What is Percussion Welding?
Introduction
Percussion welding is a specialized welding technique that involves the joining of two workpieces through the application of high pressure and electrical energy. It is a solid-state welding process, meaning that it does not involve the melting of the base metals. Instead, percussion welding relies on the rapid generation of heat through the conversion of kinetic energy into thermal energy, resulting in the formation of a strong weld bond.
Percussion welding is widely recognized for its ability to produce high-quality weld joints with excellent mechanical strength and durability. It offers several advantages over traditional fusion welding methods, such as minimal material distortion, faster welding speeds, and the absence of filler materials. These advantages make percussion welding particularly suitable for applications where strong, reliable, and efficient welds are required.
The importance and applications of percussion welding span across various industries. In the automotive and aerospace sectors, percussion welding is used for joining components such as fuel lines, brake lines, exhaust systems, and engine parts. Its ability to withstand vibrations and harsh operating conditions makes it a preferred choice in these industries. In the electrical and electronic sectors, percussion welding is employed for joining electrical connectors, terminals, and wires, ensuring reliable electrical conductivity. Additionally, percussion welding finds applications in plumbing and pipe fittings, where it enables leak-free connections in plumbing systems and industrial piping networks.
The versatility of percussion welding also extends to other industrial and manufacturing sectors. It is utilized in the fabrication of pressure vessels, heat exchangers, and storage tanks, where strong welds are crucial for ensuring structural integrity. In the construction industry, percussion welding is employed for joining structural elements, such as beams, columns, and trusses, contributing to the stability and strength of buildings and infrastructure. Moreover, percussion welding is applied in the production of machinery and equipment, including agricultural machinery, industrial tools, and automotive assemblies.
Basic Principles of Percussion Welding
Description of the Welding Process
Percussion welding, also known as impact welding or high-velocity welding, is a solid-state welding technique that involves the joining of two metal workpieces through the application of pressure and electrical energy. The process can be broken down into the following steps:
1. Preparation: The workpieces to be welded are prepared by cleaning their surfaces and ensuring proper alignment. This is crucial for achieving a successful weld.
2. Contact and Pressure Application: The two workpieces are brought into contact under pressure. The pressure can be applied by hydraulic systems, pneumatic systems, or mechanical mechanisms, depending on the specific equipment used.
3. Electrical Energy Transfer: Once the workpieces are in contact, an electrical current is passed through them. The electrical energy helps facilitate the welding process by generating heat at the interface of the workpieces.
4. High-Velocity Impact: Following the application of electrical energy, one of the workpieces is accelerated rapidly towards the other using a mechanical driver. This high-velocity impact generates a localized temperature rise at the interface due to the conversion of kinetic energy into heat energy.
5. Heat Generation and Weld Formation: The rapid collision and subsequent heat generation cause the material at the interface to soften and reach a semi-molten state. As the impacting workpiece rebounds, the softened material flows together, forming a metallurgical bond between the two workpieces.
6. Cooling and Solidification: After the impact, the heat quickly dissipates, and the molten material solidifies, resulting in a solid and strong weld joint. The cooling rate and solidification process can significantly affect the microstructure and mechanical properties of the weld.
