What is Projection Welding?
Introduction
Projection welding is a specialized welding technique that plays a crucial role in various industries where strong and reliable weld joints are required. It is a form of resistance welding that involves joining two or more metal components together using localized heat generated by passing an electrical current through specifically designed projections or embossed features on the workpieces.
Definition and Overview of Projection Welding
Projection welding is a resistance welding process where small, raised projections or embossed features on the workpieces concentrate the heat and pressure during the welding operation. These projections act as localized resistance points, allowing the electrical current to pass through them, creating intense heat at those points. The heat causes the projections to melt, resulting in fusion between the workpieces and the formation of a strong weld joint.
Importance and Applications of Projection Welding
Projection welding holds significant importance in industries where high-speed and efficient welding is required. It offers several advantages over other welding techniques, such as its ability to produce strong and reliable welds without the need for additional materials like filler metals or fluxes.
Projection welding finds extensive applications in the automotive industry, where it is used for welding components such as brackets, clips, and fasteners. It is also widely utilized in the electrical and electronic industry for joining terminals, connectors, and other small electrical components. Moreover, projection welding is commonly employed in appliance manufacturing, where it is used for assembling parts of household appliances like refrigerators, ovens, and washing machines.
The versatility of projection welding allows it to be used with a wide range of materials, including steels, stainless steels, and aluminum alloys. This makes it a preferred choice in industries that work with diverse materials and require strong and durable welds.
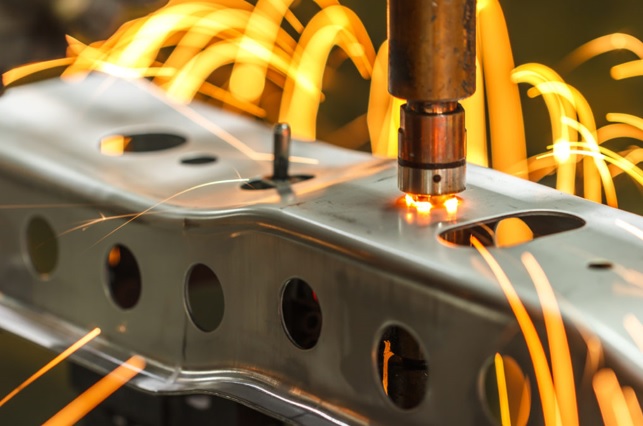
Understanding Projection Welding
Explanation of the Welding Process
Projection welding involves a series of steps that result in the creation of a weld joint between two or more metal components. Here is a simplified explanation of the projection welding process:
- Preparation: The metal components to be joined are properly prepared by cleaning the surfaces to remove any dirt, oils, or oxides that could hinder the welding process.
- Alignment: The workpieces are aligned and positioned in the welding machine, ensuring that the projections or embossed features are in contact with each other.
- Application of Pressure: Electrodes are positioned on either side of the workpieces. These electrodes apply pressure to hold the workpieces firmly together during the welding process.
- Application of Current: An electrical current is passed through the electrodes, which in turn passes through the projections on the workpieces. The electrical resistance at the projection points generates intense heat, causing the projections to melt.
- Formation of Weld: As the projections melt, they fuse with the adjacent workpiece, creating a solid weld joint. The heat and pressure applied ensure proper bonding and integrity of the joint.
- Cooling: Once the welding is complete, the workpieces are allowed to cool down. Cooling may involve various methods, such as natural air cooling or water cooling, depending on the application requirements.
Comparison to Other Welding Techniques
Projection welding differs from other welding techniques in terms of its specific advantages and limitations. Here are a few points of comparison:
- Resistance Spot Welding: In resistance spot welding, electrical current is passed through the workpieces at specific spots using circular electrodes. This technique is suitable for joining thin sheets of metal, whereas projection welding is better suited for thicker materials and components with localized projections.
- Laser Welding: Laser welding utilizes a highly focused laser beam to create welds. While laser welding offers high precision and flexibility, projection welding is often more cost-effective and suitable for high-volume production due to its simplicity and speed.
