Vertical Welding Vs. Horizontal Welding
Introduction
Welding stands as a cornerstone of modern fabrication, enabling the transformation of raw materials into intricate structures and products. Within the realm of welding, the orientation in which the process is conducted holds significant sway over the outcome. Vertical welding and horizontal welding, two distinct techniques, vie for supremacy in various applications, each bearing its own merits and challenges. The choice between these orientations can determine the strength, quality, and efficiency of the welded joint.
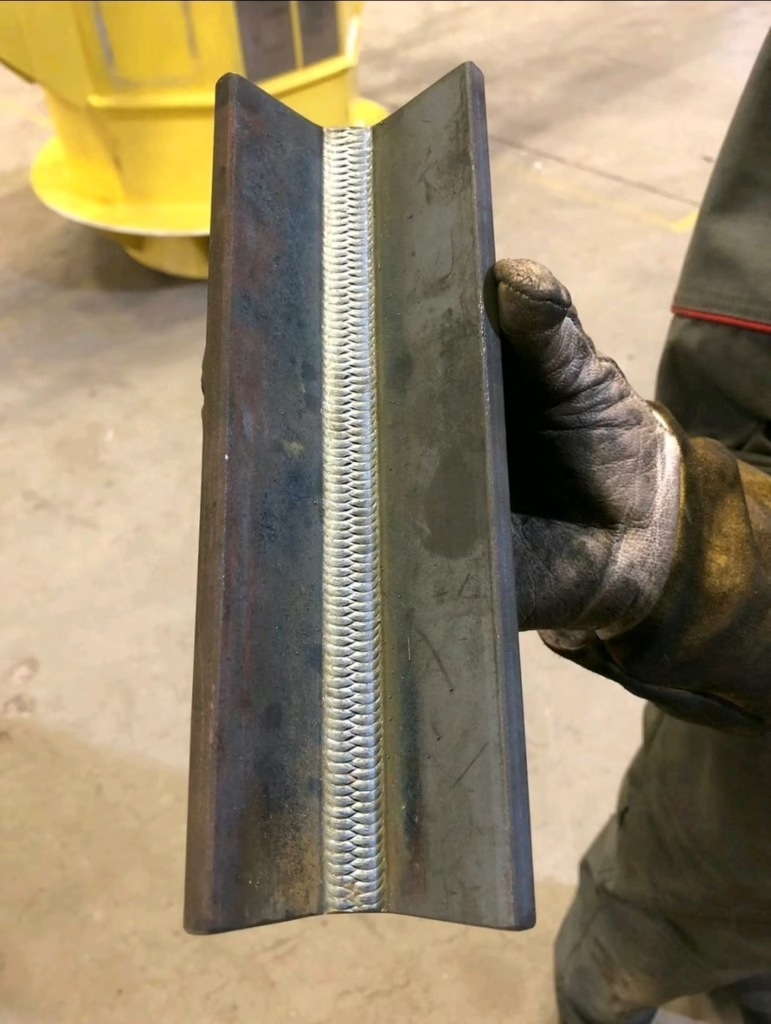
Vertical Welding
Explanation of Vertical Welding
Vertical welding involves joining materials in an upward or downward direction. The weld bead’s orientation is perpendicular to the ground, making it suitable for scenarios where materials need to be joined vertically.
Advantages
Reduced Distortion: Vertical welding experiences less distortion compared to other orientations due to the natural gravitational pull on the molten metal, resulting in a more stable weld pool.
Better Penetration: The downward force of gravity helps enhance weld penetration, ensuring a strong bond between the materials.
Improved Access: Vertical welding can provide improved access to joints that are difficult to reach horizontally, making it valuable in specific applications.
Challenges
Gravity Effects: While gravity aids penetration, it can also lead to challenges in controlling the weld pool’s shape and stability, requiring skilled techniques.
Welder Positioning and Comfort: Vertical welding demands precise positioning of the welder, which can be physically demanding and less comfortable than other orientations.
Applications
Shipbuilding: Vertical welding is extensively used in shipbuilding for joining various components, ensuring strong and durable connections.