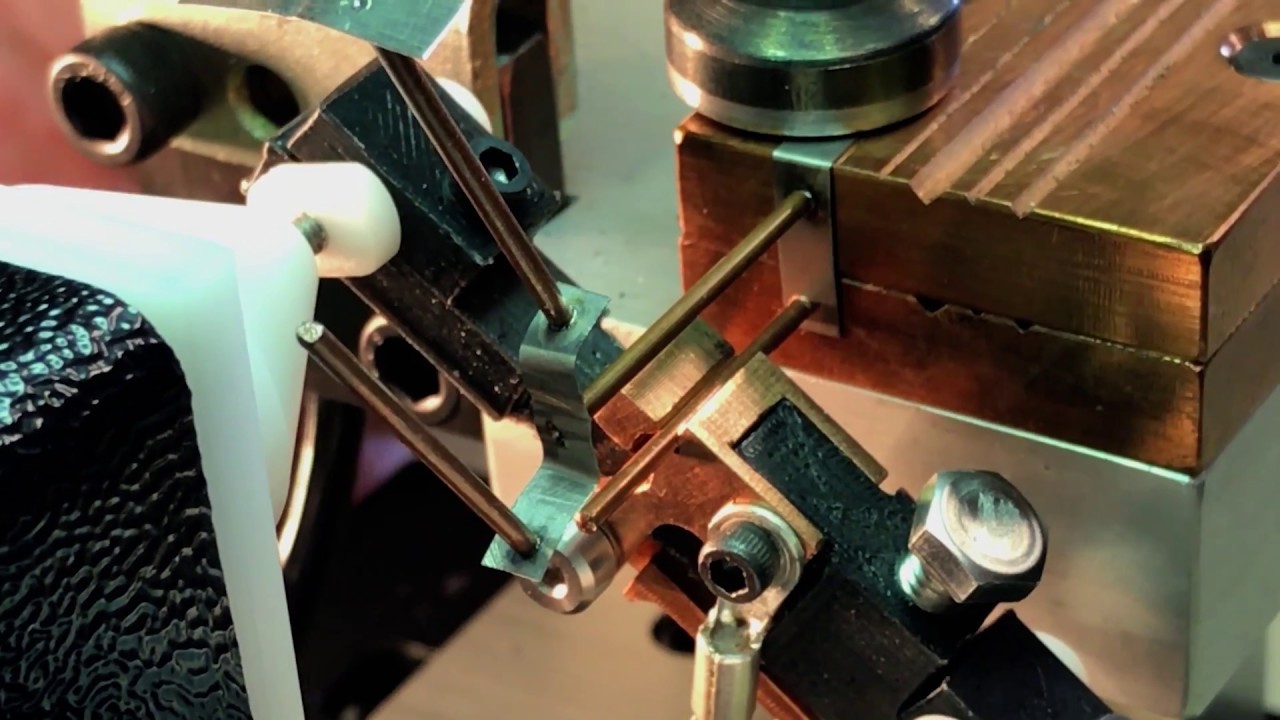
Key Components and Equipment Used in Percussion Welding
1. Welding Machine: A percussion welding machine consists of various components, including a power supply, a control unit, and mechanical drivers. The power supply delivers the necessary electrical energy to create the weld, while the control unit regulates process parameters such as pressure, current, and timing. Mechanical drivers are responsible for providing the high-velocity impact.
2. Workpiece Fixturing: Proper alignment and clamping of the workpieces are essential for achieving accurate and reliable welds. Fixtures or clamps are used to hold the workpieces securely in place during the welding process, ensuring precise alignment and contact.
3. Electrodes: Electrodes are used to apply pressure and conduct electrical current to the workpieces. They are typically made of a conductive material, such as copper or tungsten, and are designed to withstand the high forces and temperatures involved in percussion welding.
Explanation of the Energy Transfer Mechanism
The energy transfer mechanism in percussion welding involves the conversion of electrical energy and kinetic energy into heat energy. This conversion occurs through a combination of electrical resistance heating and mechanical impact:
1. Electrical Energy Transfer: When an electrical current passes through the workpieces, resistance within the materials generates heat. This localized heating occurs primarily at the interface between the workpieces, where the electrical contact is established.
2. Kinetic Energy Transfer: The mechanical driver accelerates one of the workpieces towards the other, resulting in a high-velocity impact. This impact releases a significant amount of kinetic energy, which is converted into heat energy upon collision.
The combination of electrical resistance heating and mechanical impact leads to rapid and intense heating at the interface, causing the material to soften and form a weld bond. The energy transfer mechanism is carefully controlled by adjusting process parameters such as pressure, current, and impact velocity to ensure optimal weld quality and integrity.
Percussion Welding Process
Preparation and Alignment of the Workpieces
Before initiating the percussion welding process, proper preparation and alignment of the workpieces are crucial for a successful weld. The steps involved in this stage include:
1. Cleaning: The surfaces of the workpieces that will be joined are thoroughly cleaned to remove any dirt, grease, oxides, or contaminants. This ensures optimal contact and promotes strong weld formation.
2. Surface Preparation: In some cases, the surfaces may require additional preparation, such as machining or bevelling, to ensure proper fit-up and alignment. This step helps maximize the contact area between the workpieces, facilitating efficient energy transfer during welding.
3. Alignment: The workpieces are carefully aligned to ensure precise contact and parallelism between the mating surfaces. Proper alignment is crucial for achieving a uniform weld and preventing any misalignment or offset that may compromise the strength and integrity of the joint.
Application of Pressure and Electrical Energy
Once the workpieces are prepared and aligned, the percussion welding process proceeds with the application of pressure and electrical energy. This stage involves the following steps:
1. Clamping: The workpieces are securely clamped or held in place using fixtures or clamping mechanisms. This ensures that the workpieces remain in contact and maintain proper alignment throughout the welding process.