- Gas Metal Arc Welding (GMAW): GMAW, also known as MIG welding, involves the use of an electric arc and a consumable electrode wire. It is commonly used for welding thick sections and offers high deposition rates, but it may not be as suitable for joining small components or materials with dissimilar melting points.
Projection welding’s key advantages include high speed, efficiency, and the ability to create strong and reliable welds without additional materials. Its simplicity and versatility make it a preferred choice in various industries, especially when dealing with localized projections or embossed features on workpieces.
Components and Setup
Description of Projection Welder Machine
A projection welder machine is specifically designed to facilitate the projection welding process efficiently. It consists of several components and mechanisms that work together to achieve precise and reliable welds. Here is a brief description of a typical projection welder machine:
- Frame: The machine’s frame provides the structural support and stability required during the welding process. It is designed to withstand the forces exerted during the application of pressure and current.
- Power Supply: The power supply unit is responsible for providing the electrical energy required for projection welding. It delivers controlled electrical current to the welding electrodes.
- Control Panel: The control panel allows the operator to adjust and monitor various parameters of the welding process, such as current intensity, welding time, and pressure. It provides a user-friendly interface for precise control and monitoring.
- Electrode System: The electrode system includes the upper and lower electrodes, which apply pressure to the workpieces during welding. These electrodes conduct the electrical current and help concentrate the heat at the projection points.
- Cooling System: To prevent excessive heat buildup and ensure the longevity of the machine, a cooling system is integrated. It may include fans, water circulation, or other cooling mechanisms to maintain optimal operating temperatures.
Key Components Involved in Projection Welding
In projection welding, several components play essential roles in achieving successful welds. These components work in tandem to provide the necessary heat and pressure for the welding process. Here are the key components involved:
- Workpieces: The metal components to be joined are referred to as workpieces. These can be sheets, plates, or other forms with localized projections or embossed features that facilitate the welding process.
- Projections: The projections on the workpieces are crucial elements in projection welding. These raised features concentrate the heat and pressure, facilitating localized melting and fusion between the workpieces.
- Electrodes: The upper and lower electrodes are responsible for conducting the electrical current and applying pressure to the workpieces. They ensure proper contact between the projections, allowing efficient heat generation and weld formation.
- Electrical Current: The electrical current passes through the electrodes and flows through the projections, generating heat due to resistance. The current intensity and duration are carefully controlled to achieve the desired weld quality.
Importance of Electrode Design
The design of the electrodes used in projection welding is critical for achieving optimal weld quality. Here are a few reasons why electrode design is important:
- Contact and Pressure: The electrode design should ensure proper contact with the workpieces and provide sufficient pressure to hold the components together during welding. A good electrode design ensures uniform pressure distribution across the projections, leading to consistent and reliable welds.
- Heat Dissipation: Efficient heat dissipation is crucial to prevent excessive heat buildup and electrode damage. The design should consider factors such as electrode material, cooling mechanisms, and surface area to maximize heat dissipation and prolong electrode lifespan.
- Electrical Conductivity: Electrodes should have high electrical conductivity to minimize energy loss and promote efficient current flow through the projections. Choosing appropriate electrode materials with good conductivity helps optimize the welding process.
- Durability and Maintenance: Electrode design affects the durability and maintenance requirements of the projection welder machine. Well-designed electrodes are easier to replace, clean, and maintain, reducing downtime and ensuring consistent performance.
By considering these aspects of electrode design, projection welding can be carried out effectively, resulting in high-quality weld joints that meet industry standards and requirements.
How Projection Welding Works
Step-by-step Process of Projection Welding
Projection welding follows a systematic process to create strong and reliable weld joints. Here is a step-by-step overview of how projection welding works:
- Preparation: The workpieces to be welded are prepared by cleaning the surfaces to remove any contaminants that could affect the welding process.
