A Comprehensive Overview, Process, and Benefits
Introduction
Flame hardening, also known as flame surface hardening or flame heating, is a heat treatment method used to increase the hardness and wear resistance of metal surfaces. It involves the localized heating of a metal component using a high-temperature flame, followed by rapid cooling. The goal is to achieve a hardened surface layer while maintaining the desired properties in the core of the material.
In this process, a focused flame, typically fueled by acetylene or propane, is directed onto the surface of the metal workpiece. The intense heat generated by the flame causes the surface layer of the metal to reach critical temperatures, where it undergoes transformation, primarily through austenitization. This phase change alters the microstructure of the surface, resulting in increased hardness upon quenching.
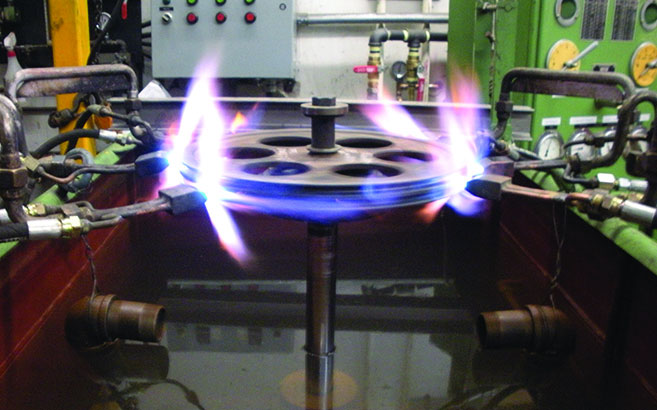
Understanding the Process
Flame hardening is a sophisticated heat treatment technique used to improve the surface properties of metal components, enhancing their hardness and wear resistance. This section delves into the intricacies of the flame hardening process, exploring its fundamental principles, equipment requirements, heat generation mechanisms, and comparative advantages over other hardening methods.
Overview of Flame Hardening Technique
Flame hardening is a localized heat treatment process that involves heating specific areas of a metal workpiece to high temperatures, followed by rapid quenching to achieve desired material properties. Unlike traditional heat treatment methods that subject the entire component to uniform heating, flame hardening targets only the surface layer, minimizing distortion and energy consumption.
The process begins with the preparation of the workpiece, including cleaning and surface profiling to ensure uniform heat distribution. A focused flame, typically generated from a fuel gas such as acetylene or propane, is then directed onto the desired areas of the metal surface. The intense heat from the flame causes the surface layer to reach critical temperatures, inducing phase transformations that increase hardness.
After the surface has been adequately heated, the workpiece is quickly cooled using methods such as water spray or quenching oils. This rapid cooling solidifies the transformed microstructure, resulting in a hardened surface layer with improved mechanical properties. The core of the material remains relatively unaffected, preserving its original properties.
Key Components and Equipment Involved
Several essential components and equipment are required to perform flame hardening effectively. These include:
- Flame Torch: The primary tool used to generate the high-temperature flame. It typically consists of a handle, fuel gas supply system, and mixing chamber where the gas and oxygen are combined and ignited.
- Fuel Gas: Commonly used gases include acetylene, propane, or natural gas, which serve as the primary fuel source for the flame.
- Oxygen Supply: Essential for combustion, oxygen is supplied to the flame torch at controlled pressures to maintain optimal combustion conditions.
- Manipulation System: Mechanisms for controlling the movement and orientation of the flame torch relative to the workpiece, ensuring precise heating.
- Cooling Medium: Water spray or quenching oils are used to rapidly cool the heated surface after the desired temperature is achieved, preventing excessive heat transfer to the core.
Heat Generation Mechanism
The heat generation mechanism in flame hardening relies on the combustion of fuel gas and oxygen to produce a high-temperature flame. When the fuel gas and oxygen mix in the combustion chamber of the torch and ignite, they release significant amounts of heat energy. This intense heat is then directed onto the surface of the metal workpiece, raising its temperature to the desired level for hardening.
Comparison with Other Hardening Methods
Flame hardening offers several distinct advantages compared to other hardening methods such as induction hardening or case hardening:
- Localized Heating: Flame hardening allows for precise targeting of specific areas, minimizing heat distortion and energy consumption compared to uniform heating methods.
- Versatility: It can be applied to a wide range of metals, shapes, and sizes, offering flexibility in manufacturing processes.
- Cost-Effectiveness: The equipment and operational costs associated with flame hardening are often lower compared to other hardening techniques, making it a cost-effective solution for many applications.
- Surface Quality: Flame hardening produces smooth, clean surfaces with minimal oxide formation, resulting in improved surface finish and aesthetics.
