Pipe Weld Failures: Causes and Prevention
Introduction
Welding is an intricate skill that demands precision, technique, and experience. When done right, welds form the backbone of metal constructions, holding up buildings, machinery, pipelines, and countless other structures. However, when a weld fails, it can lead to catastrophic consequences, especially in critical systems like pipelines, industrial structures, or pressure vessels. The image above is a clear example of a weld failure that many experienced welders might recognize — a crack running through a pipe joint, showing a complete breach in integrity.
This kind of damage is more than just an eyesore; it’s a potential hazard. But what exactly causes such failures? Is it the material? The welding technique? Or perhaps some unseen internal stress that has silently built up over time? This article delves deep into the various causes of pipe weld failures and explores methods to prevent them. We’ll cover the technicalities, share insights from experts, and provide a comprehensive guide to ensuring your welds stay solid and safe.
By understanding the reasons behind these failures, welders can not only improve their craftsmanship but also enhance the safety and longevity of the systems they work on. Let’s explore some of the most common reasons for weld failures, particularly in pipes, and discuss how to prevent them.
1. Understanding Weld Failures: What Does It Mean?
When we talk about “weld failures,” we refer to instances where a weld doesn’t meet the required strength or durability standards. This failure can be seen through visible cracks, incomplete fusion, or other signs of structural weakness. In some cases, the failure is internal and might not be immediately visible, making it even more dangerous.
Weld failures are especially critical in pipelines, which often carry hazardous materials, operate under high pressure, or are exposed to harsh environments. A single crack in a pipe weld could result in gas leaks, contamination, or even explosions.
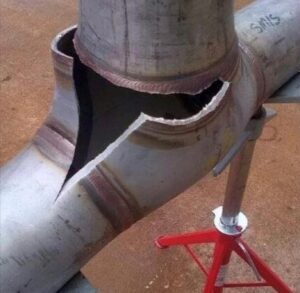
A comprehensive understanding of why welds fail is the first step toward prevention. Broadly, weld failures/ weld defects can be categorized into several types, each with unique characteristics and causes:
- Cracks – The most common and serious type of failure, often caused by internal stress or improper cooling.
- Porosity – Small holes in the weld metal due to trapped gas, compromising the weld’s strength.
- Incomplete Fusion or Penetration – When the weld metal does not fuse properly with the base metal.
- Distortion – Deformation of the material due to improper heat control.
- Burn-Through – Excessive heat causing holes in the base material.
Each of these defects has its own specific causes, but they often boil down to three main factors: human error, material issues, and environmental conditions.
2. Common Causes of Pipe Weld Failures
Poor Welding Technique
One of the leading causes of weld failures is improper technique. This issue can arise due to insufficient training, lack of experience, or simply neglecting proper procedures. Here are some specific ways poor technique can manifest:
- Improper Heat Application
Applying too much or too little heat can significantly affect the integrity of a weld. If the heat is too low, the weld may not penetrate the base metal fully, leading to weak joints. On the other hand, too much heat can cause the metal to burn through or result in a brittle weld due to excessive grain growth. - Wrong Filler Material
Using a filler material that is incompatible with the base metals can lead to weak welds. For instance, if the thermal expansion coefficients of the filler and base metal don’t match, the weld may crack as the materials expand and contract at different rates. - Inadequate Fusion
This occurs when the weld metal does not completely melt and bond with the base material. As a result, the joint may look solid from the outside but have internal weaknesses that make it prone to failure. - Weld Pool Contamination
External contaminants such as dirt, rust, or oil can prevent the filler material from bonding correctly. This often results in porosity, leading to a weakened structure.
Preventive Measures:
- Ensure proper training and certification for all welders.
- Conduct thorough pre-weld inspections to check for contaminants and clean the surfaces.
- Maintain strict adherence to welding parameters such as heat input, travel speed, and filler material selection.
Residual Stresses and Distortion
During welding, the base metal undergoes rapid heating and cooling, leading to expansion and contraction. This thermal cycle introduces residual stresses into the material. If these stresses are not relieved, they can cause cracks, warping, or even complete weld failure under load.
