What Is Hot Pressure Welding?
Introduction
Welding is an important process used in various industries for joining materials. One of the most effective welding techniques is hot pressure welding, which involves the use of heat and pressure to join materials together. In this article, we will explore the basics of hot pressure welding, its importance in various industries, and its brief history.
Hot pressure welding is a welding technique that involves the use of heat and pressure to join two materials together. The process works by heating the materials to a specific temperature, and then applying pressure to them to create a bond. The heat softens the materials, making them more malleable and easier to join, while the pressure helps to create a strong, permanent bond. Hot pressure welding is commonly used in industries such as automotive, aerospace, and construction.
Hot pressure welding is an important process used in various industries due to its many advantages. One of the main benefits of hot pressure welding is that it creates a strong, permanent bond between materials. This makes it ideal for use in applications where strength and durability are important, such as in the construction of buildings and bridges, or in the production of automobiles and aircraft.
Hot pressure welding is also a cost-effective welding technique, as it requires fewer materials and less energy compared to other welding methods. This makes it a popular choice for manufacturing processes that require high volumes of production. Additionally, hot pressure welding can be used to join dissimilar materials, such as metals and plastics, which is not possible with other welding techniques.
Brief history of hot pressure welding
The history of hot pressure welding dates back to the early 20th century when the process was first developed for use in the manufacturing of aircraft. Over time, the process has been refined and improved, and today it is widely used in various industries around the world.
In the early days of hot pressure welding, the process was performed manually, with skilled welders using torches and other heating elements to apply heat and pressure to the materials being joined. Today, hot pressure welding has been automated, with computer-controlled machines and robotic welders performing the process with greater accuracy and efficiency.
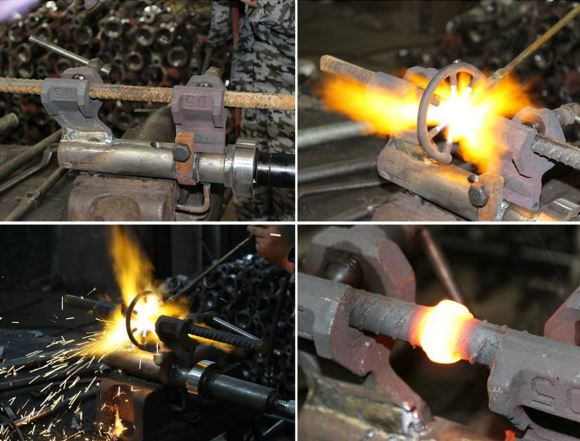
Hot pressure welding is an important welding technique used in various industries due to its many advantages, including its strength, durability, and cost-effectiveness. As technology continues to advance, we can expect to see further improvements in the process, making it an even more essential part of modern manufacturing processes.
The Science Behind Hot Pressure Welding
Hot pressure welding is a welding process that involves the application of heat and pressure to two or more materials to form a permanent bond. The process can be performed manually, using specialized tools and equipment, or through automated machines and robotic welders. Here are the basic steps involved in hot pressure welding:
- Preparing the materials The materials to be welded are first prepared by cleaning and aligning them properly. This ensures that there are no contaminants on the surfaces and that the materials are in the correct position for welding.
- Applying heat Heat is then applied to the materials using a heating element such as a torch, hot plate or oven. The heat softens the materials and prepares them for the application of pressure.
- Applying pressure Once the materials have been heated to the appropriate temperature, pressure is then applied to the materials to form a bond. The pressure is applied using specialized tools such as rollers, hydraulic presses or clamps. The amount of pressure applied depends on the materials being welded and the thickness of the materials.
- Cooling and Finishing Once the materials have been bonded, they are allowed to cool down before finishing touches such as grinding, sanding or polishing are done to smooth out the weld.
Types of Hot Pressure Welding
There are several types of hot pressure welding methods used in various industries. Some of the common types of hot pressure welding include:
- Butt Welding This type of hot pressure welding is used to join two materials end-to-end, creating a strong, permanent bond.
- Flash Welding Flash welding is a type of hot pressure welding that involves the use of an electrical current to heat the materials being welded. The heat generated by the electrical current is used to soften the materials and form a bond.
