Keyhole Welding
Introduction
Definition and Explanation of Keyhole Welding
Keyhole welding is an advanced welding technique that involves the creation of a keyhole or hole at the leading edge of the weld pool. It is achieved by using a concentrated heat source, such as a laser or an electron beam, to generate intense heat and melt the material. The heat source penetrates partially or completely through the workpiece, forming a void or channel known as the keyhole. As the heat source progresses, the molten metal fills in behind the keyhole, forming the weld bead. The keyhole provides deep penetration into the workpiece, resulting in a strong and efficient weld.
Importance and Applications of Keyhole Welding
Keyhole welding offers several advantages over conventional welding techniques. Its deep penetration capability allows for the joining of thick materials with a single pass, reducing the need for multiple weld layers. This results in improved productivity and cost savings. Keyhole welding also minimizes heat input and distortion, making it suitable for welding heat-sensitive materials. Furthermore, it provides excellent weld quality with minimal defects, reducing the need for extensive post-weld processing.
Keyhole welding finds applications in various industries, including aerospace, automotive, energy, and manufacturing. It is used for joining structural components, such as aircraft parts, automotive frames, and pressure vessels. Keyhole welding is particularly beneficial in applications that require high weld strength, tight tolerances, and efficient production rates. Additionally, it is utilized in welding dissimilar materials and creating hermetic seals, making it indispensable in specialized fields such as electronics and medical device manufacturing.
The significance of keyhole welding lies in its ability to achieve deep penetration, high welding speeds, and superior weld quality, making it a preferred choice for many advanced welding applications.
Keyhole Welding Process
Heat Source Selection (Laser, Electron Beam, etc.)
In keyhole welding, the selection of the heat source is crucial to achieve the desired welding results. Commonly used heat sources include lasers and electron beams. Laser keyhole welding utilizes a high-energy laser beam, generated by a laser source, which can be further categorized into solid-state lasers, CO2 lasers, or fiber lasers. Electron beam keyhole welding, on the other hand, employs a focused stream of high-velocity electrons generated in a vacuum chamber.
The heat source, whether it is a laser or an electron beam, is generated and then precisely focused onto the workpiece. Optics, lenses, and mirrors are used to concentrate and direct the heat source to a specific point on the workpiece. The goal is to create a highly concentrated energy beam that can generate intense heat at the targeted area.
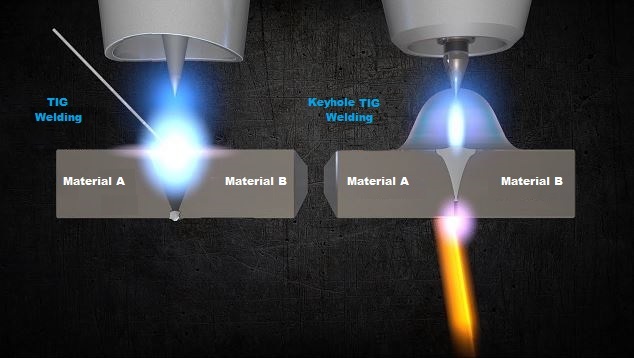
Formation of the Keyhole
As the concentrated heat source interacts with the workpiece, the intense heat rapidly melts and vaporizes the material at the point of contact. The combination of the heat source’s energy and the material’s properties leads to the formation of a keyhole—a narrow void or channel. The keyhole extends partially or completely through the workpiece, exposing the underlying material.
Molten Metal Filling and Formation of the Weld Bead
Once the keyhole is formed, the molten metal adjacent to the keyhole’s leading edge flows behind it, filling in the void. This molten metal forms the weld bead as the heat source progresses along the joint. The molten metal solidifies and cools, creating a strong fusion between the workpiece and the filler material (if used). The result is a continuous, high-quality weld bead with deep penetration and minimal defects.
The keyhole welding process combines precise heat source control, material properties, and skilled technique to achieve effective penetration, fusion, and weld formation. The process parameters such as power, speed, and shielding gas are carefully adjusted to ensure optimal weld quality and integrity.
Advantages of Keyhole Welding
Deep Penetration and High Welding Speed
One of the significant advantages of keyhole welding is its ability to achieve deep penetration into the workpiece. The focused heat source creates a narrow keyhole that allows the molten metal to flow deep into the joint. This results in strong and reliable welds, especially in thick materials. Additionally, keyhole welding enables high welding speeds due to its efficient heat transfer mechanism, leading to increased productivity and reduced production time.