2. Pressure Application: A predetermined pressure is applied to the workpieces using hydraulic systems, pneumatic systems, or mechanical mechanisms. The applied pressure ensures intimate contact between the mating surfaces, promoting efficient energy transfer and facilitating the formation of a strong weld.
3. Electrical Current Application: An electrical current is then passed through the workpieces. The electrical current flows through the conductive electrodes, which are in contact with the workpieces. The electrical energy is dissipated as heat due to the resistance encountered within the materials, primarily at the interface between the workpieces.
Generation of Heat and Formation of a Weld Bond
The application of pressure and electrical energy leads to the generation of heat at the interface of the workpieces, resulting in the formation of a weld bond. The process unfolds as follows:
1. Heat Generation: The electrical resistance within the workpieces causes localized heating at the interface. This leads to the softening and partial melting of the material in the vicinity, facilitating the formation of a metallurgical bond.
2. Rapid Heating and Cooling: The high-velocity impact occurs, resulting in a rapid and intense release of kinetic energy. This impact further increases the temperature at the interface, aiding in the softening and fusion of the material. However, the duration of heating is extremely short, as the energy is quickly dissipated upon impact, allowing for rapid cooling and solidification of the material.
3. Weld Formation: As the softened material solidifies, it forms a metallurgical bond between the workpieces. The bond is typically characterized by atomic diffusion and mechanical interlocking, resulting in a strong and durable joint.
Control of Process Parameters for Optimal Results
To achieve optimal results in percussion welding, various process parameters must be controlled and optimized. These parameters include:
1. Pressure: The applied pressure influences the contact between the workpieces, affecting the heat generation and the formation of the weld. Proper pressure control ensures sufficient deformation and contact at the interface while avoiding excessive deformation that could lead to material expulsion or distortion.
2. Electrical Current: The magnitude and duration of the electrical current passing through the workpieces impact the heat generation. Controlling the electrical current allows for precise control of the temperature rise, ensuring sufficient melting and bonding without overheating or damaging the workpieces.
3. Impact Velocity: The velocity at which one workpiece impacts the other significantly affects the heat generation and resulting weld quality. Optimizing the impact velocity ensures efficient energy transfer and proper material deformation, enhancing the weld quality.
Advantages of Percussion Welding
Percussion welding offers several advantages over other welding techniques, making it a preferred choice in various industries. The key advantages of percussion welding are as follows:
Strong and Durable Weld Joints
Percussion welding produces weld joints that are known for their exceptional strength and durability. The solid-state nature of the process eliminates the need for a filler material, resulting in a weld that consists solely of the base metal. This absence of a fusion zone and the avoidance of potential fusion defects ensure the integrity and reliability of the joint. The metallurgical bond formed during percussion welding exhibits high mechanical strength, enabling the welded components to withstand demanding operational conditions, such as vibration, stress, and temperature fluctuations.
Minimal Material Deformation or Distortion
Compared to other welding methods, percussion welding minimizes material deformation and distortion. The localized heating and rapid cooling characteristic of this process result in a narrow heat-affected zone (HAZ), which reduces the risk of warping or damage to the surrounding material. This is particularly beneficial when working with thin or delicate materials that are susceptible to distortion or dimensional changes during welding. The ability to maintain the original shape and dimensional accuracy of the workpieces is crucial in applications where precision and aesthetics are important.
Versatility and Suitability for Various Materials
Percussion welding is highly versatile and can be used to join a wide range of materials and alloys. It is applicable to metals such as aluminum, copper, steel, and titanium, among others. Additionally, percussion welding allows for the joining of dissimilar materials, including combinations of different metals or alloys. This versatility is valuable in industries where the combination of different materials is required to achieve desired properties, such as in the automotive and aerospace sectors. Percussion welding’s compatibility with diverse materials expands its applications across different industries.
High Welding Speed and Efficiency
Percussion welding is known for its high welding speed and efficiency. The process can be completed in a fraction of a second, making it significantly faster than many other welding techniques. This rapid welding speed translates into increased productivity and shorter production cycles. Additionally, percussion welding does not require the use of consumables or filler materials, reducing material waste and associated costs. The efficiency of the process is further enhanced by its ability to create strong and reliable weld joints in a single operation, eliminating the need for additional post-welding treatments or inspections.
