What Skills Are Required for Welding?
Welding is a crucial trade in numerous industries, ranging from construction and automotive to aerospace and manufacturing. It involves joining metal parts together using various techniques and processes to create a strong bond. To excel in welding, one must possess a combination of technical knowledge, practical skills, and a commitment to safety. This article explores the essential skills required for welding, offering an in-depth understanding of what it takes to become a proficient welder.
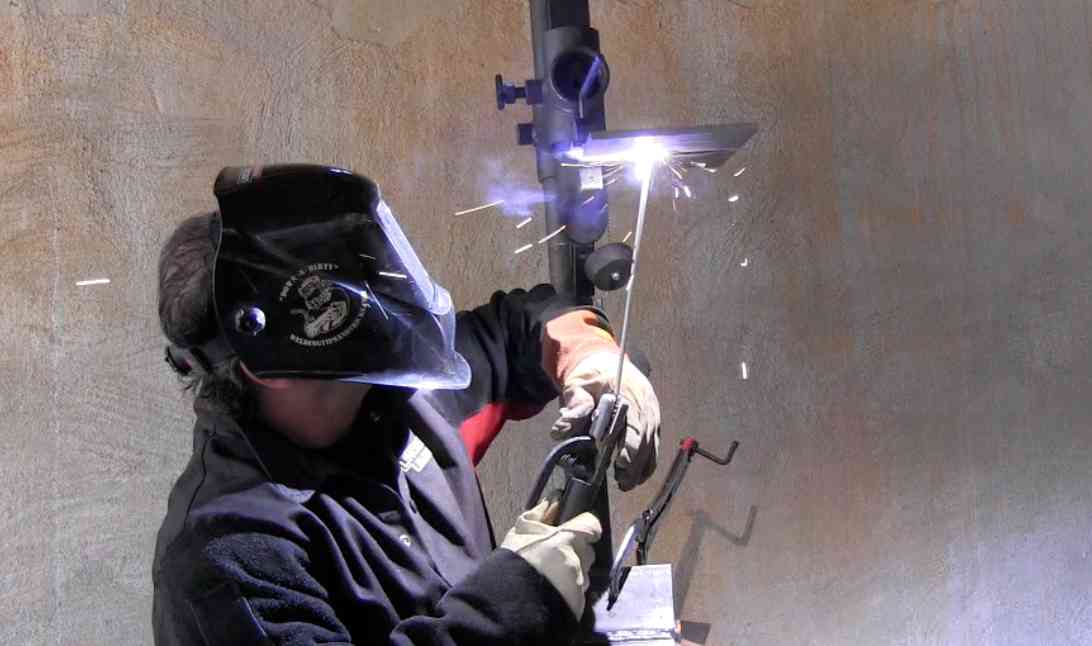
1. Understanding Different Welding Processes
- MIG Welding (Metal Inert Gas)
Overview: Metal Inert Gas (MIG) welding, also known as Gas Metal Arc Welding (GMAW), is one of the most common welding processes. It uses a continuously fed wire electrode and shielding gas to protect the weld from contaminants.
Skills Required: MIG welding requires precision in controlling the feed rate of the wire, the flow of shielding gas, and the welding current. Welders must be adept at adjusting these parameters based on the material and thickness being welded. Knowledge of the correct wire type, gas mixture, and technique is essential for producing strong, clean welds.
Applications: MIG welding is widely used in the automotive industry, metal fabrication, and construction due to its speed and ease of automation.
- TIG Welding (Tungsten Inert Gas)
Overview: Tungsten Inert Gas (TIG) welding, or Gas Tungsten Arc Welding (GTAW), is known for its precision and ability to produce high-quality welds. It uses a non-consumable tungsten electrode and an inert gas shield, usually argon.
Skills Required: TIG welding demands a high level of skill, particularly in hand-eye coordination and manual dexterity. Welders must control the torch in one hand while feeding the filler material with the other, all while maintaining a steady arc. Mastery of TIG welding involves understanding how to manipulate the heat input and welding speed to achieve clean, defect-free welds.
Applications: TIG welding is ideal for welding thin materials, such as stainless steel and aluminum, and is commonly used in aerospace, motorsports, and piping systems.
Stick Welding (Shielded Metal Arc Welding – SMAW)
Overview: Stick welding, or Shielded Metal Arc Welding (SMAW), is a versatile process that uses a consumable electrode coated in flux. The flux creates a protective gas shield during welding, making it suitable for outdoor and adverse conditions.
