What is Induction Welding?
Introduction
Welding Induction welding is a welding technique that utilizes electromagnetic induction to generate heat and join metal components. It is a solid-state welding process where the workpieces are heated locally without the need for an external heat source, such as a flame or electrical arc. The heat is generated by inducing electrical currents in the workpieces using high-frequency alternating current (AC).
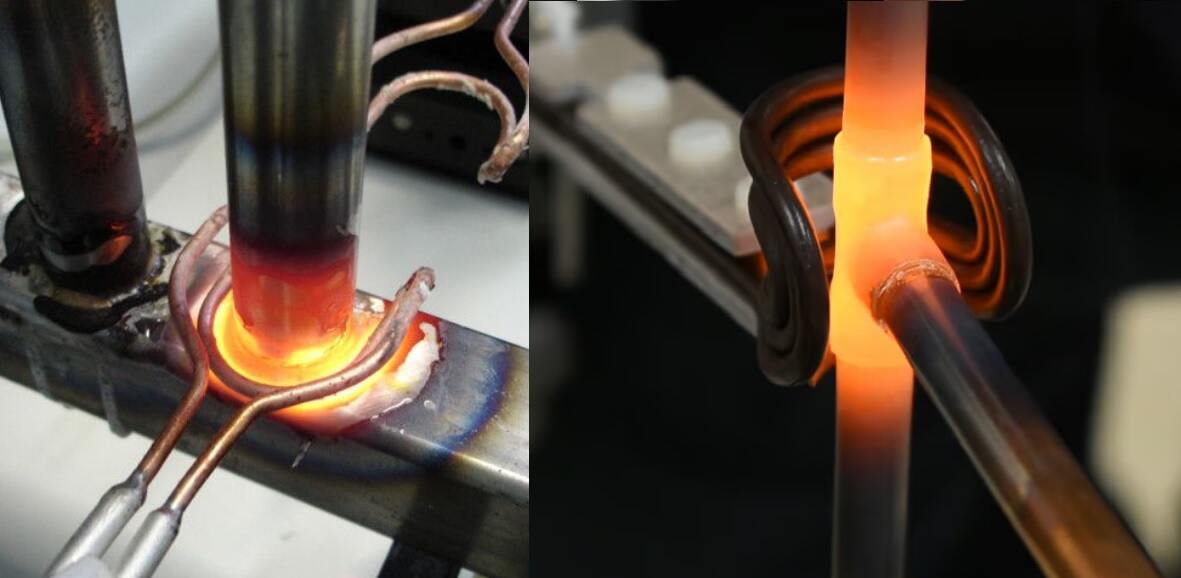
Induction welding has gained prominence in various industries due to its unique advantages and wide range of applications. Some notable points include:
- Automotive Industry: Induction welding is extensively used in the automotive industry for joining components such as exhaust systems, fuel tanks, and engine parts. It offers fast and reliable joining, ensuring strong and leak-free connections.
- Aerospace and Aviation Sector: Induction welding finds applications in the aerospace and aviation sector for joining critical components like turbine blades, engine components, and structural parts. It provides precise and repeatable welding results, meeting stringent quality standards.
- Metal Fabrication and Manufacturing: Induction welding is employed in metal fabrication and manufacturing processes, including the production of pipes, tubes, and other metal structures. It enables efficient and high-speed welding, improving productivity and reducing production costs.
- Pipe and Tube Welding: Induction welding is widely used for pipe and tube welding applications, such as in the oil and gas industry. It allows for continuous and high-quality welding of longitudinally welded pipes and tubes.
- Other Industrial Sectors: Induction welding finds applications in various other industries, including electrical and electronics manufacturing, power generation, heat exchanger fabrication, and more. It offers versatility in joining different types of metals and provides consistent and reliable weld quality.
The advantages of induction welding include:
- Rapid and localized heating: Induction welding provides fast and localized heating, allowing for precise control over the heat-affected zone and minimizing thermal distortion.
- Non-contact heating process: The absence of direct contact between the heat source and the workpieces reduces the risk of contamination and allows for the joining of delicate or heat-sensitive components.
- High energy efficiency and precise control: Induction welding is energy-efficient as it directly heats the workpieces without wasting energy on heating surrounding areas. The process offers precise control over heating parameters, resulting in consistent and repeatable welding results.
- Versatility in joining various materials: Induction welding can be used to join a wide range of metals, including ferrous and non-ferrous materials, offering flexibility in material selection for different applications.
Principle of Induction Welding
Explanation of the basic principle
Induction welding operates on the principle of electromagnetic induction, which involves the generation of heat by inducing electrical currents in conductive materials. The basic principle of induction welding can be summarized as follows:
- The workpieces to be welded are placed in close proximity to each other, forming a joint interface.