- Resistance Welding Resistance welding is a type of hot pressure welding that involves the use of electrical resistance to generate heat and join materials together.
- Friction Welding Friction welding is a type of hot pressure welding that involves the use of friction to generate heat and create a bond between materials. This is done by rotating one material against the other at high speeds until they soften and bond together.
Advantages of Hot Pressure Welding
Hot pressure welding has several advantages over other welding techniques. Some of the main advantages of hot pressure welding include:
- Strength Hot pressure welding creates a strong, permanent bond between materials, making it ideal for applications where strength and durability are important.
- Cost-effective Hot pressure welding requires fewer materials and less energy compared to other welding methods, making it a more cost-effective option for manufacturing processes.
- Versatile Hot pressure welding can be used to join dissimilar materials, such as metals and plastics, making it a versatile option for various industries.
- Automation With the use of computer-controlled machines and robotic welders, hot pressure welding can be automated for greater efficiency and accuracy.
Hot pressure welding is an important welding technique used in various industries due to its many advantages. The process involves the application of heat and pressure to join materials together to create a strong, permanent bond. With the use of advanced technology, hot pressure welding has become a more efficient and cost-effective option for modern manufacturing processes. As the need for stronger and more durable materials continues to grow, hot pressure welding will continue to play a vital role in meeting these demands.
Applications of Hot Pressure Welding
Hot pressure welding is a versatile technique used in various industries due to its many advantages, including strength, durability, and cost-effectiveness. Here are some of the main applications of hot pressure welding in different industries:
Aerospace industry
Hot pressure welding is widely used in the aerospace industry to join high-strength metals such as titanium and aluminum alloys. These materials are often used to create aircraft parts such as wings, fuselage, and landing gear. Hot pressure welding is preferred in the aerospace industry due to its ability to create strong, lightweight, and durable welds that can withstand high stress and extreme temperatures.
Automotive industry
Hot pressure welding is commonly used in the automotive industry to join sheet metals and various types of alloys. The technique is used to create car parts such as body panels, frames, and exhaust systems. Hot pressure welding in the automotive industry is preferred due to its ability to create strong, lightweight, and corrosion-resistant welds that can withstand high stress and vibrations.
Electronics industry
Hot pressure welding is used in the electronics industry to join different types of metals and alloys to create electronic components such as connectors, switches, and sensors. Hot pressure welding is preferred in the electronics industry due to its ability to create precise and consistent welds that can withstand high temperatures and corrosion.
Construction industry
Hot pressure welding is used in the construction industry to join different types of metals and alloys to create structural components such as beams, columns, and trusses. Hot pressure welding is preferred in the construction industry due to its ability to create strong, durable, and weather-resistant welds that can withstand extreme loads and environmental conditions.
Medical industry
Hot pressure welding is used in the medical industry to join different types of metals and alloys to create medical devices such as orthopedic implants, dental implants, and surgical instruments. Hot pressure welding is preferred in the medical industry due to its ability to create precise and biocompatible welds that are free from contaminants and corrosion.
Hot pressure welding is a versatile technique that is widely used in various industries due to its many advantages. The technique is used to join different types of metals and alloys to create strong, durable, and precise welds that can withstand high stress, extreme temperatures, and environmental conditions. As technology continues to advance, the applications of hot pressure welding will continue to grow, making it a vital technique in modern manufacturing processes.
Advantages of Hot Pressure Welding
Hot pressure welding offers many advantages compared to other welding techniques. Here are some of the main advantages of hot pressure welding:
High strength joints
Hot pressure welding creates strong and durable welds that can withstand high stress, extreme temperatures, and environmental conditions. This is because the welding process uses both heat and pressure to create a metallurgical bond between the two materials being joined. The resulting weld has excellent mechanical properties and can provide high strength joints that are essential in many industrial applications.
High-quality finish
Hot pressure welding produces high-quality finishes with minimal oxidation, discoloration, and deformation of the welded material. This is because the welding process is carried out in a controlled environment with precise temperature and pressure settings. The resulting welds are clean, smooth, and free from porosity and other defects that can compromise the quality of the weld.
