Welding in Automobile Sector: Enhancing Structural Integrity and Safety
Introduction
In the dynamic world of automotive manufacturing, welding plays a crucial role in ensuring the structural integrity, safety, and overall performance of vehicles. The welding process binds various components together, creating a cohesive unit that can withstand the demands of the road. In this article, we’ll delve into the realm of welding in the automobile sector, exploring its importance, techniques, challenges, and advancements.
Welding in Automobile Sector: Driving Innovations Forward
The Welding in Automobile Sector is an indispensable aspect that shapes modern vehicles. The fusion of various materials through precise welding techniques ensures that vehicles are not only mechanically robust but also safe for passengers. This section will explore the various welding methods employed in the automobile sector.
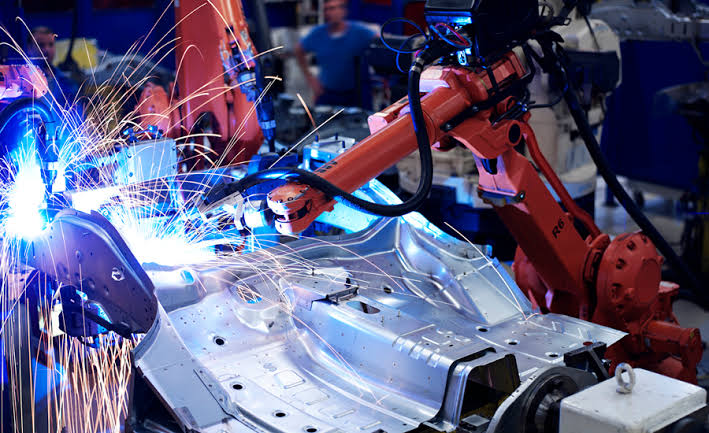
Traditional Spot Welding: A Strong Foundation
Traditional spot welding remains a cornerstone in automobile manufacturing. It involves the use of electricity to join metal sheets by creating localized heat through resistance. This method is efficient, economical, and provides strong bonds, making it ideal for components like the vehicle’s chassis and body panels.
Laser Welding: Precision Redefined
Laser welding, a cutting-edge technique, involves the use of high-intensity lasers to fuse metal components. Its precision and minimal heat-affected zone make it suitable for intricate parts such as sensors, electronic components, and advanced safety systems. The Welding in Automobile Sector has benefited greatly from this technology, enabling manufacturers to create lighter, safer, and more efficient vehicles.
Friction Stir Welding: Uniting Dissimilar Materials
Friction stir welding is revolutionizing the industry by enabling the joining of dissimilar materials, such as aluminum and steel. This technique uses frictional heat generated by a rotating tool to create a weld. The resulting joints are strong, lightweight, and corrosion-resistant, contributing to fuel efficiency and extended vehicle lifespan.
Resistance Spot Welding: Ensuring Electrical Connectivity
In addition to structural integrity, welding is essential for ensuring proper electrical connectivity throughout the vehicle. Resistance spot welding is widely employed to create reliable electrical connections, contributing to the seamless operation of various systems, including lighting, entertainment, and safety features.
Challenges and Innovations in Welding Techniques
The Welding in Automobile Sector isn’t without its challenges. As vehicles become more complex and materials diversify, welding techniques must adapt. This section delves into the obstacles faced by manufacturers and the innovative solutions that have emerged.
Overcoming Material Diversity
Modern vehicles incorporate an array of materials, from traditional steel to advanced composites. Welding these diverse materials requires specialized techniques, such as hybrid welding, which combines laser and arc welding to effectively join dissimilar components without compromising structural integrity.
Enhancing Structural Rigidity
As vehicle safety regulations become more stringent, manufacturers must enhance the structural rigidity of their vehicles. Innovative welding methods, like tailored blank welding, enable the precise joining of materials with varying thicknesses, resulting in components that offer both strength and weight reduction.
Addressing Thermal Distortion
Heat generated during welding can lead to thermal distortion, affecting the vehicle’s dimensional accuracy and performance. Manufacturers are implementing techniques like adaptive welding, which adjusts parameters in real-time to mitigate distortion and ensure consistent weld quality.
Advancements Driving the Future
The world of automobile welding is in constant evolution, driven by technological advancements and the pursuit of safer, more efficient vehicles. This section highlights some of the latest developments that are shaping the future of Welding in the Automobile Sector.
Additive Manufacturing: Redefining Possibilities
Additive manufacturing, often referred to as 3D printing, has found its way into automobile manufacturing. Through techniques like selective laser melting, components can be built layer by layer, allowing for intricate designs, reduced material waste, and improved strength-to-weight ratios.
Smart Welding Robots: Precision and Efficiency
Automation is transforming the welding process with the introduction of smart welding robots. These robots utilize advanced sensors and algorithms to perform intricate welds with unparalleled precision, increasing efficiency and consistency while reducing human error.
Improved Weld Inspection: Ensuring Quality
Quality control is paramount in welding. Advancements in non-destructive testing methods, such as ultrasonic and radiographic testing, enable manufacturers to detect defects and inconsistencies without compromising the integrity of the welded components.
FAQs
How does welding contribute to vehicle safety?
Welding ensures the structural integrity of vehicles, enhancing their ability to withstand collisions and other road hazards, thereby ensuring passenger safety.
What challenges do manufacturers face in welding diverse materials?
Manufacturers encounter challenges in joining dissimilar materials, as their melting points and properties differ. Hybrid welding techniques, like laser-arc welding, offer solutions for such scenarios.
How is additive manufacturing changing automobile welding?
Additive manufacturing allows for intricate designs and reduced material waste, transforming the way components are produced and assembled.
What role do smart welding robots play in the industry?
Smart welding robots automate the welding process, improving precision and efficiency while reducing the potential for human error.
How does welding impact the longevity of vehicles?
Welding techniques like friction stir welding create strong, corrosion-resistant joints, contributing to the extended lifespan of vehicles.
What is the significance of quality control in welding?
Quality control methods, such as ultrasonic and radiographic testing, ensure that welded components meet rigorous safety and performance standards.
Conclusion
As the automobile sector continues to innovate, welding remains a fundamental process that underpins vehicle safety, performance, and longevity. From traditional spot welding to cutting-edge additive manufacturing, the diverse techniques and advancements in welding empower manufacturers to create vehicles that are not only reliable but also pushing the boundaries of design and engineering.