- Alignment: The workpieces are aligned and positioned in the projection welding machine, ensuring that the projections on each piece are properly matched and in contact with each other.
- Electrode Placement: Upper and lower electrodes are positioned on either side of the workpieces, with the projections fitting within the electrode indentations. The electrodes apply pressure to hold the workpieces firmly together during welding.
- Electrical Current Application: Once the electrodes are in place, an electrical current is applied to the electrodes. The current passes through the electrodes and flows through the projections, creating intense heat at those localized points.
- Heat Generation: The electrical resistance at the projection points causes the projections to heat up rapidly. As a result, the projections melt, reaching their melting temperature, while the surrounding material remains relatively unaffected.
- Weld Formation: The molten projections fuse with the adjacent workpiece, creating a solid weld joint. The pressure applied by the electrodes ensures intimate contact between the melted projections and the surrounding material, facilitating proper bonding and metallurgical fusion.
- Cooling: After the welding is complete, the electrodes are lifted, and the workpieces are allowed to cool down. Cooling may be done using natural air cooling or water cooling, depending on the application requirements and the materials being welded.
Role of Electrical Current and Pressure in the Process
In projection welding, electrical current and pressure play vital roles in achieving successful welds:
- Electrical Current: The electrical current passing through the projections generates heat due to resistance. This heat melts the projections, enabling them to fuse with the adjacent material. The current intensity and duration are carefully controlled to ensure proper heat generation without causing excessive damage or distortion.
- Pressure: The electrodes apply pressure to the workpieces during the welding process. Pressure helps establish and maintain good contact between the projections, ensuring proper heat transfer and bonding. It also helps to squeeze out any trapped air or contaminants between the workpieces, promoting sound weld formation.
The combination of electrical current and pressure allows for localized heating and controlled fusion at the projection points, resulting in reliable and strong weld joints.
Factors Influencing the Quality of Projection Welds
Several factors influence the quality of projection welds. These factors should be carefully considered and controlled to achieve desired weld characteristics:
- Projections Design: The size, shape, and distribution of the projections on the workpieces impact the welding process. Proper projection design ensures effective heat concentration and facilitates proper fusion during welding.
- Material Properties: The material composition and properties of the workpieces influence the weldability and the resulting weld quality. Factors such as electrical conductivity, melting temperature, and thermal conductivity affect the heat generation and transfer during projection welding.
- Electrode Design and Condition: The design and condition of the electrodes significantly impact weld quality. Proper electrode alignment, shape, and condition ensure uniform pressure distribution and efficient current flow, resulting in consistent welds.
- Current Intensity and Duration: The electrical current parameters, such as intensity and duration, should be optimized for the specific materials and projections involved. Controlling these parameters ensures proper heat generation without causing excessive heat damage or insufficient fusion.
- Pressure Application: The pressure applied by the electrodes should be sufficient to ensure proper contact and intimate bonding between the projections and the surrounding material. Insufficient pressure can lead to weak welds, while excessive pressure may cause deformation or damage to the workpieces.
- Surface Preparation: Proper cleaning and preparation of the workpiece surfaces are crucial for achieving good weld quality. Contaminants, oxides, or coatings can inhibit heat transfer and negatively affect the weld integrity.
By carefully considering and controlling these factors, projection welding can produce high-quality welds that meet the required standards and performance criteria.
Advantages of Projection Welding
Projection welding offers several advantages that make it a preferred welding method in various industries. Here are the key advantages of projection welding:
High-speed and Efficient Welding Method
Projection welding is known for its high-speed capabilities and efficient operation. The concentrated heat generated at the projection points allows for rapid melting and fusion, resulting in shorter welding cycle times compared to other welding techniques. This makes projection welding ideal for high-volume production environments where speed and productivity are essential.
Strong and Reliable Weld Joints
Projection welding produces weld joints that exhibit exceptional strength and reliability. The localized heat and pressure applied to the projections ensure proper bonding and metallurgical fusion between the workpieces. As a result, projection welds often have excellent mechanical properties, including high tensile and shear strength. These strong and reliable weld joints are critical for applications that require structural integrity and resistance to mechanical stress.
