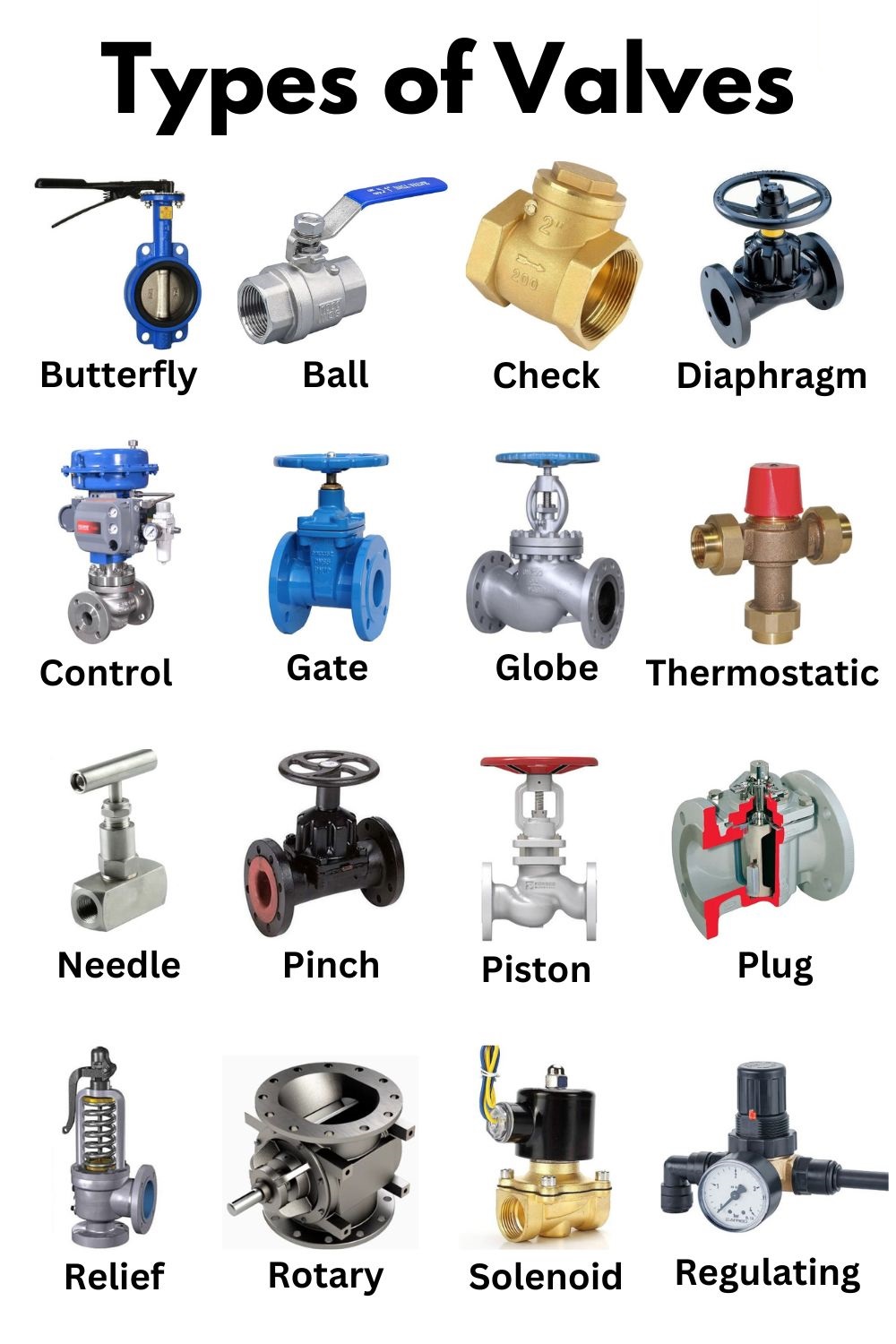
Butterfly Valve
Purpose: Butterfly valves are designed for quick shut-off applications. They are quarter-turn valves, meaning they only require a 90-degree turn to go from fully open to fully closed.
