Risk Management in Underwater Welding
Introduction
Underwater welding plays a crucial role in maritime, offshore, and infrastructure maintenance industries, enabling repairs and construction work on submerged structures. Despite its importance, underwater welding is one of the most hazardous professions, involving significant risks from high pressures, electrical hazards, and limited visibility. Managing these risks effectively is essential for the safety of divers and the efficiency of operations.
Risk management in underwater welding is a systematic approach to identifying, assessing, and controlling the inherent dangers of working underwater. This process is key to minimizing accidents and ensuring the physical, psychological, and environmental safety of underwater welders. Below, we explore the different aspects of risk in underwater welding and strategies to mitigate them.
Understanding the Risks in Underwater Welding
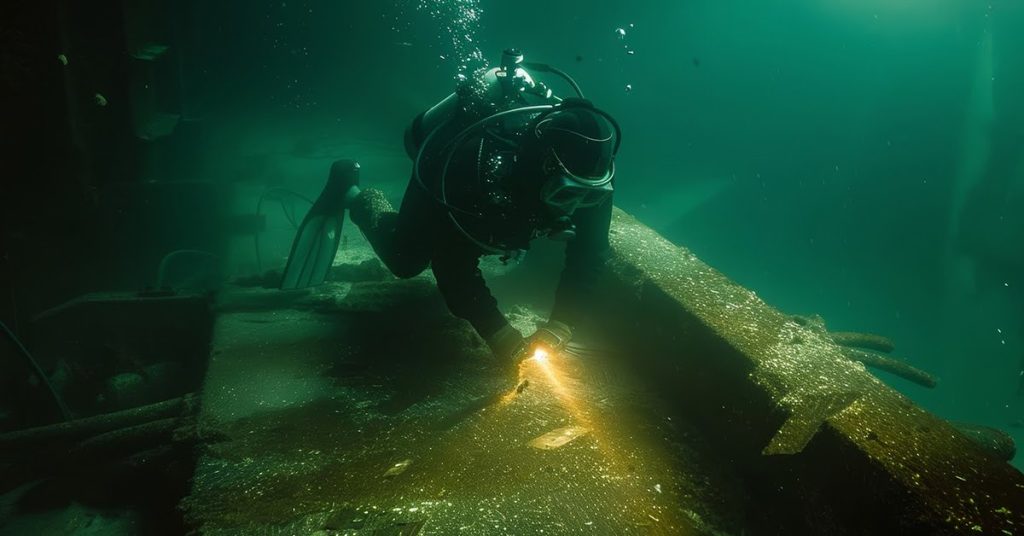
- Physical Hazards
- Electric Shock: Since water is an excellent conductor of electricity, underwater welding poses high risks of electric shock. Divers are susceptible to shock from faulty equipment or poor insulation, leading to serious injuries or fatalities.
- Pressure Hazards: The depth at which a welder operates directly affects pressure levels, which increase dramatically with depth. Pressure-related risks include decompression sickness (the bends) and barotrauma (pressure injuries).
- Thermal Hazards: Underwater welders are exposed to extreme temperatures, especially during wet welding where the welding arc generates heat in a confined space. Improper temperature control can lead to burns and heat-induced equipment failures.
- Restricted Visibility: Visibility underwater can be challenging due to suspended particles, murky water, and insufficient lighting, increasing the risk of accidents from miscommunication or disorientation.
- Chemical Hazards
- Underwater welders may be exposed to hazardous fumes produced during the welding process, which can react with the surrounding water to create toxic compounds. For instance, if oxygen and hydrogen gas bubbles become trapped, they may lead to explosive reactions.
- Exposure to chemicals present in marine environments or from fuel leaks increases the risk of toxic exposure, necessitating specialized protective gear.
- Psychological and Physiological Risks
- Stress Factors: Underwater welding demands a high degree of concentration and calm under pressure. The isolation, high-pressure environment, and limited time can lead to stress and fatigue, affecting a welder’s decision-making and response time.
- Physical Strain: Physical exertion in cold temperatures, restricted movement in bulky diving suits, and the need for prolonged focus can lead to exhaustion, which heightens the risk of accidents.
- Environmental Risks
- Environmental challenges include strong currents, sudden temperature changes, and unpredictable weather. Marine life, such as sharks or jellyfish, may also pose unexpected hazards.
- Current and Flow Hazards: Water currents can increase the risk of loss of control during welding operations, and sudden underwater movements can destabilize both the welder and equipment.
