Common Welding Failures
Introduction
Welding is a fundamental process in manufacturing and construction, crucial for joining metals and creating structures of all kinds. However, despite its widespread use and importance, welding is not immune to failures. These failures, also known as welding defects, can compromise the integrity, strength, and safety of welded joints.
Definition of Welding Failure
Welding failure refers to any deviation from the desired or expected outcome in a welded joint. It encompasses a wide range of defects that can occur during the welding process, leading to compromised structural integrity or performance. These defects may result from various factors such as improper welding techniques, inadequate preparation, or material deficiencies.
Importance of Understanding Welding Failures
Understanding welding failures is critical for several reasons. Firstly, welding failures can pose significant safety risks, particularly in applications where structural integrity is paramount, such as in aerospace, automotive, or pressure vessel fabrication. Secondly, welding failures can lead to costly repairs, rework, or even the need for complete replacement of welded components, resulting in financial losses for individuals or organizations. Thirdly, identifying and addressing welding failures is essential for maintaining quality standards and ensuring compliance with industry regulations and codes.
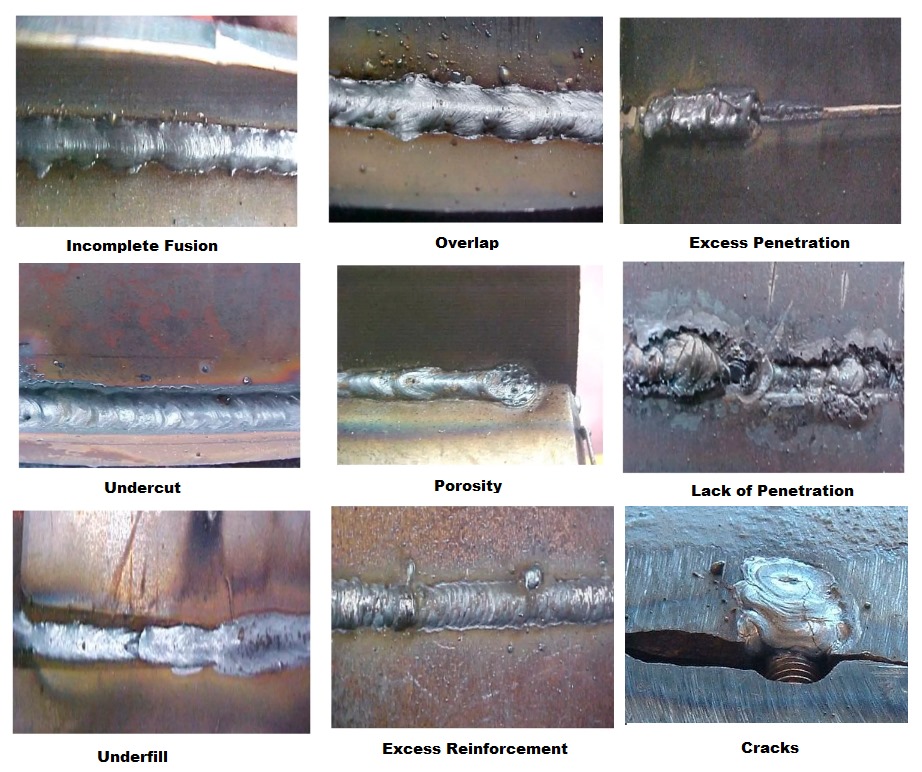
Effects of Welding Failure
Incomplete Fusion
- Definition and Causes Incomplete fusion occurs when the weld metal fails to fully fuse with the base metal or previous weld pass, leaving voids or unfused areas within the joint. This defect can result from insufficient heat input, improper welding technique, or inadequate cleaning of the base metal surface prior to welding.
- Consequences of Incomplete Fusion The consequences of incomplete fusion can be severe, compromising the strength, ductility, and fatigue resistance of the welded joint. Incomplete fusion creates weak points within the weld, making it susceptible to premature failure under load. Additionally, incomplete fusion can lead to porosity, which further reduces the mechanical properties of the weld and increases the risk of crack initiation and propagation.
