TIP TIG Welding System
Introduction
TIP TIG welding is a welding technique that enhances the traditional TIG welding process. TIG welding is known for its precision and the use of a non-consumable tungsten electrode, which creates an electric arc to melt the base metal while an inert gas shield protects the weld from contamination. TIP technology, on the other hand, introduces a filler wire oscillation system that deposits the filler metal into the weld pool in a specific way. The combination of these two technologies results in improved weld quality, speed, and versatility.
Understanding TIG Welding
TIG welding, short for Tungsten Inert Gas welding, is a precise and versatile welding process that relies on the controlled fusion of materials. This section delves into the intricacies of TIG welding, explaining its process, the principles of arc welding, the role of inert gas, comparing it to other welding methods, and highlighting its diverse applications.
Explanation of TIG Welding Process
- Principles of Arc Welding: TIG welding is categorized as an arc welding process. It operates on the fundamental principle of creating an electric arc between a non-consumable tungsten electrode and the workpiece. This arc generates intense heat, melting the base metal and allowing for the fusion of materials.Tungsten is chosen as the electrode material due to its high melting point and low rate of consumption. This non-consumable aspect distinguishes TIG welding from other welding methods like MIG (Metal Inert Gas) or stick welding, where the electrode material is consumed during the process.
- Role of Inert Gas: In TIG welding, an inert gas, often argon or helium, is used to create a protective atmosphere around the weld area. This inert gas shield prevents the molten metal from coming into contact with atmospheric contaminants like oxygen and nitrogen. As a result, it ensures a clean and contamination-free weld, enhancing its quality and integrity.The use of inert gas also serves the purpose of cooling the tungsten electrode and stabilizing the arc. The control of the arc is essential for precise and controlled weld bead formation.
Comparison of TIG Welding with Other Welding Methods
TIG welding distinguishes itself from other welding methods through several key characteristics:
- Precision: TIG welding is renowned for its precision and the ability to create exceptionally clean, aesthetically pleasing welds. This makes it ideal for applications where weld quality is paramount, such as in aerospace and medical device manufacturing.
- Non-Consumable Electrode: Unlike some other welding methods, TIG welding uses a non-consumable electrode (tungsten). This results in less contamination of the weld and no need for electrode replacement during the process.
- Versatility: TIG welding can be applied to a wide range of materials, including aluminum, stainless steel, carbon steel, and exotic alloys. This versatility makes it a preferred choice for industries dealing with diverse materials.
- Controlled Heat: TIG welding allows for precise control of heat input, which is essential when working with materials sensitive to heat or when welding thin sections.
- Clean Welds: The use of inert gas creates clean, spatter-free welds with minimal post-welding cleanup required.
Applications of TIG Welding
TIG welding finds extensive applications across various industries, owing to its qualities of precision and control. Some notable applications include:
- Aerospace Industry: TIG welding is commonly used for critical aerospace components due to its ability to provide high-quality welds in materials like titanium and aluminum.
- Automotive Industry: TIG welding is employed in the fabrication of exhaust systems, aluminum components, and other critical parts where precision is crucial.
- Oil and Gas Industry: TIG welding plays a role in the construction of pipelines, as well as the repair and maintenance of offshore platforms, where the welds must withstand harsh environmental conditions.
- Structural and Architectural Welding: TIG welding is used for architectural features, sculptures, and ornamental metalwork where aesthetic considerations are important.
- Nuclear Industry: TIG welding is utilized for welding components in nuclear power plants, as the process ensures the integrity and quality of the welds in this critical sector.
Introduction to TIP (Technologie Ingenieur Plasch)
TIP welding, short for Technologie Ingenieur Plasch, represents a significant advancement in the field of welding technology. In this section, we will explore the TIP welding technology, its key features and benefits, as well as the notable advancements and innovations that have shaped its development.
