Tips for out-of-position welding
Table of Contents
ToggleIntroduction
Welding is a versatile skill that forms the backbone of numerous industries, contributing to the creation of structures and products that shape our world. Within the realm of welding, mastering the art of out-of-position welding is a crucial aspect that separates the novice from the expert. This comprehensive guide aims to delve into the intricacies of out-of-position welding, providing valuable tips and insights for welders looking to enhance their skills.
Understanding Out-of-Position Welding
Out-of-position welding refers to the technique of welding joints in positions other than the conventional flat position. Welding positions are classified into four main categories: flat, horizontal, vertical, and overhead. Each position presents its unique set of challenges, influenced by factors such as gravity, joint design, and material properties.
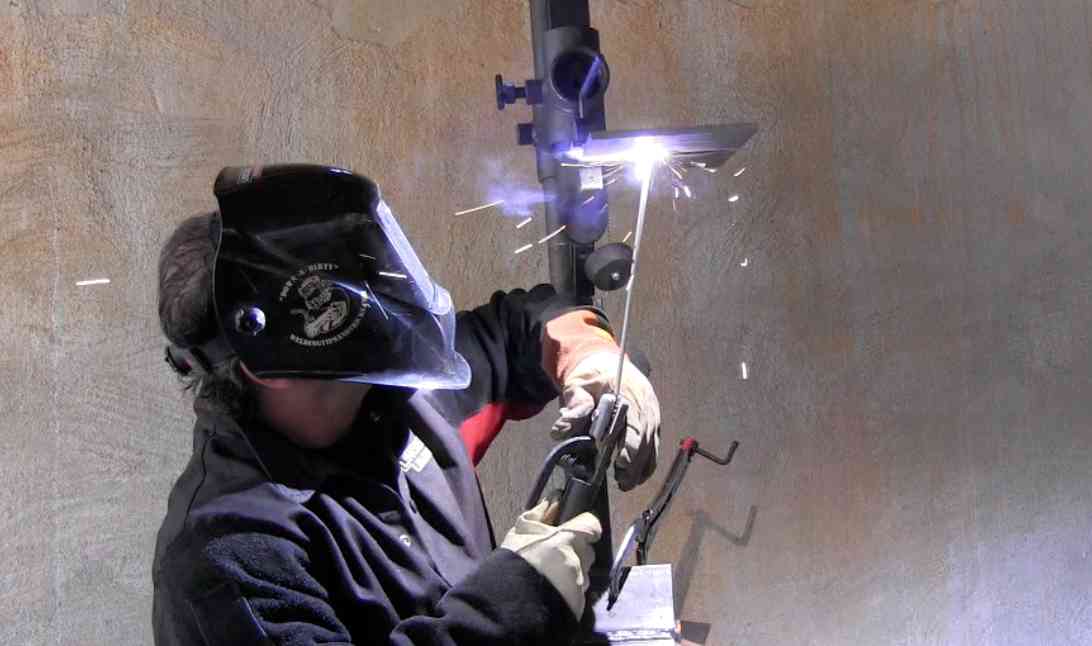
- Definition and Types of Welding Positions
- Flat Position:
The flat position involves welding on a horizontal surface, making it one of the easiest positions. Gravity has minimal influence, allowing for better control of the weld pool.
- Horizontal Position:
Welding in the horizontal position requires careful manipulation of the molten metal due to the gravitational pull. Proper technique is essential to ensure even bead placement.
- Vertical Position:
Vertical welding involves moving upward or downward. Gravity significantly affects the molten metal, making control and proper deposition challenging.
- Overhead Position:
Overhead welding is perhaps the most challenging, as gravity pulls the molten metal downward. Skillful technique and control are crucial to prevent defects such as undercutting.
Factors Influencing Welding Positions
- Gravity and Its Effects:
Understanding how gravity influences the molten metal is fundamental to successful out-of-position welding. Welders must adapt their technique to counteract the effects of gravity and ensure proper bead formation.
- Joint Design:
The type of joint being welded plays a significant role in determining the welding position. Some joints are naturally suited for certain positions, while others may require creative solutions to achieve optimal results.
- Material Properties:
Different materials respond differently to welding in various positions. Factors such as thermal conductivity and expansion rates must be considered when choosing welding parameters for out-of-position welding.
