Metal Active Gas Welding – MAG Welding
Introduction to MAG Welding
Metal Active Gas (MAG) welding, commonly known as MIG (Metal Inert Gas) welding, is a versatile and widely used welding process in various industries. This article provides a comprehensive guide to understanding and mastering the MAG welding technique. Developed in the mid-20th century, MAG welding revolutionized metal joining processes, offering efficiency, speed, and quality welds. Let’s explore the intricacies of this welding method and its applications.
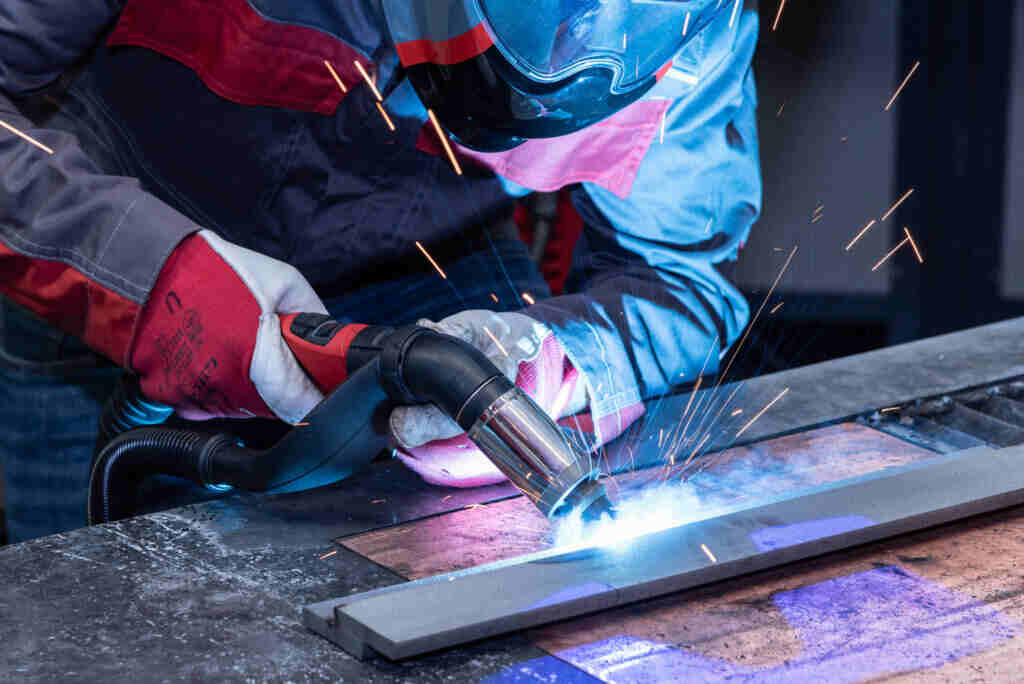
MAG Welding Process
Description of the MAG Welding Setup
- Welding Machine and Power Source: The MAG welding process requires a welding machine that provides a direct current (DC) power source. The power source supplies the necessary electrical energy to create an electric arc between the wire electrode and the workpiece.
- Shielding Gas Supply: Shielding gas is a crucial component in MAG welding. It is stored in pressurized gas cylinders and is fed through hoses to the welding gun. The choice of shielding gas depends on the material being welded and the desired welding characteristics.
- Wire Electrode Feeder: The wire electrode feeder is an essential part of the MAG welding setup. It continuously feeds the consumable electrode wire into the welding gun at a controlled rate. The wire is consumed during the welding process, providing the filler metal for the weld joint.
- Workpiece and Joint Preparation: Before starting the welding process, proper preparation of the workpiece and joint is essential. This involves cleaning the base metal to remove any dirt, rust, or contaminants that could affect the weld quality. Joint preparation may involve beveling or chamfering the edges of the metal to ensure proper penetration during welding.
Explanation of the Welding Circuit
- Electrical Connections and Current Flow: In MAG welding, the welding machine generates a direct current (DC). The electrode wire is connected to the positive terminal (anode) of the power source, while the workpiece is connected to the negative terminal (cathode). This setup establishes an electric circuit, allowing current to flow from the wire electrode to the workpiece, creating an arc and melting the wire and base metal.
- Role of the Wire Electrode and Its Composition: The wire electrode is the consumable filler metal used in MAG welding. It is typically made of solid steel, and its composition may include various alloying elements to achieve specific weld characteristics. As the electrode wire is consumed during the welding process, it forms the weld bead and joins the workpiece.