Steps Involved in Flame Hardening
Flame hardening is a multi-step process that requires careful preparation, precise application of heat, controlled quenching, and subsequent post-processing to achieve desired results. This section outlines the key steps involved in flame hardening, from surface preparation to final treatment.
Preparing the Surface
Before flame hardening can commence, thorough surface preparation is essential to ensure optimal heat distribution and treatment effectiveness. This step typically involves:
- Cleaning: The workpiece surface must be free from contaminants such as dirt, grease, and rust. Cleaning methods may include solvent degreasing, abrasive blasting, or chemical treatments.
- Profiling: Achieving uniform heat distribution requires profiling or masking certain areas of the workpiece that do not require hardening. This prevents unintended heat transfer and distortion.
- Preheating (Optional): In some cases, preheating the workpiece to a moderate temperature may be necessary to reduce thermal shock during the hardening process. This step helps minimize distortion and cracking.
Application of Heat
Once the surface is adequately prepared, the next step involves the controlled application of heat using a flame torch. This phase includes:
- Positioning: The flame torch is positioned at the desired location on the workpiece, ensuring proper alignment and coverage of the target area.
- Heat Application: The flame is ignited, and the torch is manipulated to direct the heat onto the surface of the workpiece. The intensity and duration of heating depend on factors such as material composition, thickness, and hardening requirements.
- Monitoring: Throughout the heating process, temperature monitoring techniques such as infrared thermography or pyrometers may be employed to ensure precise temperature control and uniform heating.
Quenching Process
After the surface has been sufficiently heated to the desired temperature, rapid quenching is employed to cool the metal and solidify the transformed microstructure. This step involves:
- Quenching Medium Selection: Depending on the material and hardening requirements, the workpiece is immersed in a quenching medium such as water, oil, or polymer solution.
- Cooling Rate Control: The rate of cooling is carefully controlled to achieve the desired hardness and minimize the risk of cracking or distortion. Proper agitation or circulation of the quenching medium helps ensure uniform cooling.
- Tempering (Optional): In some cases, the hardened surface may undergo tempering, a heat treatment process that reduces internal stresses and improves toughness. Tempering may follow immediately after quenching or as a separate step.
Post-Processing Steps
Once the quenching process is complete, several post-processing steps may be carried out to optimize the final product:
- Cleaning and Inspection: The workpiece is thoroughly cleaned to remove any residual quenching medium or surface contaminants. Inspection methods such as visual examination, hardness testing, and metallurgical analysis are conducted to assess the quality of the hardened surface.
- Surface Finishing: Depending on the application and aesthetic requirements, additional surface finishing techniques such as grinding, polishing, or shot blasting may be employed to achieve the desired surface texture and appearance.
- Protective Coating (Optional): To further enhance corrosion resistance and surface durability, a protective coating such as plating, painting, or chemical passivation may be applied to the hardened surface.
Benefits of Flame Hardening
Flame hardening offers a plethora of advantages that make it a preferred choice for enhancing the performance and durability of metal components. This section highlights the key benefits associated with flame hardening, ranging from enhanced surface hardness to cost-effectiveness and efficiency.
Enhanced Surface Hardness
One of the primary benefits of flame hardening is its ability to significantly increase the surface hardness of metal components. By subjecting specific areas to localized heating followed by rapid quenching, flame hardening transforms the microstructure of the surface layer, resulting in a hardened surface that is resistant to wear, abrasion, and indentation. This enhanced hardness improves the longevity and performance of critical components, reducing the need for frequent maintenance and replacement.
Increased Wear Resistance
In addition to surface hardness, flame hardening also imparts increased wear resistance to metal components. The hardened surface layer exhibits superior resistance to mechanical wear and frictional forces, making it ideal for applications subjected to high levels of abrasion and surface contact. Components treated with flame hardening are better equipped to withstand harsh operating conditions, prolonging their service life and reducing downtime associated with premature wear and failure.
Retention of Core Properties
Unlike some conventional hardening methods that can compromise the core properties of the material, flame hardening offers the distinct advantage of preserving the integrity and properties of the core material. By selectively heating only the surface layer to critical temperatures, flame hardening minimizes the risk of structural changes or distortion in the core, ensuring that the component retains its desired mechanical properties, such as strength, toughness, and ductility. This balanced combination of surface hardness and core properties makes flame-hardened components highly versatile and reliable in a variety of applications.