Minimal distortion of the welded material
Hot pressure welding produces minimal distortion of the welded material due to the even distribution of heat and pressure during the welding process. This means that the welded material retains its original shape and dimensions, reducing the need for post-welding machining and other finishing operations.
Reduced risk of defects
Hot pressure welding has a reduced risk of defects such as porosity, cracking, and incomplete fusion. This is because the welding process creates a metallurgical bond between the two materials being joined, resulting in a homogeneous and defect-free weld. Additionally, the controlled environment of hot pressure welding reduces the risk of contamination from external sources such as air and moisture.
Increased productivity
Hot pressure welding is a fast and efficient welding technique that can significantly increase productivity in industrial applications. The process can be automated, reducing the need for manual labor, and can be performed in a single pass, reducing the overall welding time. The resulting high-quality welds also reduce the need for post-welding inspections and repairs, further increasing productivity.
Hot pressure welding offers many advantages compared to other welding techniques. The process produces high strength joints, high-quality finishes, minimal distortion of the welded material, reduced risk of defects, and increased productivity. These advantages make hot pressure welding a preferred technique in many industrial applications where strength, durability, and precision are essential.
Disadvantages of Hot Pressure Welding
Despite its numerous advantages, hot pressure welding does have some disadvantages that limit its use in certain applications. Here are some of the main disadvantages of hot pressure welding:
High cost of equipment
Hot pressure welding requires specialized equipment that can be expensive to purchase and maintain. The equipment needs to maintain precise temperature and pressure conditions, and it must be capable of handling large and heavy materials. The high cost of equipment can make hot pressure welding unaffordable for small-scale projects or industries with tight budgets.
Skilled labor required
Hot pressure welding is a complex process that requires skilled and experienced welders to ensure the quality of the welds. Welders must have a good understanding of the equipment, materials, and welding parameters to produce high-quality welds consistently. The shortage of skilled labor can also be a challenge for industries that rely on hot pressure welding.
Limited to certain types of materials
Hot pressure welding is only suitable for certain types of materials, including metals and some thermoplastics. Materials with low melting points or poor thermal conductivity are not suitable for hot pressure welding, and the process can cause damage to some composite materials. This limitation can be a significant disadvantage for industries that require the joining of materials that are not compatible with hot pressure welding.
Difficulties in welding dissimilar materials
Hot pressure welding can be challenging when joining dissimilar materials with different thermal properties and coefficients of expansion. The different rates of expansion and contraction of the materials during the welding process can cause cracking and deformation of the welded joint. Welders must use specialized techniques and equipment to minimize these difficulties, making the process more challenging and time-consuming.
Hot pressure welding has some disadvantages that limit its use in certain applications. The high cost of equipment, the need for skilled labor, limitations on the types of materials that can be welded, and difficulties in welding dissimilar materials are some of the main disadvantages. Despite these limitations, hot pressure welding remains a preferred technique in many industries where the advantages outweigh the disadvantages.
Safety Considerations for Hot Pressure Welding
Hot pressure welding can be a hazardous process, as it involves high temperatures and pressures that can cause serious injury if not handled properly. Here are some of the main safety considerations for hot pressure welding:
Hazards associated with high temperatures and pressure
The high temperatures and pressures used in hot pressure welding can pose a risk of burns, explosions, and other serious accidents. Welders must be aware of the hazards and take appropriate precautions to minimize the risks. Failure to follow proper safety procedures can result in severe injuries or even fatalities.
Protective equipment and clothing
Welders must wear appropriate protective equipment and clothing to protect themselves from the hazards associated with hot pressure welding. This includes heat-resistant gloves, aprons, and face shields to protect against heat, sparks, and debris. Welders must also wear protective clothing made from materials that can withstand high temperatures and pressure.
Safe handling of hot pressure welding equipment
Hot pressure welding equipment must be handled with care to prevent accidents and injuries. Welders must be trained on the proper use and maintenance of the equipment to ensure that it is used safely and effectively. The equipment must be inspected regularly to identify any potential hazards or defects.