In summary, the advantages of percussion welding include the production of strong and durable weld joints, minimal material deformation or distortion, versatility in working with various materials, and high welding speed and efficiency. These advantages make percussion welding a preferred choice in industries where strength, precision, and productivity are paramount.
Limitations and Challenges of Percussion Welding
Percussion welding, despite its advantages, also has certain limitations and challenges that need to be considered. These include:
Restrictions on Materials and Thicknesses
Percussion welding is most suitable for certain materials and thickness ranges. While it can join a wide range of metals and alloys, some materials may not be well-suited for this welding technique. For example, materials with significantly different melting points or those prone to heat-affected zone (HAZ) cracking may pose challenges during welding. Additionally, percussion welding is more effective for moderate to thick material thicknesses, as thin materials may experience excessive deformation or burn-through during the process. Therefore, careful consideration of material selection and thickness is necessary to ensure successful welds.
Requirement for Precise Alignment
Achieving precise alignment of the workpieces is crucial for successful percussion welding. Any misalignment or offset between the mating surfaces can negatively impact the quality and integrity of the weld joint. Proper alignment requires meticulous setup and fixturing to ensure that the workpieces are in intimate contact and parallel to each other. Any deviation in alignment can result in incomplete fusion, weak bonds, or even joint failure. Therefore, the requirement for precise alignment adds complexity to the welding process and necessitates careful attention to detail.
Potential for Surface Damage or Contamination
During percussion welding, the workpiece surfaces come into contact with each other under pressure. This contact can result in surface damage, such as scratches, indentations, or marring. Surface damage can weaken the material or create stress concentration points that may compromise the integrity of the weld joint. Additionally, any contamination present on the workpiece surfaces, such as dirt, oils, or oxides, can negatively affect the quality of the weld. Thorough surface cleaning and proper handling techniques are necessary to minimize the risk of surface damage or contamination.
Cost Considerations and Specialized Equipment
Percussion welding requires specialized equipment and machinery, which can be costly to acquire and maintain. The high-speed impact drivers, power supplies, and control units specific to percussion welding may require substantial investment. Additionally, the process may require skilled operators who are trained in the setup, operation, and maintenance of the equipment. These factors contribute to the overall cost of implementing percussion welding in industrial applications. Therefore, cost considerations and the availability of suitable equipment and trained personnel need to be evaluated when considering the feasibility of percussion welding for a specific project.
Despite these limitations and challenges, percussion welding remains a valuable welding technique in various industries. Through careful material selection, precise alignment, surface preparation, and cost evaluation, many of these limitations can be mitigated or overcome, allowing for successful and efficient percussion welding operations.
Applications of Percussion Welding
Percussion welding finds widespread application in various industries due to its ability to produce strong and reliable weld joints. Some notable applications include:
Automotive and Aerospace Industries
Percussion welding is extensively utilized in the automotive and aerospace sectors. In automotive manufacturing, it is employed for joining components such as fuel lines, brake lines, exhaust systems, and engine parts. The high strength and durability of percussion welds make them well-suited for withstanding the rigorous operating conditions and vibrations experienced in vehicles. In the aerospace industry, percussion welding is used for joining components in aircraft structures, fuel systems, hydraulic systems, and engine components. The lightweight yet robust weld joints produced by percussion welding contribute to the overall performance and safety of aerospace systems.
Electrical and Electronic Components
Percussion welding is employed in the production of electrical and electronic components where reliable electrical conductivity and mechanical strength are essential. It is commonly used for joining electrical connectors, terminals, and wires. The solid-state welding process ensures a low-resistance electrical connection while maintaining the integrity of the conductive materials. The minimal heat-affected zone (HAZ) and lack of filler material help preserve the electrical properties of the components, making percussion welding suitable for high-performance electrical systems, such as those found in power distribution, telecommunications, and electronic devices.
Plumbing and Pipe Fittings
Percussion welding is also utilized in the plumbing and pipe fitting industries. It is employed for joining pipes, tubes, and fittings made of materials such as copper, stainless steel, or brass. The strong weld joints produced by percussion welding ensure leak-free connections, making it suitable for plumbing systems, heating and cooling systems, and industrial piping networks. The efficiency and speed of the welding process contribute to shorter installation times and improved productivity in plumbing and pipe fitting applications.
