Welding of Magnesium and its Alloys
Introduction
Magnesium, a lightweight and versatile metal, has found its place in numerous industries due to its exceptional properties. Its alloys, created by combining magnesium with other elements, further enhance its usability and performance in various applications. However, the welding of magnesium and its alloys poses unique challenges and requires specialized knowledge and techniques. In this blog post, we will delve into the intricacies of welding magnesium and its alloys, exploring the importance of this process in fabrication and addressing the specific purpose of our discussion.
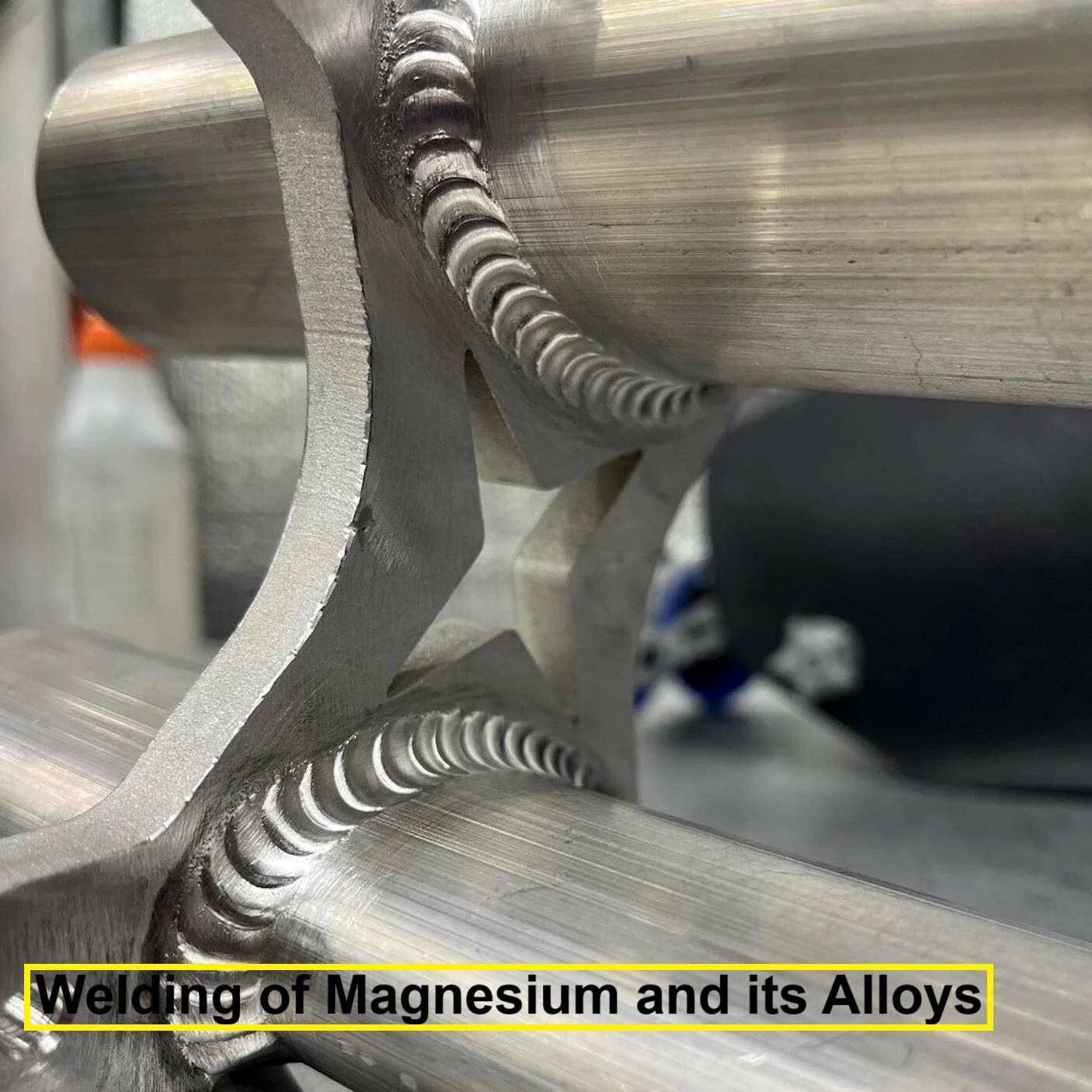
Understanding Magnesium and its Alloys
Properties of Magnesium
Magnesium boasts a range of remarkable properties that make it a desirable material across diverse industries. As one of the lightest structural metals, magnesium exhibits a low density, offering significant weight savings in applications where weight reduction is critical. Despite its lightweight nature, magnesium also showcases impressive strength, particularly when alloyed with other elements. Additionally, magnesium possesses excellent machinability, allowing for ease of fabrication into various shapes and forms. Its exceptional electrical and thermal conductivity further enhance its utility in electrical and heat transfer applications.
