Radiography Testing (RT)- NDT Inspection
Basics of Radiography Testing
Radiography Testing (RT) relies on certain fundamental principles to assess the integrity of welds. Additionally, specific types of radiation are employed in the process, and strict safety measures must be followed to protect personnel and the environment.
Principles of Radiography
Radiography is based on the principle that X-rays or gamma rays can penetrate materials and create an image by interacting differently with various materials and defects. When radiation passes through a material, it may be absorbed, scattered, or transmitted depending on the density and composition of the material. The resulting image provides information about the internal structure, including weld quality and the presence of any defects.
Types of Radiation Used in RT
Radiography Testing commonly employs two types of radiation: X-rays and gamma rays. X-rays are generated by X-ray machines, which produce a controlled beam of radiation. On the other hand, gamma rays are emitted by radioactive isotopes, such as iridium-192 or cobalt-60, contained in sealed sources. Both X-rays and gamma rays have similar properties and are effective in penetrating various materials to produce detailed images of welds.
Radiation Safety Measures
Due to the potential hazards associated with radiation exposure, strict safety measures must be implemented during Radiography Testing. These measures include:
- Compliance with regulatory requirements and guidelines for radiation safety.
- Restricting access to the radiography area and implementing proper signage.
- Monitoring radiation levels using dosimeters and ensuring regular calibration of radiation detection equipment.
- Providing appropriate personal protective equipment (PPE) to workers, including lead aprons, gloves, and safety glasses.
- Conducting regular training and certification for personnel involved in radiography operations.
- Implementing proper storage, handling, and disposal procedures for radioactive sources. 7. Conducting periodic inspections and audits to ensure compliance with radiation safety protocols.
By adhering to radiation safety measures, the risks associated with Radiography Testing can be effectively minimized, ensuring the well-being of personnel and the environment during the inspection process.
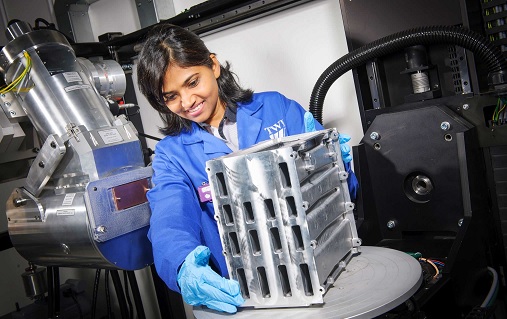
Radiographic Equipment and Setup
Radiography Testing (RT) requires specific equipment and setup to effectively capture and evaluate radiographic images of welds. This section discusses the key components involved in the process.
X-ray Machines and Gamma-ray Sources
X-ray machines are commonly used in RT to generate controlled beams of X-rays. They consist of an X-ray tube that produces the radiation and a high-voltage generator to power the tube. Gamma-ray sources, such as iridium-192 or cobalt-60, are also utilized in RT. These radioactive isotopes emit gamma rays that can penetrate materials and create radiographic images.
Film-based Radiography vs. Digital Radiography
Two main approaches are used for capturing radiographic images: film-based radiography and digital radiography. Film-based radiography involves the use of photographic film, which is exposed to radiation and then processed in a darkroom to develop the image. In digital radiography, a digital image receptor, such as a flat-panel detector, captures the radiation and converts it into a digital image in real-time. Digital radiography offers advantages such as immediate image availability, enhanced image manipulation, and easier storage and sharing of images.
Radiographic Film and Image Receptors
In film-based radiography, special radiographic film is used to record the X-ray or gamma-ray exposure. The film is sensitive to radiation and produces a latent image when exposed. This image is then chemically processed to reveal the final radiographic image. In digital radiography, image receptors such as flat-panel detectors capture the radiation and convert it into a digital image that can be viewed and analyzed on a computer.
Radiographic Exposure Devices
Radiographic exposure devices are used to position and control the source of radiation during RT. These devices can be manipulators, cameras, or shielded containers that hold the radioactive source in place. They ensure precise placement of the radiation source relative to the weld being inspected, allowing for consistent and accurate exposure.
