Robotic Grinding and Sanding Automation
In today’s rapidly evolving industrial landscape, the term “automation” has become synonymous with efficiency, precision, and cost-effectiveness. Robotic Grinding and Sanding Automation is at the forefront of this automation revolution, offering a myriad of advantages to various industries. This article delves into the world of Robotic Grinding and Sanding Automation, shedding light on its applications, benefits, and the latest trends in the field.
Introduction
Robotic Grinding and Sanding Automation, often referred to as “RGS Automation,” is the integration of robotic technology to perform precision grinding and sanding tasks. This technology is transforming industries by automating processes that were once labor-intensive, time-consuming, and often prone to errors. Let’s explore the key aspects of RGS Automation that make it a game-changer.
Basics of Robotic Grinding and Sanding
Robotic grinding and sanding are sophisticated techniques used to refine and finish various surfaces in manufacturing. This section explores the fundamental aspects of these processes.
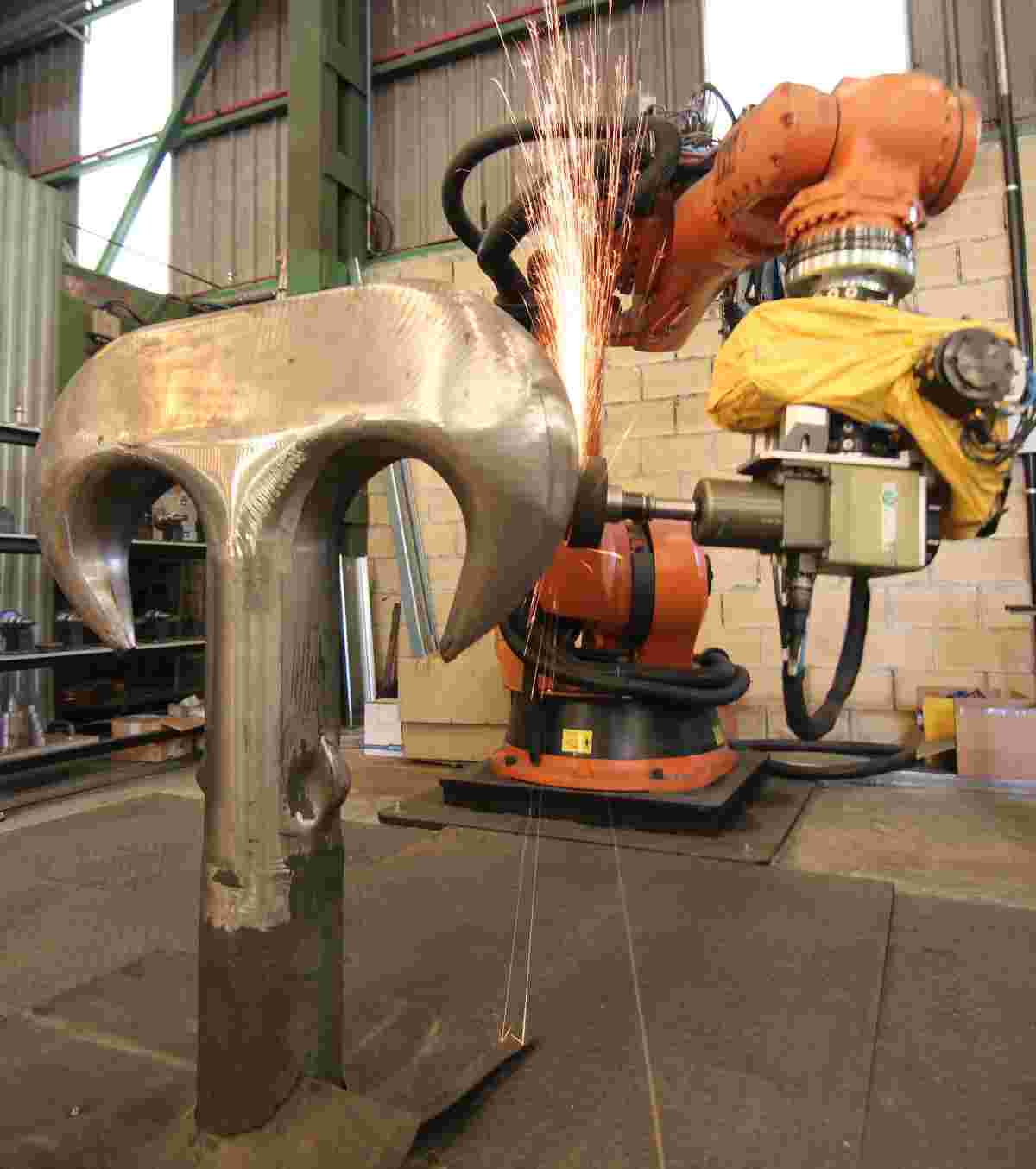
Explanation of Grinding and Sanding Processes
Grinding and sanding are material removal processes that are crucial for achieving smooth, precise, and aesthetically pleasing surfaces. They involve the following:
- Grinding is a material removal process that employs abrasive cutting to remove excess material from a workpiece. It typically uses abrasive wheels or belts that rotate or move linearly, coming into contact with the workpiece. The abrasives grind away imperfections, burrs, and excess material, leaving a smoother and more precise surface.