Overlap
- Explanation and Occurrence Overlap occurs when the weld metal extends beyond the weld groove, forming a protrusion along the weld joint. This defect often occurs due to excessive weld deposition or improper welding technique, such as excessive travel speed or improper electrode angle.
- Impact on Weld Quality and Strength Overlap compromises the quality and strength of the weld by creating stress concentrations and reducing the effective cross-sectional area of the joint. The protrusion of excess weld metal can also interfere with the fit-up of adjacent components or introduce discontinuities that weaken the weld. Additionally, overlap can serve as a site for crack initiation and propagation, further compromising the integrity of the joint.
Lack of Penetration
- Definition and Common Reasons Lack of penetration refers to the failure of the weld to fully penetrate the thickness of the base metal, resulting in a weak and unreliable joint. Common reasons for lack of penetration include inadequate heat input, improper welding parameters, or insufficient preparation of the joint geometry.
- Effects on Structural Integrity Lack of penetration significantly reduces the load-bearing capacity and structural integrity of the welded joint. The lack of fusion between the weld metal and base metal results in a discontinuous bond, making the joint susceptible to failure under applied loads. In structural applications, lack of penetration can lead to catastrophic failure, posing serious safety risks to personnel and equipment.
Undercut
- Understanding Undercut in Welding Undercutting is characterized by a groove or depression along the weld toe, typically caused by excessive heat or improper welding technique. It occurs when the weld metal fails to completely fill the weld groove, leaving a void at the joint interface.
- Potential Risks and Implications Undercut compromises the structural integrity and fatigue resistance of the weld by reducing the effective cross-sectional area of the joint. The presence of undercut creates stress concentrations and weak points within the weld, making it susceptible to crack initiation and propagation. Additionally, undercut can lead to poor weld quality and aesthetic appearance, necessitating costly repairs or rework.
Rusty Welds
- Causes of Rust Formation in Welds Rust formation in welds can occur due to exposure to atmospheric moisture, improper storage of welding materials, or inadequate cleaning of base metals prior to welding. Rusty welds typically occur in environments with high humidity or corrosive atmospheres, where the protective oxide layer on the base metal surface is compromised.
- Impact on Weld Performance and Longevity Rusty welds compromise the performance and longevity of the weld by promoting corrosion and reducing the mechanical properties of the joint. The presence of rust weakens the bond between the weld metal and base metal, leading to reduced strength and increased susceptibility to cracking and failure. In corrosive environments, rusty welds can accelerate the degradation of the welded structure, necessitating frequent maintenance or replacement.
Lack of Fusion
- Definition and Contributing Factors Lack of fusion refers to the failure of the weld metal to completely fuse with the adjacent surfaces, resulting in a weak and unreliable joint. Contributing factors to lack of fusion include inadequate heat input, improper welding technique, or contamination of the weld zone.
- Consequences for Weld Strength and Durability Lack of fusion compromises the strength and durability of the weld by creating discontinuities and weak points within the joint. The absence of a continuous bond between the weld metal and base metal reduces the load-bearing capacity of the joint and increases the risk of premature failure under load. Lack of fusion can also lead to porosity and inclusion defects, further compromising the mechanical properties of the weld.
Underfill
- Explanation and Occurrence Underfill occurs when the weld metal does not adequately fill the weld groove or joint, leaving unfilled voids or gaps. This defect typically occurs due to insufficient weld deposition, improper welding technique, or poor fit-up of the joint components.
- Effects on Weld Integrity and Strength Underfill significantly reduces the integrity and strength of the weld by creating discontinuities and weak points within the joint. The presence of unfilled voids or gaps compromises the load-bearing capacity of the weld and increases the susceptibility to crack initiation and propagation. Underfill can also lead to poor weld quality and aesthetics, requiring rework or repair to meet performance standards.
Excess Reinforcement
- Defining Excess Reinforcement Excess reinforcement refers to an excessive buildup of weld metal above the surface of the base metal. This defect often occurs due to excessive weld deposition, improper welding technique, or inadequate control of welding parameters.