How Residual Stresses Develop:
- Heating and Cooling
As the metal is heated, it expands, and when it cools, it contracts. If this process is uneven (which is often the case in manual welding), it sets up internal stresses. - Thermal Gradient
The part of the metal directly under the welding arc is much hotter than the surrounding areas, creating a thermal gradient. As the weld cools, the differences in contraction can lead to stress concentration. - External Restraint
If the welded part is restrained (for example, by clamps or supports), it cannot expand and contract freely, leading to higher stress levels.
Preventive Measures:
- Preheat the metal before welding to reduce the temperature gradient.
- Use post-weld heat treatments (such as annealing) to relieve residual stresses.
- Allow for proper cooling times and avoid external restraints wherever possible.
Material Defects and Selection Issues
Even with perfect technique, a weld can fail if the materials used are substandard or incompatible. Defects such as inclusions, segregation, or poor chemical composition can weaken the weld metal and cause premature failure.
Common Material-Related Issues:
- Hydrogen Embrittlement
Hydrogen can enter the weld metal from moisture, oils, or cleaning solutions. Once inside, it can cause the metal to become brittle and crack under stress. - Sulfur or Phosphorus Contamination
Elements like sulfur and phosphorus are often considered impurities in steel. If present in high quantities, they can make the metal brittle and prone to cracking. - Incompatible Materials
Using materials with vastly different thermal or mechanical properties can cause the weld to crack as it cools and contracts. For example, welding high-carbon steel with austenitic stainless steel without a transition layer can lead to immediate or delayed cracking.
Preventive Measures:
- Conduct thorough material inspections and tests before welding.
- Use compatible filler materials that match the mechanical properties of the base metals.
- Avoid moisture or contaminants in the welding environment.
Environmental Factors
The environment in which welding is performed can also influence the quality of the weld. Humidity, temperature, and exposure to chemicals or dust can cause weld defects.
Environmental Challenges:
- Moisture
Water or humidity can introduce hydrogen into the weld, causing porosity or hydrogen embrittlement. - Extreme Temperatures
Welding in very hot or very cold conditions can cause uneven cooling and thermal stresses. For example, welding in sub-zero temperatures can make the metal more brittle. - Wind or Air Currents
For processes like MIG or TIG welding, wind can blow away the shielding gas, resulting in oxidation or contamination.
Preventive Measures:
- Use welding enclosures or tents in outdoor environments.
- Avoid welding in extreme temperatures or use temperature-controlled environments.
- Ensure proper ventilation to prevent gas contamination.
3. Preventive Strategies for Long-Lasting Welds
Preventing weld failures is not just about correcting the defects after they happen — it’s about ensuring that they don’t occur in the first place. Here are some comprehensive strategies to ensure high-quality welds:
- Training and Certification
Ensure that all welders are adequately trained and certified for the type of work they are performing. Regular training sessions and workshops on the latest welding techniques can help maintain high standards. - Use of Quality Materials
Invest in high-quality base materials and filler metals. Conduct material tests to ensure compatibility. - Strict Adherence to Standards
Follow the welding codes and standards laid out by professional organizations such as the American Welding Society (AWS). These standards provide guidelines on everything from filler selection to pre- and post-weld heat treatment. - Implementing Quality Control
Conduct inspections at every stage of the welding process — from pre-weld cleaning to post-weld inspections. Use non-destructive testing methods like ultrasonic testing or radiographic testing to identify internal defects. - Environmental Controls
Set up controlled environments for welding, especially in critical applications. Use tents, shelters, or other barriers to minimize the impact of environmental factors. - Proper Heat Management
Use preheating, post-heating, and slow cooling techniques to manage heat input and reduce the risk of thermal stresses. - Regular Maintenance and Monitoring
Even after welding, regular maintenance and monitoring of welds can help catch early signs of deterioration, such as corrosion or stress cracking.
Conclusion
Weld failures, especially in pipelines, are a serious concern that can lead to hazardous situations, economic losses, and, most importantly, compromise safety. Understanding the root causes of these failures — whether they stem from poor technique, material defects, or environmental factors — is essential for preventing them. By implementing rigorous quality control measures, ensuring proper training, and following industry best practices, welders and engineers can create robust and long-lasting welds that stand the test of time.
For anyone in the welding industry, staying informed about these issues and continuously improving one’s skills is the key to preventing such catastrophic failures and ensuring the safety and integrity of welded structures.