How to Weld Varying Diameter Pipes
Introduction
Welding varying diameter pipes can be a challenging task that requires expertise and precision. Whether you’re working on a plumbing project, industrial construction, or any other application involving pipes, understanding the proper techniques for welding different pipe diameters / pipe welding is essential. In this article, we will delve into the intricacies of welding varying diameter pipes, providing you with valuable insights, step-by-step instructions, and expert tips to ensure successful welds.
Understanding the Importance of Welding Varying Diameter Pipes
Welding varying diameter pipes is crucial in various industries where pipes with different diameters need to be joined together seamlessly. This process ensures a continuous flow of fluids, gases, or other substances without leaks or structural weaknesses. Whether you’re connecting small pipes to larger ones or pipes of varying sizes, understanding the principles of welding these pipes will enable you to achieve secure and efficient joints.
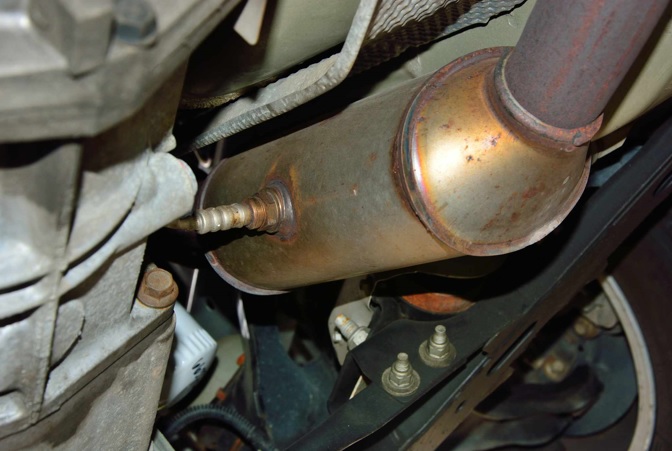
Preparing for the Welding Process
Before starting the welding process, proper preparation is vital for successful outcomes. Follow these steps to ensure you’re well-prepared:
Gathering the Necessary Tools and Equipment
To weld varying diameter pipes effectively, you’ll need a set of essential tools and equipment, including:
- Welding machine: Choose a machine suitable for the pipe material and the welding method you intend to use.
- Welding electrodes or filler wire: Select the appropriate type and diameter based on the pipe material and welding process.
- Safety gear: Wear protective clothing, gloves, helmet, and safety glasses to ensure your safety during the welding process.
- Measuring tools: Use a tape measure or calipers to accurately determine the pipe diameters.
Cleaning the Pipe Surfaces
Proper cleaning of the pipe surfaces is crucial for achieving high-quality welds. Use a wire brush or a suitable cleaning solution to remove any dirt, rust, or contaminants from the surfaces to be welded. This ensures optimal fusion and prevents impurities from compromising the weld joint.
Choosing the Right Welding Method
Selecting the appropriate welding method is essential to ensure strong and durable welds when working with varying diameter pipes. Different welding techniques can be employed, depending on the pipe material, project requirements, and available equipment. Some commonly used methods include:
Shielded Metal Arc Welding (SMAW)
SMAW, also known as stick welding, is a versatile and widely used welding method. It involves using a flux-coated electrode, which melts and forms the weld joint when struck by an electric arc. SMAW is suitable for various pipe materials, making it a popular choice for welding varying diameter pipes.
Gas Tungsten Arc Welding (GTAW)
GTAW, or TIG welding, utilizes a non-consumable tungsten electrode to produce the weld joint. This method offers excellent control, producing precise and high-quality welds. GTAW is particularly suitable for thin-walled pipes or applications that require aesthetic welds.
Gas Metal Arc Welding (GMAW)
GMAW, commonly known as MIG welding, employs a consumable wire electrode and shielding gas to create the weld. This method is known for its speed and efficiency, making it suitable for projects involving larger diameter pipes or high production volumes.
