What is x-ray welding?
Introduction
Definition of X-ray welding
X-ray welding is a specialized welding technique that utilizes X-rays to weld two pieces of metal together. The process involves using an X-ray machine to generate high-energy radiation, which is then directed onto the weld area to produce a weld. This technique is particularly useful for welding materials that are difficult to weld using traditional welding methods.
Importance of X-ray welding
X-ray welding is a crucial technique in many industries, including aerospace, automotive, construction, and medical. It provides a high level of precision and control, allowing for the creation of strong, durable, and defect-free welds. The technique is particularly useful in the production of high-stress components, such as those used in the aerospace industry, where strength and durability are paramount.
Purpose of the article
The purpose of this article is to provide a comprehensive overview of X-ray welding. We will discuss the X-ray welding process, its advantages and limitations, and its applications in various industries. We will also examine the safety considerations that must be taken into account when performing X-ray welding, as well as the importance of X-ray welding inspection. By the end of the article, readers will have a better understanding of X-ray welding and its place in modern manufacturing.
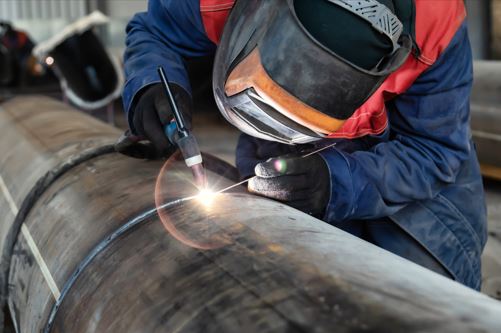
X-ray Welding process
How X-ray welding works
X-ray welding utilizes high-energy radiation to generate heat at the weld area, which then melts the two pieces of metal together. The process involves directing the X-ray beam onto the weld area, where it is absorbed by the metal and converted into heat. This heat then melts the metal, allowing it to fuse together.
X-ray welding machines use either an X-ray tube or a radioactive isotope as the source of the X-rays. The X-ray tube generates X-rays using an electron beam, while the radioactive isotope emits X-rays as it decays. Both methods produce high-energy radiation that can penetrate the metal and generate the required heat.
The X-ray welding process requires specialized equipment and trained operators, as the radiation produced by the X-ray machine can be dangerous. Protective gear, such as lead aprons and gloves, must be worn to minimize the risk of exposure to radiation.
Advantages of X-ray welding
X-ray welding offers several advantages over traditional welding techniques, including:
- High precision: X-ray welding allows for precise control over the amount of heat applied to the weld area, resulting in a high degree of precision and accuracy in the final product.
- Strong, durable welds: X-ray welding produces strong, high-quality welds that are free from defects, such as cracks, porosity, and inclusions.
- Versatility: X-ray welding can be used to weld a wide range of materials, including metals that are difficult to weld using traditional methods, such as titanium and magnesium.
- Reduced distortion: X-ray welding produces minimal distortion in the metal, allowing for the creation of complex shapes and designs.
Limitations of X-ray welding
X-ray welding also has some limitations, including:
- Cost: X-ray welding requires specialized equipment and trained operators, making it more expensive than traditional welding techniques.
- Safety concerns: The radiation produced by the X-ray machine can be dangerous if proper safety protocols are not followed. Operators must be trained in radiation safety and wear appropriate protective gear.
- Time-consuming: X-ray welding is a time-consuming process, as each weld must be carefully inspected using X-ray imaging to ensure quality and accuracy.
- Accessibility: X-ray welding may not be accessible in all locations, as it requires specialized equipment and trained operators.
Applications of X-ray Welding
Aerospace Industry
X-ray welding is widely used in the aerospace industry for the production of aircraft parts and components. The high precision and strong welds produced by X-ray welding make it ideal for creating components that are required to withstand high stress and pressure, such as those found in jet engines and spacecraft. X-ray welding is also used in the repair and maintenance of aircraft parts, ensuring that they are safe and reliable.
Automotive Industry
The automotive industry also utilizes X-ray welding for the production of vehicle components, such as engine parts and exhaust systems. X-ray welding is particularly useful in the production of components made from high-strength materials, such as aluminum and titanium, which are difficult to weld using traditional methods. X-ray welding is also used in the repair and maintenance of vehicles, ensuring that they are safe and reliable.
Construction Industry
X-ray welding is used in the construction industry for the production of large-scale components, such as pipelines and oil rigs. X-ray welding allows for the creation of strong, durable welds that are free from defects, ensuring that the components can withstand harsh environmental conditions and heavy usage. X-ray welding is also used in the repair and maintenance of structures, ensuring that they are safe and structurally sound.
Medical Industry
The medical industry utilizes X-ray welding for the production of medical devices, such as pacemakers and implantable devices. X-ray welding allows for the creation of strong, durable welds that are free from defects, ensuring that the devices are safe and reliable. X-ray welding is also used in the repair and maintenance of medical equipment, ensuring that it is safe and effective.
Overall, X-ray welding is a versatile welding technique that is used in a wide range of industries for the production of high-quality, reliable components and devices. Its ability to produce precise, strong, and durable welds makes it an essential part of modern manufacturing.
Safety Considerations in X-ray Welding
Protective Equipment
Protective equipment is essential when working with X-ray welding equipment. The following protective gear is necessary:
1. Lead aprons: These protect the operator from exposure to X-ray radiation.
2. Lead gloves: These protect the operator’s hands from exposure to X-ray radiation.
3. Lead glasses: These protect the operator’s eyes from X-ray radiation.
4. Respirator: X-ray welding can produce toxic fumes and gases, so a respirator must be worn to protect the operator from inhaling them.