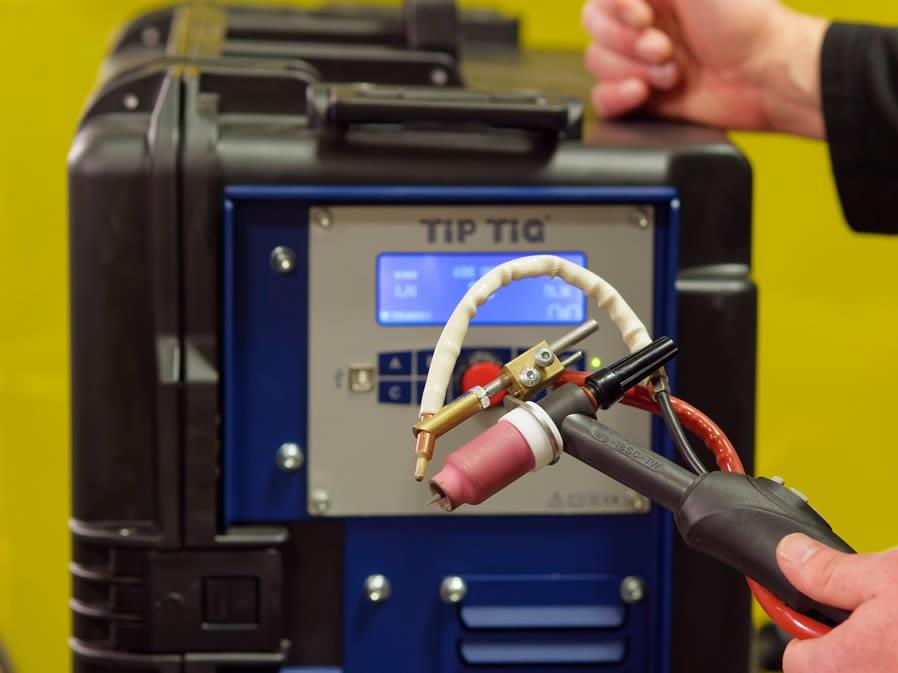
Overview of TIP Welding Technology
TIP welding is a cutting-edge welding process that brings innovation to traditional welding methods, particularly Tungsten Inert Gas (TIG) welding. It introduces a unique approach to how the filler metal is deposited into the weld pool. Here’s an overview of TIP welding technology:
- Filler Wire Oscillation: The core of TIP welding lies in its filler wire oscillation system. Unlike conventional TIG welding, where the filler wire is manually fed into the weld puddle, TIP welding uses a mechanism that oscillates the filler wire rapidly in and out of the weld pool. This controlled motion ensures precise and consistent filler metal deposition.
- Enhanced Arc Stability: The filler wire oscillation in TIP welding contributes to superior arc stability. This results in better control over the welding process, reducing the chances of arc interruptions and weld defects.
- Increased Deposition Rate: TIP welding’s innovative approach allows for a higher deposition rate of filler metal. This means that more material can be added to the weld quickly, which can significantly improve welding speed and efficiency.
- Reduced Heat Input: TIP welding’s unique filler wire delivery system helps in managing the heat input more effectively. This reduction in heat input is essential for minimizing the heat-affected zone (HAZ) and reducing the risk of material distortion, making it suitable for thin materials and heat-sensitive alloys.
Key Features and Benefits of TIP Welding
TIP welding offers a range of key features and benefits that have made it a popular choice in various industries:
- Exceptional Weld Quality: TIP welding consistently delivers high-quality welds with minimal defects and improved aesthetics. The precise control over the filler wire and the arc results in clean and well-formed weld beads.
- Increased Welding Speed: The enhanced deposition rate of filler metal in TIP welding translates to increased welding speed. This benefit is particularly valuable in high-production environments where efficiency is critical.
- Minimized Heat-Affected Zones (HAZ): TIP welding’s ability to manage heat input effectively leads to smaller heat-affected zones, reducing the risk of distortion in the base material. This is vital for welding materials with heat-sensitive properties.
- Versatility: TIP welding is suitable for a wide range of materials, making it a versatile choice for industries that work with diverse alloys and metals.
- Environmental Benefits: TIP welding contributes to environmental sustainability by minimizing the emission of harmful fumes and reducing the need for extensive post-welding cleaning processes, aligning with the growing focus on eco-friendly practices.
Advancements and Innovations in TIP Welding
TIP welding is an evolving technology with ongoing advancements and innovations. Some notable developments include:
- Improved Wire Oscillation Control: Ongoing research and development efforts are focused on enhancing the precision and control of the filler wire oscillation system, further improving weld quality and efficiency.
- Automation and Robotics Integration: TIP welding is increasingly being integrated into automated and robotic welding systems, allowing for even greater precision and consistency in welds.
- New Materials Compatibility: Researchers are continually expanding the range of materials that can be effectively welded using TIP technology, making it suitable for an even broader array of applications.
TIP TIG Welding System
The TIP TIG welding system represents a fusion of TIP (Technologie Ingenieur Plasch) technology and the well-established TIG (Tungsten Inert Gas) welding process. In this section, we’ll explore how TIP and TIG welding merge in the TIP TIG system, the key components that make up this welding setup, and the working principle behind it.
