Multipass Welding
Introduction to Multipass Welding
Multipass welding is a sophisticated welding technique employed in various industries for joining materials of substantial thickness. Unlike single-pass welding, where the entire weld is completed in one pass, multipass welding involves layering multiple passes of weld metal to achieve the desired joint strength and integrity.
Definition and Purpose
In multipass welding, the process involves depositing successive layers of weld metal onto the workpiece, gradually building up the weld joint to the required size and strength. This method is commonly used when welding thicker materials or when the joint design necessitates a stronger bond.
The primary purpose of multipass welding is to ensure that the resulting weld exhibits sufficient strength, durability, and quality to withstand the intended service conditions. By layering multiple passes, welders can effectively distribute heat, control distortion, and mitigate the risk of defects, ultimately producing welds that meet or exceed industry standards.
Importance in Various Industries
Multipass welding plays a pivotal role across a wide range of industries, including construction, manufacturing, automotive, aerospace, and shipbuilding, among others. Its versatility and effectiveness make it indispensable for fabricating structures, components, and assemblies that require robust and reliable welds.
Fundamentals of Multipass Welding
Multipass welding encompasses a set of fundamental principles and practices essential for achieving successful welds in complex joints and thick materials. Understanding the welding process, acquiring the necessary materials and equipment, and adhering to safety precautions are crucial components of mastering multipass welding techniques.
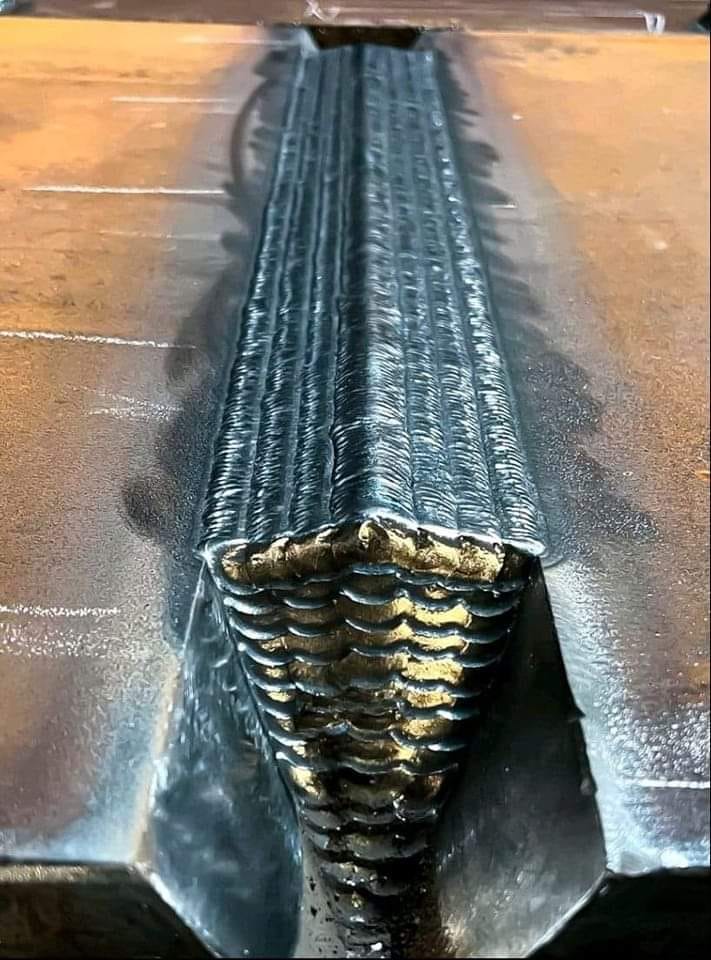
Understanding the Welding Process
At its core, multipass welding involves the deposition of multiple layers of weld metal to create a robust and durable joint. The process typically begins with the preparation of the workpiece and the selection of suitable welding parameters, such as current, voltage, and travel speed, based on the material type, thickness, and joint configuration.
During welding, each pass serves a specific purpose, whether it’s filling the joint, adding reinforcement, or controlling distortion. Welders must carefully manage heat input, arc length, and welding technique to ensure proper fusion, minimal distortion, and satisfactory weld quality.
As successive passes are deposited, welders may need to employ techniques such as weaving, oscillating, or staggered bead placement to achieve uniform coverage and penetration throughout the joint. Close attention to detail, including interpass cleaning and preparation, is essential to prevent defects and ensure the integrity of the final weld.