Reduced Heat Input and Distortion
Keyhole welding minimizes heat input and associated thermal effects compared to conventional welding techniques. The concentrated heat source melts only a small portion of the material, reducing the overall heat input into the workpiece. As a result, keyhole welding helps to minimize distortion, warping, and residual stresses in the welded components. This makes it particularly suitable for joining heat-sensitive materials or intricate structures that require dimensional accuracy.
Versatility in Welding Different Materials
Keyhole welding exhibits versatility in welding various materials, including metals and alloys with different compositions and thicknesses. It can effectively join dissimilar materials with distinct properties, expanding the range of applications. The ability to control the keyhole size and welding parameters allows for customization according to the specific material requirements, ensuring strong and reliable welds across a wide range of material combinations.
Minimal Post-Weld Processing Requirements
Keyhole welding produces high-quality welds with minimal defects, which often reduces the need for extensive post-weld processing. The deep penetration and controlled heat input result in a narrow heat-affected zone (HAZ) and limited distortion. Consequently, there is less need for weld cleanup, such as grinding, polishing, or rework, saving time and resources. This advantage is especially valuable in industries where precise and clean welds are essential, such as aerospace and electronics.
The advantages of keyhole welding make it a preferred choice for many applications, providing efficient and reliable welding solutions with deep penetration, high welding speeds, reduced distortion, and minimal post-weld processing requirements.
Keyhole Welding Techniques
Laser Keyhole Welding
- Explanation of Laser Keyhole Welding Process
Laser keyhole welding utilizes a high-energy laser beam to create and maintain a keyhole during the welding process. The laser beam is focused onto the workpiece, generating intense heat that melts and vaporizes the material at the point of contact. The vaporized material forms a keyhole, and as the laser beam moves along the joint, the molten metal fills in behind the keyhole to create the weld bead.
- Advantages and Limitations of Laser Keyhole Welding Advantages
- Precise control over the welding process, including power, speed, and focus.
- High welding speeds and deep penetration capabilities.
- Excellent weld quality with minimal defects.
- Versatility in welding various materials, including metals, alloys, and even dissimilar materials.
- Minimal heat input and reduced distortion in the workpiece.
- Non-contact nature of laser welding eliminates the need for direct contact with the workpiece.
Limitations
- Higher equipment and maintenance costs compared to conventional welding techniques.
- Sensitivity to surface conditions, such as cleanliness and reflectivity.
- Limited effectiveness on highly reflective or transparent materials.
- Requires precise alignment and positioning of the laser beam for optimal results
Application Examples
- Automotive manufacturing, including body panels, chassis components, and engine parts.
- Aerospace industry for the production of aircraft structures, turbine components, and engine parts.
- Electronics industry for precise and clean welding of components, such as microcircuits and sensors.
- Medical device manufacturing, where precision, cleanliness, and minimal heat input are crucial.
Electron Beam Keyhole Welding
- Explanation of Electron Beam Keyhole Welding Process
Electron beam keyhole welding employs a focused stream of high-velocity electrons to create and maintain the keyhole during the welding process. The electron beam is generated in a vacuum chamber and focused onto the workpiece, delivering intense heat that vaporizes the material. The vaporized material forms a keyhole, and as the electron beam moves along the joint, the molten metal fills in behind the keyhole, resulting in the formation of the weld bead.
- Advantages and Limitations of Electron Beam Keyhole Welding Advantages
- High power density enables deep penetration and high welding speeds.
- Excellent control over the welding process parameters.
- Minimal heat input and reduced distortion in the workpiece.
- Superior weld quality with minimal defects.
- Versatility in welding various materials, including metals, alloys, and refractory materials.
Limitations
- Requires a vacuum chamber for operation, which adds complexity and cost.
- Limited to welding conductive materials due to the nature of the electron beam.
- Higher equipment and maintenance costs compared to conventional welding techniques.
- Requires careful handling and safety precautions due to the use of high-energy electron beams.
Application Examples
- Automotive and aerospace industries for joining critical structural components.
- Energy sector for welding components in nuclear power plants and oil refineries.
- Research and development of advanced materials and high-performance alloys.
- Semiconductor industry for precision welding of electronic components.
Both laser keyhole welding and electron beam keyhole welding techniques offer unique advantages and find extensive applications in various industries. The choice between these techniques depends on factors such as the specific material, desired welding characteristics, budget, and available infrastructure.
Factors Affecting Keyhole Welding
Material Considerations
The choice of materials plays a crucial role in keyhole welding. Different materials have varying melting points, thermal conductivities, and physical properties that influence the welding process. Factors to consider include:
- Material composition: Different alloys, metals, or composite materials require specific welding parameters.
- Thickness: Thicker materials may require adjustments in power, speed, and focus to ensure proper penetration.