How TIP and TIG Welding Combine in the TIP TIG System
The TIP TIG welding system harmoniously combines the principles of TIG welding with the innovative TIP technology. Here’s how these two welding methods merge:
- TIG Welding Foundation: The TIG welding torch, electrode, and inert gas shielding from the traditional TIG welding process provide the foundation for the TIP TIG system. The TIG setup is used to create the initial electric arc, generate heat, and maintain a protective gas shield.
- Incorporation of TIP Technology: TIP technology brings a critical enhancement to the process by introducing a controlled filler wire oscillation system. This system facilitates the precise delivery of filler metal into the weld pool. It works in tandem with the TIG setup, ensuring that the filler wire is deposited with accuracy and control.
- Improved Efficiency and Quality: The combination of TIP and TIG welding results in a welding system that offers improved efficiency, speed, and weld quality. The precise control of the filler wire and the stable TIG arc contribute to clean, well-formed welds with minimal defects.
Components of the TIP TIG Welding System
The TIP TIG welding system comprises several key components that work together to deliver exceptional welding performance. These components include:
- TIG Welding Torch: The TIG torch is a critical component that houses the tungsten electrode. It serves to create the initial electric arc, maintain the shielding gas, and provide a stable platform for the TIP technology components to operate.
- Power Source: The power source is responsible for providing the necessary electrical current for the welding process. It controls the intensity of the arc and ensures a consistent flow of electricity.
- TIP Technology Components: The TIP technology components include the filler wire oscillation system, wire feeder, and other mechanisms that enable the precise and controlled delivery of filler metal. These components work in conjunction with the TIG welding setup to enhance the welding process.
Working Principle of the TIP TIG Welding System
The working principle of the TIP TIG welding system can be summarized as follows:
- Arc Initiation: The process begins with the TIG welding torch creating an electric arc by striking the tungsten electrode against the workpiece. This arc generates the intense heat required for welding.
- Inert Gas Shielding: Simultaneously, the TIG torch releases an inert gas, typically argon or helium, to create a shielding atmosphere around the weld area. This inert gas prevents atmospheric contamination and provides a stable environment for the welding process.
- TIP Technology Activation: The TIP technology components come into play by introducing a filler wire into the process. The filler wire oscillation system rapidly moves the wire in and out of the weld pool. This controlled motion ensures that the filler metal is deposited accurately and consistently.
- Welding Process: The combination of the TIG arc and the precise filler wire delivery system results in a controlled and efficient welding process. The filler metal melts into the weld pool, forming a strong, clean, and defect-free weld bead.
Advantages of TIP TIG Welding
The TIP TIG welding system offers a range of advantages that have made it a preferred choice in various industries. In this section, we’ll explore these key advantages, highlighting how TIP TIG welding excels in different aspects of the welding process.
Improved Weld Quality and Aesthetics
TIP TIG welding is renowned for its ability to produce welds of exceptional quality and aesthetics. Some of the advantages in this regard include:
- Reduced Weld Defects: The precise control of the filler wire and the stability of the TIG arc result in welds with minimal defects, such as porosity, inclusions, and spatter.
- Clean and Well-Formed Weld Beads: TIP TIG welding consistently produces clean, well-formed weld beads with smooth, uniform profiles, enhancing the overall appearance of the weld.
- Fine Control over the Weld Pool: Welders have fine control over the weld pool and can make subtle adjustments, ensuring that the weld meets the desired specifications.
Increased Welding Speed and Efficiency
Efficiency is a crucial factor in many welding applications, and TIP TIG welding excels in this regard:
- Higher Deposition Rate: The TIP TIG system’s filler wire oscillation system allows for a higher deposition rate of filler metal. This translates to faster welding speeds and increased productivity.
- Reduced Downtime: The stability of the arc and the controlled filler wire delivery system minimize arc interruptions, reducing downtime and the need for rework.
- Cost-Effective Solution: The improved efficiency and productivity of TIP TIG welding make it a cost-effective solution for industries with high-production demands.
Reduction in Heat-Affected Zones (HAZ)
TIP TIG welding offers advantages in terms of heat management and its impact on the base material:
- Smaller Heat-Affected Zones: TIP TIG welding effectively manages heat input, resulting in smaller heat-affected zones. This is crucial for minimizing the risk of material distortion, warping, and damage, making it suitable for welding thin materials and heat-sensitive alloys.
- Less Post-Welding Distortion: The reduced HAZ leads to less post-welding distortion, ensuring that the final component maintains its shape and integrity.
Versatility and Suitability for Various Materials
TIP TIG welding is versatile and well-suited for a wide range of materials, making it an ideal choice for industries that work with diverse alloys and metals:
- Compatible with Multiple Materials: TIP TIG welding can be applied to various materials, including stainless steel, carbon steel, aluminum, nickel alloys, and exotic materials. This versatility makes it adaptable to different industrial applications.
