Welding High-Speed Steel
Welding high-speed steel (HSS) requires specialized knowledge due to its unique composition and properties. In this comprehensive guide, we’ll dive into each stage of the welding process, from preparation to post-welding treatment, covering the techniques and precautions needed to achieve high-quality results with HSS. Let’s explore how to weld HSS effectively, avoid common pitfalls, and produce durable welds that can withstand high temperatures and stress.
Introduction to High-Speed Steel Welding
Understanding High-Speed Steel (HSS)
High-speed steel (HSS) is an alloy known for maintaining hardness at high temperatures, making it ideal for cutting tools, drills, and other equipment exposed to intense heat and friction. The steel derives its name from its ability to cut other materials at high speeds without losing effectiveness. High-speed steel typically contains elements like tungsten, molybdenum, chromium, and sometimes cobalt, which give it its remarkable resistance to wear, abrasion, and high temperatures.
Importance of Welding High-Speed Steel
Welding high-speed steel is critical in tool repair, manufacturing, and fabrication industries where the metal’s unique properties are required for specific applications. Welding enables the extension of tool life by allowing damaged or broken high-speed steel components to be repaired or modified rather than replaced. It also helps in custom fabrications, which demand high wear resistance and strength.
Properties of High-Speed Steel Relevant to Welding
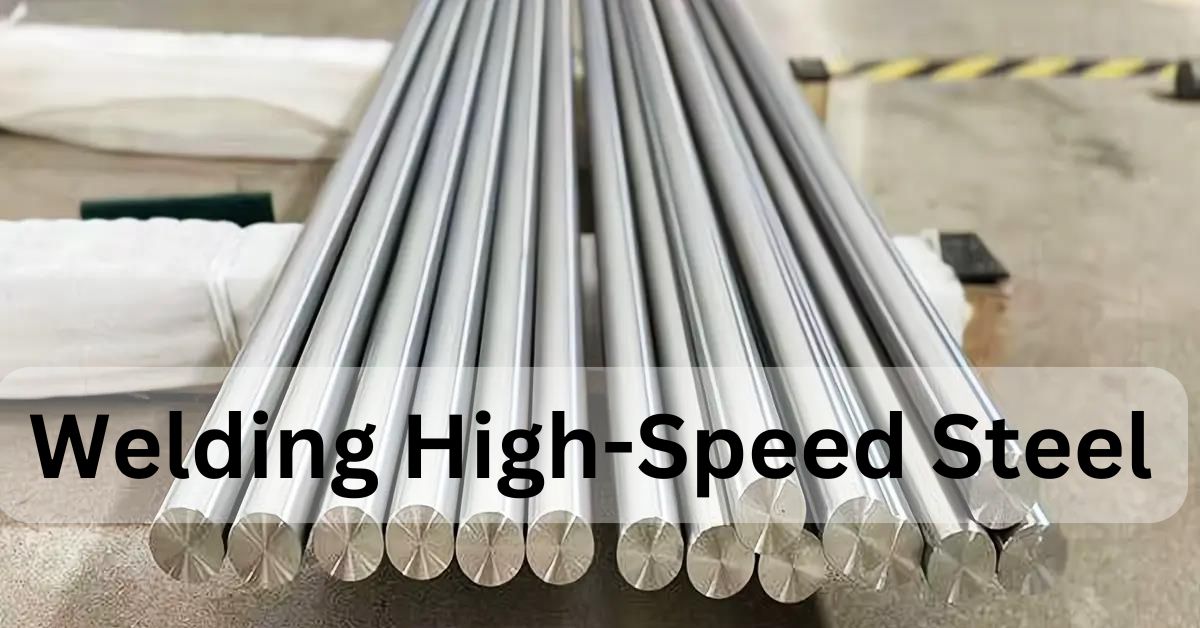
Composition of High-Speed Steel
HSS is an alloy typically composed of tungsten, molybdenum, chromium, and sometimes cobalt. These elements contribute to its high hardness, durability, and heat resistance. The exact composition can vary, leading to different types of HSS, each suited to specific applications. For example, tungsten-based HSS tends to withstand high temperatures well, while molybdenum-based variants may offer additional flexibility.