Structural Steel Fabrication: Welding vertical joints in structural steel creates robust frameworks for buildings, bridges, and other large structures.
Pipe Welding: Vertical welding is crucial in pipeline construction, providing secure and reliable connections for transporting fluids and gases.
Horizontal Welding
Explanation of Horizontal Welding
Horizontal welding involves fusing materials along a horizontal plane, with the weld bead’s orientation parallel to the ground. This technique is particularly suitable for scenarios where materials need to be joined horizontally.
Advantages
Faster Deposition Rates: Horizontal welding allows for quicker deposition of filler material, increasing the welding speed and overall productivity.
Reduced Need for Repositioning: Welding horizontally minimizes the need for frequent repositioning of the workpiece, saving time and effort.
Better Visibility of the Weld Pool: The horizontal orientation offers improved visibility of the weld pool, enabling welders to monitor and control the welding process more effectively.
Challenges
Increased Distortion: The horizontal orientation can lead to higher distortion levels in the final weld due to the direction of gravity acting on the molten metal.
Weld Pool Control: Achieving precise control over the shape and size of the weld pool can be more challenging in horizontal welding scenarios.
Applications
Automotive Manufacturing: Horizontal welding is vital in automobile production, where it is used to join various components of vehicle frames and structures.
Rail Construction: Horizontal welding is employed in the fabrication of rail tracks and structures, ensuring reliable connections for safe and efficient rail transportation.
Pipeline Construction: Horizontal welding plays a crucial role in laying and joining pipes for pipelines, facilitating the transportation of fluids and gases over long distances.
Vertical vs Horizontal Welding
The comparison between vertical and horizontal welding reveals a dynamic interplay of advantages and challenges, each orientation uniquely influencing the welding process. Vertical welding, characterized by its upward or downward direction, offers reduced distortion due to the stabilizing effect of gravity on the molten metal. This results in stronger fusion and enhanced penetration, particularly beneficial for joints requiring utmost integrity. However, gravitational effects can also pose complexities in weld pool control, demanding skilled techniques. Vertical welding finds its forte in applications such as shipbuilding, structural steel fabrication, and pipe welding.
Factors Influencing Choice of Welding Orientation
Material Type and Thickness: Material properties and thickness influence the optimal welding orientation for achieving desired weld quality.
Joint Configuration: The shape and position of the joint affect the choice between vertical and horizontal welding.
Welding Process: Different welding processes (MIG, TIG, Stick, etc.) may perform differently in vertical and horizontal orientations.
Environmental Conditions: Factors like wind, humidity, and temperature can impact the choice of welding orientation for optimal results.
FAQs
What is vertical welding?
Vertical welding involves joining materials in an upward or downward direction, with the weld bead oriented perpendicular to the ground.
What are the advantages of vertical welding?
- Reduced distortion due to gravity.
- Enhanced penetration for strong bonds.
- Improved access for challenging joints.
What challenges does vertical welding pose?
- Contending with gravity effects on the weld pool.
- Ensuring precise welder positioning and comfort.
Where is vertical welding commonly applied?
- Shipbuilding.
- Structural steel fabrication.
- Pipe welding.
What is horizontal welding?
Horizontal welding entails fusing materials along a horizontal plane, with the weld bead parallel to the ground.
What are the benefits of horizontal welding?
- Faster deposition rates for increased productivity.
- Reduced need for frequent repositioning.
- Better visibility of the weld pool.
What challenges are associated with horizontal welding?
- Potential for increased distortion due to gravity.
- Complex control of the weld pool’s shape and size.
In which industries is horizontal welding frequently utilized?
- Automotive manufacturing.
- Rail construction.
- Pipeline construction.
Conclusion
The choice between vertical and horizontal welding, driven by the equilibrium of advantages and challenges, emerges as a testament to the artistry and skill that welding demands. In the forge of creation, whether in the towering structures of steel or the intricate pipelines that pulse with life, the decision between vertical and horizontal welding shapes the very foundations of our built world.