Skills Required: Stick welding requires a good understanding of electrode selection, arc control, and technique. Welders must be able to strike and maintain an arc, manage slag, and work in various positions. Knowledge of different electrodes and their applications is crucial for achieving strong welds in different environments.
Applications: Stick welding is commonly used in construction, maintenance, and repair work, particularly for structural steel, pipelines, and heavy equipment.
Flux-Cored Arc Welding (FCAW)
Overview: Flux-Cored Arc Welding (FCAW) is similar to MIG welding but uses a tubular wire filled with flux. This process can be used with or without an external shielding gas, depending on the application.
Skills Required: Welders must understand the differences between gas-shielded and self-shielded FCAW and how to adjust settings accordingly. This process requires skill in managing spatter and slag, and ensuring proper penetration and fusion.
Applications: FCAW is often used in construction, shipbuilding, and heavy manufacturing due to its ability to weld thicker materials at high speeds.
Oxy-Acetylene Welding (Gas Welding)
Overview: Oxy-Acetylene welding is a traditional welding process that uses a flame produced by burning acetylene with oxygen. It is less common in industrial applications today but is still valuable for certain tasks.
Skills Required: Mastery of gas welding involves controlling the flame and heat input to achieve proper fusion without overheating the material. Welders need to be proficient in selecting the correct tip size and flame settings for different materials.
Applications: Oxy-Acetylene welding is often used in repair work, artistic metalwork, and situations where portability and flexibility are important.
2. Metal Preparation
Surface Cleaning
Overview: Proper surface preparation is essential for achieving a clean, strong weld. Contaminants like rust, paint, oil, and dirt can lead to weak welds and defects.
Skills Required: Welders must know how to effectively clean and prepare metal surfaces using tools like wire brushes, grinders, and chemical cleaners. Understanding when and how to use each tool is crucial for ensuring that the base metal is ready for welding.
Importance: Clean metal surfaces lead to better fusion and prevent defects such as porosity, cracking, and lack of fusion.
Cutting and Shaping
Overview: Before welding, metal often needs to be cut and shaped to the correct dimensions. This step is crucial for ensuring proper fit-up and joint alignment.
Skills Required: Proficiency in using cutting tools such as oxy-fuel torches, plasma cutters, and angle grinders is essential. Welders must also understand how to create accurate cuts and shapes to ensure that the pieces fit together correctly.
Applications: Cutting and shaping are required in almost every welding project, from small repairs to large-scale fabrication.
Beveling
Overview: Beveling involves creating an angled edge on the metal pieces to allow for deeper penetration during welding. This technique is commonly used in thicker materials to ensure a strong weld joint.
Skills Required: Welders must be skilled in using beveling tools and understand the appropriate bevel angle for different materials and thicknesses. Proper beveling helps in achieving full penetration welds, which are stronger and more reliable.
Applications: Beveling is often used in pipe welding, structural welding, and situations where the strength of the weld is critical.
3. Joint Preparation
Types of Joints
Overview: Different welding projects require different types of joints, each with its own set of challenges and techniques. Common joint types include butt joints, lap joints, corner joints, T-joints, and edge joints.
Skills Required: Welders must understand the strengths and weaknesses of each joint type and be able to select the appropriate joint for the specific application. Knowledge of joint preparation techniques, such as gap spacing and tack welding, is essential for achieving a strong, reliable weld.
Applications: Joint preparation is critical in all welding projects, from simple repairs to complex fabrication tasks.
Fitting and Clamping
Overview: Proper alignment and fit-up of the metal pieces before welding are crucial for achieving accurate and strong welds. Clamping helps to hold the pieces in place during welding.
Skills Required: Welders need to be proficient in using clamps, fixtures, and jigs to hold metal pieces in the correct position. Understanding how to achieve proper alignment and prevent distortion during welding is key to producing high-quality welds.
Applications: Fitting and clamping are used in various welding projects, from small assemblies to large structural components.
4. Welding Technique
Controlling Heat
Overview: Managing the heat input during welding is critical to preventing defects such as warping, burn-through, and cracking. Different materials and thicknesses require different heat levels.
Skills Required: Welders must be skilled in adjusting the welding machine settings to control the heat input. This involves understanding the relationship between voltage, amperage, and travel speed. Proper heat control ensures that the weld penetrates the material without causing damage.