- Implications for Weld Quality and Appearance Excess reinforcement can adversely affect the quality and appearance of the weld by creating stress concentrations and reducing the fit-up of adjacent components. While excess reinforcement may not always compromise the mechanical properties of the weld, it can lead to aesthetic issues, dimensional inaccuracies, and difficulties in subsequent machining or assembly processes. Additionally, excess reinforcement can interfere with the performance of protective coatings or surface treatments, reducing the overall durability and corrosion resistance of the welded structure.
Cracks
- Types of Cracks in Welding Cracks in welding can occur in various forms, including longitudinal cracks, transverse cracks, crater cracks, and toe cracks. These cracks may originate from the weld metal, heat-affected zone, or base metal and can propagate under load or residual stress conditions.
- Significance and Potential Dangers Cracks in welding pose significant dangers to the structural integrity and safety of welded components. Cracks can propagate rapidly, leading to catastrophic failure without warning. Additionally, cracks serve as initiation sites for fatigue failure, corrosion, and stress corrosion cracking, further compromising the durability and reliability of the welded structure. Proper inspection, detection, and remediation of cracks are essential to prevent catastrophic failure and ensure the long-term performance of welded components.
Common Causes of Welding Failure
Welding failures can occur due to a variety of factors, ranging from procedural errors to material deficiencies. Understanding these common causes is essential for implementing preventive measures and ensuring the quality and reliability of welded joints.
Incorrect Welding Parameters
Incorrect welding parameters, such as improper voltage, current, or travel speed, can significantly affect the quality of the weld. Welding processes have specific parameter ranges that must be adhered to for optimal results. Deviating from these parameters can lead to defects such as incomplete fusion, lack of penetration, or excessive spatter. Moreover, improper welding parameters may result in poor bead appearance and compromised mechanical properties, reducing the overall integrity of the welded joint.
Poor Weld Preparation
Proper weld preparation is critical for achieving sound and durable welds. Poor weld preparation, such as inadequate cleaning or improper joint geometry, can lead to welding defects and reduced weld quality. Insufficient removal of surface contaminants, such as rust, oil, or paint, can result in contamination of the weld pool and the formation of defects like porosity or lack of fusion. Similarly, improper joint fit-up or misalignment can lead to gaps, underfill, or excessive reinforcement, compromising the structural integrity of the weld.
Insufficient Cleaning of Base Materials
Inadequate cleaning of base materials prior to welding can have detrimental effects on weld quality and performance. Surface contaminants, such as oils, greases, oxides, or mill scale, can inhibit proper fusion and lead to defects such as porosity, lack of fusion, or incomplete penetration. Additionally, contaminants present in the weld zone can introduce inclusions or impurities, weakening the weld and increasing susceptibility to corrosion or cracking. Proper cleaning and surface preparation are essential for ensuring clean, defect-free welds and maximizing the integrity of welded joints.
Inadequate Shielding Gas or Flux
The selection and application of shielding gas or flux are critical aspects of many welding processes, particularly gas metal arc welding (GMAW), gas tungsten arc welding (GTAW), and flux-cored arc welding (FCAW). Inadequate shielding gas coverage or improper flux application can result in weld defects such as porosity, oxidation, or excessive spatter. Insufficient shielding gas can also lead to incomplete fusion, lack of penetration, or excessive oxidation of the weld metal and base material. Proper selection and maintenance of shielding gas or flux are essential for protecting the weld pool from atmospheric contamination and ensuring the quality and integrity of the weld.
Lack of Operator Skill or Experience
The skill and experience of the welder play a crucial role in the quality and reliability of welded joints. Lack of operator skill or experience can lead to inconsistent weld bead profiles, improper weld technique, or inadequate heat control, resulting in defects such as undercut, incomplete fusion, or excessive reinforcement. Additionally, inexperienced welders may struggle with proper joint preparation, fit-up, or welding parameter selection, further increasing the risk of welding failures. Ongoing training, certification programs, and mentorship are essential for developing the skills and expertise of welders and ensuring the production of high-quality welds that meet performance standards and specifications.