- Sanding, on the other hand, is a finishing process that smoothens a surface by abrading it with sandpaper or abrasive pads. Sanding is typically used to refine surfaces, remove imperfections, and prepare them for finishing painting, or other treatments. It is often a crucial step in achieving a polished and presentable surface.
Advantages of Using Robots in These Tasks
Utilizing robots in grinding and sanding processes offers several significant advantages:
- Precision and Consistency: Robots can execute grinding and sanding tasks with unmatched precision, ensuring that every part or product meets exact specifications. This consistency is difficult to achieve manually.
- Speed and Efficiency: Robots work at a consistent pace, often faster than human workers. This results in increased production efficiency and reduced cycle times.
- Labor Cost Reduction: Automation reduces the need for manual labor, leading to cost savings in the long run. Robots can operate 24/7 without breaks.
- Improved Safety: Dangerous or repetitive tasks that may cause worker fatigue or injury can be delegated to robots, enhancing workplace safety.
- Quality Assurance: Robotic systems can incorporate sensors and vision systems to detect and correct deviations in real-time, ensuring high-quality surface finishes.
Common Applications of Robotic Grinding and Sanding
Robotic grinding and sanding have found applications in a wide range of industries, including:
- Automotive Industry: Robots are used to grind and sand vehicle components like car bodies, panels, and gears to achieve smooth surfaces and precise fits.
- Aerospace Industry: Aircraft components often require intricate surface finishing, and robots play a crucial role in this process.
- Metalworking: In metal fabrication, robots are employed to grind and sand metal parts, ensuring they meet the required specifications.
- Woodworking: In furniture manufacturing and woodworking, robots are used to achieve high-quality finishes on wooden surfaces.
- Construction: Robots are used for concrete surface grinding to prepare floors or walls for finishing in construction projects.
Components of Robotic Grinding and Sanding Systems
Robotic grinding and sanding systems consist of several critical components that work together to ensure efficient and precise execution of these tasks. In this section, we explore the key components that make up these systems.
Robot Arms and End-Effectors
- Robot Arms: The core of any robotic system, the robot arm, provides the necessary dexterity and movement required for grinding and sanding. These arms are typically equipped with multiple joints, enabling a wide range of motion.
- End-Effectors: These are the tools or attachments at the end of the robot arm responsible for carrying out the grinding or sanding operations. End-effectors are designed to securely hold abrasive tools such as grinding wheels or sanding pads. They must provide the required force, speed, and precision for the specific application.
Sensing and Vision Systems
- Force and Tactile Sensors: Force sensors are often integrated into the robot’s end-effector to measure the force applied during grinding or sanding. This feedback allows the robot to adjust its pressure to maintain consistent material removal.
- Vision Systems: Vision systems, including cameras and machine vision software, are used for real-time monitoring and quality control. They can detect surface imperfections, track the tool’s position, and adjust the robot’s movements accordingly.
- 3D Scanning: Some applications use 3D scanning technology to create detailed surface maps, enabling the robot to adapt its grinding or sanding path based on the workpiece’s actual shape.
Control Software and Programming
- Robot Control Software: This software governs the robot’s movement, speed, and precision. It integrates with the vision system, sensors, and other peripherals to ensure accurate execution of grinding and sanding tasks.
