Welding Metallurgy And Properties of Metals
Introduction
Welding metallurgy is the study of how the properties of metals are affected by the welding process. This field of metallurgy is important for understanding how to properly join different types of metals in order to create a strong and durable weld. In this article, we will explore the basics of welding metallurgy and the properties of metals that are important in welding technology. We will also discuss the various types of welding processes and the effects they have on the properties of the metals being joined. Understanding welding metallurgy is crucial for those involved in the design, fabrication, and repair of metal structures and products.
What is Welding Metallurgy?
Welding metallurgy is the scientific study of the properties, behavior, and manipulation of metals during the welding process. It involves understanding the effects of heat, pressure, and other factors on the metal being welded, as well as the properties of the finished weld. This knowledge is used to optimize the welding process, improve the quality of the weld, and minimize the risk of defects or failure. It also includes the selection of appropriate welding techniques and materials, and the design of welding procedures and parameters.
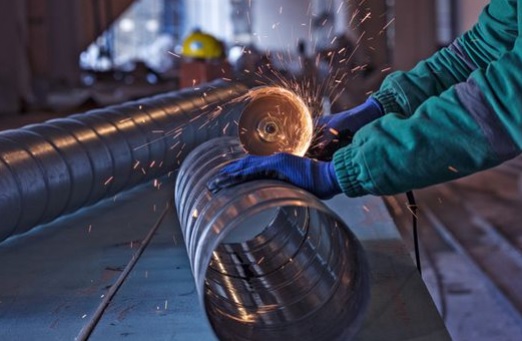
Types of Metals
There are many different types of metals that can be used in welding, including ferrous and nonferrous metals.
Ferrous metals, such as carbon steel and cast iron, are commonly used in welding. They contain iron and small amounts of carbon, which makes them strong and durable. However, they are also prone to rust and corrosion. Low-alloy steels, which contain small amounts of other elements such as nickel and chromium, are also commonly used in welding. These additional elements improve the corrosion resistance and toughness of the metal.
Nonferrous metals, such as aluminum, copper, and nickel, are also used in welding. These metals do not contain iron and are often used in applications where corrosion resistance is a primary concern. Aluminum and copper are lightweight and have good electrical conductivity, making them useful in electrical and electronic applications. Nickel is resistant to corrosion and high temperatures, making it useful in power generation and chemical processing industries.
In addition, there are also other types of metals such as stainless steel, titanium, and magnesium, which are commonly used in specific applications due to their unique properties. It is important to note that the type of metal used in welding will affect the type of welding process and filler metal used, as well as the final properties of the welded joint. A proper selection of the welding process, filler metal and proper technique, is crucial to achieve a good quality weld and obtain the desired properties of the final joint.
For example, aluminum and copper are lightweight and have good thermal conductivity, but they are also prone to warping and bending during welding, which can make welding more difficult. On the other hand, steels have higher melting point, but with proper selection of filler metal and welding process, steels can be welded with relative ease. Stainless steel is known to be more difficult to weld than mild steel because it is prone to warping and cracking, but with proper techniques and filler metals, it can be welded with good results. In general, nonferrous metals such as aluminum and copper tend to be more difficult to weld than ferrous metals such as carbon steel, but with proper techniques and equipment, they can be welded successfully.
Here in this article we will dicuss welding metallurgy and properties of metals.
Properties of Metals
Metals are a class of materials that are characterized by their metallic bonding, which results in high electrical conductivity and thermal conductivity
1-Physical Properties
In welding, the physical properties of the metal being welded play a critical role in determining the success of the weld. Some of the most important physical properties of metals in welding include:
- Melting point
The melting point of a metal is the temperature at which it changes from a solid to a liquid state. The melting point of a metal affects the type of welding process that can be used, as well as the filler metal that is required. For example, metals with a high melting point, such as nickel-based alloys, require specialized welding processes and filler metals.
- Thermal conductivity
Thermal conductivity is a measure of a metal’s ability to conduct heat. Metals with high thermal conductivity, such as aluminum and copper, are more likely to warp or bend during welding, while metals with low thermal conductivity, such as stainless steel, are less likely to be affected by the heat of welding.
- Thermal expansion
Thermal expansion is the change in a metal’s dimensions due to a change in temperature. Metals with different thermal expansion coefficients may experience different levels of stress and distortion during the welding process, which can affect the quality of the weld.
- Density
Density is a measure of the mass of a material per unit volume. The density of a metal affects its weight and strength, and can impact the welding process. For example, lightweight metals such as aluminum are easier to handle and manipulate during welding, while denser metals such as tungsten may require specialized equipment and techniques to be welded effectively.
