TIG Welding Aluminum: Techniques, Challenges, and Expert Tips
Table of Contents
ToggleIntroduction to TIG Welding Aluminum
TIG (Tungsten Inert Gas) welding, also known as GTAW (Gas Tungsten Arc Welding), is a welding method known for producing high-quality, clean, and precision welds. It is particularly effective for aluminum welding due to its control over heat and filler material. However, aluminum’s unique characteristics, such as its high thermal conductivity and tendency to oxidize, make it a challenging metal to weld. This guide explores the intricacies of TIG welding aluminum, focusing on preparation, techniques, challenges, and practical tips for achieving the best results.
Understanding Aluminum and TIG Welding Basics
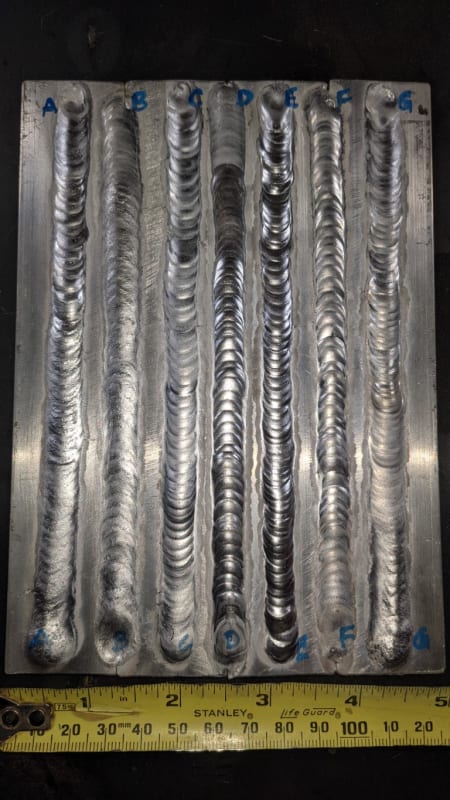
- Properties of Aluminum Aluminum is a lightweight, corrosion-resistant metal widely used in various industries, including automotive, aerospace, and construction. However, welding aluminum requires understanding its unique properties:
- High Thermal Conductivity: Aluminum dissipates heat quickly, which can make it challenging to maintain the weld pool. This rapid heat dissipation requires careful control over the welding process to prevent overheating.
- Oxidation: Aluminum forms a thin oxide layer on its surface when exposed to air. This oxide layer melts at a much higher temperature than the base aluminum, which can interfere with the welding process and cause impurities.
- Softness and Variable Strength: Aluminum is softer than other metals, meaning it requires low heat input during welding. Its alloy compositions, such as 6061 and 5052, exhibit varying levels of strength and ductility, affecting how they respond to heat and filler material.
- Advantages of Using TIG Welding for AluminumTIG welding is highly regarded for aluminum welding due to its precision, cleanliness, and control over heat. Some benefits include:
- Precision Control: TIG welding offers the highest level of control over the weld puddle, enabling welders to achieve accurate, aesthetically pleasing welds.
- Clean Welds: TIG welding requires no flux, reducing the chances of slag or impurities, resulting in high-quality, clean welds.
- Versatile Applications: TIG welding is suitable for a range of aluminum applications, including automotive components, aerospace structures, and custom fabrication.
- Essential Equipment for TIG Welding AluminumTo TIG weld aluminum successfully, specific equipment and settings are crucial:
- TIG Welder with AC Capabilities: TIG welders for aluminum should have an AC (Alternating Current) setting to break the oxide layer. Adjustable amperage control and balance settings are also beneficial for fine-tuning the weld.
- Tungsten Electrodes: Aluminum welding typically requires pure tungsten or zirconium-alloyed tungsten electrodes for optimal arc stability.
- Shielding Gas: Pure argon or an argon-helium mix is commonly used for TIG welding aluminum to shield the weld pool and prevent oxidation.
- Filler Rods: The filler rod alloy should match the aluminum base metal, such as 4043 or 5356, to ensure strength and compatibility.
Preparing for TIG Welding Aluminum
Proper preparation is essential to achieving clean and strong welds with aluminum. The steps include cleaning the metal surface, adjusting machine settings, and understanding the heat input required.
- Cleaning the Metal Surface
- Removing Oxide Layer: Aluminum’s oxide layer must be removed before welding to prevent impurities. Using a stainless-steel brush or a chemical cleaner designed for aluminum removes this layer effectively.
- Surface Preparation: After brushing, clean the aluminum surface with acetone to remove any oil, grease, or other contaminants that could compromise the weld.
- Setting Up the Welding Machine
- Amperage Control: The amperage setting for TIG welding aluminum varies with metal thickness. A general rule is 1 amp per 0.001 inches of metal thickness, but adjustments may be necessary based on specific alloy properties.
- AC Frequency and Balance Control: Adjusting the AC balance helps control the cleaning and penetration phases. Increasing the cleaning action is essential for thick oxide layers, while higher penetration is beneficial for thick sections of aluminum.
- Preheat Option: For thicker aluminum pieces, preheating the workpiece (typically to around 300°F) helps control the weld pool and minimize heat distortion. However, avoid excessive preheating to prevent warping.