5. Radiation dosimeter: This device measures the amount of radiation to which the operator has been exposed.
Hazards of X-ray radiation
X-ray radiation can be hazardous to human health, so proper safety measures must be taken when working with X-ray welding equipment. The following are the hazards of X-ray radiation:
1. Skin burns: X-ray radiation can cause burns on the skin if the operator is not wearing protective gear.
2. Radiation sickness: Prolonged exposure to X-ray radiation can lead to radiation sickness, which can cause nausea, vomiting, and fatigue.
3. Cancer: Exposure to X-ray radiation over a long period can increase the risk of developing cancer.
4. Genetic damage: Exposure to X-ray radiation can cause genetic damage, which can be passed on to future generations.
Safety protocols
To minimize the risks associated with X-ray welding, the following safety protocols must be followed:
1. Proper training: Operators must receive proper training on the safe use of X-ray welding equipment.
2. Protective gear: Operators must wear appropriate protective gear, such as lead aprons, gloves, and glasses.
3. Radiation monitoring: Radiation dosimeters must be used to measure the amount of radiation to which the operator has been exposed.
4. Controlled areas: X-ray welding must be carried out in a controlled area that is restricted to authorized personnel only.
5. Inspection: X-ray welds must be inspected using X-ray imaging to ensure quality and accuracy.
Safety considerations are of utmost importance when working with X-ray welding equipment. Operators must be trained in radiation safety, wear appropriate protective gear, and follow proper safety protocols to minimize the risk of exposure to X-ray radiation.
X-ray Welding Inspection
Importance of X-ray welding inspection
X-ray welding inspection is a critical part of the X-ray welding process. Inspection helps to ensure the quality and integrity of the welds produced. Welds that are not inspected can lead to failures in service, which can be catastrophic, particularly in industries such as aerospace, automotive, and medical. X-ray welding inspection also helps to identify defects early in the welding process, making it easier to correct them before the components are put into service.
Methods of X-ray inspection
There are two primary methods of X-ray inspection in X-ray welding:
1. Radiographic inspection: This involves exposing the weld to X-rays and capturing the resulting image on film or digital media. The image produced shows the internal structure of the weld, making it possible to detect any defects or inconsistencies.
2. Computed tomography (CT) inspection: This method uses X-ray imaging to create a 3D image of the weld. The resulting image can be manipulated to visualize the internal structure of the weld, making it easier to detect defects and inconsistencies.
Qualification of X-ray inspectors
X-ray inspection is a specialized field that requires a high level of expertise and training. X-ray inspectors must be trained to read and interpret X-ray images accurately. They must also be familiar with the codes and standards that govern X-ray welding in their industry. The following are the steps involved in the qualification of X-ray inspectors:
1. Formal education: X-ray inspectors must have a formal education in non-destructive testing (NDT) and X-ray inspection. They must have a basic understanding of radiation safety, physics, and the principles of X-ray imaging.
2. On-the-job training: X-ray inspectors must receive on-the-job training under the supervision of a qualified inspector. This training typically involves hands-on experience in X-ray inspection and interpretation of X-ray images.
3. Certification: X-ray inspectors must obtain certification from a recognized organization, such as the American Society for Non-Destructive Testing (ASNT). Certification requires passing a written exam and a practical exam, demonstrating the ability to interpret X-ray images accurately.
X-ray welding inspection is a crucial part of the X-ray welding process, ensuring the quality and integrity of the welds produced. X-ray inspection methods include radiographic inspection and CT inspection, and X-ray inspectors must undergo a rigorous qualification process to ensure their competence and expertise in the field of X-ray inspection.
FAQs
What is X-ray welding?
X-ray welding is a type of welding process that uses high-energy X-rays to heat and join metal parts together, producing a precise, strong weld.
What is the principle of X-ray?
The principle of X-ray involves the use of electromagnetic radiation to create images of the internal structures of objects, including metals. X-rays penetrate materials, and the resulting image shows the internal structure of the object, making it possible to detect any defects or inconsistencies.
Why do you X-ray welds?
Welds are X-rayed to ensure their quality and integrity. Welds that are not inspected can lead to failures in service, which can be catastrophic. X-ray inspection also helps to identify defects early in the welding process, making it easier to correct them before the components are put into service.
What is the X-ray source for weld inspection?
The X-ray source for weld inspection is typically a high-energy X-ray machine. This machine produces X-rays that penetrate the weld and create an image of its internal structure.
Which ray is produced during welding?
During welding, X-rays are produced as a result of the high-energy electron interaction with the metal atoms.
What are the two sources of radiation used in radiographic NDT?
The two sources of radiation used in radiographic NDT are X-rays and gamma rays.
What are the two types of radiation?
The two types of radiation are ionizing radiation and non-ionizing radiation.
What are the two types of radiography?
The two types of radiography are film radiography and digital radiography.
Conclusion
X-ray welding is a welding technique that uses X-rays to create precise, strong, and durable welds in a wide range of materials. It is used in various industries, including aerospace, automotive, construction, and medical. The high precision and strong welds produced by X-ray welding make it ideal for creating components that are required to withstand high stress and pressure. The future of X-ray welding looks bright, with advancements in technology and research leading to improved techniques and equipment. The use of robotics and automation is becoming increasingly popular in X-ray welding, allowing for greater efficiency and accuracy in the welding process. The development of new materials and alloys is also driving the need for improved welding techniques, and X-ray welding is expected to play a significant role in meeting these demands. In conclusion, X-ray welding is a valuable welding technique that offers precision, strength, and durability in the production of components and devices across various industries. While there are hazards associated with X-ray radiation, proper safety measures can minimize the risks. With advancements in technology and research, the future of X-ray welding looks promising, and it is likely to remain an essential part of modern manufacturing for years to come.