- Path Planning: Programming the robot to follow specific paths on the workpiece is essential. Path planning algorithms are used to determine the most efficient routes for material removal, minimizing cycle time.
- Material Removal Algorithms: Depending on the material being processed and the desired finish, specialized algorithms may be employed to optimize the grinding or sanding process.
Safety Measures and Precautions
- Safety Barriers: In industrial settings, physical barriers and safety enclosures are used to separate robots from human workers, preventing accidents and ensuring compliance with safety regulations.
- Emergency Stop Systems: Emergency stop buttons and safety interlocks are installed to halt robot operations in case of unexpected situations or hazards.
- Operator Training: Proper training of personnel is crucial to ensure they understand the robot’s operation, potential hazards, and how to interact with the system safely.
- Safety Sensors: Robots can be equipped with safety sensors to detect the presence of humans in their workspace. When a human enters the robot’s vicinity, the robot can slow down or stop to prevent collisions.
Benefits of Robotic Grinding and Sanding
Robotic grinding and sanding automation offer a multitude of advantages for various industries. These benefits not only enhance the quality of the finished products but also contribute to overall process efficiency, safety, and cost-effectiveness.
Improved Precision and Consistency
One of the primary advantages of employing robots in grinding and sanding is the remarkable improvement in precision and consistency. Robots can execute tasks with unparalleled accuracy, ensuring that every part or product meets exact specifications. This consistency is challenging to achieve through manual labor, where human operators might introduce variations due to fatigue or differing skill levels. The result is a higher quality surface finish that adheres to stringent tolerances, reducing the likelihood of defects or rework.
Increased Productivity and Efficiency
Automation significantly boosts productivity and efficiency in grinding and sanding processes. Robots work tirelessly and at a consistent pace, often faster than human workers. They can operate 24/7 without the need for breaks, reducing cycle times and increasing the throughput of products. This enhanced efficiency ultimately leads to cost savings and shorter lead times, benefiting manufacturers and customers alike.
Reduction in Labor Costs
Robotic automation in grinding and sanding translates to a reduction in labor costs. By automating these labor-intensive and often repetitive tasks, manufacturers can allocate their workforce to more complex and value-added roles. Over time, this can lead to substantial savings as fewer human operators are required to monitor and operate the systems. It also minimizes the impact of labor shortages, especially in industries where skilled labor is in high demand.
Enhanced Workplace Safety
Safety is paramount in any manufacturing environment. Robotic grinding and sanding systems enhance workplace safety by eliminating or reducing the need for human operators to perform potentially hazardous tasks. Dangerous tasks, such as exposure to harmful dust, fumes, or sharp objects, are now delegated to robots. Additionally, safety sensors and emergency stop systems are integrated into these systems to prevent accidents. This not only reduces the risk of workplace injuries but also lowers insurance and workers’ compensation costs for manufacturers.
Challenges and Limitations
While robotic grinding and sanding offer significant advantages, they also come with a set of challenges and limitations that manufacturers need to address. These challenges can impact the cost, operation, and flexibility of these systems.
Initial Setup and Integration Costs
- Capital Investment: Acquiring and installing robotic grinding and sanding systems involves a substantial capital investment. The cost includes purchasing the robot, end-effectors, sensors, and any additional equipment, as well as integrating these components into the existing manufacturing infrastructure.
- Expertise: Manufacturers require specialized expertise to select the right equipment, design the system, and ensure proper integration. This often necessitates hiring or contracting experts, which can add to the overall setup costs.
Programming Complexity
- Skilled Programmers: Programming robots for grinding and sanding tasks can be complex and requires skilled programmers. These individuals must have a deep understanding of the robotic system, the specific application, and the required safety protocols.
- Adaptability: Changing the robot’s programming to accommodate new products or materials can be time-consuming and costly. Manufacturers need to ensure that their systems are adaptable and can be reprogrammed efficiently to handle variations in production.
Handling Complex Shapes and Materials
- Complex Shapes: Robots may struggle with handling complex workpiece shapes, especially those with intricate contours or internal features. Special end-effectors and advanced programming are needed to address such challenges.
- Material Variability: Different materials require varying grinding or sanding parameters. Handling a range of materials, such as metals, composites, or ceramics, may demand constant adjustments to the robotic system, which can complicate the process.