Additional safety considerations include proper ventilation to prevent the buildup of toxic fumes, and the use of fire extinguishers and other safety equipment in case of an emergency.
Hot pressure welding is a hazardous process that requires strict adherence to safety procedures to prevent accidents and injuries. Welders must be aware of the hazards associated with high temperatures and pressures and use appropriate protective equipment and clothing. Safe handling of hot pressure welding equipment is also essential to prevent accidents and maintain a safe working environment. By following proper safety procedures, welders can minimize the risks and ensure a safe and productive workplace.
FAQs
What is the process of hot welding?
Hot pressure welding is a technique that uses heat and pressure to join two materials together. The process involves heating the materials to a specific temperature, and then applying pressure to them in order to create a bond.
What is cold pressure welding process?
Cold pressure welding, also known as cold welding, is a technique that involves applying pressure to two metals at room temperature in order to create a bond. The process is typically used for soft metals like copper, aluminum, and gold.
What is hot welding and cold welding?
Hot welding and cold welding are two different techniques for joining metals. Hot welding involves heating the materials to a high temperature before applying pressure to create a bond, while cold welding involves applying pressure to two metals at room temperature.
Is heat and pressure called welding?
Heat and pressure are often used in the welding process to join two materials together, but they are not the only factors involved. Other welding techniques, such as gas welding and electric welding, use different methods to create a bond between materials.
Where is cold pressure welding used?
Cold pressure welding is commonly used in industries where soft metals like copper, aluminum, and gold need to be joined. It is often used in the electronics and electrical industries to create connections between wires and terminals.
What are all 4 types of welding?
There are several types of welding, including:
Gas welding, Electric welding, Arc welding and Resistance welding.
How does hot pressure welding work?
Hot pressure welding involves heating the materials to a specific temperature, and then applying pressure to them in order to create a bond. The heat softens the materials, making them more malleable and easier to join, while the pressure helps to create a strong, permanent bond.
What do you mean by hot welding?
Hot welding refers to a welding process that uses heat to soften the materials being joined, making them easier to manipulate and join together. The heat is typically applied using a torch or other heating element.
What is the temperature of hot gas welding?
Hot gas welding typically involves heating the materials to a temperature of around 1,800 degrees Fahrenheit. The heat is applied using a torch that mixes fuel gas and oxygen to create a flame.
Which gas is used in hot welding?
The gas used in hot welding depends on the specific process being used. Some common gases used in welding include acetylene, propane, and natural gas.
Which gas is used in hot welding?
The gas used in hot welding can vary depending on the process and the materials being joined. For example, acetylene is commonly used in oxyacetylene welding, while propane and natural gas are often used in gas welding.
Which welding has highest temperature?
The welding process with the highest temperature is typically gas welding, which can reach temperatures of up to 6,500 degrees Fahrenheit. However, other processes like electric welding and plasma arc welding can also reach extremely high temperatures.
Conclusion
Hot pressure welding is an essential joining process in the manufacturing industry that involves the use of heat and pressure to join two or more metal parts together. This process has a wide range of applications in various industries, including automotive, aerospace, and construction, among others. Hot pressure welding is preferred over other joining techniques because it produces high-quality and durable joints with excellent mechanical properties. Additionally, it allows for the joining of dissimilar metals, which cannot be done using other techniques.
In recent years, there have been significant advancements in hot pressure welding technology. The future of this technology looks promising, with continued research and development expected to enhance its capabilities further. One area of focus is the development of new welding materials that can withstand high temperatures and pressures. Additionally, new welding techniques, such as friction stir welding and laser welding, are being explored to improve the efficiency and effectiveness of hot pressure welding. There is also ongoing research on the automation of hot pressure welding processes to increase productivity and reduce costs.
Hot pressure welding is a critical joining process that is vital to the manufacturing industry. Therefore, there is a need for continued research and development to improve the process and its capabilities. This can be achieved through collaborations between researchers, academia, and industry stakeholders. Moreover, government agencies should invest in funding research programs aimed at advancing hot pressure welding technology. With further development, hot pressure welding can become an even more efficient and cost-effective joining technique, making it an essential tool in the manufacturing industry.