- An induction coil, typically made of copper or another conductive material, is wrapped around one of the workpieces or positioned adjacent to the joint area.
- High-frequency alternating current (AC) is passed through the induction coil, creating a rapidly changing magnetic field around it.
- The alternating magnetic field induces electrical currents, known as eddy currents, in the conductive workpiece(s) placed within the magnetic field.
- The eddy currents generate resistive heating in the workpieces due to the electrical resistance encountered as the currents flow through the conductive material.
- The resistive heating raises the temperature of the workpieces at the joint interface, causing the material to soften and eventually melt.
- Pressure is applied to the softened material, forging a bond between the workpieces as they cool and solidify.
Description of the equipment and components used
The equipment and components used in induction welding typically include:
- Induction Coil: The induction coil is a key component that generates the rapidly changing magnetic field when energized with high-frequency AC. It is usually made of a conductive material, such as copper, and is designed to fit around or near the joint area.
- Power Supply: The power supply provides the high-frequency alternating current needed to energize the induction coil. It generates the required electrical energy and controls the frequency, power output, and other parameters of the welding process.
- Workpiece Fixturing: Fixturing components, such as clamps or jigs, are used to hold the workpieces securely in place during the welding process. They ensure proper alignment and positioning to achieve the desired weld joint.
- Cooling System: In some cases, a cooling system is employed to remove excess heat and cool the workpieces after the welding phase. This helps in solidifying the weld and achieving the desired metallurgical properties.
Role of electromagnetic induction in the process
Electromagnetic induction is the fundamental principle behind induction welding. When the high-frequency alternating current passes through the induction coil, it creates a rapidly changing magnetic field. This magnetic field induces electrical currents, or eddy currents, in the conductive workpieces placed within the magnetic field. These eddy currents generate resistive heating due to the electrical resistance encountered in the workpieces, resulting in localized heating at the joint interface. The heat generated by electromagnetic induction softens and melts the material, enabling the formation of a strong bond when pressure is applied. The use of electromagnetic induction allows for precise and efficient heating, with minimal energy loss to surrounding areas, facilitating the welding of conductive materials in a controlled and effective manner.
Process Steps
Pre-welding Preparation
- Selection of suitable materials for induction welding: Induction welding is primarily used for joining conductive materials, such as various metals and alloys. The materials selected should have sufficient electrical conductivity to allow for the generation of eddy currents and subsequent heating during the process.
- Surface preparation and cleaning of workpieces: Prior to welding, the surfaces of the workpieces need to be prepared and cleaned. This typically involves removing any contaminants, such as dirt, grease, or oxide layers, that may hinder proper bonding. Surface preparation methods may include grinding, sanding, or chemical cleaning.
- Fixturing and alignment of the components: The workpieces are securely fixed and aligned using fixtures, clamps, or other means. Proper alignment ensures that the joint interface is accurately positioned for effective heat transfer and optimal weld quality. Fixturing also helps maintain stability and alignment during the welding process.
Heating Phase
- Activation of the equipment and setup of welding parameters: The induction welding equipment is activated, and the necessary parameters are set. This includes adjusting the power output, frequency, and other relevant parameters based on the material being welded and desired welding conditions.
- Introduction of high-frequency alternating current (AC): The high-frequency alternating current is supplied to the induction coil, which generates the rapidly changing magnetic field. This current induces eddy currents in the conductive workpieces positioned within the magnetic field.
- Electromagnetic induction and heating of the workpieces: The induction coil generates the alternating magnetic field, which induces eddy currents in the workpieces. These eddy currents encounter electrical resistance within the material, leading to resistive heating. The heat generated softens the material at the joint interface, preparing it for the welding phase.
Welding Phase
- Control and monitoring of heating time and temperature: The heating time and temperature are carefully controlled and monitored during the welding phase. Precise control ensures proper heating of the joint interface while minimizing heat-affected zones and potential material distortion.
- Application of pressure to create a weld: Once the desired temperature is reached, pressure is applied to the softened material at the joint interface. The pressure facilitates material flow and intimate contact between the workpieces, ensuring proper bonding. The pressure is maintained until the weld solidifies.
- Cooling and solidification of the welded joint: After the pressure is applied, the cooling phase begins. The joint is allowed to cool and solidify, forming a strong metallurgical bond between the workpieces. Controlled cooling helps ensure proper solidification and desirable mechanical properties.