- Hardness
Hardness is a measure of a metal’s resistance to deformation. Harder metals may require more specialized welding techniques and equipment to be welded effectively, while softer metals may be more easily welded.
- Conductivity
Conductivity is a measure of a metal’s ability to conduct electricity. Metals with high electrical conductivity, such as copper and aluminum, are commonly used in electrical and electronic applications, while metals with low electrical conductivity, such as stainless steel, are less likely to be affected by the electrical current of welding.
2-Mechanical Properties
In welding, the mechanical properties of metals are important to consider because they can affect the strength and integrity of the welded joint. Some common mechanical properties of metals that are relevant to welding include:
- Tensile strength
The maximum amount of tensile stress a metal can withstand before breaking or failing.
- Yield strength
The amount of stress at which a material begins to deform plastically.
- Elasticity
The ability of a metal to return to its original shape after being deformed.
- Ductility
The ability of a metal to be stretched or deformed without breaking.
- Hardness
The resistance of a metal to deformation or scratching.
- Toughness
The ability of a metal to absorb energy and deform without breaking.
- Fatigue Resistance
The ability of a metal to withstand cyclic loading without failure.
- Creep Resistance
The ability of a metal to withstand high levels of stress without deforming over time.
- Corrosion Resistance
The ability of a metal to resist corrosion or deterioration in a specific environment.
Weldability of Metals
The properties of metals can have a significant impact on their weldability, which is the ability of a metal to be welded without cracking, warping, or other defects. Some of the properties that affect weldability include:
Melting point
Metals with a high melting point, such as nickel-based alloys, can be more difficult to weld because they require specialized welding techniques and filler metals.
Thermal conductivity
Metals with high thermal conductivity, such as aluminum and copper, can warp or bend during welding, making them more difficult to weld.
Thermal expansion
Metals with different thermal expansion coefficients may experience different levels of stress and distortion during the welding process, which can affect the quality of the weld.
Hardness
Harder metals may require more specialized welding techniques and equipment to be welded effectively, while softer metals may be more easily welded.
Carbon content
Higher carbon content can make steel harder and more brittle, which can make welding more difficult and increase the chances of cracking or warping.
Welding Techniques and Types of Metals
There are several common welding techniques that are used for different types of metals. Some examples include:
- Gas metal arc welding (GMAW) is a common welding technique that is used for a wide range of metals, including carbon steel, stainless steel, and aluminum.
- Gas tungsten arc welding (GTAW) is a precise welding technique that is often used for welding thin sections of metal and for welding metals with high melting points, such as nickel-based alloys.
- Shielded metal arc welding (SMAW) is a common welding technique that is used for welding carbon steel and other ferrous metals.
- Submerged arc welding (SAW) is a high-productivity welding technique that is often used for welding thick sections of metal.
Common Metals Used in Welding
1-Carbon steel is a commonly used metal in welding. It is made up of iron and small amounts of carbon, which gives it its strength and durability. Carbon steel is widely used in the construction and manufacturing industry, for example, bridges, buildings, machinery and vehicles. It is also relatively inexpensive and easy to weld with various welding methods such as Shielded Metal Arc Welding (SMAW), Gas Metal Arc Welding (GMAW), and Gas Tungsten Arc Welding (GTAW).
2-Stainless steel is another commonly used metal in welding. It is known for its excellent corrosion resistance and high strength. Stainless steel is used in a wide range of applications, such as kitchen utensils, medical instruments, and chemical processing equipment. It is also commonly used in the construction of buildings and infrastructure. Welding stainless steel requires specialized techniques and filler metals to prevent warping and cracking. Gas Tungsten Arc Welding (GTAW) and Gas Metal Arc Welding (GMAW) with filler metals are the common techniques used.
3-Aluminum is a lightweight metal that is often used in welding. It is used in the aerospace, transportation, and construction industries, as well as in electronic and electrical applications. Welding aluminum requires specialized techniques and filler metals to prevent warping and cracking. Gas Tungsten Arc Welding (GTAW) and Gas Metal Arc Welding (GMAW) are the most common welding methods used for aluminum.
4-Copper and brass are nonferrous metals that are used in welding. They are known for their good electrical conductivity and corrosion resistance. Copper and brass are commonly used in electrical and electronic applications, as well as in plumbing and construction. Welding copper and brass can be challenging due to their high thermal conductivity and tendency to warp and crack. Gas Tungsten Arc Welding (GTAW) and Gas Metal Arc Welding (GMAW) with filler metals are the common techniques used.