Shielding Gas in MAG Welding
- Types of Gases Used: The choice of shielding gas in MAG welding depends on the material being welded and the welding conditions. Common shielding gases include carbon dioxide (CO2), argon (Ar), and a mixture of CO2 and argon (often called C25 or 75/25 mix).
- Purpose of Shielding Gas and Its Importance: Shielding gas serves two primary purposes in MAG welding. Firstly, it protects the welding arc and molten weld pool from atmospheric contamination, such as oxygen and nitrogen, which can cause weld defects. Secondly, the composition of the shielding gas influences the weld characteristics, including penetration, bead appearance, and overall weld quality.
Advantages and Disadvantages of MAG Welding
Advantages:
- High welding speed and efficiency
- Suitable for a wide range of materials and thicknesses
- Minimal post-weld cleaning and finishing required
- Continuous wire feed enables long welds without interruptions
Disadvantages:
- Susceptible to wind interference outdoors due to the shielding gas
- May produce spatter, requiring post-weld cleanup
- Limited vertical and overhead welding capability compared to other processes, like TIG or Stick welding
Shielding Gas in MAG Welding
Shielding gases are selected based on the specific metal being welded and the desired characteristics of the weld joint. Commonly used gases include carbon dioxide (CO2), argon (Ar), and a mixture of CO2 and argon. These gases protect the welding arc, stabilize the molten pool, and influence the weld penetration and bead appearance.
Equipment and Safety
Personal Protective Equipment (PPE) for Welders
Welders must wear appropriate personal protective equipment (PPE) to safeguard themselves from potential hazards during MAG welding. The essential PPE includes:
1. Welding Helmet: A helmet with a shaded lens protects the eyes and face from harmful UV radiation and sparks.
2. Flame-Resistant Clothing: Non-flammable clothing, such as a welding jacket or apron, shields the body from sparks and molten metal splatter.
3. Welding Gloves: Heat-resistant gloves provide protection for the hands against burns and heat exposure.
4. Safety Glasses: Safety glasses with side shields offer additional eye protection from flying debris and welding sparks.
5. Safety Boots: Sturdy, fire-resistant boots protect the feet from hot metal and potential falling objects.
Safety Precautions and Guidelines
To ensure a safe working environment and prevent accidents, welders should follow specific safety precautions and guidelines:
1. Proper Ventilation and Fume Extraction:
Welding produces hazardous fumes and gases, such as welding fumes and ozone, which can be harmful when inhaled. Adequate ventilation and fume extraction systems help remove these contaminants, protecting both the welder and others in the vicinity.
2. Fire Prevention and Extinguishing Measures:
Welding involves high temperatures and sparks, making fire prevention crucial. Keep the work area clear of flammable materials and have fire extinguishers readily available. Ensure that welders know how to use fire extinguishing equipment effectively.
3. Electrical Safety and Grounding:
Welding equipment operates on high currents, posing electrical hazards. Proper grounding of welding equipment and electrical connections is essential to prevent electric shock and electrical fires.
4. Handling and Storage of Gas Cylinders:
Gas cylinders, containing shielding gases for MAG welding, should be handled with care. Securely fasten cylinders to prevent them from falling or being knocked over. Store gas cylinders in a well-ventilated, upright position, away from heat sources and flammable materials.
Welding Techniques
MAG Welding Positions
1. Flat Position:
In the flat position, the welding is performed on the upper side of the joint, and the molten weld pool spreads out horizontally. This position is the easiest for MAG welding, as gravity helps in stabilizing the weld pool. It is commonly used for fillet welds and flat plate welding.
2. Horizontal Position:
In the horizontal position, the welding is performed on the side of the joint, and the molten metal flows towards the lower side of the joint. Horizontal welding requires careful control of the welding parameters to prevent excessive weld sagging. It is used for welding joints in the horizontal plane, such as pipe welding.
3. Vertical Position:
In the vertical position, the welding is performed on the vertical surface of the joint. It requires the welder to control the molten metal flow and prevent it from sagging or dripping. Vertical welding is commonly used for joining vertical seams and walls.
4. Overhead Position:
In the overhead position, the welding is performed on the underside of the joint, and the molten metal is against gravity. Overhead welding is the most challenging position, as the weld pool tends to be less stable and may lead to weld defects. It is commonly used for welding overhead joints and ceilings.
Welding Parameters
1. Voltage and Current Settings:
Welding voltage and current settings are critical for achieving proper penetration and bead appearance. Higher voltage and current settings result in deeper penetration, while lower settings are suitable for thinner materials.