Applications: Heat control is important in all welding processes and applications, particularly when working with thin materials or heat-sensitive metals.
Puddle Control
Overview: The weld puddle, or molten pool, must be carefully controlled to ensure a consistent weld bead. Proper puddle control leads to strong, defect-free welds.
Skills Required: Welders must develop the ability to manage the size, shape, and movement of the weld puddle. This skill requires practice and experience, as different welding positions and materials affect puddle behavior.
Applications: Puddle control is a fundamental skill in all welding processes, from MIG and TIG to stick and flux-cored welding.
Weaving and Stringer Bead
Overview: Weaving and stringer beads are techniques used to control the width and penetration of the weld bead. Stringer beads are straight, while weaving involves a side-to-side motion.
Skills Required: Welders must understand when to use stringer beads or weaving techniques based on the application and material thickness. Proper technique ensures that the weld bead is uniform, penetrates adequately, and covers the joint fully.
Applications: These techniques are used in various welding processes, particularly when welding thicker materials or in challenging positions.
5. Post-Weld Inspection and Finishing
Visual Inspection
Overview: After welding, the welds must be inspected for defects such as cracks, porosity, undercutting, and incomplete fusion. Visual inspection is the first step in quality control.
Skills Required: Welders must be trained to recognize common welding defects and understand their causes. This skill involves attention to detail and a thorough understanding of welding standards and codes.
Applications: Visual inspection is used in all welding projects, from small repairs to large-scale fabrication, to ensure that the welds meet the required standards.
Grinding and Smoothing
Overview: Post-weld finishing often involves grinding and smoothing the welds to achieve the desired appearance and function. This step is crucial in applications where aesthetics or precise dimensions are important.
Skills Required: Welders must be skilled in using grinders, files, and other finishing tools. Understanding how to blend welds with the surrounding material without compromising the strength of the weld is essential.
Applications: Finishing is commonly required in industries such as automotive, aerospace, and metal fabrication, where the appearance and function of the weld are critical.
Stress Relief and Heat Treatment
Overview: Welding can introduce residual stresses into the material, leading to potential failure. Stress relief and heat treatment are processes used to reduce these stresses and improve the weld’s performance.
Skills Required: Welders must understand the principles of stress relief and heat treatment, including the appropriate temperatures and cooling rates for different materials. This knowledge ensures that the welds maintain their strength and integrity over time.
Applications: Stress relief and heat treatment are particularly important in critical applications, such as pressure vessels, pipelines, and structural components.
6. Safety Practices
Protective Gear
Overview: Welding involves exposure to high temperatures, sparks, UV radiation, and harmful fumes. Proper protective gear is essential for the safety of the welder.
Skills Required: Welders must be knowledgeable about the different types of protective gear, including welding helmets, gloves, jackets, and respirators. Understanding the correct usage and maintenance of this gear is crucial for preventing injuries.
Applications: Safety practices are critical in all welding environments, from small workshops to large industrial sites.
Ventilation
Overview: Welding generates hazardous fumes and gases, making proper ventilation essential for the welder’s health. Ventilation systems help to remove these fumes from the workspace.
Skills Required: Welders must understand the importance of ventilation and how to set up and maintain ventilation systems. Knowledge of different ventilation methods, such as local exhaust ventilation and general shop ventilation, is important for ensuring a safe working environment.
Applications: Proper ventilation is necessary in all welding environments, particularly in enclosed spaces or when working with materials that produce toxic fumes.
Fire Safety
Overview: Welding poses a significant fire hazard due to the high temperatures and sparks generated during the process. Fire safety measures are essential to prevent accidents.
Skills Required: Welders must be trained in fire safety practices, including the proper use of fire extinguishers, the importance of keeping flammable materials away from the welding area, and the procedures for responding to a fire emergency. Knowledge of fire prevention measures, such as using fire-resistant barriers and maintaining a clean work area, is also crucial.
Applications: Fire safety practices are essential in all welding environments, particularly in areas where flammable materials are present.
7. Problem-Solving
Troubleshooting Defects
Overview: Welding defects can occur due to various factors, including improper technique, material contamination, and equipment malfunctions. Troubleshooting these defects is crucial for producing high-quality welds.