Common Magnesium Alloys and Their Compositions
Magnesium alloys are created by blending magnesium with other metals and elements to enhance specific properties or address particular application requirements. Some of the most common magnesium alloys include:
- AZ31: This alloy consists of magnesium combined with aluminum and zinc. It offers good mechanical properties, corrosion resistance, and weldability, making it suitable for applications in automotive components, electronics, and consumer goods.
- AZ91: Comprising magnesium, aluminum, and a higher proportion of zinc compared to AZ31, AZ91 exhibits improved strength and creep resistance. It finds use in automotive parts, aerospace components, and electronic enclosures.
- AM50/60: These alloys contain magnesium, aluminum, and manganese, offering improved strength and ductility compared to AZ series alloys. They are commonly used in automotive and aerospace applications where higher mechanical performance is required.
- WE43: WE43 is a magnesium alloy alloyed with yttrium and rare earth elements. It provides excellent high-temperature strength and creep resistance, making it suitable for applications in aerospace, defense, and high-performance racing components.
Applications of Welding Magnesium and its Alloys
Aerospace Industry
Magnesium and its alloys are prized for their lightweight properties, making them ideal for aircraft components like fuselage panels and engine parts, as well as missile components.
Automotive Industry
In automotive manufacturing, magnesium alloys are used for engine blocks, transmission cases, and lightweight body panels, contributing to improved fuel efficiency and performance.
Electronics Industry
Magnesium alloys find applications in electronics for laptop casings, smartphone frames, and other device enclosures, offering electromagnetic shielding and effective heat dissipation.
Defense Industry
In defense applications, magnesium alloys are utilized for military vehicles, armored vehicles, and weaponry components, benefiting from their strength-to-weight ratio and durability.
Medical Industry
Magnesium alloys are valued in the medical sector for their biocompatibility, used in orthopedic implants, surgical tools, and other medical devices, with welding ensuring precision and reliability.
Challenges in Welding Magnesium
High Reactivity with Oxygen
One of the primary challenges encountered when welding magnesium is its high reactivity with oxygen. Magnesium readily reacts with oxygen from the atmosphere, forming a layer of magnesium oxide on its surface. This oxide layer can impede the welding process by inhibiting proper fusion between the base metal and the filler material. Additionally, the presence of oxides can weaken the weld joint and compromise its mechanical properties.
Formation of Oxide Layer
During welding, the formation of an oxide layer on the surface of magnesium poses significant obstacles. This oxide layer forms quickly when exposed to air and must be removed prior to welding to ensure a clean and successful weld. If not adequately addressed, the oxide layer can lead to weld defects such as porosity, lack of fusion, and reduced weld strength.
Special Precautions Required
Welding magnesium requires adherence to strict safety protocols and special precautions due to its reactive nature. Proper ventilation is essential to prevent the buildup of flammable magnesium fumes, which can pose fire hazards if ignited. Additionally, protective measures such as the use of welding screens, gloves, and appropriate personal protective equipment (PPE) are necessary to safeguard against potential exposure to magnesium fumes and ultraviolet radiation emitted during the welding process.