Techniques for Successful TIG Welding on Aluminum
- Establishing a Stable Arc
- Short Arc Length: Aluminum requires a steady, short arc length to concentrate heat. This ensures adequate penetration without overheating the surrounding material, which can lead to burn-through on thinner metals.
- Electrode Angle: Keeping the tungsten electrode at a slight angle, typically around 15 degrees from the vertical, helps direct the arc and control the weld pool.
- Controlling Heat Input
- Pulsed TIG Welding: Pulsed current settings allow for alternate high and low amperage, reducing heat input. This is particularly beneficial for thinner sections of aluminum or intricate welds, preventing burn-through.
- Travel Speed: Aluminum requires a quicker travel speed than many other metals to prevent excessive heat buildup. A steady hand is essential, as moving too fast or too slow affects the weld bead’s quality.
- Adding Filler Material
- Dab Technique: A popular method for adding filler rod when TIG welding aluminum is the dab technique, where the rod is periodically added to the molten pool. This helps control the heat and maintains a uniform weld bead.
- Matching Filler Alloy: Choosing a filler alloy that matches the aluminum alloy of the base metal helps prevent brittleness or cracking.
Common Challenges in TIG Welding Aluminum and How to Overcome Them
- Oxidation and ContaminationAluminum’s oxide layer melts at a much higher temperature than the base metal, causing impurities in the weld pool if not removed. Using a stainless-steel brush before welding and employing pure argon shielding gas helps prevent contamination.
- Cracking and Warping
- Cracking: Cracking, especially hot cracking, occurs when welds cool too quickly. This can be minimized by controlling the heat input, using a compatible filler rod, and preheating the metal.
- Warping: Aluminum is prone to warping due to its high thermal conductivity. Minimizing heat input, using fixturing or clamps, and welding in shorter segments can help reduce the likelihood of warping.
- Porosity in Welds
- Porosity often results from contaminants or insufficient shielding gas coverage. Properly cleaning the metal, using a sufficient gas flow rate, and ensuring the filler rod is free from oil or moisture help reduce porosity.
- Hot Cracking
- Hot cracking can be prevented by using the correct filler alloy and allowing the weld to cool at a controlled rate. TIG welders should also avoid adding too much filler material at once, which can induce additional stress in the weld.
Applications of TIG Welding in Aluminum Fabrication
- Automotive IndustryAluminum is used extensively in the automotive industry for parts like frames, engine components, and suspension systems, where its light weight and strength are advantageous. TIG welding ensures high-quality welds for aluminum components, contributing to fuel efficiency and durability.
- Aerospace IndustryAerospace demands precise, lightweight, and strong materials, making aluminum a top choice. TIG welding is ideal for fabricating aircraft parts where exact control and minimal contamination are critical.
- Fabrication and Custom MetalworkTIG welding aluminum is popular in custom metalworking, where weld aesthetics are as important as strength. Bike frames, furniture, and railings are commonly made from aluminum welded with TIG for clean, appealing welds.
- Marine and Industrial ApplicationsAluminum’s corrosion resistance is beneficial for marine environments, and TIG welding ensures durable, watertight welds for boat hulls, offshore rigs, and other marine structures.
Maintenance and Safety Tips for TIG Welding Aluminum
- Regular Electrode MaintenanceTungsten electrodes should be regularly cleaned and inspected, especially if contaminated by the weld pool. A contaminated electrode can destabilize the arc and compromise weld quality.
- Safety Gear and PrecautionsTIG welding aluminum produces intense UV light and heat. Welders should wear appropriate protective gear, including welding gloves, helmets, and flame-resistant clothing, and ensure adequate ventilation to avoid inhaling fumes.
- Calibrating the Welding MachineRegular calibration of the TIG welder ensures consistent performance. Adjusting settings according to the thickness and type of aluminum will improve welding efficiency and quality.
Advanced Techniques for Mastering TIG Welding on Aluminum
- Fine-Tuning AC Balance and Frequency
- Experimenting with AC balance and frequency provides welders more control over cleaning action and arc focus. Adjusting these settings based on the aluminum alloy and thickness helps produce cleaner, more precise welds.
- Mastering Heat Control
- Practice welding on different thicknesses of aluminum to understand how each piece reacts to heat. This builds familiarity with adjusting travel speed and filler addition based on heat input needs.
- Experimenting with Different Filler Rods
- Trying different filler rods allows welders to learn which alloys provide the best results for specific applications. This is especially important in high-stress environments, where selecting the right filler alloy can prevent cracking and improve weld integrity.
Conclusion
TIG welding aluminum requires a combination of skill, precision, and in-depth understanding of aluminum’s unique properties. From equipment setup and metal preparation to advanced welding techniques, each element plays a vital role in producing high-quality welds. By following best practices, maintaining equipment, and continuously refining skills, welders can achieve strong, clean, and reliable welds that meet the demands of various industries. Whether for automotive, aerospace, or custom fabrication, mastering TIG welding aluminum is a valuable skill that enables welders to create lasting, durable, and visually appealing projects.