- Suitability for Thin Materials: The precise control and reduced heat input of TIP TIG welding make it suitable for welding thin materials without the risk of burn-through.
Environmental Benefits of TIP TIG Welding
TIP TIG welding also offers environmental benefits that align with the growing emphasis on sustainability in industry:
- Reduced Emissions: TIP TIG welding generates fewer harmful fumes and emissions compared to some other welding processes. This is advantageous for the health and safety of welders and the environment.
- Minimized Post-Welding Cleanup: The clean and spatter-free welds produced by TIP TIG welding reduce the need for extensive post-welding cleaning processes, saving time and resources.
Applications of TIP TIG Welding
The TIP TIG welding system’s exceptional capabilities have found applications in a wide range of industries, where precise and high-quality welding is paramount. Here, we explore specific applications in industries where TIP TIG welding has made a significant impact:
Aerospace Industry
The aerospace industry demands the highest standards of quality and precision in welding, making TIP TIG welding an ideal choice for several applications:
- Aircraft Components: TIP TIG welding is used for joining critical components of aircraft, such as airframes, engine parts, and fuel systems. Its ability to produce clean, defect-free welds ensures the structural integrity and safety of aircraft.
- Spacecraft and Satellites: In the production of spacecraft and satellites, TIP TIG welding plays a role in joining aluminum and titanium components, where weld quality and the absence of defects are crucial for the reliability of missions.
Automotive Industry
The automotive industry relies on TIP TIG welding for various welding applications, particularly where high-quality and efficient welds are needed:
- Exhaust Systems: TIP TIG welding is commonly used for joining exhaust system components, including mufflers and catalytic converters. Its ability to create clean and strong welds contributes to the durability of these components.
- Aluminum and High-Strength Steel: As automakers increasingly turn to lightweight materials like aluminum and high-strength steel, TIP TIG welding provides the precision and control required for these materials’ successful integration.
Oil and Gas Industry
In the oil and gas sector, where welding is critical for the construction and maintenance of pipelines, offshore platforms, and other equipment, TIP TIG welding is applied in various ways:
- Pipelines: TIP TIG welding is used to create high-integrity welds in pipelines that transport oil and gas. Its efficiency and weld quality ensure the reliability and safety of these vital infrastructure components.
- Offshore Structures: Offshore platforms and structures are subjected to harsh environmental conditions. TIP TIG welding’s ability to produce corrosion-resistant and durable welds is invaluable in this industry.
Structural and Architectural Welding
TIP TIG welding has found applications in the construction and architectural sectors, where aesthetics and structural integrity are paramount:
- Structural Steel: TIP TIG welding is used for joining structural steel components in building construction. The clean and aesthetically pleasing welds meet architectural requirements while maintaining structural integrity.
- Ornamental Metalwork: Welders employ TIP TIG welding for creating ornamental metalwork, such as decorative railings, gates, and sculptures. Its precision and ability to deliver clean welds enhance the visual appeal of these artistic pieces.
Nuclear Industry
The nuclear industry demands exceptional precision and control in welding due to the critical nature of its components. TIP TIG welding is applied in various nuclear applications:
- Nuclear Power Plants: TIP TIG welding is used for welding components in nuclear power plants, including reactor vessels and piping systems. The ability to produce high-quality and defect-free welds is vital for safety and longevity.
- Research and Development: TIP TIG welding is employed in research and development efforts within the nuclear industry to fabricate and test specialized components for reactors and other nuclear technologies.
Challenges and Considerations
While TIP TIG welding offers numerous advantages, there are challenges and considerations that individuals and industries need to address to ensure the successful and safe implementation of this technology. This section explores key challenges and important considerations in TIP TIG welding.
Training and Skill Requirements for TIP TIG Welding
- Specialized Training: TIP TIG welding requires specialized training beyond standard welding techniques. Welders must be trained to operate and maintain the TIP TIG equipment, as well as understand the nuances of filler wire oscillation and its impact on the welding process.
- Advanced Skill Set: Achieving the full potential of TIP TIG welding demands a higher level of skill and expertise. Welders need to master the coordination of the filler wire oscillation system with the TIG arc, ensuring precise control.
- Adaptation Period: Transitioning to TIP TIG welding from traditional methods may require an adaptation period for welders to become proficient in this advanced technology.
Equipment and Maintenance Considerations
- Investment in Equipment: TIP TIG welding systems can be more expensive to acquire and set up compared to traditional welding equipment. This initial investment needs to be considered in budget planning.