- Equipment and Structural Risks
- Equipment failures can occur due to corrosion, high pressure, or improper maintenance, while structural hazards involve potential collapsing structures or falling debris during repair operations.
- Flammable materials present in certain underwater environments create a unique explosion risk if ignited by welding sparks.
Comprehensive Risk Assessment in Underwater Welding
- Identifying HazardsConducting a hazard identification (HAZID) assessment is the first step in understanding the risks present in any underwater welding job. Site-specific risk factors, such as the depth and location of the work, help welders and safety teams tailor safety protocols.
- Analyzing Risk FactorsWith each identified hazard, assessing factors such as the likelihood of occurrence and potential severity is crucial. For example, deeper dives may require decompression planning, while colder waters may necessitate additional thermal protection.
- Risk Evaluation Techniques
- Failure Mode and Effects Analysis (FMEA): FMEA is a systematic method to identify potential equipment failures and determine their impact on safety.
- Job Safety Analysis (JSA): JSA involves breaking down each welding task into steps, analyzing risks for each step, and implementing measures to mitigate them.
Risk Control Strategies and Techniques
- Preventive Measures
- Pre-Dive Checks: Inspecting all equipment, performing pre-dive checks, and confirming communication protocols are in place are essential steps before starting any underwater welding operation.
- Regular Maintenance: Routine inspections, testing, and maintenance of all welding and diving equipment reduce the risk of malfunction during operations.
- Control Measures
- Insulation and Grounding: Ensuring electrical components are well-insulated and grounded can prevent electrical hazards. Insulated gloves and boots are standard requirements.
- Safety Barriers and Supports: The use of barriers and supports can protect welders from debris, enhance stability, and provide emergency support in case of structural failure.
- Emergency Protocols and Rescue Plans
- Emergency response plans are critical, including the establishment of escape routes, availability of emergency power, and oxygen supplies. Rescuers should be on standby with medical expertise for treating diving-specific injuries.
Training and Competency Development in Risk Management
- Training Requirements
- Welders should undergo safety training tailored to underwater environments, including certifications in welding, diving, and risk management.
- Skills Development
- Developing emergency response skills is crucial, as welders should be prepared to handle various underwater emergencies independently.
- Training in handling specific underwater welding tools and equipment ensures that divers can safely operate in challenging conditions.
- Physical and Mental Fitness Standards
- Divers must meet physical and mental fitness standards to withstand the physiological pressures of underwater work. Regular fitness checks ensure divers can handle the demands of the job.
Technological Advancements for Reducing Risks
- Advanced Equipment
- Innovations in waterproof welding tools, remote-controlled welding systems, and robotic technology are enabling welders to perform tasks with reduced exposure to hazards.
- Use of Monitoring Technologies
- Real-time environmental monitoring allows divers to stay informed about conditions like pressure changes, currents, and visibility, enabling them to adjust safety measures accordingly.
- Safety Gear Improvements
- Advances in diving suits, breathing apparatus, and communication systems have significantly improved the protection and safety of underwater welders.
Regulatory Standards and Compliance in Underwater Welding
- International Standards
- The Occupational Safety and Health Administration (OSHA), American Welding Society (AWS), and American National Standards Institute (ANSI) have established guidelines and standards specific to underwater welding safety.
- Legal and Safety Obligations
- Employers and workers are required to maintain safety standards to prevent legal ramifications. Compliance involves regular inspections, maintaining training records, and ensuring appropriate documentation for safety equipment.
- Certification Requirements
- Certifications for welders and equipment are necessary to comply with safety standards. These certifications ensure welders are qualified to handle equipment safely in high-risk environments.
Real-World Applications
Case studies from past incidents highlight the evolution of risk management practices. For instance, an incident where a lack of pre-dive checks led to equipment failure can demonstrate the importance of following safety protocols. Such examples provide insight into successful risk management practices that have improved over time to ensure the safety of underwater welders.
The Future of Risk Management in Underwater Welding
Emerging technologies, such as autonomous underwater welding robots, AI, and predictive analytics, offer promising advancements in reducing risks. AI systems can analyze environmental data to predict potential hazards, helping to optimize safety measures and minimize human involvement in high-risk operations.
Conclusion
Effective risk management in underwater welding is essential to protect welders, prevent accidents, and maintain operational efficiency. As new technologies emerge, and standards evolve, underwater welding will become safer and more efficient. Prioritizing risk management practices will not only protect workers but also pave the way for innovations in this vital field.