Mastering Oxyacetylene Welding: Essential Equipment Guide
Introduction
Oxyacetylene welding, often referred to as oxy-fuel welding or gas welding, is a versatile and widely used method for joining metals. This welding process involves the combustion of oxygen and acetylene gases to generate a high-temperature flame, which melts the base metal and filler material, creating a strong bond upon cooling. While oxyacetylene welding has been around for over a century, it remains a fundamental technique in various industries, including automotive repair, construction, and metal fabrication.
Oxyacetylene Welding Equipment
Oxyacetylene welding relies on a set of specialized equipment to create the necessary conditions for the welding process. Understanding the various components of this equipment is crucial for both safety and efficiency in welding operations.
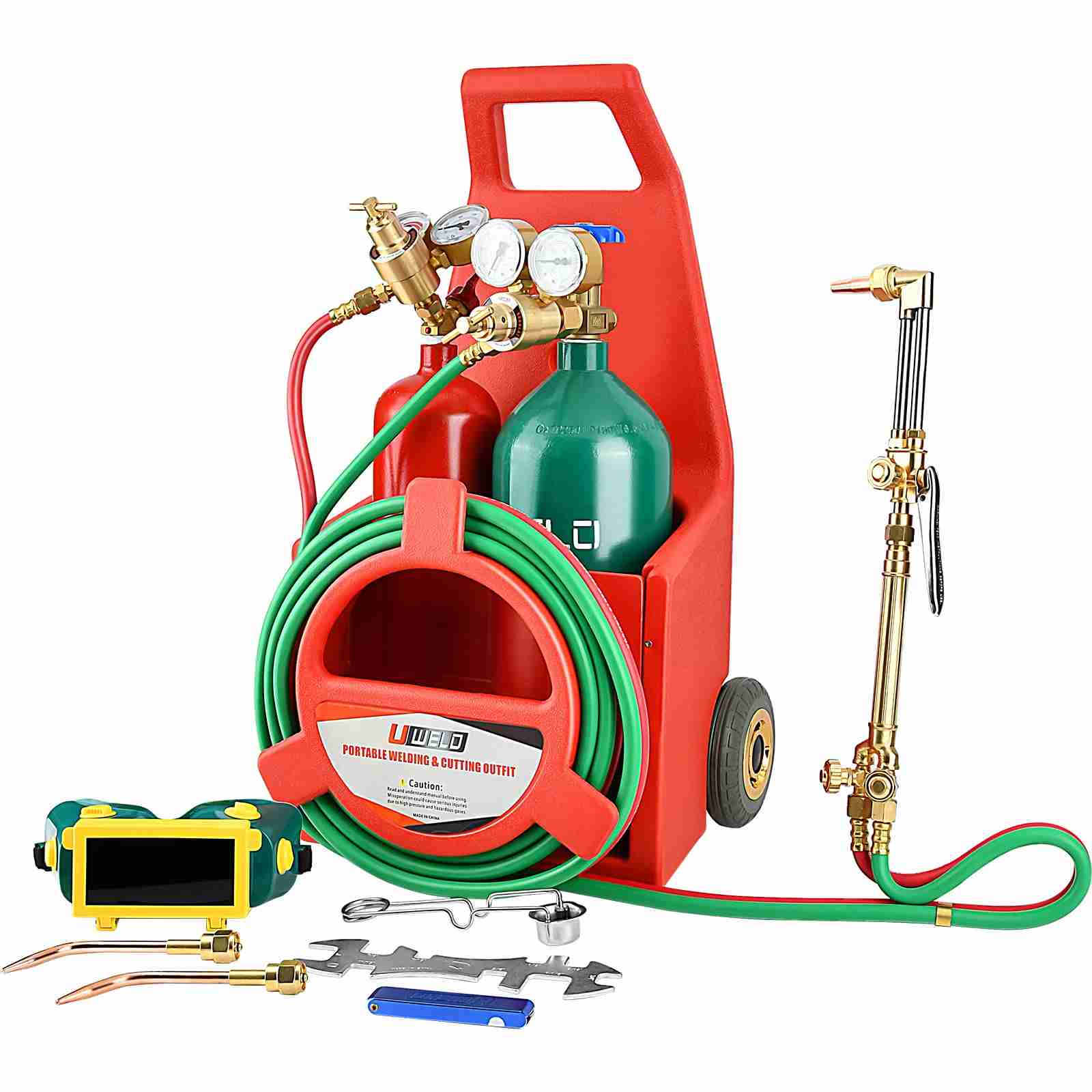
1. Oxyacetylene Torch
The oxyacetylene torch is the heart of the oxyacetylene welding setup, responsible for producing the intense flame required to melt the base metals. There are several types of oxyacetylene torches, each designed for specific welding tasks:
Types of Torches:
- Welding Torch: Used primarily for joining metals by melting the edges and adding filler material.
- Cutting Torch: Equipped with a cutting attachment to facilitate the cutting of metal plates and structures.