Applications: Commonly used in water supply, wastewater treatment, and chemical processing. They are particularly useful in large-diameter pipes where space and weight are concerns.
Advantages: Lightweight, compact, and easy to operate. Suitable for high-pressure and high-temperature applications.
Ball Valve
Purpose: Ball valves utilize a spherical disc (the “ball”) to control the flow. When the ball’s hole is aligned with the flow, the valve is open; when it’s perpendicular, the valve is closed.
Applications: Frequently used in residential plumbing, gas pipelines, and industries where a tight seal is essential, such as in the oil and gas sector.
Advantages: Offers reliable sealing with minimal leakage, easy to operate, and durable under high-pressure conditions.
Check Valve
Purpose: Check valves are one-way valves, allowing flow in only one direction. They prevent backflow in a system, protecting equipment from damage.
Applications: Widely used in water and wastewater treatment, chemical processing, and in pump systems to prevent reverse flow and maintain pressure.
Advantages: Simple design, automatic operation, and low maintenance. Critical for protecting systems from contamination or damage due to reverse flow.
Diaphragm Valve
Purpose: Diaphragm valves use a flexible diaphragm to control the flow of fluid. The diaphragm presses down to block flow or lifts to allow fluid to pass through.
Applications: Commonly found in pharmaceutical, food, and water treatment industries where contamination must be minimized.
Advantages: Excellent for handling corrosive or abrasive fluids, providing a tight seal, and ideal for hygienic processes due to the non-contact between the fluid and the valve components.
Control Valve
Purpose: Control valves regulate the flow of fluids by varying the size of the flow passage, often used to control pressure, temperature, or fluid level.
Applications: Integral in industries like power generation, oil and gas, and chemical processing for maintaining process variables within desired ranges.
Advantages: Provides precise control over process conditions, can be automated, and is essential for maintaining system efficiency and safety.
Gate Valve
Purpose: Gate valves are designed to either completely stop or fully allow the flow of fluid. The gate (a metal slab) moves up or down to open or close the valve.
Applications: Typically used in pipelines that transport liquids like oil, water, and gas. Ideal for applications where the valve is not frequently operated.
Advantages: Offers minimal flow resistance when fully open, suitable for high-pressure applications, and ensures a tight seal.
Globe Valve
Purpose: Globe valves are used for throttling flow. They consist of a movable plug or disc element and a stationary ring seat in a spherical body.
Applications: Found in systems where flow regulation is needed, such as in cooling water systems, fuel oil systems, and high-pressure steam lines.
Advantages: Provides good flow control, easier to maintain than other types of valves, and offers a reliable seal.
Thermostatic Valve
Purpose: Thermostatic valves automatically control the temperature of a system by adjusting the flow of heat transfer fluids.
Applications: Common in heating, ventilation, and air conditioning (HVAC) systems, as well as in hot water supply systems to maintain a consistent temperature.
Advantages: Enhances energy efficiency by maintaining optimal temperature, reduces manual intervention, and improves system safety.
Needle Valve
Purpose: Needle valves are used for precise control of flow. The thin, needle-like plunger allows for fine adjustments in flow rate.
Applications: Often used in instrumentation, hydraulic systems, and applications where precise flow control is required, such as in laboratories.
Advantages: Provides precise flow control, suitable for low flow rates, and offers a tight seal.
Pinch Valve
Purpose: Pinch valves control fluid flow by pinching a flexible tube or hose, thereby stopping or allowing flow.
Applications: Ideal for handling slurries, granular materials, or fluids with suspended solids. Used in wastewater treatment, food processing, and mining industries.
Advantages: No contact between the fluid and valve components, minimizing contamination risk. Easy to maintain and ideal for abrasive or corrosive fluids.
Piston Valve
Purpose: Piston valves use a cylindrical piston to control flow, offering a tight seal and long service life.
Applications: Often found in steam, condensate, and high-pressure systems, especially in industries like power generation and chemical processing.
Advantages: Provides a reliable seal, durable under high-pressure conditions, and offers low maintenance.
Plug Valve
Purpose: Plug valves use a cylindrical or conically-tapered plug to control fluid flow. By rotating the plug, the flow can be either directed or blocked.