Darkroom and Image Processing
In film-based radiography, a darkroom is used for processing the exposed radiographic film. The film is developed, fixed, washed, and dried in a light-restricted environment. Image processing techniques may also be applied to enhance the visibility and interpretation of radiographic images, such as adjusting contrast or brightness levels.
Note: With the shift towards digital radiography, the need for darkrooms and chemical processing is eliminated, as digital images can be directly captured, viewed, and processed using appropriate software.
Effective utilization of radiographic equipment and proper setup play a crucial role in obtaining high-quality radiographic images for accurate evaluation of welds during RT.
Radiographic Techniques in Welding
Radiography Testing (RT) employs various techniques to optimize the inspection process and obtain accurate radiographic images for evaluating weld quality. This section explores the key aspects involved in radiographic techniques specific to welding.
Selection of Appropriate Technique
Different radiographic techniques can be applied based on the specific requirements of the weld being inspected. This includes direct exposure techniques, where the radiation source is placed in direct contact with the weld, and indirect exposure techniques, where the radiation passes through a separate object to reach the weld. Examples of techniques include the direct exposure technique, double wall technique, and panoramic technique, among others. The selection of the appropriate technique depends on factors such as weld configuration, material thickness, and the type of defect to be detected.
Determining Exposure Parameters
Exposure parameters, including kilovoltage (kV), milliamperage (mA), and exposure time, need to be determined for each RT examination. These parameters are influenced by factors such as material thickness, weld geometry, and the desired sensitivity of defect detection. Optimizing exposure parameters ensures that the radiographic image provides adequate contrast and clarity for accurate interpretation.
Use of Collimators and Filters
Collimators and filters are used to control the X-ray or gamma-ray beam during RT. Collimators restrict the size and shape of the radiation beam, ensuring that only the desired area is exposed and reducing scattered radiation. Filters are employed to remove unwanted radiation and enhance image quality. For instance, aluminum filters can be used to remove low-energy X-rays, improving contrast and reducing image noise.
Choice of Film or Digital Image Capture
The choice between film-based radiography and digital radiography depends on factors such as the specific application, desired workflow, and available resources. Film-based radiography relies on photographic film to capture the radiographic image, while digital radiography uses digital detectors to convert radiation into digital images. Digital radiography offers advantages such as immediate image availability, manipulation capabilities, and easier storage and sharing of images.
Setting up the Radiographic Inspection Area
Proper setup of the radiographic inspection area is essential for successful RT. This includes ensuring a controlled environment free from excessive ambient light and radiation interference. The area should be properly shielded to prevent radiation exposure to personnel and surrounding areas. Safety measures, including radiation warning signs, restricted access, and protective barriers, should be in place. Additionally, the positioning of the radiation source, detector, and weld specimen should be carefully arranged to achieve optimal image quality and coverage.
Implementing appropriate radiographic techniques in welding helps to maximize the effectiveness of RT inspections, enabling the detection and evaluation of welding defects accurately.
Interpretation of Radiographs
The interpretation of radiographs is a crucial step in Radiography Testing (RT) for welding. It involves a detailed analysis of the radiographic images to identify and classify defects, apply acceptance criteria, and document the findings. This section explores the key aspects of radiograph interpretation.
Reviewing Radiographic Images
The interpretation process begins with a thorough review of the radiographic images captured during RT. The radiographs are carefully examined to ensure proper exposure, image quality, and coverage of the weld area. Radiographic images may be viewed on lightboxes or digital displays, allowing inspectors to scrutinize the details of the weld and any potential indications of defects.
Identifying and Classifying Defects
The primary objective of radiograph interpretation is to identify and classify defects or discontinuities present in the weld. Common defects include lack of fusion, porosity, cracks, incomplete penetration, and undercutting. Inspectors rely on their expertise and knowledge of welding standards to accurately identify and characterize these defects. The size, shape, location, and severity of the defects are evaluated to assess their impact on the integrity of the weld.