Cost-Effectiveness and Efficiency
Flame hardening is renowned for its cost-effectiveness and efficiency compared to other hardening methods. The equipment and operational costs associated with flame hardening are often lower, making it an attractive option for manufacturers seeking to optimize their production processes without compromising on quality. Moreover, the localized nature of flame hardening reduces energy consumption and material waste, resulting in improved resource utilization and overall efficiency. These cost-saving benefits, coupled with the ability to achieve precise and consistent results, make flame hardening a preferred choice for a wide range of industrial applications.
Applications and Industries
Flame hardening finds diverse applications across various industries, where its ability to enhance surface hardness and wear resistance is instrumental in improving the performance and longevity of critical components. This section explores the key applications of flame hardening in prominent industries, including automotive, aerospace, machinery, tool manufacturing, and other potential fields.
Automotive Sector
In the automotive industry, flame hardening plays a crucial role in improving the durability and reliability of components subjected to high levels of wear and friction. Common applications include:
- Crankshafts and Camshafts: Flame hardening is utilized to harden the bearing surfaces of crankshafts and camshafts, enhancing their resistance to abrasion and extending their service life.
- Gears and Transmission Components: Flame hardening is applied to gear teeth and transmission components to improve their wear resistance and ensure smooth operation under heavy loads.
- Axles and Drive Shafts: Flame hardening is employed to harden the surface of axles and drive shafts, reducing wear and increasing fatigue resistance in automotive drivetrain systems.
Aerospace Industry
In the aerospace industry, where safety and reliability are paramount, flame hardening is utilized to enhance the performance and longevity of critical components subjected to extreme operating conditions. Key applications include:
- Landing Gear Components: Flame hardening is applied to landing gear components such as axles, spindles, and wheels to increase their wear resistance and withstand the forces encountered during takeoff and landing.
- Turbine Blades and Engine Components: Flame hardening is employed to harden the surfaces of turbine blades, engine shafts, and compressor components, ensuring optimal performance and durability in aircraft propulsion systems.
- Structural Components: Flame hardening is used to improve the wear resistance of structural components such as brackets, fittings, and fasteners, enhancing the overall reliability and safety of aircraft structures.
Machinery and Tool Manufacturing
In machinery and tool manufacturing, flame hardening is widely utilized to improve the performance and longevity of critical components subjected to heavy-duty operations. Common applications include:
- Machine Tool Components: Flame hardening is applied to machine tool components such as slides, ways, and gears to increase their wear resistance and precision, ensuring smooth and accurate machining operations.
- Hydraulic Cylinder Rods: Flame hardening is employed to harden the surfaces of hydraulic cylinder rods, reducing wear and extending the service life of hydraulic systems used in industrial machinery.
- Cutting Tools: Flame hardening is utilized to harden the cutting edges of tools such as drills, milling cutters, and lathe tools, increasing their resistance to wear and prolonging tool life in metal cutting applications.
Other Potential Fields
In addition to the aforementioned industries, flame hardening holds potential applications in various other fields, including:
- Mining and Construction: Flame hardening can be used to enhance the wear resistance of components used in mining equipment, construction machinery, and earthmoving vehicles, increasing their durability and productivity in harsh environments.
- Railroad and Transportation: Flame hardening is employed to harden the surfaces of rail tracks, wheels, and other railway components, reducing wear and ensuring reliable performance in rail transportation systems.
- Oil and Gas: Flame hardening can be utilized to increase the wear resistance of components used in oil and gas drilling equipment, pipelines, and valves, improving reliability and safety in upstream and downstream operations.
FAQs
Is flame hardening suitable for all types of metal alloys?
Flame hardening can be applied to a wide range of metal alloys, but the suitability depends on factors such as composition and metallurgical properties.
How does flame hardening compare to other hardening methods in terms of cost?
Flame hardening is generally more cost-effective than methods like induction hardening due to lower equipment costs and simpler process requirements.
What safety precautions should be taken during flame hardening operations?
Operators should wear appropriate protective gear, ensure proper ventilation, and follow fire safety protocols to minimize the risk of accidents.
Can flame hardening induce distortion in metal components?
Yes, rapid heating and cooling cycles involved in flame hardening can induce residual stresses and dimensional changes, leading to distortion or warping of the workpiece.
What are the typical applications of flame hardening in the automotive industry?
Flame hardening is commonly used in the automotive industry for hardening critical engine components such as crankshafts, camshafts, and gears to improve their wear resistance and durability.
Conclusion
In conclusion, flame hardening remains a valuable tool for achieving superior surface properties and performance in metal components. By capitalizing on its inherent advantages and embracing future advancements, manufacturers can continue to leverage flame hardening to meet the evolving demands of modern industry while promoting sustainability and innovation.