Materials and Equipment Needed
To perform multipass welding effectively, welders require a range of materials and equipment tailored to the specific welding process and application. This includes:
- Welding machine: A power source capable of delivering the required current and voltage for the chosen welding process, such as shielded metal arc welding (SMAW), gas metal arc welding (GMAW), or flux-cored arc welding (FCAW).
- Consumables: Electrodes, filler wires, fluxes, and shielding gases suitable for the welding process and material being welded. Proper selection of consumables is critical to achieving the desired weld properties and performance.
- Welding accessories: Protective gear, including welding helmets, gloves, jackets, and safety glasses, to safeguard against arc radiation, heat, and flying debris. Additionally, tools for joint preparation, such as grinders, wire brushes, and chipping hammers, are essential for ensuring clean, sound welds.
- Workpiece materials: Base metals and components to be joined through multipass welding. These materials may include steel, stainless steel, aluminum, and other alloys commonly used in construction, fabrication, and manufacturing.
Safety Precautions
Safety is paramount in multipass welding operations to protect welders, bystanders, and the work environment from hazards associated with arc welding processes. Key safety precautions include:
- Personal protective equipment (PPE): Welders must wear appropriate PPE, including welding helmets with protective lenses, flame-resistant clothing, gloves, and safety shoes, to shield against arc radiation, sparks, and molten metal.
- Ventilation and fume extraction: Adequate ventilation and fume extraction systems should be in place to remove welding fumes, gases, and airborne contaminants from the work area, minimizing exposure and health risks.
- Fire prevention: Welding operations can generate sparks, heat, and hot slag, increasing the risk of fires and burns. Welders should maintain a clear, clutter-free work area and have fire extinguishing equipment readily available to respond to emergencies promptly.
- Electrical safety: Welding equipment should be properly grounded, and electrical cables and connections should be inspected regularly for damage or wear. Welders must avoid contact with live electrical components and take precautions to prevent electric shock hazards.
Procedure of Multipass Welding
Multipass welding involves a systematic approach to laying down successive layers of weld metal to create strong and durable weld joints. Navigating this procedure requires careful assessment of job requirements, determining the optimal number of passes, and following a step-by-step procedure tailored to the specific welding task.
Assessing Job Requirements
Before initiating multipass welding, it’s essential to assess the requirements of the welding job thoroughly. This includes:
- Material type and thickness: Understanding the properties of the base metals being welded, such as composition, mechanical properties, and thickness, is crucial for selecting appropriate welding processes, consumables, and parameters.
- Joint design and configuration: Evaluating the joint geometry, including the type of joint (e.g., butt joint, fillet joint, lap joint), fit-up, and accessibility, helps determine the welding technique and sequence required to achieve full penetration and adequate reinforcement.
- Welding position and accessibility: Considering the welding position (e.g., flat, horizontal, vertical, overhead) and accessibility constraints helps determine the most suitable welding method and approach for achieving consistent and quality welds.
- Welding standards and specifications: Adhering to applicable welding codes, standards, and specifications, such as those provided by organizations like the American Welding Society (AWS) or the International Organization for Standardization (ISO), ensures that the welds meet the required quality and performance criteria.
Determining the Optimal Number of Passes
Determining the optimal number of passes is a critical aspect of multipass welding, as it directly influences the quality, strength, and integrity of the final weld. Factors to consider include:
- Weld joint thickness: Thicker materials typically require more passes to achieve complete fusion and adequate reinforcement. Welders must assess the thickness of the base metals and calculate the number of passes needed to achieve the desired weld size and strength.
- Welding process and parameters: The choice of welding process, along with parameters such as current, voltage, travel speed, and deposition rate, affects the rate of weld metal deposition and penetration. Adjusting these parameters enables welders to control the number of passes and optimize weld quality.
- Joint preparation and fit-up: Proper joint preparation, including beveling, edge alignment, and gap control, facilitates penetration and fusion during welding, reducing the number of passes required to fill the joint adequately.
- Welding technique and skill level: Experienced welders can optimize multipass welding by employing advanced techniques, such as weaving, oscillating, or layering, to achieve uniform coverage and penetration with fewer passes.