Skills Required: Welders must be skilled in identifying and diagnosing common welding defects, such as cracks, porosity, and lack of fusion. This involves understanding the root causes of these defects and knowing how to adjust the welding parameters, materials, or techniques to correct them.
Applications: Troubleshooting is an essential skill in all welding projects, from small repairs to large-scale fabrication, ensuring that the welds meet the required quality standards.
Adapting Techniques
Overview: Welding often involves working with different materials, thicknesses, and positions. Adapting techniques to suit the specific requirements of each job is crucial for achieving strong, reliable welds.
Skills Required: Welders must be versatile and able to adjust their techniques based on the material type, thickness, and welding position. This includes understanding how to modify the welding parameters, such as voltage, amperage, and travel speed, to achieve the best results.
Applications: Adaptability is important in all welding projects, particularly in industries that require working with a variety of materials and complex assemblies.
8. Blueprint Reading
Interpreting Weld Symbols
Overview: Welding blueprints and drawings contain specific symbols and instructions that indicate the type of weld, size, and other important details. Understanding these symbols is essential for executing the weld correctly.
Skills Required: Welders must be proficient in reading and interpreting welding symbols and blueprints. This involves understanding the various symbols used to represent different weld types, joint configurations, and dimensions. Knowledge of industry standards for weld symbols is also important.
Applications: Blueprint reading is essential in industries such as construction, manufacturing, and aerospace, where precision and accuracy are critical.
Measurement and Layout
Overview: Accurate measurement and layout are crucial for ensuring that the welded components fit together correctly and meet the required specifications.
Skills Required: Welders must be skilled in using measurement tools, such as rulers, calipers, and tape measures, to accurately mark and measure materials. Understanding how to create accurate layouts and ensure proper alignment is key to achieving precise welds.
Applications: Measurement and layout are important in all welding projects, from simple assemblies to complex structures.
9. Equipment Maintenance
Routine Checks
Overview: Welding equipment requires regular maintenance to ensure it operates safely and efficiently. Routine checks help to identify potential issues before they become serious problems.
Skills Required: Welders must be knowledgeable about the maintenance requirements of their equipment, including how to perform routine checks on welding machines, cables, and accessories. This includes understanding how to inspect for wear and tear, clean the equipment, and replace consumable parts as needed.
Applications: Equipment maintenance is critical in all welding environments, ensuring that the tools and machines operate at peak performance and reduce the risk of equipment failure.
Calibration
Overview: Welding machines must be calibrated to ensure that they deliver the correct voltage, amperage, and wire feed speed. Calibration is important for producing consistent, high-quality welds.
Skills Required: Welders must be skilled in calibrating their welding machines to match the specific requirements of the job. This involves understanding how to adjust the machine settings and perform test welds to verify the calibration.
Applications: Calibration is essential in industries that require precise and consistent welds, such as aerospace, automotive, and high-pressure systems.
10. Continuous Learning
Staying Updated
Overview: The welding industry is constantly evolving, with new techniques, materials, and technologies being introduced. Staying updated on these developments is crucial for maintaining and improving welding skills.
Skills Required: Welders must be committed to continuous learning, which involves attending training sessions, workshops, and industry conferences. Staying informed about the latest advancements in welding technology and materials is essential for staying competitive in the field.
Applications: Continuous learning is important for all welders, regardless of experience level, as it ensures that they remain proficient in the latest techniques and best practices.
Certification
Overview: Welding certifications, such as those offered by the American Welding Society (AWS), validate a welder’s skills and knowledge. Obtaining and maintaining these certifications is important for career advancement and credibility in the industry.
Skills Required: Welders must be prepared to pass certification exams, which typically involve both written and practical tests. This requires a thorough understanding of welding principles, techniques, and safety practices. Continuing education and recertification are also important for keeping skills up to date.
Applications: Certification is often required in industries such as construction, manufacturing, and aerospace, where weld quality and safety are paramount.
Conclusion
Welding is a highly skilled trade that requires a deep understanding of various processes, techniques, and safety practices. From mastering different welding methods like MIG, TIG, and Stick welding to ensuring proper metal preparation, joint fit-up, and post-weld inspection, welders must possess a diverse set of skills. Continuous learning and staying updated on industry advancements are also essential for maintaining proficiency and advancing in the welding profession. Whether you’re a beginner or an experienced welder, developing and honing these skills is crucial for achieving success in the field of welding.