Techniques for Welding Magnesium
Tungsten Inert Gas (TIG) Welding
Tungsten Inert Gas (TIG) welding, also known as Gas Tungsten Arc Welding (GTAW), is one of the most commonly used techniques for welding magnesium. In TIG welding, a non-consumable tungsten electrode is used to create the arc, while an inert gas, such as argon or helium, is used to shield the weld area from atmospheric contamination. TIG welding offers precise control over the welding process, making it suitable for welding thin magnesium sheets and intricate components. However, TIG welding of magnesium requires careful attention to shielding gas coverage and proper cleaning of the workpiece to prevent oxidation.
Metal Inert Gas (MIG) Welding
Metal Inert Gas (MIG) welding, also known as Gas Metal Arc Welding (GMAW), is another technique used for welding magnesium. In MIG welding, a consumable electrode wire is fed continuously into the weld pool, while an inert gas shield protects the weld area from atmospheric contamination. MIG welding offers higher deposition rates compared to TIG welding, making it suitable for welding thicker magnesium sections and high-volume production applications. However, MIG welding of magnesium requires precise control of welding parameters to prevent overheating and avoid weld defects.
Resistance Welding
Resistance welding is a technique that utilizes the heat generated by electrical resistance to join two or more pieces of metal. In resistance welding of magnesium, high electrical current is passed through the workpieces, creating localized heat at the joint interface. Once the desired temperature is reached, pressure is applied to forge the weld. Resistance welding is commonly used for joining magnesium sheets and components in automotive and aerospace applications. However, special precautions must be taken to control the welding parameters and prevent overheating, which can lead to weld cracking and degradation of mechanical properties.
Comparison of Different Welding Techniques
Each welding technique has its advantages and limitations when it comes to welding magnesium. TIG welding offers precise control and is suitable for thin sections and intricate welds, but it may be slower compared to MIG welding. MIG welding, on the other hand, offers higher deposition rates and is more suitable for thicker sections and high-volume production. Resistance welding is preferred for its ability to join magnesium sheets quickly and efficiently, but it requires specialized equipment and careful control of welding parameters.
Safety Measures and Precautions
Importance of Proper Ventilation
Proper ventilation is paramount when welding magnesium due to the potential hazards associated with magnesium fumes. During welding, magnesium emits fine particles and fumes that, when inhaled, can pose serious health risks to welders. These fumes may contain magnesium oxide, which can irritate the respiratory system and cause respiratory problems. Therefore, it is essential to ensure adequate ventilation in the welding area to remove fumes and maintain a safe working environment. Ventilation systems such as exhaust hoods or local exhaust ventilation should be used to capture and remove fumes directly from the welding process, minimizing exposure to harmful contaminants.
Protective Equipment Required for Magnesium Welding
Welding magnesium requires the use of appropriate personal protective equipment (PPE) to safeguard against potential hazards and ensure the safety of welders. Some essential protective equipment for magnesium welding includes:
- Welding Helmet: A welding helmet with a proper shade lens is essential to protect the eyes and face from intense ultraviolet (UV) and infrared (IR) radiation emitted during the welding process.
- Welding Gloves: Heat-resistant welding gloves should be worn to protect the hands from burns and injuries caused by contact with hot metal and welding sparks.
- Protective Clothing: Welders should wear flame-resistant clothing made of natural fibers such as cotton or wool to protect against burns and minimize the risk of clothing catching fire.
- Respiratory Protection: Respiratory protection, such as a respirator with appropriate filters, should be worn to prevent inhalation of magnesium fumes and airborne contaminants generated during welding.
- Safety Glasses: Safety glasses with side shields are recommended to protect the eyes from welding sparks, flying debris, and ultraviolet radiation.
Fire Hazards and Prevention Methods
Welding magnesium poses inherent fire hazards due to its high flammability and reactivity with oxygen. Magnesium can ignite spontaneously when exposed to certain conditions, such as high temperatures or contact with water. To mitigate the risk of fire hazards during magnesium welding, several prevention methods should be employed:
- Clean Work Area: Ensure the work area is free from flammable materials, debris, and clutter that could ignite during welding operations.