- Reflectivity: Highly reflective materials, such as aluminum, may require modifications in the laser wavelength or beam intensity to achieve effective welding.
Welding Parameters (Power, Speed, etc.)
Various welding parameters need to be carefully controlled to achieve optimal keyhole welding results. Key parameters include:
- Power: The power level of the heat source affects the depth and width of the keyhole and the amount of heat input into the workpiece.
- Speed: Welding speed determines the amount of time the heat source spends on a particular area, influencing keyhole formation and weld bead size.
- Focus: The focal point of the heat source affects the spot size and energy concentration, directly impacting keyhole stability and penetration.
- Pulse duration: In pulsed keyhole welding, the duration and frequency of pulses influence the heat input and material solidification.
Joint Design and Preparation
Proper joint design and preparation are essential for successful keyhole welding. Considerations include:
- Joint geometry: The joint design should provide easy access for the heat source and ensure proper alignment of the workpieces.
- Gap and fit-up: The gap between the workpieces and the fit-up accuracy affect the molten metal flow and the integrity of the weld.
- Surface preparation: Clean, smooth surfaces with minimal oxides, contaminants, or surface irregularities facilitate efficient keyhole formation and weld quality.
Shielding Gas and Atmosphere
The choice of shielding gas and atmosphere around the welding area is crucial for keyhole welding. It impacts:
- Gas selection: Inert gases such as argon or helium are commonly used to prevent oxidation and provide a stable welding environment.
- Flow rate: Proper gas flow rate ensures effective shielding of the keyhole and protection of the molten metal from atmospheric contamination.
- Atmosphere control: In electron beam keyhole welding, a vacuum environment is used to prevent electron scattering and ensure efficient beam focus and penetration.
By carefully considering and controlling these factors, keyhole welding can be optimized for different materials, joint configurations, and desired welding outcomes. This ensures consistent weld quality, deep penetration, and successful weld formation.
Challenges and Solutions in Keyhole Welding
Keyhole Stability and Control
One of the challenges in keyhole welding is maintaining keyhole stability throughout the welding process. Factors such as material properties, joint design, and welding parameters can affect keyhole stability. Solutions to address this challenge include:
- Precise control of welding parameters, such as power, speed, and focus, to maintain a stable keyhole.
- Optimization of shielding gas flow and atmosphere to prevent disturbances and ensure consistent keyhole formation.
- Use of advanced monitoring and control systems to continuously monitor and adjust the welding parameters in real-time.
Defects and Quality Issues
Keyhole welding can be susceptible to certain defects and quality issues that may impact the integrity of the weld. Common defects include porosity, lack of fusion, and solidification cracks. Solutions to address these issues include:
- Proper joint design and preparation to ensure good fit-up and alignment, minimizing the chances of defects.
- Adequate shielding gas and atmosphere control to prevent oxidation and contamination, which can contribute to defects.
- Optimization of welding parameters, such as power, speed, and pulse duration, to achieve the desired weld quality and minimize defects.
- Implementation of non-destructive testing techniques, such as X-ray or ultrasonic inspection, to detect and address potential defects.
Process Optimization and Parameter Selection
Achieving optimal keyhole welding results requires careful process optimization and parameter selection. This involves finding the right balance between power, speed, focus, and other parameters to achieve the desired weld characteristics. Solutions to address this challenge include:
- Conducting process trials and experiments to determine the optimal combination of welding parameters for a specific application and material.
- Utilizing simulation and modeling techniques to predict the behavior of the keyhole and optimize welding parameters before the actual welding process.
- Continuous monitoring and feedback systems that provide real-time data on keyhole stability, weld quality, and process performance, enabling adjustments and improvements.
By addressing these challenges and implementing the appropriate solutions, keyhole welding can be effectively optimized, leading to improved weld quality, productivity, and reliability in a wide range of applications.
Future Developments in Keyhole Welding
Advancements in Heat Sources and Equipment
Future developments in keyhole welding will likely involve advancements in heat sources and equipment used for the welding process. This may include:
- Development of more efficient and powerful laser and electron beam sources, allowing for higher welding speeds and deeper penetration.
- Advancements in laser beam delivery systems and optics to improve beam quality and enhance control over the welding process.
- Integration of innovative heat sources, such as plasma arc welding, to expand the range of materials and applications suitable for keyhole welding.
- Exploration of alternative heat sources and energy generation methods to further enhance keyhole welding capabilities.
Process Monitoring and Control Technologies
The future of keyhole welding will see advancements in process monitoring and control technologies to ensure consistent and high-quality welds. This may involve:
- Integration of advanced sensors and imaging systems to provide real-time feedback on keyhole stability, weld quality, and process performance.