Other Industrial and Manufacturing Sectors
Percussion welding finds applications across various other industrial and manufacturing sectors. It is employed in the fabrication of pressure vessels, heat exchangers, and storage tanks, where strong and durable welds are necessary to ensure structural integrity. In the construction industry, percussion welding is used for joining structural elements, such as beams, columns, and trusses, as well as in the fabrication of bridges and infrastructure. Additionally, percussion welding is utilized in the production of machinery and equipment, such as agricultural machinery, industrial tools, and automotive assemblies.
Comparison with Other Welding Techniques
Percussion welding possesses distinct characteristics that set it apart from other welding techniques. A comparison with fusion welding methods and resistance welding techniques reveals the unique advantages and considerations of percussion welding.
Contrast with Fusion Welding Methods
Fusion welding methods, such as arc welding and gas welding, involve the melting and subsequent solidification of base metals and often require the use of a filler material. When compared to percussion welding, fusion welding methods exhibit the following contrasts:
1. Heat Input: Fusion welding methods introduce a substantial amount of heat into the workpiece, resulting in a larger heat-affected zone (HAZ). In contrast, percussion welding minimizes the heat input due to its rapid heating and cooling cycle, resulting in a narrow HAZ and reduced thermal distortion.
2. Filler Material: Fusion welding methods typically require the use of filler materials to bridge gaps between workpieces and promote metallurgical bonding. In percussion welding, the absence of filler material contributes to the formation of a weld joint consisting solely of the base metals, eliminating the need for additional material and reducing the risk of incompatibility or contamination.
3. Joint Strength: Percussion welding often produces stronger weld joints compared to fusion welding methods due to the absence of fusion defects, such as porosity or incomplete penetration. The solid-state nature of percussion welding results in metallurgical bonds that exhibit high mechanical strength, making it particularly suitable for applications requiring strong and durable welds.
Comparison with Resistance Welding Techniques
Resistance welding techniques, such as spot welding and seam welding, rely on the localized heating and subsequent coalescence of materials under pressure. When compared to percussion welding, resistance welding techniques demonstrate the following comparisons:
1. Energy Transfer Mechanism: In resistance welding, the heat is primarily generated by passing an electrical current through the workpieces, causing resistance and localized heating at the interface. Percussion welding, on the other hand, combines the application of pressure with a rapid impact, resulting in mechanical deformation and the conversion of kinetic energy into heat.
2. Joint Configuration: Resistance welding techniques are often used for spot or seam welding, where the welds are typically localized and relatively small in size. Percussion welding, with its high-speed impact and larger contact area, enables the formation of broader welds and is particularly advantageous for joining larger components or areas requiring a wider bond.
3. Material Compatibility: Percussion welding offers greater flexibility in joining dissimilar materials compared to some resistance welding techniques. While resistance welding techniques are commonly used for similar materials with good electrical conductivity, percussion welding allows for the joining of dissimilar materials, including combinations of metals and alloys with varying properties.
Future Developments and Trends in Percussion Welding
Percussion welding, like many other welding techniques, continues to evolve and adapt to meet the changing needs of industries. Several future developments and trends are expected to shape the future of percussion welding:
Advancements in Process Automation and Control
The future of percussion welding is likely to see significant advancements in process automation and control. Automation technologies, such as robotics and advanced control systems, can enhance the precision, repeatability, and efficiency of percussion welding processes. Automated systems can ensure accurate alignment of workpieces, consistent application of pressure and energy, and real-time monitoring of process parameters. These advancements will not only improve the quality and reliability of weld joints but also increase productivity and reduce the dependence on manual labor.
Integration with Additive Manufacturing Technologies
Percussion welding has the potential to be integrated with additive manufacturing technologies, such as 3D printing. Additive manufacturing enables the fabrication of complex geometries and customized components. By combining additive manufacturing with percussion welding, it may be possible to produce multi-material structures with localized weld joints, eliminating the need for separate assembly steps. This integration can open up new possibilities for creating high-performance, lightweight, and customized products in industries such as aerospace, automotive, and medical.
Exploration of New Materials and Applications
As industries continue to seek innovative solutions, percussion welding is expected to expand its capabilities by exploring new materials and applications. Research and development efforts will focus on understanding the behavior of unconventional materials, such as composites and advanced alloys, during percussion welding. The exploration of new materials will enable the application of percussion welding in emerging sectors, including renewable energy, electronics, and wearable technology. Additionally, advancements in joining dissimilar materials will open up opportunities for creating hybrid structures with tailored properties for specific applications.
FAQs
What is percussion welding used for?