Applications: Widely used in the oil and gas industry, chemical plants, and wherever quick and reliable flow control is necessary.
Advantages: Simple design, fast operation, and effective in handling corrosive fluids or slurries.
Relief Valve
Purpose: Relief valves are safety devices designed to protect systems from overpressure by automatically releasing excess pressure.
Applications: Common in boilers, pressure vessels, and chemical processing equipment to prevent system failures due to overpressure.
Advantages: Essential for system safety, prevents equipment damage, and operates automatically under excessive pressure conditions.
Rotary Valve
Purpose: Rotary valves control the flow of bulk materials by rotating a cylindrical rotor within a casing.
Applications: Commonly used in material handling systems, such as in the food, chemical, and pharmaceutical industries, for metering and feeding applications.
Advantages: Provides precise material flow control, handles a variety of materials, and operates efficiently in both low and high-pressure environments.
Solenoid Valve
Purpose: Solenoid valves are electrically operated valves that control the flow of fluids through a system using an electromagnetic solenoid.
Applications: Used in automated systems for fluid control, such as in irrigation systems, refrigeration units, and pneumatic control systems.
Advantages: Quick response time, easily automated, and ideal for remote operation.
Regulating Valve
Purpose: Regulating valves maintain a constant pressure or flow rate within a system, adjusting to changes in demand or operating conditions.
Applications: Found in water distribution systems, gas pipelines, and HVAC systems to ensure consistent operation and efficiency.
Advantages: Enhances system stability, reduces the need for manual adjustments, and improves overall efficiency.
FAQs
What are the key differences between a Globe Valve and a Gate Valve in terms of flow control and sealing capability?
Key Differences Between Globe and Gate Valves:
- Flow Control: Globe valves are designed for precise flow regulation and throttling, making them suitable for applications where flow control is critical. Gate valves, however, are intended for fully open or fully closed positions, with minimal flow resistance in the open position, making them ideal for on/off control rather than throttling.
- Sealing Capability: Globe valves offer better sealing for applications requiring frequent operation and flow adjustment. Gate valves, while providing a tight seal when fully closed, are less effective for applications requiring fine flow control and are more prone to leakage in throttling positions.
How does the material of a Diaphragm Valve’s diaphragm influence its application in different industries?
Impact of Diaphragm Material in Diaphragm Valves:
- The material of the diaphragm is crucial because it must withstand the specific chemical, temperature, and pressure conditions of the application. For example, elastomers like EPDM are used for general chemical resistance, while PTFE diaphragms are chosen for high chemical resistance and sterilization processes in the pharmaceutical industry. The diaphragm’s material determines the valve’s durability and suitability for specific fluids and operating environments.
In what scenarios would a Pinch Valve be preferred over a Ball Valve, particularly in handling abrasive fluids?
Scenarios for Preferring a Pinch Valve Over a Ball Valve:
- Pinch valves are preferred when handling abrasive fluids, slurries, or materials with suspended solids because the valve mechanism does not come into contact with the fluid, reducing wear and preventing blockages. In contrast, ball valves may suffer from wear or damage in such conditions due to direct contact between the fluid and the valve components.
Why are Solenoid Valves commonly used in automated systems, and what are their limitations compared to manually operated valves?
Solenoid Valves in Automated Systems:
- Solenoid valves are commonly used in automated systems because they offer fast and precise control with the ability to be operated remotely via electrical signals. They are ideal for applications requiring quick opening and closing. However, their limitations include dependency on power supply, potential for overheating in continuous operation, and they may not be suitable for high-pressure or high-temperature applications where manual valves might perform better.
How does the operation of a Relief Valve contribute to the overall safety of pressure-sensitive systems, and what factors determine its set pressure?
Relief Valve Operation for System Safety:
- Relief valves enhance the safety of pressure-sensitive systems by automatically releasing excess pressure when it exceeds a preset limit, preventing potential damage or explosions. The set pressure is determined based on the system’s maximum allowable working pressure, ensuring that the valve opens at the right moment to protect the system while maintaining operational efficiency.