- Heating Torch: Designed for applications requiring localized heating, such as bending or shaping metal components.
Components and Functionality:
- The torch consists of a handle, mixing chamber, and various tips or nozzles.
- Oxygen and acetylene are supplied separately to the torch, where they mix and combust to produce a high-temperature flame.
- Different tips or nozzles can be attached to the torch to adjust the flame size and shape according to the welding task.
2. Gas Cylinders
Oxygen and acetylene are stored in separate cylinders and are essential components of the oxyacetylene welding process.
Oxygen Cylinder:
- Contains compressed oxygen gas used as an oxidizing agent in the combustion process.
- Oxygen cylinders are typically color-coded green for easy identification.
- Proper handling and storage of oxygen cylinders are essential to prevent leaks and accidents.
Acetylene Cylinder:
- Stores acetylene gas, which serves as the fuel source for the oxyacetylene flame.
- Acetylene cylinders are distinguishable by their maroon or red color coding.
- Due to its chemical instability, acetylene must be stored and transported under specific pressure conditions to prevent decomposition or explosion hazards.
Proper Handling and Storage:
- Both oxygen and acetylene cylinders should be stored upright in a well-ventilated area, away from flammable materials and heat sources.
- Cylinders must be securely fastened to prevent tipping or falling, which could lead to damage or leakage.
- Regular inspections and maintenance are necessary to ensure the integrity of cylinder valves and fittings.
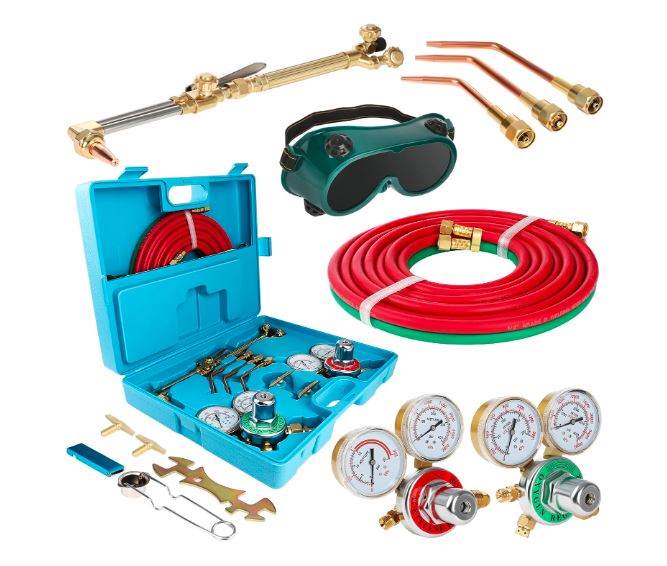
3. Regulators
Regulators are essential components that control the flow and pressure of gases from the cylinders to the torch.
Purpose and Function:
- Regulators reduce the high pressure stored in the gas cylinders to a safe and manageable level for welding operations.
- They maintain a consistent flow rate of oxygen and acetylene to the torch, allowing for precise control of the welding flame.
Types of Regulators:
- Single-Stage Regulators: Suitable for low to medium pressure applications, where a single reduction in pressure is sufficient.
- Dual-Stage Regulators: Provide more precise control by reducing pressure in two stages, ensuring a stable output pressure regardless of fluctuations in cylinder pressure.
4. Hoses and Fittings
Hoses and fittings connect the gas cylinders to the torch and play a critical role in ensuring a safe and leak-free welding environment.
Materials and Specifications:
- Hoses are typically made of reinforced rubber or thermoplastic materials capable of withstanding high pressures and temperatures.
- Fittings are available in various sizes and configurations to accommodate different torches and regulators.
Importance of Leak-Free Connections:
- Proper installation and maintenance of hoses and fittings are essential to prevent gas leaks, which can pose serious safety hazards.
- Regular inspections, including checking for cracks, abrasions, or loose connections, are necessary to detect and rectify potential leaks promptly.
5. Welding Goggles and Protective Gear
Welding goggles and protective gear are indispensable for safeguarding the welder against hazards such as intense light, sparks, and debris.
Eye Protection:
- Welding goggles or helmets with shaded lenses protect the eyes from harmful ultraviolet (UV) and infrared (IR) radiation emitted during welding.
- Properly shaded lenses must be selected based on the welding process and intensity of the light produced.
Clothing and Gloves for Safety:
- Welders should wear flame-resistant clothing, such as cotton or leather, to minimize the risk of burns from hot metal or sparks.
- Heat-resistant gloves provide additional protection for the hands and arms against burns and abrasions caused by handling hot materials or welding equipment.
Setting Up Your Workspace
Setting up a conducive workspace is crucial for ensuring safety, efficiency, and quality results in oxyacetylene welding operations. Proper ventilation, organization of equipment, and a stable work surface are essential considerations for welders.