Mastering out-of-position welding begins with a solid understanding of the welding positions and the factors that influence them. In the following sections, we will explore the common welding processes used for out-of-position welding and provide practical tips for success.
Common Welding Processes for Out-of-Position Welding
Out-of-position welding can be achieved through various welding processes, each with its strengths and considerations. Understanding the suitability of these processes for different positions is crucial for achieving high-quality welds.
- Gas Metal Arc Welding (GMAW/MIG):Gas Metal Arc Welding, commonly known as MIG welding, is versatile and well-suited for out-of-position welding. The use of a shielding gas provides excellent control over the welding environment. MIG welding is particularly effective in the flat and horizontal positions.
- Shielded Metal Arc Welding (SMAW/Stick):Stick welding is a robust and widely used process for out-of-position welding. Its versatility makes it suitable for various positions, though it requires a skilled hand to control the arc and manage the slag effectively.
- Flux-Cored Arc Welding (FCAW):Flux-cored welding combines elements of MIG and stick welding, making it well-suited for out-of-position applications. The flux in the electrode helps protect the weld pool, making it effective in challenging positions like overhead welding.
- Gas Tungsten Arc Welding (GTAW/TIG):TIG welding is known for its precision and cleanliness. While more commonly used in flat and horizontal positions, TIG welding can be adapted for vertical and overhead welding with the right techniques and equipment.
- Submerged Arc Welding (SAW):Submerged Arc Welding is often used for flat position welding due to its high deposition rates. However, with the right setup and equipment adjustments, it can also be utilized in other positions.
Tips for Successful Out-of-Position Welding
Mastering out-of-position welding requires a combination of technique, equipment knowledge, and an understanding of the specific challenges posed by each welding position.
- Proper Joint Preparation:Joint preparation is crucial for successful out-of-position welding. Cleaning and beveling the joint edges ensure proper penetration and minimize the risk of defects. Attention to fit-up and alignment is equally important.
- Selection of Appropriate Electrode or Filler Metal:Choosing the right electrode or filler metal is essential for achieving the desired weld quality. Considerations such as material compatibility, position, and welding process play a crucial role in selection. Understanding the American Welding Society (AWS) classification system aids in making informed choices.
- Controlling Heat Input:Heat input significantly affects the welding process. Adjusting amperage and voltage, as well as managing travel speed and arc length, allows for control over the heat input. Maintaining the proper balance is essential to prevent issues like insufficient penetration or excessive heat-affected zones.
- Managing Welding Technique:The welding technique employed greatly influences the quality of the weld. Weaving and oscillation techniques help distribute heat evenly and promote better fusion. Understanding when to use a stringer bead or multi-pass approach is essential for achieving the desired results.
- Electrode Angle and Work Angle:Proper electrode and work angles contribute to the success of out-of-position welding. The angle of the electrode affects penetration and deposition rates. Adjusting these angles based on the welding position is crucial for optimal results.
- Utilizing Backing and Fixturing:Backing material and proper fixturing play a vital role in out-of-position welding. Backing helps prevent issues like lack of penetration, while effective fixturing ensures proper joint alignment. Employing these tools enhances overall weld quality.
- Monitoring and Adjusting for Joint Distortion:Out-of-position welding can lead to joint distortion. Pre-weld and in-process monitoring techniques, such as tack welding and proper sequencing, help mitigate distortion. Techniques for minimizing distortion, such as backstepping, can be employed during welding.
Safety Considerations in Out-of-Position Welding
Welding, by its nature, involves inherent risks, and these risks can be amplified when working in out-of-position situations. Ensuring the safety of the welder and those in the surrounding environment is paramount.
- Protective Gear and Equipment:Proper personal protective equipment (PPE) is essential for out-of-position welding. This includes but is not limited to welding helmets with appropriate shading, flame-resistant clothing, gloves, and steel-toed boots. The selection of PPE should consider the specific challenges posed by the welding position.
- Ventilation and Fume Extraction:Out-of-position welding can result in the generation of welding fumes and gases that pose respiratory hazards. Adequate ventilation and fume extraction systems are critical to maintaining a safe work environment. Welding in enclosed spaces or in positions that limit natural ventilation requires additional precautions.