Heat Resistance and Hardness
High-speed steel retains its hardness even at high temperatures (up to around 600°C or more). This heat resistance can complicate welding because the high heat required for welding may cause cracking if not managed properly. The steel’s hardness is due to a fine-grain structure that is sensitive to thermal stress, which means it can quickly become brittle if cooling isn’t carefully controlled.
Challenges in Welding High-Speed Steel
Welding HSS presents challenges, such as cracking and distortion. The heat-affected zone (HAZ) – the area of the steel that is altered by the welding heat – can become brittle if too much heat is applied or if cooling is too rapid. Special care is needed to control the heat input and cooling rates to prevent these issues, which can compromise the strength and durability of the weld.
Common Applications of High-Speed Steel Welding
Industrial Use Cases
High-speed steel is extensively used in industrial manufacturing for cutting tools like drill bits, saw blades, and end mills. The need to weld HSS arises when these tools require repair or modification, which is often more cost-effective than producing new tools. HSS welding is also used in the automotive and aerospace sectors, where components must endure high temperatures and mechanical stress.
Tool Fabrication and Repair
Since HSS tools are costly to produce, welding is a popular option to repair or reshape broken or worn-out tools. This extends the life of the tool while maintaining its performance characteristics. Welded HSS tools can continue to perform at high levels of durability and precision when repaired correctly, which is particularly important in precision manufacturing.
Specialized Welding in Precision Equipment
High-speed steel is sometimes used in precision equipment where accuracy, sharpness, and durability are vital. Welding HSS allows these precision components to be modified or repaired to exacting standards. This process, however, requires careful welding to avoid any distortion or compromise of the part’s precision.
Preparing High-Speed Steel for Welding
Cleaning and Surface Preparation
Preparation is critical for successful HSS welding. The surfaces must be thoroughly cleaned to remove any oil, rust, grease, or other contaminants. Contaminants can weaken the weld joint, causing imperfections or poor fusion between the base metal and the filler. Using a wire brush or chemical cleaner can help in achieving a pristine surface.
Preheating Requirements for HSS
Preheating is essential when welding high-speed steel to reduce thermal shock and minimize the risk of cracking. The preheat temperature varies but is typically between 400°C to 600°C, depending on the type of HSS. Preheating reduces the difference between the welding temperature and the base temperature of the steel, making cooling more gradual and controlled, which is critical to preventing brittleness in the weld.
Choosing the Right Filler Material
Using the appropriate filler material is crucial for HSS welding to maintain the base metal’s characteristics. Typically, a filler that closely matches the base metal composition is selected to ensure compatibility and maintain hardness and durability. The right filler also reduces the likelihood of creating weak points in the weld that could crack or break under stress.
Selecting the Right Welding Technique
Shielded Metal Arc Welding (SMAW)
Shielded Metal Arc Welding, or SMAW, is a versatile and commonly used welding technique. However, due to the high heat generated, SMAW requires strict control to avoid overheating the HSS, which can lead to cracking. SMAW can be useful for welding thicker sections of HSS or repairing large tools.
Gas Tungsten Arc Welding (GTAW)
Also known as TIG welding, GTAW is ideal for HSS due to its precise control over heat input. This method is often preferred for thin sections or detailed welds where minimal heat input is needed to avoid damaging the steel’s microstructure. GTAW is favored in applications requiring high-quality, precision welds, such as in tool repairs.
Laser Beam Welding (LBW)
Laser Beam Welding (LBW) is an advanced method that provides highly concentrated heat, allowing for a precise weld with minimal heat-affected zones. This method is effective for thin, high-speed steel components, reducing distortion and avoiding unnecessary hardening of the HAZ. LBW is common in high-precision applications.
Comparison of Welding Techniques
Each technique has unique advantages and limitations. SMAW is cost-effective for general repairs, while GTAW and LBW offer finer control. Selection depends on the specific HSS properties and the application requirements, including the thickness of the material and the level of precision needed.
Welding High-Speed Steel: Step-by-Step Process
Setting Up the Equipment
Setting up for welding involves selecting the correct equipment and parameters. Choosing the right electrode, filler, and settings for heat and voltage is crucial for achieving a strong, crack-free weld. Equipment setup also involves adjusting the welding machine to match the material thickness and desired outcome.