Suitable for a Wide Range of Materials
One of the significant advantages of projection welding is its versatility in joining a wide range of materials. It is compatible with various metals, including steels, stainless steels, and aluminum alloys. This flexibility allows projection welding to be used in diverse industries that work with different materials. Whether it is automotive, electrical, or appliance manufacturing, projection welding provides a reliable and efficient solution for joining dissimilar or similar materials.
Additionally, projection welding can join materials of varying thicknesses without compromising the weld quality. This versatility expands its application potential and makes it a preferred choice for welding components of different sizes and configurations.
Applications of Projection Welding
Projection welding finds widespread applications in various industries where strong and reliable weld joints are required. Here are some notable industries that extensively utilize projection welding:
Automotive Industry
The automotive industry relies heavily on projection welding for joining various components. It is commonly used for welding brackets, clips, fasteners, and other structural elements in automobile assembly. Projection welding provides the necessary strength and durability for critical automotive components, ensuring the integrity and safety of the vehicles. Additionally, its high-speed capabilities make it well-suited for automotive mass production environments.
Electrical and Electronic Industry
Projection welding plays a vital role in the electrical and electronic industry. It is employed for joining terminals, connectors, and small electrical components like switches and sensors. The precision and reliability of projection welding make it ideal for applications that require secure electrical connections and resistance to vibration or thermal stress. By ensuring strong and consistent welds, projection welding helps maintain the functionality and performance of electrical and electronic devices.
Appliance Manufacturing
In appliance manufacturing, projection welding is extensively used for assembling various components of household appliances. It is employed for joining parts such as refrigerator shelves, oven racks, dishwasher racks, washing machine drums, and other structural elements. The strength and durability provided by projection welding ensure the longevity and reliability of appliances, withstanding the daily wear and tear they experience.
Other Industries Utilizing Projection Welding
Projection welding also finds applications in other industries, including:
- Aerospace: Projection welding is used for joining components in the aerospace industry, such as aircraft structures, engine parts, and fuel system components. The strong and reliable welds achieved through projection welding contribute to the safety and performance of aerospace systems.
- Furniture: Projection welding is employed in the manufacturing of furniture, particularly in metal furniture production. It helps join various metal components, such as frames, brackets, and supports, ensuring the structural stability and longevity of the furniture.
- Construction: In the construction industry, projection welding is utilized for joining structural elements like steel beams, columns, and other metal components. The robust weld joints achieved through projection welding contribute to the overall strength and stability of the constructed structures.
- General Manufacturing: Projection welding is widely used in general manufacturing applications where strong welds are required for various metal components. It finds applications in industries such as machinery manufacturing, metal fabrication, and tooling.
The versatility of projection welding makes it suitable for numerous industries where strong and reliable weld joints are necessary. Its applications span from automotive and electrical industries to appliance manufacturing and beyond, providing efficient and durable solutions for joining metal components together.
Challenges and Limitations
While projection welding offers many advantages, there are also challenges and limitations that need to be considered. Understanding these limitations helps in selecting the appropriate welding method for specific applications. Here are some common challenges and limitations of projection welding:
Heat Generation and Distortion
One challenge in projection welding is the generation of intense heat at the projection points. This heat can potentially cause distortion or deformation in the workpieces, especially if they are thin or have uneven heat dissipation properties. It is essential to carefully control the welding parameters, such as current intensity and duration, to prevent excessive heat buildup and minimize distortion.
Complexity of Electrode Design
The design and maintenance of electrodes in projection welding can be complex. Achieving uniform pressure distribution and proper alignment of the electrodes on the projections require careful electrode design and setup. Additionally, electrode wear and maintenance are important considerations to ensure consistent welding performance. Regular maintenance and replacement of electrodes may be required to maintain optimal weld quality.