Acceptance Criteria and Industry Standards
To determine the acceptability of a weld, acceptance criteria based on industry standards and codes must be applied. These standards may vary depending on the specific application, project requirements, and governing bodies. For example, welding standards such as AWS D1.1 (for structural welding) or the ASME Boiler and Pressure Vessel Code (for pressure vessel fabrication) provide guidelines on acceptable levels of defects and the criteria for rejecting or accepting a weld based on the identified indications in the radiographic images.
Reporting and Documentation of Findings
The findings from radiograph interpretation need to be accurately documented and reported. Inspection reports typically include detailed information about the weld, such as location, material, and welding procedure, as well as a description of the identified defects and their characteristics. Clear and concise descriptions, including defect size, length, and orientation, are essential for communication and decision-making regarding repair or acceptance of the weld. Proper documentation ensures traceability and serves as a reference for future inspections and quality control purposes.
Accurate interpretation of radiographs enables inspectors to assess the integrity of welds, identify defects, and determine compliance with applicable standards and codes. Thorough reporting and documentation facilitate effective communication among stakeholders and aid in the decision-making process regarding the acceptance or repair of welds.
Practical Considerations
In Radiography Testing (RT) for welding, several practical considerations must be taken into account to ensure the effectiveness, accuracy, and safety of the inspection process. This section explores key practical considerations that need to be addressed.
Preparation of Test Specimens for RT
Before conducting RT, proper preparation of test specimens is essential. This includes ensuring that the welds to be inspected are clean, free from surface contaminants, and properly prepared according to the applicable welding standards. The surface condition of the weld can significantly affect the quality of the radiographic images and the ability to detect defects accurately.
Proper Positioning of Radiographic Source and Detector
The positioning of the radiographic source and detector is critical for obtaining clear and informative radiographic images. The source should be aligned and centered with the weld to ensure adequate coverage and consistent exposure throughout the weld volume. The detector, whether it is film or a digital image receptor, should be positioned at the appropriate distance and angle to capture the desired views and maximize the sensitivity to detect defects.
Control of Surrounding Factors
Several surrounding factors must be controlled during RT to minimize potential interference and optimize image quality. These factors include:
- Radiation Shielding: Implementing proper shielding measures, such as lead curtains or walls, to prevent unnecessary radiation exposure to personnel and surrounding areas.
- Ambient Light: Minimizing ambient light in the radiographic inspection area to enhance the visibility of radiographic images and prevent interference or degradation of image quality.
- Background Radiation: Assessing and mitigating background radiation sources, such as natural radioactivity, which can interfere with the detection and interpretation of defects.
- Scatter Radiation: Controlling scatter radiation by employing appropriate collimation and shielding techniques to minimize unwanted exposure and maintain image clarity.
Safety Precautions for Personnel Involved
The safety of personnel involved in RT is of paramount importance. Key safety precautions include:
- Radiation Safety Training: Providing comprehensive training to personnel involved in RT to ensure they are knowledgeable about radiation hazards, safety protocols, and proper use of personal protective equipment (PPE).
- Personal Protective Equipment (PPE): Ensuring that personnel wear appropriate PPE, such as lead aprons, gloves, and safety glasses, to minimize radiation exposure.
- Radiation Monitoring: Regularly monitoring radiation levels using dosimeters and ensuring that equipment is properly calibrated and maintained.
- Controlled Access: Restricting access to the radiographic inspection area to authorized personnel and implementing appropriate warning signs and barriers.
By addressing these practical considerations, RT can be conducted with precision, accuracy, and the highest level of safety. Adequate preparation, proper positioning, control of surrounding factors, and adherence to safety precautions contribute to reliable and effective radiographic inspections for welding.
Limitations and Challenges
Radiography Testing (RT) for welding, like any inspection method, has certain limitations and challenges that need to be considered. Understanding these limitations and implementing appropriate mitigation strategies is crucial for obtaining reliable results. This section explores the key limitations and challenges associated with RT in welding.