Post-welding
- Inspection and testing of the weld quality: The welded joint undergoes inspection and testing to assess its quality and integrity. Various methods, such as visual inspection, non-destructive testing, or mechanical testing, may be employed to verify the strength and reliability of the weld.
- Post-weld processing or finishing: Depending on the specific application or desired aesthetics, post-weld processing or finishing may be performed. This can include processes such as grinding, polishing, or surface treatment to achieve the desired final appearance and functionality of the welded components.
Advantages and Limitations
Advantages of Induction Welding
- Rapid and localized heating: Induction welding offers rapid heating capabilities, allowing for faster welding cycles compared to other methods. The induction heating process delivers heat directly to the workpiece, resulting in localized heating at the desired joint area.
- Non-contact heating process: Induction welding is a non-contact heating process, meaning that the heat is generated without physical contact between the heat source and the workpieces. This eliminates the risk of contamination or damage to the surfaces being welded, particularly when working with delicate or sensitive materials.
- High energy efficiency and precise control: Induction welding is known for its high energy efficiency since the heat is generated directly in the workpieces, minimizing energy loss to the surrounding environment. It also offers precise control over heating parameters, such as power output and duration, allowing for consistent and repeatable weld quality.
- Versatility in joining various materials: Induction welding has the capability to join a wide range of conductive materials, including ferrous and non-ferrous metals and alloys. It provides flexibility in material selection, making it suitable for diverse applications across different industries.
Limitations and Considerations
- Material compatibility and electrical conductivity: Induction welding requires the workpieces to be conductive to facilitate the generation of eddy currents and subsequent heating. Some non-conductive materials, such as ceramics or certain plastics, cannot be effectively joined using induction welding.
- Surface finish and cleanliness requirements: Proper surface preparation is critical for successful induction welding. The workpiece surfaces should be clean and free from contaminants, such as oil, grease, or oxide layers, to ensure optimal heat transfer and bonding. Surface roughness or irregularities can affect the quality of the weld.
- Equipment cost and complexity: The equipment required for induction welding can be relatively expensive compared to some other welding methods. It involves specialized power supplies, induction coils, and cooling systems. Additionally, the setup and operation of the equipment may require training and expertise, adding to the complexity of the process.
Applications of Induction Welding
Automotive Industry
Induction welding finds extensive application in the automotive industry for joining various components. Some notable examples include:
- Engine components: Induction welding is used for joining engine components such as crankshafts, camshafts, and connecting rods, ensuring reliable and durable connections.
- Transmission systems: Induction welding is employed for joining gears, shafts, and other transmission components, providing strong and precise assemblies.
- Exhaust systems: Induction welding is used for joining exhaust pipes, mufflers, and catalytic converters, ensuring leak-free and high-strength connections.
Aerospace and Aviation Sector
Induction welding plays a crucial role in the aerospace and aviation sector, where high-quality and reliable connections are essential. Some applications include:
- Turbine components: Induction welding is used for joining turbine blades, vanes, and other critical components in gas turbines, ensuring secure and high-integrity assemblies.
- Structural components: Induction welding is employed for joining structural components of aircraft, such as fuselage sections, wings, and landing gear components, providing strong and lightweight structures.
- Heat exchangers: Induction welding is utilized for joining heat exchanger tubes and fins, ensuring efficient heat transfer and optimal performance.
Metal Fabrication and Manufacturing
Induction welding is widely used in metal fabrication and manufacturing processes. Some applications include:
- Sheet metal assemblies: Induction welding is employed for joining sheet metal components in industries such as appliance manufacturing, HVAC systems, and general metal fabrication.
- Tool and die making: Induction welding is used for joining tooling components and dies, providing strong and precise assemblies for various manufacturing processes.
- Pipelines and tanks: Induction welding is utilized for joining metal pipelines, tanks, and vessels, ensuring reliable and leak-free connections in industries such as oil and gas, petrochemical, and water treatment.
Pipe and Tube Welding
Induction welding is extensively used in pipe and tube manufacturing processes. Some applications include:
- Longitudinal pipe welding: Induction welding is employed for welding longitudinal seams in pipes, ensuring continuous and high-quality welds in industries such as oil and gas, construction, and infrastructure.
- Tube welding: Induction welding is used for joining tubes, including heat exchanger tubes, boiler tubes, and automotive tubes, providing efficient and precise welds.
- Pipe and tube fittings: Induction welding is utilized for joining pipe and tube fittings, ensuring secure and reliable connections in plumbing, irrigation, and hydraulic systems.
Other Industrial Sectors
Induction welding has applications in various other industrial sectors, including:
- Power generation: Induction welding is used for joining components in power generation equipment such as generators, transformers, and turbines.