Material Limitations
While projection welding is compatible with a wide range of metals, certain materials may pose challenges. Materials with significantly different melting points or poor thermal conductivity may require specialized approaches or alternative welding methods. Some materials, such as certain heat-sensitive plastics or non-conductive materials, are not suitable for projection welding due to their inability to conduct electrical current.
Moreover, dissimilar material combinations can present challenges in achieving strong and reliable welds. The compatibility of materials in terms of metallurgical compatibility, joint strength, and susceptibility to galvanic corrosion should be carefully considered.
FAQs
What is an example of projection welding?
An example of projection welding is joining metal brackets or clips to a larger structure, such as in automotive assembly.
What is spot and projection welding?
Spot welding and projection welding are both resistance welding techniques. Spot welding involves joining two overlapping metal sheets by applying pressure and electrical current to localized spots, while projection welding uses specially designed projections on one or both workpieces to concentrate heat and facilitate the weld.
What is seam welding and projection welding?
Seam welding is a process where two overlapping metal sheets are continuously welded along the entire seam, creating a leak-tight joint. Projection welding, on the other hand, focuses on joining specific projection points on the workpieces.
What materials are used in projection welding?
Projection welding can be performed on various materials, including steels, stainless steels, aluminum alloys, and other conductive metals that can effectively conduct electrical current and generate localized heat.
What is called seam welding?
Seam welding refers to the continuous welding of overlapping metal sheets along a seam, creating a continuous joint. It is often used for creating leak-tight seals, such as in tanks or pipes.
What are the 4 different types of welding?
The four different types of welding are arc welding, gas welding, resistance welding, and solid-state welding.
What is the temperature of projection welding?
The temperature of projection welding can vary depending on factors such as the material being welded, the current intensity, and the duration of the weld. Generally, temperatures can reach the melting point of the projections, ensuring proper fusion with the surrounding material.
Which electrode are used for projection welding?
Projection welding typically uses copper alloy electrodes. The electrodes are designed to match the shape of the projections, providing optimal contact and ensuring efficient heat transfer during the welding process.
What are the characteristics of projection welding?
Characteristics of projection welding include high-speed operation, strong and reliable weld joints, compatibility with a wide range of materials, and the ability to join dissimilar materials of varying thicknesses.
What are the advantages of projection welding?
The advantages of projection welding include high-speed and efficient welding, strong and reliable weld joints, suitability for a wide range of materials, and the ability to join dissimilar materials.
What is the strength of a projection weld?
The strength of a projection weld is typically high, with mechanical properties comparable to or exceeding the base material. The localized heat and pressure in projection welding facilitate proper fusion and metallurgical bonding, resulting in robust and durable weld joints.
What are the problems with projection welding?
Some potential problems with projection welding include heat generation leading to distortion or deformation of workpieces, the complexity of electrode design and maintenance, and limitations in joining dissimilar materials with significantly different properties. Careful process control and optimization are necessary to address these challenges and achieve desired weld quality.
Conclusion
In conclusion, projection welding is a highly efficient and versatile welding method used in various industries for creating strong and reliable weld joints. Its ability to deliver high-speed welding, coupled with the strength and durability of the resulting welds, makes it a preferred choice for many applications. The automotive, electrical and electronic, and appliance manufacturing industries extensively utilize projection welding for joining components that require structural integrity and resistance to mechanical stress.
However, projection welding does have its challenges and limitations. Heat generation and potential distortion of workpieces, complexity in electrode design and maintenance, and material limitations are factors that need to be carefully addressed. By understanding these limitations and considering alternative welding methods when necessary, manufacturers can ensure successful and efficient welding operations.
Despite these challenges, projection welding remains a widely adopted welding technique due to its advantages, including high-speed operation, strong weld joints, and compatibility with a wide range of materials. Its applications extend beyond the automotive, electrical, and appliance industries, finding use in aerospace, furniture, construction, and general manufacturing sectors.