Applying Correct Welding Techniques
To ensure successful welds when working with varying diameter pipes, it’s essential to apply the correct welding techniques. Follow these guidelines for optimal results:
Positioning and Tack Welding
Before starting the main welding process, position the pipes correctly and use tack welds to hold them in place. Tack welding involves creating small, temporary welds that secure the pipes together, allowing for easy adjustment and alignment. This step helps maintain the desired position and ensures accurate alignment during the final welding.
Adjusting Current and Voltage Settings
Proper adjustment of current and voltage settings is critical for achieving the desired weld quality. Consult the welding machine’s manual and consider the pipe material and thickness to determine the appropriate settings. Use trial welds on scrap material to fine-tune the settings before proceeding with the actual welding.
Employing Proper Welding Techniques
When welding varying diameter pipes, employ the following techniques to ensure strong and reliable weld joints:
- Maintain a consistent travel speed to ensure uniform heat distribution.
- Control the welding arc length to prevent excessive heat input or lack of fusion.
- Use the correct weaving technique, such as a slight oscillation, to distribute the weld metal evenly.
- Employ proper joint preparation, ensuring suitable bevels or edge preparations for optimal weld penetration.
Dealing with Common Challenges
Welding varying diameter pipes can present some challenges. By being aware of these challenges and implementing appropriate solutions, you can overcome them effectively. Here are a few common challenges you may encounter:
Pipe Misalignment
Misalignment is a common issue when welding varying diameter pipes. It can lead to poor fit-up and inadequate fusion. To address this, use clamps or alignment tools to ensure proper alignment before tack welding. Additionally, consider using back purging techniques to protect the weld from oxidation and achieve better penetration.
Heat Distortion
Welding generates heat, which can cause distortion, especially in larger diameter pipes. To mitigate heat distortion, utilize preheating techniques to balance the temperature distribution and minimize the risk of warping or buckling. Post-weld heat treatment may also be necessary for specific applications or materials.
Inadequate Penetration
Insufficient weld penetration can weaken the joint, making it susceptible to leaks or failure. Ensure proper joint preparation, adjust welding parameters as needed, and use suitable welding techniques to achieve sufficient penetration. Performing non-destructive testing, such as radiographic or ultrasonic inspection, can help verify the weld quality.
Ensuring Weld Quality
To ensure the highest quality welds when working with varying diameter pipes, follow these guidelines:
Conducting Visual Inspection
Perform a visual inspection of the welds to identify any defects or irregularities. Check for proper fusion, absence of cracks, and adequate penetration. If any issues are detected, they should be repaired promptly to maintain the integrity of the weld joint.
Performing Non-Destructive Testing (NDT)
Non-destructive testing methods, such as radiographic testing (RT), ultrasonic testing (UT), or dye penetrant testing (PT), can provide valuable insights into the internal structure and integrity of the welds. Consider employing NDT techniques, especially for critical applications or when welding high-pressure pipes.
Adhering to Welding Standards and Codes
Consult relevant welding standards and codes, such as those provided by the American Welding Society (AWS) or the International Organization for Standardization (ISO). Adhering to these standards ensures compliance with industry best practices, enhancing the quality and reliability of the welds.
Maintaining Safety Measures
Welding varying diameter pipes involves inherent risks, and maintaining safety measures is crucial to protect yourself and others involved in the welding process. Here are some safety guidelines to follow:
Personal Protective Equipment (PPE)
Always wear appropriate personal protective equipment, including welding helmets, safety glasses, welding gloves, flame-resistant clothing, and steel-toed boots. PPE protects you from sparks, ultraviolet (UV) radiation, and potential hazards associated with welding.
Ventilation and Respiratory Protection
Ensure proper ventilation in the welding area to prevent the accumulation of harmful fumes and gases. If working in confined spaces or poorly ventilated areas, use respiratory protection, such as a powered air-purifying respirator (PAPR) or a supplied-air respirator (SAR), to safeguard against inhalation of welding fumes.
