Slag Inclusions in Welding: Ensuring Seamless Joints
Welding, a crucial process in various industries, is not without its challenges. One common issue that welders encounter is the presence of slag inclusions. This article dives deep into the world of welding, exploring what slag inclusions are, their impact on weld quality, and how to prevent them for impeccable results.
Introduction
Definition of Slag Inclusions in Welding
Welding slag inclusions refer to the entrapped non-metallic materials within the weld metal or between weld layers. These inclusions can compromise the structural integrity and appearance of welded joints.
Importance of Addressing Slag Inclusions
Understanding and addressing slag inclusions are paramount to ensuring the longevity and reliability of welded structures. Neglecting this aspect can lead to weld failures, posing risks to both safety and project success.
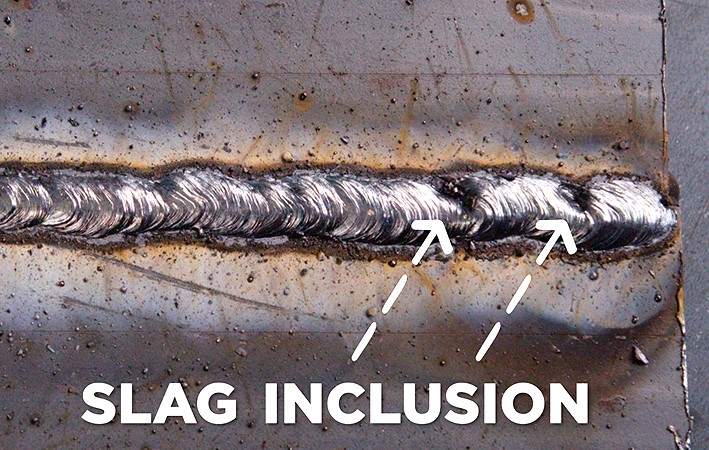
Understanding Slag Inclusions
Formation of Slag Inclusions
Slag inclusions typically occur during the welding process when molten metal fails to fuse properly, trapping slag within the weld. This can happen due to various factors, including improper welding techniques and inadequate cleanliness.
Common Causes in Welding Processes
Identifying the root causes of slag inclusions involves a comprehensive examination of welding parameters, material conditions, and environmental factors. Common culprits include insufficient shielding gas, electrode contamination, and poor welder technique.
Impact on Weld Quality
Structural Weakness
The presence of slag inclusions can lead to structural weaknesses in welded joints, compromising the load-bearing capacity of the structure. This aspect is particularly critical in applications where safety is paramount.
Aesthetic Concerns
Beyond structural issues, slag inclusions can affect the visual appeal of welds. In industries where aesthetics matter, such as architectural welding, the presence of slag can be a significant drawback.
Identification of Slag Inclusions
Visual Inspection
Visual inspection remains a primary method for identifying slag inclusions. Welders and inspectors must be trained to recognize the visual characteristics of slag, ensuring prompt corrective action.
Non-Destructive Testing Techniques
In addition to visual inspection, non-destructive testing techniques like ultrasonic testing and radiography play a vital role in detecting hidden slag inclusions. These methods provide a more in-depth analysis without compromising the integrity of the weld.
Prevention Measures
Proper Welding Techniques
Adopting proper welding techniques is fundamental in preventing slag inclusions. This includes maintaining the correct welding parameters, ensuring proper electrode storage, and following established procedures for specific welding processes.
Quality Control Procedures
Implementing stringent quality control procedures is crucial for preventing slag inclusions. Regular inspections, adherence to industry standards, and the use of advanced monitoring technologies contribute to a proactive approach in ensuring weld quality.
Case Studies
Examples of Welding Failures Due to Slag Inclusions
Examining real-world examples of welding failures due to slag inclusions highlights the importance of addressing this issue. Case studies serve as valuable lessons, emphasizing the consequences of overlooking slag-related challenges.
Lessons Learned
From these case studies, valuable lessons emerge, underlining the need for rigorous quality control, proper training, and the application of advanced technologies to mitigate the risks associated with slag inclusions.
Best Practices for Welding Without Slag Inclusions
Cleanliness in Welding Environment
Maintaining a clean welding environment is foundational for preventing slag inclusions. Regular cleaning of welding equipment, work surfaces, and ensuring proper storage of welding consumables contribute to a contamination-free workspace.
Choosing the Right Welding Materials
Selecting the appropriate welding materials is critical. Compatibility between base metals and electrodes, as well as ensuring the quality of consumables, plays a pivotal role in preventing slag-related defects.
Industry Standards and Regulations
Compliance Requirements
Adhering to industry standards and regulations is non-negotiable. Compliance ensures that welding processes meet the necessary safety and quality benchmarks, reducing the likelihood of slag inclusions and other defects.
Certification Programs for Welders
Certification programs for welders play a vital role in standardizing skills and knowledge. A certified welder is more likely to be adept at preventing and addressing issues like slag inclusions, contributing to overall weld quality.
Addressing Slag Inclusions in Different Welding Processes
Arc Welding
Each welding process has its unique considerations. In arc welding, attention to electrode selection, proper voltage, and appropriate amperage are crucial to preventing slag inclusions.
MIG/MAG Welding
Metal Inert Gas (MIG) and Metal Active Gas (MAG) welding processes require careful control of shielding gas and wire feed speed to avoid slag-related defects.
TIG Welding
Tungsten Inert Gas (TIG) welding demands precision. Maintaining a stable arc, proper tungsten electrode sharpening, and shielding gas purity are essential for preventing slag inclusions.
FAQs
Can slag inclusions be completely eliminated in welding?
While complete elimination may be challenging, stringent quality control measures and proper training significantly reduce the occurrence of slag inclusions.
How often should welders undergo training to stay updated on best practices?
Continuous learning is encouraged, and regular training sessions, at least annually, help welders stay abreast of the latest developments in the industry.
What role do industry certifications play in preventing welding defects?
Industry certifications ensure that welders meet established standards, indicating a higher likelihood of preventing defects like slag inclusions.
Are robotic welding systems foolproof in preventing slag inclusions?
While robotic systems enhance precision, human oversight remains crucial to address dynamic challenges in welding.
How can the welding community contribute to environmentally friendly practices?
The welding community can adopt eco-friendly consumables, optimize energy usage, and implement waste management practices to minimize environmental impact.
Conclusion
In conclusion, addressing slag inclusions in welding is imperative for ensuring the longevity, safety, and aesthetic appeal of welded structures. By understanding the causes, implementing prevention measures, and embracing advanced technologies, the welding community can elevate the standards of weld quality.