Managing Heat Input and Temperature Control
Excessive heat can cause HSS to lose its hardness or develop cracks. Controlling the heat input during the weld by using short, controlled passes and adjusting the amperage and voltage is vital. Maintaining the correct temperature ensures that the base metal doesn’t become too brittle and helps avoid weakening the HAZ.
Avoiding Cracks and Distortion
HSS is prone to cracking if cooled too quickly or heated unevenly. To avoid cracks, controlled cooling and uniform heat application are necessary. Distortion can be minimized by using fixturing devices and monitoring the weld pool size to prevent excess metal from spreading.
Cooling Down Procedures
Post-weld cooling should be gradual to prevent thermal stress. Techniques like placing the workpiece in a heat-resistant blanket or using controlled air cooling can help. Gradual cooling helps retain the strength and integrity of the weld and avoids unwanted brittleness.
Post-Welding Treatments for High-Speed Steel
Stress Relief and Annealing
Stress relief and annealing reduce residual stress, helping to stabilize the welded structure and prevent cracks. Annealing involves heating the welded part to a temperature below its melting point, then slowly cooling it, which softens the metal and enhances durability.
Tempering Process
Tempering is performed after welding to restore hardness and reduce brittleness. The tempering temperature depends on the specific type of HSS and the desired mechanical properties. This process ensures that the welded joint is not only durable but also able to handle high-speed applications effectively.
Hardness Testing
Post-weld hardness testing verifies that the HSS retains its expected hardness levels. Testing ensures that the metal has not lost its wear resistance and can perform as needed in its intended applications.
Common Challenges and Solutions
Addressing Cracking Issues
Cracking can occur due to rapid cooling or inadequate preheating. Solutions include preheating, using slow, controlled cooling, and selecting compatible filler materials to ensure a strong, crack-free weld.
Managing Heat-Affected Zones (HAZ)
The HAZ can weaken the material if too much heat is applied. Managing the HAZ involves careful control of heat input, using preheating, and choosing welding methods that minimize the extent of the HAZ, such as GTAW or LBW.
Reducing Brittleness in Welded Joints
To reduce brittleness, gradual cooling, tempering, and stress relief treatments are employed. These techniques help restore flexibility to the material and prevent fractures.
Safety Considerations
Protecting Against Fumes and Metal Dust
Welding HSS can release hazardous fumes and particles, particularly when alloyed with elements like chromium or cobalt. Proper ventilation, respirators, and protective clothing are crucial to protect welders from these toxic byproducts.
Preventing Burns and Eye Damage
The intense heat and light generated during HSS welding necessitate proper protective gear, such as heat-resistant gloves, face shields, and safety glasses. Additionally, handling preheated HSS requires caution due to high temperatures.
Safe Handling of Equipment and Materials
Handling HSS requires careful planning to avoid mishaps. Proper storage and handling prevent injury, while safety training ensures welders understand and mitigate the risks associated with high-temperature welding.
FAQs
What are the main challenges in welding high-speed steel?
The biggest challenges are managing heat input to avoid cracking and maintaining the material’s hardness after welding.
How does preheating affect the welding of high-speed steel?
Preheating reduces thermal shock, lowering the risk of cracks and improving weld quality.
What is the best welding technique for high-speed steel?
GTAW (TIG) and LBW are effective for precision, while SMAW is popular for general use, depending on the application.
Why is tempering necessary after welding high-speed steel?
Tempering restores hardness and reduces brittleness, making the weld stronger and more durable.
How can I reduce the risk of cracks when welding high-speed steel?
Preheating, controlled cooling, and using compatible filler materials help reduce the risk of cracks.
Conclusion
Welding high-speed steel is challenging but manageable with the right techniques, equipment, and safety measures. By understanding HSS properties, selecting the appropriate welding method, and following necessary post-weld treatments, welders can achieve durable, high-performance welds that meet the demands of industrial applications. Effective HSS welding allows for the repair, customization, and enhancement of critical tools and components, proving to be a valuable skill in specialized manufacturing and repair sectors.