- Equipment Maintenance: TIP TIG welding systems, like any complex machinery, require regular maintenance to ensure consistent performance. This includes maintaining the filler wire oscillation system, the power source, and the TIG torch. Routine maintenance schedules should be established and adhered to.
- Consumable Costs: While the tungsten electrode in TIP TIG welding is non-consumable, there are consumable costs associated with filler wires. These costs can add up, particularly in high-production environments, and should be factored into overall welding expenses.
Safety Precautions and Measures
- Inert Gas Handling: TIP TIG welding relies on the use of inert gases, which are typically non-toxic. Nevertheless, proper handling and storage of gas cylinders are crucial to avoid leaks, contamination, and potential safety hazards. Welders must be trained in the safe use of these gases.
- Arc Radiation: TIP TIG welding produces intense ultraviolet (UV) radiation and visible light. Welders and anyone in the vicinity must use appropriate eye protection, such as welding helmets with UV filters, to prevent eye damage and skin protection to prevent burns from arc radiation.
- Ventilation: Adequate ventilation is essential to disperse welding fumes and maintain a safe working environment. Local exhaust ventilation systems should be in place to remove fumes and gases generated during welding.
- Personal Protective Equipment (PPE): Welders should use appropriate PPE, including flame-resistant clothing, gloves, and welding boots, to protect themselves from heat, sparks, and potential hazards associated with the welding process.
- Fire Safety: Welding is a hot work process that carries the risk of fire. Fire prevention measures, such as the presence of fire extinguishers and fire-resistant barriers, should be in place to mitigate the risk.
- Training and Certification: Welders must receive proper training in TIP TIG welding and adhere to safety protocols. Obtaining certification in TIP TIG welding ensures that welders have met the required standards for safety and proficiency.
Future Developments
The field of welding is continually evolving, and TIP TIG welding is no exception. As technology and industry needs progress, there are several areas of potential advancements and emerging trends worth considering in TIP TIG welding and the broader welding industry.
Potential Advancements and Research in TIP TIG Welding
- Enhanced Filler Wire Oscillation Control: Ongoing research aims to refine and advance the control of the filler wire oscillation system in TIP TIG welding. This includes developing more sophisticated mechanisms and algorithms that allow for even greater precision in filler metal deposition.
- Materials Compatibility: Research is expanding the range of materials that can be effectively welded using TIP technology. This includes developing techniques for welding exotic materials, composites, and dissimilar metals, broadening the applications of TIP TIG welding.
- Automation and Robotics Integration: The integration of TIP TIG welding with automation and robotics is expected to advance further. This includes the development of advanced robotic systems that can perform TIP TIG welding with high precision, speed, and consistency.
- Remote Welding Solutions: Research and development efforts are focused on enabling remote or semi-autonomous welding systems, which can be especially useful in hazardous or hard-to-reach environments, such as offshore platforms and nuclear facilities.
- Online Monitoring and Quality Control: The integration of sensors and real-time monitoring systems into TIP TIG welding equipment is an emerging trend. These systems can monitor key parameters, detect defects, and provide immediate feedback to operators, contributing to improved quality control.
Emerging Trends and Technologies in Welding
- Laser Welding: Laser welding is gaining prominence in various industries due to its high precision and ability to weld materials with minimal heat input. It’s particularly valuable for micro-welding applications and for joining dissimilar materials.
- Additive Manufacturing: Welding and additive manufacturing are converging in innovative ways, with technologies like wire arc additive manufacturing (WAAM) and laser powder bed fusion (LPBF) enabling the creation of complex, fully 3D-printed metal components.
- Friction Stir Welding: This solid-state welding process is becoming more widely adopted for joining aluminum, particularly in the automotive and aerospace sectors. It offers benefits such as reduced heat-affected zones and improved mechanical properties.
- Welding Simulations: Computational tools and simulations are increasingly used to model and optimize welding processes. These simulations help predict welding outcomes, reduce trial and error, and optimize parameters for enhanced efficiency and quality.
- Welding in Space: As space exploration and commercial space industries grow, there is a need for welding technologies that can operate effectively in space environments. Research is ongoing to develop welding techniques suitable for space-based applications and repairs.
- Green Welding Technologies: There is a growing emphasis on environmentally friendly welding practices. Green welding technologies aim to reduce energy consumption, emissions, and waste, promoting sustainability in the welding industry.
Conclusion
TIP TIG welding, a fusion of Technologie Ingenieur Plasch (TIP) technology with the established Tungsten Inert Gas (TIG) welding process, stands as a significant advancement in the world of welding. As we conclude, let’s recap its significance and advantages, consider its role in the welding industry, and encourage further exploration and adoption in various sectors.