- Electrical and electronics manufacturing: Induction welding finds application in joining electrical conductors, busbars, and electrical connectors.
- Rail and transportation: Induction welding is employed for joining rail components, including tracks, rails, and train carriages, ensuring strong and durable connections.
- Renewable energy: Induction welding is utilized in the fabrication of components for renewable energy systems such as wind turbines, solar panels, and battery systems.
FAQs
What do you mean by induction welding?
Induction welding refers to a welding technique that uses electromagnetic induction to generate heat and join metal components. It involves the induction of electrical currents, known as eddy currents, in conductive materials, which then produce resistive heating and facilitate the bonding of the workpieces.
What is the principle of induction welding?
The principle of induction welding is based on electromagnetic induction. It involves passing high-frequency alternating current through an induction coil, which creates a rapidly changing magnetic field. This magnetic field induces electrical currents, or eddy currents, in the conductive workpieces. The resistive heating generated by these eddy currents softens the material, allowing for welding under pressure.
What are the disadvantages of induction welding?
Some disadvantages of induction welding include:
- Limited applicability to conductive materials: Induction welding is primarily suitable for joining conductive materials and may not be effective for non-conductive or low-conductivity materials.
- Surface preparation requirements: Proper surface preparation and cleanliness are crucial for successful induction welding, which can be time-consuming and may require additional steps.
- Equipment complexity and cost: Induction welding equipment can be relatively expensive and may require specialized knowledge for operation and maintenance.
What is induction welding of plastic?
Induction welding of plastic involves using electromagnetic induction to heat thermoplastic materials for the purpose of joining them. The process relies on the induction of electrical currents in conductive additives or coatings within the plastic material, generating heat and enabling the fusion of the thermoplastic components.
Why is it called induction?
Induction welding is called so because it relies on the principle of electromagnetic induction. The term “induction” refers to the process of inducing electrical currents, known as eddy currents, within conductive materials by means of a rapidly changing magnetic field.
What is induction and its process?
Induction is the process of generating electrical currents within conductive materials through electromagnetic induction. It involves passing high-frequency alternating current through an induction coil, which creates a rapidly changing magnetic field. This magnetic field induces eddy currents in the conductive materials, leading to resistive heating and subsequent bonding in the case of induction welding.
What is the temperature of induction welding?
The temperature of induction welding can vary depending on the materials being welded and the specific process parameters. Generally, temperatures within the range of 200°C to 1200°C (392°F to 2192°F) can be achieved during induction welding.
What is the advantage of induction welding?
Some advantages of induction welding include:
- Rapid and localized heating: Induction welding offers fast and precise heating, minimizing the heat-affected zone and reducing the risk of distortion.
- Energy efficiency: The heat is generated directly within the workpieces, resulting in high energy efficiency compared to other welding processes.
- Versatility in material compatibility: Induction welding can be applied to various conductive materials, allowing for versatile applications in different industries.
How many welding types are there?
There are numerous welding types available, including but not limited to arc welding, gas welding, resistance welding, laser welding, electron beam welding, friction welding, and induction welding. The specific welding type chosen depends on the materials being joined, process requirements, and desired weld characteristics.
Where is induction welding used?
Induction welding is used in various industries, including automotive, aerospace, metal fabrication, pipe and tube manufacturing, and electrical and electronics manufacturing. It finds applications in joining components such as engine parts, transmission systems, structural components, pipes, and heat exchangers.
Conclusion
In conclusion, induction welding is a highly efficient and versatile welding technique that offers numerous advantages in various industries. By utilizing electromagnetic induction, this process generates localized heat in a fast and precise manner, resulting in strong and reliable welds. One of the key benefits of induction welding is its ability to join dissimilar materials, including metals and thermoplastics, overcoming the limitations of conventional welding methods. This opens up new possibilities for designing and manufacturing complex structures and components, enabling the production of lightweight and durable products.
Induction welding also offers improved process control and automation capabilities. The non-contact nature of the induction heating process allows for precise heat application, minimizing the risk of damage to surrounding areas. Additionally, the rapid heating and cooling cycles reduce the overall processing time and increase production efficiency. Another advantage of induction welding is its eco-friendliness. Compared to traditional welding techniques, it produces minimal fumes, emissions, and waste, contributing to a cleaner and safer working environment. This aligns with the growing focus on sustainability and environmental responsibility in modern industries.
While induction welding has proven its effectiveness in various applications, it is essential to consider factors such as material compatibility, design considerations, and equipment selection to ensure optimal results. Additionally, ongoing advancements in induction welding technology, such as improved power supplies and control systems, continue to enhance the process’s capabilities and expand its applications further.