Percussion welding is used for joining various components in industries such as automotive, aerospace, electrical, plumbing, and manufacturing. It is commonly applied in the fabrication of fuel lines, brake lines, exhaust systems, engine parts, electrical connectors, terminals, pipes, pressure vessels, and structural elements. Its strong and reliable weld joints make it suitable for applications that require durability and resistance to vibrations and harsh operating conditions.
What is percussion welding limited to?
Percussion welding is limited to certain materials and thicknesses. It is typically used for joining similar or compatible metals and alloys, such as stainless steel, copper, brass, and aluminum. It may not be suitable for dissimilar material combinations or extremely thick workpieces where the impact and pressure may not be sufficient to achieve proper bonding.
Which welding is pressure welding?
Percussion welding falls under the category of pressure welding. Pressure welding encompasses welding techniques that rely on the application of pressure to create a weld bond. In percussion welding, pressure is applied through a rapid impact between the workpieces, resulting in the deformation and bonding of the materials.
What are all 4 types of welding?
The four main types of welding are:
– Arc Welding: It uses an electric arc to generate heat and melt the base metals, while a filler material is often used to fill the joint.
– Gas Welding: It involves the use of a gas flame (such as acetylene) to generate heat and melt the base metals, with or without the use of a filler material.
– Resistance Welding: It utilizes the resistance to electric current flow in the workpieces to generate localized heat, allowing for the joining of materials under pressure.
– Percussion Welding: It is a solid-state welding technique that combines pressure and electrical energy to create a weld bond without melting the base metals.
Why are percussion instruments used?
Percussion instruments are used for various reasons, including providing rhythm, creating different sound effects, and enhancing musical compositions. They contribute to the overall musical experience by adding texture, dynamics, and a rhythmic foundation to a piece of music.
What tools are used during percussion?
Percussion instruments encompass a wide range of tools, including drums (such as snare drums, bass drums, and tom-toms), cymbals, tambourines, maracas, xylophones, gongs, and many others. Each instrument produces distinctive sounds and is played using different techniques, such as striking, shaking, or scraping.
Which welding is strongest?
The strength of a weld depends on various factors, including the welding technique used, the materials being joined, and the welding parameters. Different welding techniques can produce strong welds depending on the application. For example, processes like electron beam welding and friction stir welding are known for producing high-strength welds in certain materials and applications. However, it is important to select the appropriate welding technique based on the specific requirements of the project to ensure the desired strength of the weld joint.
What is pressure vs non-pressure welding?
Pressure welding refers to welding techniques that involve the application of pressure to create a weld bond. Examples of pressure welding include percussion welding, resistance welding, and forge welding. Non-pressure welding, on the other hand, refers to welding techniques that do not rely on the application of pressure to join materials. Fusion welding methods, such as arc welding and gas welding, are examples of non-pressure welding techniques where heat is primarily used to melt and fuse the base metals together.
What are the 3 types of welding?
The three commonly recognized types of welding are:
– Fusion Welding: It involves the melting of the base metals to create a weld joint. Examples include arc welding, gas welding
Conclusion
Percussion welding is a versatile and efficient joining technique that offers numerous advantages in various industries. Its solid-state nature, strong weld joints, minimal material distortion, and compatibility with different materials make it a preferred choice for many applications. The percussion welding process, with its unique combination of pressure and electrical energy, facilitates the rapid generation of heat, leading to the formation of reliable weld bonds.
Throughout this discussion, we have examined the basic principles and process of percussion welding, its advantages, limitations, and comparisons with other welding techniques. We have also explored the future developments and trends in percussion welding, including advancements in automation and control, integration with additive manufacturing technologies, and the exploration of new materials and applications.
The continuous advancement of percussion welding, driven by research, innovation, and industry demands, will further enhance its capabilities and broaden its range of applications. Process automation and control will improve the precision, repeatability, and efficiency of percussion welding operations. Integration with additive manufacturing technologies will enable the creation of complex multi-material structures with localized weld joints. Exploration of new materials and applications will push the boundaries of what can be achieved with percussion welding.
In conclusion, percussion welding is a powerful joining technique that offers strength, reliability, and versatility. Its unique features and advantages make it a valuable tool in industries such as automotive, aerospace, electrical, plumbing, and more. As technology advances and new challenges arise, percussion welding will continue to evolve and contribute to the advancement of manufacturing and engineering practices. Its future holds exciting possibilities, ensuring that it remains a key process in the realm of welding.