Factors Affecting Radiographic Quality
Several factors can impact the quality and clarity of radiographic images, including:
- Material Thickness: Thick materials may require higher radiation energy levels to penetrate adequately, resulting in reduced image resolution.
- Geometry and Complex Structures: Complex weld geometries, such as fillet welds or welded joints with intricate shapes, can lead to areas of limited accessibility for radiation and result in obscured or distorted images.
- Radiation Scatter: Scatter radiation can reduce image contrast and clarity, particularly in dense materials or when inadequate collimation is employed. Scatter radiation can originate from the weld itself, adjacent structures, or equipment.
- Image Distortion: Factors such as object-to-film distance, object-to-detector distance, and X-ray source angle can introduce geometric distortion or magnification in radiographic images.
Limitations of RT in Detecting Certain Defects
While RT is a widely used and effective method for detecting weld defects, it has limitations in detecting certain types of discontinuities. These limitations include:
- Lack of Sensitivity to Certain Discontinuities: RT may have limited sensitivity in detecting small defects, such as micro-cracks or surface cracks, which may not be easily discernible on radiographic images. Other methods, such as ultrasonic testing, may be more suitable for detecting these types of defects.
- Inherent Limitations of 2D Imaging: Radiographic images provide a 2D representation of a 3D weld. As a result, the exact depth or location of a defect may be difficult to determine accurately, requiring complementary techniques or additional inspection methods.
Mitigation Strategies for Overcoming Challenges
To overcome the limitations and challenges of RT in welding, several mitigation strategies can be employed, including:
- Complementary Inspection Techniques: Utilizing additional inspection methods, such as ultrasonic testing, magnetic particle testing, or visual inspection, to enhance defect detection and characterization.
- Technique Optimization: Adjusting exposure parameters, positioning the radiation source and detector optimally, and employing appropriate collimation and filtration techniques to enhance image quality and defect detectability.
- Advanced Radiographic Techniques: Implementing advanced radiographic techniques, such as computed tomography (CT), which provides cross-sectional images for better defect visualization and characterization.
- Inspection Procedure Development: Developing comprehensive inspection procedures that address the specific limitations and challenges encountered in the welding process and the materials being inspected.
- Expertise and Training: Ensuring that personnel involved in RT receive adequate training and possess the necessary expertise to interpret radiographic images accurately and effectively.
By understanding the limitations and challenges of RT in welding and implementing appropriate mitigation strategies, the overall reliability and effectiveness of the inspection process can be enhanced. This allows for improved defect detection and characterization, leading to higher-quality welds and enhanced safety in various industries.
Advancements in Radiography Testing
Radiography Testing (RT) has witnessed significant advancements in recent years, driven by technological innovations and the need for more efficient and accurate inspection methods. This section explores the key advancements in RT techniques, their benefits and limitations, as well as current trends and future developments in RT technology.
Introduction to Advanced RT Techniques
Advanced RT techniques have emerged, offering improved capabilities and efficiency in radiographic inspections. Two notable techniques are:
- Computed Radiography (CR): CR replaces traditional film-based radiography with reusable imaging plates that capture radiation and produce digital images. These images can be viewed and analyzed using computer software, enabling enhanced image manipulation, storage, and sharing capabilities.
- Digital Radiography (DR): DR directly captures radiation using digital detectors, eliminating the need for film processing. Digital radiographic images can be viewed in real-time, allowing for immediate analysis, manipulation, and sharing of images.
Benefits and Limitations of Advanced Techniques
The advanced RT techniques mentioned above offer several benefits over traditional film-based radiography, including:
- Improved Workflow Efficiency: Advanced techniques eliminate the need for film processing, reducing inspection time and enabling real-time image viewing and analysis.
- Enhanced Image Quality: Digital images can be manipulated to optimize contrast, brightness, and zoom levels, aiding in defect identification and characterization.
- Reduced Environmental Impact: Film processing chemicals are eliminated, resulting in a more environmentally friendly inspection process. However, advanced techniques also have limitations, including:
- Initial Investment: The initial cost of equipment for CR or DR may be higher compared to traditional film-based radiography.