- Fire Extinguishers: Keep fire extinguishers readily available in the welding area and ensure all personnel are trained in their proper use. Class D fire extinguishers specifically designed for metal fires should be used for magnesium fires.
- Spark Arrestors: Install spark arrestors or flame-retardant curtains around the welding area to contain sparks and prevent them from igniting nearby combustible materials.
- Hot Work Permits: Implement a hot work permit system to control and authorize welding operations in designated areas, ensuring proper safety measures are in place.
- Emergency Procedures: Establish emergency procedures and evacuation plans in case of fire or other welding-related incidents, and ensure all personnel are familiar with these procedures.
Tips for Successful Magnesium Welding
Maintaining Proper Shielding Gas Coverage
Maintaining proper shielding gas coverage is crucial for successful magnesium welding. Shielding gas, typically argon or helium, is used to protect the weld pool from atmospheric contamination, such as oxygen and nitrogen, which can lead to the formation of oxides and other weld defects. To ensure effective shielding gas coverage:
- Use the appropriate flow rate of shielding gas recommended for magnesium welding.
- Position the gas nozzle or torch at the correct angle and distance from the weld joint to provide adequate coverage.
- Monitor gas flow and adjust as necessary to maintain a stable arc and prevent atmospheric contamination.
- Consider using a trailing shield or gas lens to enhance gas coverage and protect the weld zone from oxidation.
Controlling Heat Input
Controlling heat input is essential for achieving high-quality magnesium welds and minimizing the risk of overheating and weld defects. Excessive heat can lead to the formation of porosity, cracks, and other metallurgical issues, while insufficient heat may result in incomplete fusion and poor weld penetration. To control heat input effectively:
- Adjust welding parameters such as current, voltage, and travel speed to achieve the desired heat input for the specific application.
- Monitor the temperature of the workpiece and control preheating and interpass temperatures to prevent overheating or rapid cooling rates.
- Use pulse or waveform control settings on the welding machine to regulate heat input and minimize distortion and heat-affected zone (HAZ) problems.
- Employ proper joint design and fit-up to facilitate efficient heat transfer and minimize heat concentration in critical areas.
Avoiding Contamination of Weld Zone
Contamination of the weld zone can adversely affect weld quality and mechanical properties, particularly in magnesium welding, where the metal is highly reactive with oxygen and other atmospheric gases. To avoid contamination of the weld zone:
- Ensure thorough cleaning and surface preparation of the base metal to remove any contaminants, oils, or oxides that could compromise weld quality.
- Use clean, dry filler material and ensure proper storage and handling to prevent contamination by moisture, dirt, or other foreign particles.
- Minimize exposure of the weld zone to atmospheric gases by maintaining a tight arc length, proper shielding gas coverage, and appropriate welding techniques.
- Implement good housekeeping practices in the welding area to prevent the accumulation of debris, dust, and other potential sources of contamination.
FAQs
What are the main challenges in welding magnesium alloys?
Welding magnesium alloys presents challenges such as high reactivity, susceptibility to corrosion, and flammability risks.
Why is surface preparation crucial before welding magnesium?
Surface preparation is essential to remove surface contaminants and oxides, ensuring proper fusion and minimizing defects in the weld.
What safety precautions should welders take when working with magnesium?
Welders should ensure adequate ventilation, handle shielding gases properly, and wear appropriate personal protective equipment to mitigate the risk of fire and exposure to hazardous fumes.
How do post-welding processes contribute to the integrity of magnesium welds?
Post-welding processes such as inspection, heat treatment, and surface finishing help identify and mitigate defects, relieve residual stresses, and enhance the mechanical properties and corrosion resistance of magnesium welds.
What are some innovative applications of welded magnesium alloys?
Magnesium alloys are increasingly being used in automotive, aerospace, and consumer electronics applications for their lightweight properties, contributing to fuel efficiency, performance, and durability.
Conclusion
Welding of magnesium and its alloys presents unique challenges and opportunities for various industries. By understanding the properties of magnesium, implementing proper welding techniques, and adhering to stringent safety measures, manufacturers can harness the benefits of lightweight magnesium alloys while ensuring optimal weld quality and integrity.