2. Wire Feed Speed:
Wire feed speed determines the amount of wire electrode deposited into the weld joint per unit of time. Proper wire feed speed ensures a stable arc and consistent bead formation.
3. Travel Speed and Manipulation Techniques:
Welders must maintain a steady travel speed to achieve uniform bead width and avoid overheating. Proper manipulation of the welding torch, such as weaving or straight-line techniques, affects bead shape and penetration.
Common Weld Joint Configurations in MAG Welding
1. Butt Joint:
The butt joint is one of the most common joint configurations in welding, where two pieces of metal are joined edge-to-edge. It requires precise alignment and edge preparation to achieve a full penetration weld.
2. Lap Joint:
In a lap joint, one piece of metal overlaps the other. Lap joints are commonly used for joining thin materials and providing increased joint strength.
3. T-Joint:
The T-joint joins one piece of metal perpendicularly to the surface of another. This joint configuration is commonly used for joining components at right angles.
Weld Bead Formation and Appearance
The weld bead’s formation and appearance are influenced by welding parameters and techniques. A well-executed MAG weld should have a smooth, even, and consistent bead with good fusion to both base metals. Proper shielding gas and travel speed contribute to achieving desired bead appearance. Weld bead appearance is also an important visual inspection factor for determining the quality of the weld joint.
Applications of MAG Welding
- MAG welding finds extensive use in industrial and manufacturing sectors.
- It is favored in the automotive industry for its efficiency in joining automotive components.
- Shipbuilding and maritime applications benefit from the speed and quality of MAG welds, ensuring the structural integrity of vessels.
- In structural steel fabrication, MAG welding is indispensable for creating robust frameworks and buildings.
- MAG welding is commonly employed in repair and maintenance work.
Troubleshooting and Defects
Like any welding process, MAG welding may encounter defects that can compromise weld quality. Common defects include porosity, incomplete fusion, cracks, and excessive spatter. Understanding the root causes of these issues and implementing appropriate measures can help prevent defects and improve weld quality. Regular visual inspection and quality control are essential to ensure adherence to industry standards and specifications.
Future Trends and Innovations
Advancements in MAG welding technology continue to shape the industry. Digital welding systems allow for precise control of welding parameters, optimizing the welding process. Pulsed MAG welding enables reduced heat input, suitable for thin materials and critical applications. Automation and robotics are transforming welding operations, enhancing productivity and consistency. Moreover, environmental considerations are driving research into more sustainable welding practices.
FAQs
1. What is MAG welding?
MAG welding stands for Metal Active Gas welding, also known as MIG (Metal Inert Gas) welding. It is a welding process where a wire electrode continuously feeds through a welding gun, creating an arc with the workpiece, while a shielding gas protects the molten weld pool from atmospheric contamination.
2. What are the advantages of MAG welding?
MAG welding offers high welding speeds, ease of use, and good weld quality. It is suitable for a wide range of materials, including mild steel, stainless steel, and aluminum.
3. Which shielding gases are used in MAG welding?
Commonly used shielding gases in MAG welding are carbon dioxide (CO2), argon (Ar), and a mixture of CO2 and argon.
4. What industries use MAG welding?
MAG welding is widely used in various industries, including automotive, shipbuilding, construction, manufacturing, and repair and maintenance.
5. How do I select the right welding parameters for MAG welding?
The welding parameters, such as voltage, current, and wire feed speed, depend on the material thickness, joint configuration, and welding position. Consult the welding procedure specifications (WPS) for guidance.
6. What safety precautions should I take during MAG welding?
Welders should wear appropriate PPE, including a welding helmet, flame-resistant clothing, gloves, and safety boots. Ensure proper ventilation and use fume extraction systems to minimize exposure to welding fumes and gases.
7. What are common welding defects in MAG welding?
Common defects include porosity, incomplete fusion, cracks, and spatter. Proper weld preparation and technique, along with appropriate shielding gas selection, can help reduce these defects.
8. Can MAG welding be automated?
Yes, MAG welding can be automated using robots and computer-controlled systems, which improves productivity and consistency in welding operations.
Conclusion
Mastering MAG welding requires a combination of technical knowledge, practical skill, and a commitment to safety. As one of the most widely used welding processes, MAG welding plays a vital role in various industries, ensuring the creation of strong and reliable metal joints. By understanding the principles, techniques, and applications of MAG welding, welders can deliver high-quality welds that meet the demands of modern manufacturing and construction. As technology continues to evolve, embracing innovative practices will drive the future of MAG welding, fostering a safer, more efficient, and sustainable welding landscape.