Maintenance and System Downtime
- Regular Maintenance: Robotic systems require regular maintenance to ensure consistent performance. This includes upkeep of the robot arm, end-effectors, and associated equipment, which can be time-consuming and costly.
- System Downtime: Maintenance, repairs, or software updates can lead to system downtime. In manufacturing environments with tight production schedules, any downtime can disrupt operations and impact delivery schedules.
- Cost of Downtime: The cost of system downtime in terms of lost production, maintenance, and potential idle labor should be carefully managed to minimize its impact on overall manufacturing efficiency.
Future Trends and Innovations
As technology continues to evolve, the field of robotic grinding and sanding automation is experiencing significant advancements and innovative trends. This section explores some of these emerging trends and technologies shaping the future of this industry.
Emerging Technologies in Robotic Grinding and Sanding
- AI and Machine Learning: Robots are becoming more intelligent through AI and machine learning. They can adapt to different workpiece shapes and materials, optimize grinding paths, and make real-time adjustments for quality control.
- Force Sensing and Control: Advanced force sensing technology allows robots to apply the right amount of pressure during grinding or sanding, ensuring optimal material removal without causing damage.
- Nanorobotics: Nanorobots are being developed for ultra-precise surface finishing at the nanoscale. These tiny robots offer unprecedented precision and are finding applications in electronics and microfabrication industries.
- 3D Printing for Tooling: 3D printing is used to create customized end-effectors and tooling, providing flexibility for a wide range of applications. This allows for rapid prototyping and cost-effective solutions.
- Collaborative Robots: Collaborative robots, or cobots, are becoming more common in manufacturing. These robots can work alongside human operators, enhancing flexibility in grinding and sanding processes while maintaining safety.
Industry 4.0 and the Role of IoT and Data Analytics
- IoT Integration: Robotic systems are increasingly connected through the Internet of Things (IoT), allowing for real-time monitoring and remote control. This connectivity enables predictive maintenance, reducing downtime.
- Data Analytics: Data collected from robotic systems, sensors, and vision systems are analyzed to optimize processes. This data-driven approach helps manufacturers make informed decisions, improve quality, and increase efficiency.
- Digital Twins: Digital twin technology creates virtual replicas of physical robotic systems. Manufacturers can simulate and test different scenarios, improving system performance and reducing errors before implementing changes in the real world.
- Predictive Maintenance: Through data analytics and predictive algorithms, maintenance can be scheduled based on the actual condition of robotic systems. This reduces unplanned downtime and extends the lifespan of equipment.
Sustainability and Environmental Considerations
- Environmentally Friendly Abrasives: There is a growing emphasis on using sustainable and environmentally friendly abrasives in robotic grinding and sanding. This helps reduce the environmental impact of abrasive materials.
- Energy Efficiency: Energy-efficient robotic systems are being developed to reduce power consumption. This not only saves on operational costs but also contributes to sustainability efforts.
- Recycling and Waste Reduction: Manufacturers are implementing recycling programs for abrasive waste and grinding dust. These efforts help reduce the environmental footprint of the grinding and sanding processes.
- Green Certifications: More industries are seeking green certifications for their manufacturing processes. Robotic systems that reduce waste and energy usage can contribute to these certifications.
FAQs
Is robotic grinding and sanding suitable for small-scale manufacturing?
Robotic systems can be adapted to suit both small-scale and large-scale manufacturing, making them a versatile choice for businesses of all sizes.
What safety precautions should be taken when implementing robotic systems?
Safety measures, including emergency stop features and barrier systems, should be in place to ensure the safety of operators and equipment.
How do I choose the right robotic system for my business?
Choosing the right system depends on your industry and specific application. Consulting with experts in the field is recommended to make an informed decision.
Are robotic systems easy to program and maintain?
Advances in software and user-friendly interfaces have made programming and maintenance more accessible, reducing complexities.
What is the future of robotic automation in manufacturing?
The future holds even more advanced robotic systems with enhanced capabilities and adaptability to a wider range of applications, making automation increasingly prevalent in manufacturing.
Conclusion
Robotic Grinding and Sanding Automation is a technological marvel that’s redefining industrial processes. Its precision, efficiency, and adaptability make it an invaluable asset to a wide range of industries. As technology continues to advance, we can expect even more remarkable developments in the world of automation, driving innovation and productivity to new heights.