- Fire Prevention and Control:Welding involves the use of intense heat, and in out-of-position scenarios, the risk of sparks and molten metal reaching combustible materials is heightened. Fire prevention measures, including the use of fire-resistant barriers and having fire extinguishing equipment readily available, are crucial.
- Training and Certification:Welders working in out-of-position scenarios should undergo specific training to understand the unique challenges associated with different welding positions. Certification programs validate a welder’s competence and adherence to safety standards. Continuous training updates keep welders informed about the latest safety practices.
Common Mistakes and Troubleshooting
Even with the best practices, out-of-position welding can present challenges that may lead to common mistakes. Identifying these issues early and implementing effective troubleshooting techniques is essential for maintaining weld quality.
- Inadequate Penetration:One common mistake is insufficient penetration, especially in vertical and overhead positions. This can be addressed by adjusting welding parameters, increasing amperage, and optimizing travel speed to ensure proper fusion.
- Excessive Spatter:Excessive spatter can result from improper shielding gas flow or incorrect voltage settings. Adjusting these parameters and ensuring proper cleanliness of the workpiece can minimize spatter.
- Lack of Fusion:Incomplete fusion at the joint interface can compromise weld strength. This issue may arise from improper technique or inadequate heat input. Adjusting travel speed and ensuring proper electrode angles can enhance fusion.
- Weld Cracking:Weld cracking is a common concern, particularly in out-of-position welding. Controlling heat input, preheating the base metal, and using appropriate filler metals can help prevent cracking.
- Undercutting:Undercutting occurs when excessive metal is melted away from the joint edges. This can be addressed by adjusting welding parameters, modifying travel speed, and maintaining proper electrode angles.
- Porosity:Porosity, or the presence of gas pockets in the weld, can result from inadequate shielding gas coverage or contaminated base metal. Ensuring proper gas flow and thorough cleaning of the joint area can reduce porosity.
- Addressing Common Issues Through Adjustments:Troubleshooting out-of-position welding requires a systematic approach. By identifying the specific issue, welders can make informed adjustments to welding parameters, technique, and equipment to rectify problems and prevent their recurrence.
Understanding common mistakes and having effective troubleshooting strategies at hand is essential for welders seeking to master out-of-position welding. In the following sections, we will explore real-world case studies and examples, providing practical insights into applying the tips and techniques discussed thus far.
Future Trends in Out-of-Position Welding
As technology continues to advance, the field of welding is evolving, and out-of-position welding is no exception. Exploring future trends provides a glimpse into the innovations that may shape the practices and techniques of welders in the years to come.
- Advances in Welding Technology:
- Automation and Robotics: The integration of automation and robotics in welding processes is on the rise. Automated systems equipped with advanced sensors and machine learning algorithms can enhance the precision of out-of-position welding, improving efficiency and repeatability.
- Augmented Reality (AR) in Welding: AR technologies can provide welders with real-time visual guidance during out-of-position welding. This includes overlays of welding parameters, joint details, and optimal paths, aiding welders in maintaining the desired quality.
- Automation and Robotics in Out-of-Position Welding:
- Automated Welding Systems: Fully automated welding systems designed for out-of-position welding are becoming more prevalent. These systems offer high accuracy and efficiency, reducing the reliance on manual labor for complex welding tasks.
- Robotics for Difficult-to-Access Areas: Robots designed to navigate and weld in confined or difficult-to-access spaces are being developed. These robots can significantly improve safety and productivity in out-of-position welding applications.
- Emerging Materials and Their Impact:
- Advanced High-Strength Alloys: The use of advanced high-strength alloys in various industries presents new challenges for out-of-position welding. Research and development efforts focus on adapting welding techniques to accommodate these materials while maintaining structural integrity.
- Lightweight Composite Materials: In industries such as aerospace, the trend toward lightweight composite materials requires innovative welding solutions. Laser welding and friction stir welding are being explored for their potential in out-of-position welding of these materials.
The future of out-of-position welding is intertwined with technological advancements that offer both challenges and opportunities. Welders embracing these trends and continuously updating their skills will be better positioned to thrive in an ever-evolving welding landscape.
Conclusion
In conclusion, the art of out-of-position welding encapsulates a multifaceted skill set, demanding a nuanced understanding of welding positions, a judicious selection of welding processes, and meticulous attention to technique. Mastery of this discipline is not merely a technical feat but an ongoing journey of refinement and adaptation.