Prevention and Remedies
Welding failures can have significant consequences on the integrity and reliability of welded joints. Preventing these failures and implementing effective remedies are crucial for ensuring the quality and safety of welded structures. Below are key prevention and remediation strategies:
Proper Training and Certification for Welders
Investing in proper training and certification programs for welders is essential for ensuring competency and proficiency in welding techniques and procedures. Welders should receive comprehensive training on welding processes, equipment operation, safety protocols, and quality control measures. Certification programs help validate the skills and expertise of welders, ensuring that they possess the necessary knowledge and capabilities to produce high-quality welds. Ongoing training and professional development opportunities are also essential for keeping welders up-to-date with the latest advancements in welding technology and best practices.
Strict Adherence to Welding Procedures and Standards
Strict adherence to established welding procedures and industry standards is critical for maintaining consistency, quality, and reliability in welding operations. Welding procedures should be developed based on industry-accepted practices, manufacturer recommendations, and applicable codes and standards. Welders must follow these procedures meticulously, including proper joint preparation, welding parameters, and post-welding treatments. Adhering to welding standards helps minimize the risk of defects, ensures compliance with regulatory requirements, and promotes uniformity and consistency in weld quality.
Thorough Inspection of Materials and Joint Preparation
Thorough inspection of materials and joint preparation is essential for identifying potential defects and ensuring the integrity of the welded joint. Before welding, materials should be inspected for surface contaminants, defects, or inconsistencies that could compromise weld quality. Proper joint preparation, including cleaning, beveling, and fit-up, is critical for achieving sound welds and maximizing joint strength. Inspection techniques such as visual inspection, non-destructive testing (NDT), and destructive testing should be employed to verify weld quality, detect defects, and confirm compliance with specifications.
Regular Maintenance of Welding Equipment
Regular maintenance of welding equipment is essential for ensuring optimal performance, reliability, and safety in welding operations. Welding equipment should be inspected regularly for signs of wear, damage, or malfunction, and any issues should be addressed promptly. Routine maintenance tasks, such as cleaning, lubrication, calibration, and replacement of worn components, should be performed according to manufacturer recommendations and maintenance schedules. Proper maintenance helps prevent equipment failures, reduces downtime, and ensures consistent weld quality.
Implementation of Quality Control Measures
Implementation of quality control measures throughout the welding process is crucial for detecting and mitigating defects and ensuring the quality and reliability of welded joints. Quality control measures may include establishing welding procedure specifications (WPS), conducting pre-welding inspections, monitoring welding parameters during the welding process, and performing post-welding inspections and testing. Additionally, documenting welding procedures, materials, and inspection results helps track and trace weld quality and facilitates continuous improvement efforts. By implementing robust quality control measures, welders can identify potential issues early, address them promptly, and deliver welds that meet or exceed customer requirements and industry standards.
FAQs
What is the most common cause of incomplete fusion in welding?
Incomplete fusion in welding is often caused by inadequate heat input or improper welding technique.
How can overlap affect the structural integrity of a weld?
Excessive overlap can weaken the weld joint and increase the risk of stress concentration, leading to premature failure.
What are the main differences between lack of fusion and lack of penetration?
Lack of fusion refers to the failure of the weld metal to fuse completely with the base metal or previous weld pass, while lack of penetration occurs when the weld metal fails to penetrate fully into the base metal or root of the joint.
Is rust always a sign of welding failure?
Rust on welds can indicate inadequate surface preparation or exposure to corrosive environments, but it may not necessarily indicate welding failure.
Can cracks in welds be repaired, or is it necessary to redo the entire weld?
Depending on the severity and location of the cracks, they may be repaired using various welding and non-destructive testing techniques. However, in some cases, redoing the entire weld may be necessary to ensure structural integrity.
Conclusion
In conclusion, addressing welding failures requires a proactive approach, a commitment to quality, and a dedication to continuous improvement. By prioritizing preventive measures, investing in training and certification, and embracing ongoing education, welders can mitigate the risks of welding failures, ensure the integrity and reliability of welded joints, and uphold the highest standards of quality and safety in welding operations. Together, we can build a safer, stronger, and more resilient future through excellence in welding practices.