Step-by-Step Procedure for Multipass Welding
Once the job requirements and optimal number of passes have been determined, welders can follow a systematic procedure for multipass welding, which typically includes the following steps:
- Pre-weld preparation: Clean and prepare the base metals, removing any contaminants, oxides, or coatings that could impair weld quality. Ensure proper fit-up and alignment of the joint to facilitate welding.
- Weld sequence planning: Determine the sequence of passes based on joint configuration, welding position, and accessibility. Consider factors such as root pass welding, intermediate passes, and final cap passes to achieve full penetration and uniform reinforcement.
- Welding technique and parameters: Set up the welding equipment according to the selected welding process and parameters. Adjust current, voltage, travel speed, and wire feed rate as needed to achieve proper fusion, penetration, and bead profile.
- Pass-by-pass welding: Execute each pass according to the planned sequence, ensuring consistent deposition, penetration, and interpass cleaning as required. Monitor arc stability, weld pool behavior, and bead appearance to maintain weld quality throughout the process.
- Interpass cleaning and inspection: Clean the weld area between passes to remove slag, spatter, and other contaminants that could affect subsequent weld layers. Conduct visual inspections and, if necessary, non-destructive testing (NDT) to verify weld quality and integrity.
- Finalizing the weld: Complete the multipass welding process by applying the final pass or cap pass, ensuring proper reinforcement and surface finish. Allow the weld to cool gradually to minimize residual stresses and distortion.
Techniques for Successful Multipass Welding
Multipass welding requires a combination of techniques to ensure the quality, integrity, and consistency of the welds. From preparing the workpiece to controlling heat input and managing weld pool formation, each step plays a crucial role in achieving successful multipass welds.
Preparing the Workpiece
- Cleaning and Surface Preparation: Thoroughly clean the workpiece to remove contaminants, such as rust, oil, grease, and mill scale, which can impair weld quality. Proper surface preparation, including grinding, wire brushing, or solvent cleaning, promotes optimal weld penetration and fusion.
- Joint Preparation: Bevel or prepare the joint edges as necessary to facilitate proper weld penetration and fusion. Ensure precise fit-up and alignment to minimize gaps and inconsistencies that could lead to defects or incomplete fusion.
- Clamping and Fixturing: Securely clamp or fixture the workpieces in the desired position to maintain alignment and stability during welding. Proper fixturing helps prevent distortion and ensures uniform weld bead placement.
Choosing the Right Welding Method
- Consider Material and Joint Requirements: Select the appropriate welding method based on the material type, thickness, and joint configuration. Common multipass welding processes include shielded metal arc welding (SMAW), gas metal arc welding (GMAW), flux-cored arc welding (FCAW), and gas tungsten arc welding (GTAW), each offering unique advantages and limitations.
- Evaluate Process Efficiency and Productivity: Assess the efficiency and productivity of each welding method, considering factors such as deposition rate, travel speed, and ease of operation. Choose the method that best balances productivity with weld quality and cost-effectiveness.
- Adapt to Welding Positions: Some welding processes may be better suited for certain welding positions (e.g., flat, horizontal, vertical, overhead). Consider the positional capabilities and limitations of each welding method when selecting the most appropriate technique for multipass welding.
Managing Heat Input
- Control Welding Parameters: Adjust welding parameters, including current, voltage, travel speed, and arc length, to manage heat input and minimize the risk of overheating or underheating the weld zone. Optimize parameters for each pass to achieve proper fusion and penetration without causing excessive distortion or metallurgical changes.
- Interpass Cooling: Allow sufficient time for interpass cooling between welding passes to prevent the accumulation of excessive heat and minimize the risk of distortion, residual stresses, and weld cracking. Monitor the temperature of the workpiece and implement cooling strategies as needed to maintain weld quality.
Controlling Weld Pool and Bead Formation
- Maintain Arc Stability: Ensure consistent arc stability throughout the welding process by maintaining proper arc length, electrode angle, and travel speed. A stable arc promotes uniform heat distribution and weld pool control, resulting in smooth, consistent bead formation.
- Adjust Welding Technique: Modify welding technique, such as weaving, oscillating, or stringer beads, to achieve the desired weld bead shape, size, and reinforcement. Adapt the technique to suit the joint geometry, material thickness, and welding position for optimal results.