5-Nickel and its alloys are also commonly used in welding. Nickel is known for its excellent corrosion resistance and high strength. It is used in power generation and chemical processing industries. Nickel-based alloys such as Inconel and Hastelloy are also commonly used in these industries due to their excellent high-temperature strength and corrosion resistance. Welding nickel and its alloys requires specialized techniques and filler metals to prevent warping and cracking. Gas Tungsten Arc Welding (GTAW) and Gas Metal Arc Welding (GMAW) with filler metals are the common techniques used for nickel and its alloys.
FAQs
Why is metallurgy important in welding?
Metallurgy is important in welding because it plays a key role in understanding how different metals behave when heated and cooled, and how they respond to various welding techniques. This understanding is crucial for selecting the appropriate welding process, filler metal, and heat treatment for a particular application. Additionally, metallurgy can help predict potential problems such as cracking or warping, and can aid in the development of new welding techniques and equipment.
What are the properties of metallurgy?
- Density: the mass per unit volume of a metal
- Melting Point: the temperature at which a metal changes from solid to liquid
- Hardness: the resistance of a metal to deformation or penetration
- Toughness: the ability of a metal to absorb energy and deform plastically without breaking
- Conductivity: the ability of a metal to conduct electricity and heat
- Corrosion resistance: the ability of a metal to resist chemical or electrochemical reactions that can cause degradation
- Machinability: the ease of cutting, shaping, or machining a metal
- Weldability: the ease of joining two pieces of metal by welding
- Formability: the ease of shaping metal through processes such as bending, forging or stamping
- Stability: the ability of a metal to maintain its properties under different conditions, such as temperature changes.
These properties can be influenced by factors such as composition, microstructure, and heat treatment, and can vary depending on the specific metal or alloy.
What are the three types of metallurgy?
There are several different ways to classify metallurgy, but one common method is to divide it into three main categories: extractive metallurgy, physical metallurgy, and computational metallurgy.
- Extractive metallurgy is the process of extracting metals from ores and refining them to produce a pure metal. This includes processes such as mining, crushing, grinding, concentration, and smelting.
- Physical metallurgy is the study of the physical and mechanical properties of metals and alloys, and how they respond to various heat treatment and deformation processes. This includes processes such as casting, forging, rolling, and heat treatment.
- Computational metallurgy is a relatively new field that uses computational methods such as numerical simulations and data analysis to understand the behavior of metals and alloys at the atomic and microstructural levels. This helps to predict properties such as strength, ductility, and corrosion resistance, and to design new materials with specific properties.
What are the metallurgical effects of welding?
Welding can have a number of metallurgical effects on the materials being joined, including:
- The heat-affected zone (HAZ): The area surrounding the weld that has been heated to high temperatures, but not melted. The microstructure of the metal in this zone can change, leading to a loss of strength and toughness.
- Weld metal: The material that has been melted and solidified to form the weld. The microstructure of the weld metal can be different from that of the base metal and may have different properties as well.
- Distortion: The warping or bending of the material caused by the heat of the welding process. This can be caused by uneven cooling and can make the finished product difficult to use.
- Residual stress: Stress that remains in the material after it has cooled, caused by the contraction and expansion of the metal during the welding process.
- Porosity: Small voids or bubbles in the weld metal caused by the entrapment of gases during the welding process.
- Cracking: The formation of cracks in the metal due to a variety of factors, such as improper welding techniques or high residual stress.
Is welding part of metallurgy?
Yes, welding is considered to be a part of metallurgy. Metallurgy is the science and technology of metals, including the processes of extracting, refining, and working with metals. Welding is a process that is used to join two pieces of metal together, and it is an important aspect of the manufacturing and construction industries. Welding is also widely used in repairing, refurbishing, and maintaining structures and equipment. Welding is a process that requires a deep understanding of the properties and behavior of metals, and it is heavily dependent on metallurgical principles. Thus, welding is a subfield of metallurgy, and metallurgists who specialized in welding is called welding metallurgists. They are responsible for understanding how welding processes affect the microstructure and properties of metals, and how to minimize or prevent any negative effects.
Conclusion
In conclusion, welding metallurgy is an important field that helps to understand how the properties of metals are affected by the welding process. The physical properties of metals such as melting point, thermal conductivity, thermal expansion, density, hardness, and electrical conductivity play a critical role in determining the success of the weld. The selection of the proper welding process, filler metal and proper technique, is crucial to achieve a good quality weld and obtain the desired properties of the final joint. Different types of metals are used in welding, including ferrous metals such as carbon steel and cast iron, and nonferrous metals such as aluminum, copper, and nickel. Each type of metal has its own unique properties that affect its weldability, with some metals being more challenging to weld than others. In this article, we have discussed the welding metallurgy, the common metals used in welding, common welding techniques for different types of metals, and how their properties affect their ease of welding. Understanding welding metallurgy and the properties of different metals is essential for those involved in the design, fabrication, and repair of metal structures and products.