Proper Ventilation and Safety Precautions
- Adequate ventilation is essential to remove potentially harmful fumes, gases, and smoke generated during the welding process.
- Ensure that the workspace is well-ventilated by opening windows or using exhaust fans to facilitate airflow.
- For indoor welding, consider installing ventilation systems or using portable fume extractors to maintain air quality.
- Wear appropriate personal protective equipment (PPE), including welding helmets, gloves, and flame-resistant clothing, to protect against heat, sparks, and UV radiation.
- Keep flammable materials and combustible objects away from the welding area to prevent fire hazards.
- Have a fire extinguisher readily available and know how to use it in case of emergencies.
- Mark emergency exits and ensure clear pathways for evacuation in the event of an accident.
Arranging Equipment for Optimal Workflow
Organize Equipment Layout:
- Arrange gas cylinders, regulators, hoses, and torches in a logical and accessible manner to minimize tripping hazards and facilitate easy reach during welding.
- Consider mounting cylinders securely on carts or stands to prevent tipping and ensure stability during operation.
Tool Storage:
- Provide designated storage areas for welding accessories, such as tips, goggles, and gloves, to keep them organized and easily accessible.
- Use toolboxes or shelving units to store small components and spare parts, preventing clutter on the workspace.
Workstation Ergonomics:
- Position welding equipment at comfortable working heights to reduce strain and fatigue during prolonged welding sessions.
- Arrange tools and accessories within arm’s reach to minimize unnecessary movement and improve workflow efficiency.
Ensuring a Stable Work Surface
Flat and Level Surface:
- Choose a flat and stable surface for welding to ensure proper alignment and stability of workpieces during welding.
- Use welding tables or workbenches with sturdy legs and reinforced frames to support heavy materials and welding equipment.
Secure Workpieces:
- Use clamps or magnetic holders to secure workpieces in place, preventing movement or shifting during welding.
- Ensure that workpieces are properly aligned and positioned to achieve accurate welds and minimize distortion.
Protection Against Heat Damage:
- Place heat-resistant materials, such as welding blankets or ceramic tiles, underneath the workpiece to protect the work surface from heat damage and spatter.
- Use heat shields or barriers to prevent nearby objects or surfaces from being affected by radiant heat generated during welding.
Tips for Efficient Welding
Achieving efficient and high-quality oxyacetylene welds requires attention to detail and mastery of welding techniques. Here are some essential tips to enhance welding efficiency and ensure consistent results:
Adjusting Gas Flow and Flame Settings
Balancing Gas Flow:
- Ensure proper gas flow rates for oxygen and acetylene by adjusting the regulators to the recommended settings.
- Experiment with different gas flow combinations to achieve the ideal flame characteristics for the welding task at hand.
Flame Adjustment:
- Fine-tune the flame by adjusting the oxygen and acetylene valves on the torch to attain the desired flame size, shape, and intensity.
- Aim for a neutral flame with a well-defined inner cone surrounded by a blue outer cone for optimal heat distribution and control.
Maintaining Proper Distance and Angle
Distance from Workpiece:
- Maintain a consistent distance between the torch tip and the workpiece to ensure proper heat distribution and penetration.
- Practice controlling the torch-to-workpiece distance to achieve uniform weld bead profiles and prevent overheating or underheating.
Angle of the Torch:
- Hold the torch at the correct angle relative to the workpiece to direct the flame and molten metal effectively.
- Experiment with different torch angles to find the optimal position for achieving desired weld characteristics, such as penetration depth and bead shape.
Preparing Materials for Welding
Cleanliness is Key:
- Thoroughly clean the surfaces to be welded to remove any dirt, oil, rust, or contaminants that can adversely affect weld quality.
- Use wire brushes, solvents, or grinding tools to prep the welding area and ensure proper fusion between metal surfaces.
Fit-Up and Alignment:
- Ensure proper fit-up and alignment of workpieces before welding to minimize gaps and inconsistencies in the weld joint.
- Use clamps or fixtures to hold parts in position and maintain alignment during welding operations.
Troubleshooting Common Issues
Overheating:
- Monitor the temperature of the workpiece to prevent overheating, which can lead to distortion, warping, or metallurgical changes.
- Adjust the welding parameters, such as travel speed and heat input, to maintain control over the welding process and avoid excessive heat buildup.
Backfires and Flashbacks:
- Pay attention to signs of backfires (sudden bursts of flame) or flashbacks (flame traveling back into the torch or hoses), which indicate potential issues with gas mixture or equipment.
- Immediately shut off the torch and investigate the cause of backfires or flashbacks, such as blocked tips, improper gas pressures, or leaks in the system.
Conclusion
In conclusion, oxyacetylene welding offers a versatile and reliable method for joining metals, but success hinges on the skill, knowledge, and dedication of the welder. With the right equipment, training, and commitment to safety and efficiency, welders can unlock the full potential of oxyacetylene welding and embark on a rewarding journey of craftsmanship and innovation.