- Monitor Weld Pool Behavior: Pay close attention to weld pool behavior, including size, shape, and fluidity, to detect and correct potential defects, such as lack of fusion, undercut, or excessive reinforcement. Adjust welding parameters and technique as needed to maintain proper weld pool control and bead formation.
Common Challenges and Solutions
Multipass welding presents various challenges that can impact weld quality and integrity. Understanding these challenges and implementing effective solutions is essential for achieving successful multipass welds.
Distortion and Warping
Challenges:
- Distortion and warping occur due to the uneven distribution of heat during welding, leading to changes in the shape and dimensions of the workpiece.
- Thicker materials and multipass welding exacerbate the risk of distortion, particularly in materials with high thermal expansion coefficients.
Solutions:
- Use proper fixturing and clamping techniques to minimize movement and distortion during welding.
- Implement preheat and post-weld heat treatment processes to control residual stresses and reduce distortion.
- Employ welding sequences that alternate between different sections of the joint to balance heat input and minimize distortion.
Lack of Fusion
Challenges:
- Lack of fusion results from inadequate melting and bonding between the weld metal and base material, leading to weak or incomplete welds.
- Factors such as improper welding parameters, insufficient cleaning of joint surfaces, and poor joint fit-up contribute to lack of fusion.
Solutions:
- Optimize welding parameters, including current, voltage, travel speed, and arc length, to achieve proper penetration and fusion.
- Ensure thorough cleaning and preparation of joint surfaces to remove contaminants and promote metallurgical bonding.
- Improve joint fit-up and alignment to ensure intimate contact between the base metals and facilitate fusion.
Porosity and Inclusions
Challenges:
- Porosity and inclusions are defects characterized by the presence of gas pockets or foreign particles within the weld metal, compromising its integrity and mechanical properties.
- These defects can result from inadequate shielding gas coverage, improper welding technique, or contamination of consumables.
Solutions:
- Use high-quality welding consumables, including electrodes, filler wires, and shielding gases, to minimize the risk of contamination and porosity.
- Ensure proper gas shielding coverage by maintaining appropriate gas flow rates, nozzle positioning, and wind protection during welding.
- Implement proper cleaning and preheating procedures for materials prone to contamination, such as aluminum and stainless steel, to reduce the likelihood of inclusion defects.
Tips and Tricks for Multipass Welding
Multipass welding demands advanced techniques and strategies to overcome challenges and achieve superior weld quality. From optimizing tack welding strategies to leveraging welding positions and utilizing backing bars and fluxes, these tips and tricks empower welders to elevate their multipass welding skills.
A. Tack Welding Strategies
Tack Welding Challenges:
- Improper tack weld placement can lead to misalignment and distortion of the joint during multipass welding.
- Insufficient tack weld strength may result in joint misalignment or separation during welding operations.
Effective Tack Welding Strategies:
- Prioritize proper joint alignment and fit-up before tack welding to ensure accurate positioning during multipass welding.
- Use sufficient tack welds to securely hold the joint in place while allowing for easy removal and minimal distortion.
- Employ tack weld removal techniques, such as grinding or gouging, to eliminate tack welds without compromising the integrity of the final weld joint.
B. Welding Positions and Angles
Optimizing Welding Positions:
- Different welding positions (e.g., flat, horizontal, vertical, overhead) present unique challenges and opportunities for multipass welding.
- Improper positioning can result in inadequate penetration, inconsistent bead formation, and increased difficulty in controlling weld pool behavior.
Effective Welding Position Strategies:
- Select the most suitable welding position based on joint orientation, accessibility, and desired weld characteristics.
- Adjust welding parameters and techniques to accommodate changes in welding position, ensuring consistent weld quality and penetration.
- Practice proper body positioning and torch manipulation to maintain control and stability while welding in various positions.
C. Utilizing Backing Bars and Fluxes
Benefits of Backing Bars and Fluxes:
- Backing bars provide support and containment for molten weld metal, promoting proper penetration and preventing weld sagging or distortion.
- Fluxes facilitate shielding and slag formation, reducing the risk of oxidation and contamination while improving weld cleanliness and integrity.
Effective Utilization Strategies:
- Select backing bars with suitable materials and dimensions to match the welding application and joint configuration.
- Position backing bars securely to maintain proper root opening and alignment throughout the welding process.
- Apply fluxes judiciously to ensure adequate coverage and protection of the weld zone while minimizing post-weld cleaning requirements.