- Development of intelligent algorithms and machine learning techniques to analyze and interpret the data collected during the welding process.
- Implementation of closed-loop control systems that can automatically adjust welding parameters based on real-time feedback, optimizing the process and minimizing defects.
- Integration of augmented reality (AR) and virtual reality (VR) technologies to provide visual guidance and assist operators in performing keyhole welding tasks more accurately and efficiently.
Integration with Automation and Robotics
The future of keyhole welding will likely involve increased integration with automation and robotics, enabling improved efficiency and precision. This may include:
- Development of robotic systems specifically designed for keyhole welding applications, offering enhanced dexterity, precision, and repeatability.
- Integration of artificial intelligence (AI) and machine learning algorithms into robotic systems, enabling autonomous decision-making and adaptive control during the welding process.
- Implementation of collaborative robotic systems that work alongside human operators, combining the strengths of human skills and robotic precision.
- Advancements in programming and simulation tools for keyhole welding, allowing for offline programming and virtual testing of welding processes.
These future developments in keyhole welding hold the potential to revolutionize the welding industry by enabling faster, more precise, and more efficient welding processes. They will contribute to improved weld quality, expanded capabilities in joining a wide range of materials, and increased automation in manufacturing processes.
FAQs
What is keyhole in welding?
In welding, a keyhole refers to a hole or void formed at the leading edge of the weld pool when using a concentrated heat source. It is created as the intense heat melts and vaporizes the material, and the molten metal fills in behind the hole to form the weld bead.
What are the advantages of keyhole welding?
The advantages of keyhole welding include deep penetration and high welding speeds, reduced heat input and distortion, versatility in welding different materials, and minimal post-weld processing requirements. It offers efficient and reliable joining of materials, particularly in applications where strength and integrity are critical.
What is the difference between conduction welding and keyhole welding?
Conduction welding involves the transfer of heat through direct contact between the materials being welded, while keyhole welding utilizes a concentrated heat source to create a hole (keyhole) at the leading edge of the weld pool. Keyhole welding allows for deeper penetration and faster welding speeds compared to conduction welding.
What is the keyhole method used for?
The keyhole method is used for welding applications that require deep penetration and high welding speeds. It is particularly suitable for joining thick materials, as it allows the molten metal to fill in behind the keyhole, resulting in a strong and efficient weld.
Which welding is most efficient?
Keyhole welding, particularly laser keyhole welding and electron beam keyhole welding, is considered one of the most efficient welding techniques. It offers high welding speeds, deep penetration, and precise control over the welding process, making it suitable for various industrial applications.
What is the most efficient type of welding?
Laser welding, specifically laser keyhole welding, is often considered the most efficient type of welding. It provides precise control over the welding process, high welding speeds, and deep penetration capabilities. Laser welding is widely used in industries where precision and efficiency are paramount.
What’s the hardest type of welding?
The hardest type of welding is often considered to be underwater welding or welding in extreme environments, such as high-pressure or confined spaces. These conditions pose unique challenges and safety risks for welders, requiring specialized training and equipment to perform the welding tasks effectively and safely.
Why is it called keyhole?
The term “keyhole” in keyhole welding refers to the hole or void formed at the leading edge of the weld pool. The shape of this hole resembles a keyhole, similar to the keyholes found in locks. The name “keyhole” is derived from this resemblance.
What is A and Z in welding?
In welding, “A” and “Z” are commonly used to represent the angle of the joint preparation. “A” refers to the included angle between the surfaces being joined, while “Z” represents the depth of the groove or gap between the surfaces. These parameters play a significant role in determining the welding technique and settings needed to achieve a successful weld.
Conclusion
Keyhole welding is a highly efficient and versatile welding technique that offers numerous advantages in various industries. By utilizing a concentrated heat source, keyhole welding achieves deep penetration and high welding speeds, resulting in strong and reliable welds. Additionally, it minimizes heat input and distortion, making it suitable for heat-sensitive materials and intricate structures. Keyhole welding also exhibits versatility in welding different materials and requires minimal post-weld processing, saving time and resources.
Several factors influence keyhole welding, including material considerations, welding parameters, joint design and preparation, and shielding gas and atmosphere. Proper management of these factors is crucial for achieving optimal welding results and maintaining keyhole stability. Moreover, challenges in keyhole welding, such as keyhole control, defects, and process optimization, can be overcome through advancements in technology and process refinement.
The future of keyhole welding holds promising developments in heat sources and equipment, process monitoring and control technologies, and integration with automation and robotics. These advancements will enhance the capabilities, precision, and efficiency of keyhole welding, contributing to improved weld quality, increased productivity, and expanded applications.