Fire Safety
Keep fire extinguishers readily available and familiarize yourself with their operation. Clear the work area of flammable materials, and if necessary, use fire-resistant blankets or welding screens to protect nearby objects or structures.
Electrical Safety
Inspect the welding equipment and cables regularly for any damage or wear. Ensure proper grounding of the welding machine and avoid wet conditions or standing on damp surfaces while welding. Stay vigilant to prevent electrical hazards.
FAQs
What is pipeline welding?
Can I weld pipes with significantly different diameters?
Yes, it is possible to weld pipes with significantly different diameters. However, proper planning and selection of suitable welding techniques are crucial to ensure a secure and robust joint. Consider using transition fittings or adapters to bridge the diameter difference and achieve a seamless connection.
What type of welding machine is suitable for welding varying diameter pipes?
The choice of welding machine depends on factors such as pipe material, welding method, and project requirements. Welding machines such as stick welders (SMAW), TIG welders (GTAW), or MIG welders (GMAW) can be suitable for welding varying diameter pipes. Select a machine that offers the necessary power output and welding capabilities for your specific application.
Do I need to use different welding techniques for different pipe materials?
Yes, different pipe materials may require specific welding techniques or processes. For example, welding stainless steel pipes may require specialized techniques like purging or back purging to prevent oxidation. Consult welding procedure specifications (WPS) or industry guidelines for the recommended techniques for specific pipe materials.
How do I ensure a strong and durable weld joint when welding varying diameter pipes?
To ensure a strong and durable weld joint, follow these guidelines:
- Properly prepare the pipe surfaces by cleaning and removing contaminants.
- Use the correct welding technique and adjust welding parameters according to the pipe material and thickness.
- Ensure adequate penetration and fusion by using suitable joint preparation and welding techniques.
- Perform visual inspections and, if necessary, non-destructive testing to verify the quality of the weld.
Are there any special considerations for welding large diameter pipes?
When welding large diameter pipes, consider the following:
- Ensure proper alignment and support to prevent distortion during the welding process.
- Employ preheating techniques to minimize heat distortion.
- Use suitable joint preparation, such as beveling, to allow for better penetration.
- Consider using multiple weld passes or mechanized welding methods for efficient and high-quality welds.
What safety precautions should I take while welding varying diameter pipes?
When welding varying diameter pipes, prioritize safety by:
- Wearing appropriate personal protective equipment, including welding helmets, safety glasses, gloves, and flame-resistant clothing.
- Ensuring proper ventilation or using respiratory protection to avoid inhaling welding fumes.
- Having fire extinguishers nearby and following fire safety guidelines.
- Regularly inspecting welding equipment for any damage or wear.
- Adhering to electrical safety measures and avoiding wet conditions while welding.
Conclusion
Welding varying diameter pipes is a complex task that requires careful preparation, proper techniques, and adherence to safety measures. By following the steps outlined in this guide, you can increase your chances of achieving strong, durable, and reliable weld joints.
Proper preparation, including gathering the necessary tools and equipment, cleaning the pipe surfaces, and choosing the appropriate welding method, sets the foundation for a successful welding process. Positioning and tack welding the pipes, adjusting current and voltage settings, and employing proper welding techniques are crucial for achieving optimal weld quality.
It is important to be aware of and address common challenges such as pipe misalignment, heat distortion, and inadequate penetration through the use of clamps, alignment tools, preheating techniques, and back purging methods. Conducting visual inspections and performing non-destructive testing when necessary help ensure the integrity of the welds.
Adhering to welding standards and codes and maintaining safety measures throughout the welding process are essential for the well-being of the welder and the overall success of the project. Following industry best practices and seeking professional guidance or assistance when needed will help you develop the necessary skills and expertise for welding varying diameter pipes effectively.
Remember that practice and experience play a significant role in mastering the art of welding. With time and dedication, you will become proficient in welding varying diameter pipes and produce high-quality welds that meet the requirements of your projects.