Applications and Case Studies
Multipass welding finds extensive use in a diverse range of real-world applications, from structural welding projects to pipe welding applications and critical industries such as shipbuilding and aerospace. Let’s explore some examples and case studies showcasing the versatility and importance of multipass welding in various fields.
A. Structural Welding Projects
Example: Bridge Construction
Case Study: The construction of large-scale bridges often involves multipass welding to join structural steel components and ensure the structural integrity and longevity of the bridge. Welders utilize multipass welding techniques to fabricate bridge girders, trusses, and support structures, employing processes such as shielded metal arc welding (SMAW) or gas metal arc welding (GMAW) for efficient and reliable welds.
Benefits: Multipass welding enables welders to join thick steel plates and sections, accommodating the demanding load requirements and environmental conditions experienced by bridges. By achieving consistent and high-quality welds, multipass welding contributes to the safety, durability, and serviceability of bridges, ensuring their functionality and longevity for decades to come.
B. Pipe Welding Applications
Example: Oil and Gas Pipelines
Case Study: Multipass welding is extensively used in the construction of oil and gas pipelines, where weld quality and integrity are paramount for ensuring the safe and efficient transportation of hydrocarbons over long distances. Welders employ techniques such as gas tungsten arc welding (GTAW) or shielded metal arc welding (SMAW) to join pipe sections, incorporating multiple passes to achieve full penetration and meet industry standards.
Benefits: Multipass welding techniques enable welders to produce high-strength and leak-tight welds in various pipeline materials, including carbon steel, stainless steel, and alloy steels. By adhering to stringent welding procedures and inspection protocols, multipass welding ensures the reliability and integrity of pipeline welds, minimizing the risk of leaks, failures, and environmental damage.
C. Shipbuilding and Aerospace Industry Examples
Example: Vessel Construction
Case Study: In the shipbuilding industry, multipass welding plays a vital role in fabricating hulls, decks, bulkheads, and other structural components of marine vessels. Welders utilize advanced multipass welding techniques, such as flux-cored arc welding (FCAW) or submerged arc welding (SAW), to join thick steel plates and sections, ensuring the strength, durability, and watertightness of ship structures.
Benefits: Multipass welding enables shipbuilders to achieve robust and reliable welds capable of withstanding the harsh marine environment, including corrosion, fatigue, and dynamic loads. By employing multipass welding processes and adhering to classification society rules and standards, shipyards ensure the seaworthiness and operational performance of vessels, contributing to maritime safety and security worldwide.
Example: Aircraft Manufacturing
Case Study: In the aerospace industry, multipass welding is utilized in the fabrication of aircraft components, such as fuselage sections, wings, and engine mounts, where lightweight materials and stringent quality requirements are critical. Welders employ precision welding techniques, including laser beam welding (LBW) or electron beam welding (EBW), to join aerospace alloys and composites, incorporating multiple passes to achieve aerospace-grade welds.
Benefits: Multipass welding techniques enable aerospace manufacturers to produce high-strength and defect-free welds in lightweight materials, ensuring the structural integrity, performance, and safety of aircraft components. By adhering to aerospace welding standards and specifications, manufacturers deliver aircraft structures and assemblies that meet the rigorous demands of flight operations and regulatory authorities.
FAQs
What materials can be welded using multipass welding?
Multipass welding can be used with a wide range of materials, including carbon steel, stainless steel, aluminum, and exotic alloys.
How does multipass welding differ from single-pass welding?
Unlike single-pass welding, which involves making a single weld pass, multipass welding requires multiple passes over the joint to achieve the desired weld profile and properties.
Is multipass welding suitable for thin materials?
While multipass welding is commonly used for thicker materials, it can also be applied to thinner materials with proper control of welding parameters and techniques.
What are the common defects encountered in multipass welding?
Common defects in multipass welding include porosity, lack of fusion, cracks, and undercutting, which can be minimized through proper welding procedures and inspection.
How can I ensure the safety of multipass welding operations?
Ensuring proper ventilation, using appropriate PPE, implementing safety protocols, and providing training to personnel are essential for maintaining a safe working environment during multipass welding.
Conclusion
Multipass welding is a versatile and effective technique for joining metals, offering enhanced strength, durability, and weld quality. By understanding the process, addressing challenges, and implementing safety measures, multipass welding can deliver reliable and high-quality welded joints across various applications.