- Equipment Sensitivity: Digital detectors used in advanced techniques may be more sensitive to environmental factors, requiring careful handling and protection from damage.
Current Trends and Future Developments in RT Technology
Several current trends and future developments are shaping the future of RT technology, including:
- Automation and Robotics: The integration of RT with automation and robotics is gaining traction, enabling automated scanning and positioning of radiation sources and detectors for improved accuracy and efficiency.
- Advanced Imaging Algorithms: Ongoing research is focused on developing advanced imaging algorithms that can enhance defect detection and characterization, particularly for complex weld geometries.
- Portable and Wireless Systems: Advancements in portable and wireless RT systems enable greater flexibility and accessibility, facilitating inspections in challenging environments or remote locations.
- Hybrid Inspection Techniques: The combination of different non-destructive testing methods, such as ultrasonic testing and RT, is being explored to leverage the strengths of each technique and enhance defect detection capabilities.
These trends and developments in RT technology promise to deliver more accurate, efficient, and reliable inspection processes. As technology continues to evolve, the future of RT holds immense potential for further improving weld quality assessment, defect detection, and overall safety in various industries.
Applications
Radiography Testing (RT) finds extensive applications in the field of welding, contributing to the assessment of weld quality and ensuring the integrity of various structures. This section explores examples of RT applications in welding, success stories, lessons learned, and notable projects with specific RT requirements.
Examples of RT Applications in Welding
RT is utilized in a wide range of welding applications, including:
- Construction Industry: RT is commonly used to inspect welded joints in structural steel fabrication for buildings, bridges, and infrastructure projects.
- Oil and Gas Sector: Welds in pipelines, storage tanks, and offshore platforms undergo RT to detect defects and ensure compliance with industry standards.
- Power Generation: RT is applied in the inspection of welds in power plants, including pressure vessels, boilers, and piping systems.
- Aerospace and Automotive Industries: Welded components in aircraft, spacecraft, automobiles, and other transportation systems undergo RT to ensure structural integrity.
- Manufacturing and Fabrication: RT is employed in various manufacturing processes that involve welding, such as fabrication of heavy machinery and equipment.
Notable Projects and their RT Requirements
Notable projects that have specific RT requirements include:
- Nuclear Power Plants: RT plays a critical role in inspecting welds in nuclear power plant components, where stringent safety and quality standards must be met.
- Offshore Structures: RT is essential for ensuring the integrity of welds in offshore platforms, where environmental conditions and fatigue loading are significant considerations.
- High-Pressure Piping Systems: RT is extensively applied in the inspection of welds in high-pressure piping systems, where the risk of catastrophic failure is high.
- Aerospace Manufacturing: RT is employed in the inspection of critical welds in aerospace components, where precision, reliability, and adherence to strict standards are paramount.
Conclusion
Radiography Testing (RT) is a vital non-destructive testing (NDT) method used in the field of welding to assess weld quality and detect defects. Throughout this outline, we have explored the basics of RT, including its principles, types of radiation used, and radiation safety measures. We have also delved into the equipment and setup required for RT, the various radiographic techniques used in welding, and the interpretation and reporting of radiographic images.
Additionally, we have discussed practical considerations for RT, including specimen preparation, proper positioning of the radiographic source and detector, control of surrounding factors, and safety precautions for personnel involved. We have highlighted the limitations and challenges of RT, such as factors affecting radiographic quality and the limitations in detecting certain types of defects. Moreover, we have examined the advancements in RT techniques, including computed radiography and digital radiography, and explored the current trends and future developments in RT technology.
Furthermore, we have explored case studies and applications of RT in welding, showcasing its wide range of applications in industries such as construction, oil and gas, power generation, aerospace, and manufacturing. The success stories and lessons learned have emphasized the importance of proper procedures, collaboration, and personnel qualification in achieving accurate and reliable RT results. We have also highlighted notable projects with specific RT requirements, underlining the critical role of RT in ensuring the safety and integrity of structures and components.