Arc Welding
Introduction
Arc welding is a method of joining two or more metal parts together by using an electric arc to heat the surfaces to be joined. The electric arc is created between an electrode and the workpiece, which melts the metal and forms a weld pool. The weld pool solidifies as the metal cools, creating a strong bond between the parts. Arc welding is a versatile method of welding that can be used on a wide range of materials, including aluminum, stainless steel, and cast iron. It is commonly used in the construction of buildings, bridges, and other structures, as well as in the manufacturing of machinery, vehicles, and other equipment.
Arc Welding Process
Arc welding is a type of welding process that uses electric arc to produce an extreme heat to create a weld. Arc welding may also use filler metal for creating weld. Arc welding is popular among other types of welding because of many reasons like; its equipment is low-cost, portable and flexible in use. The discovery of electric arc was done in early eighties. According to Davies, the welding using carbon electrode was discovered in 1886. According to Kjellberg, the first covered electrode came into being in 1900. And in 1940s, the first process using a continuously feed electrode was discovered.
According to American Welding Society (AWS), the terminologies are given to the welding processes abbreviations. Shielded Metal Arc Welding (SMAW), Gas Metal Arc Welding (GMAW), Gas Tungsten Arc Welding (GTAW), Plasma Arc Welding (PAW), Submerged Arc Welding (SAW), Flux Cored Arc Welding (FCAW), Arc Stud Welding (SW), and Electro gas Welding (EGW). Electro-slag Welding (ESW) is technically not an arc welding process, but this process has some similarities to EGW that’s why sometimes it is included in list of arc welding processes. Some processes are represented by italic names like Metal Inert Gas (MIG) for GMAW, and Tungsten Inert Gas (TIG) for GTAW and Stick or Covered Electrode welding for SMAW. Where, IG represents “inert gas”, as inert gasses are used in these processes for shielding. In all the arc welding processes, the initiation of an arc, provides a closed circuit i.e., completes the circuit.
A basic arc welding process consists of a power supply, electrode and leads or cables that are to be connected to the electrode and welding pieces that are to be joined. Arc welding requires maximum of 60 volts – 80 volts of power supply at open circuit (when there is no arc). At these voltages, there is possibility to establish and maintain the arc with less risk of electrical shock. Once the arc is established it requires voltage 10 volts – 40 volts. Welding power supplies are specially designed to supply direct current (DC) electricity. Many advanced welding power supplies provides a pulsing output also called pulsed DC. To optimize the welding performance, Programmable pulsing parameters/schedules can be used. It is mostly used in GMAW. Sometimes alternating current (AC) is used it has advantage that it is simple and cheap. Welding with AC is mostly used to weld the aluminum. Sometimes variable polarity is used in power supplies; it is used to optimize the welding performance.
Principle of Arc Welding
The principle of arc welding is based on the use of an electric arc to generate heat, which melts the ends of two pieces of metal and fuses them together. The electric arc is created by an electrical current flowing through a gap between the two pieces of metal, called the electrode and the workpiece. This arc generates heat, which melts the metal and creates a pool of molten metal. As the electrode is moved along the workpiece, the molten metal is deposited, creating a strong bond between the two pieces of metal. The heat and pressure from the arc also help to remove any contaminants or impurities from the surface of the metal, ensuring a strong and clean weld.
Components Involved in Arc Welding
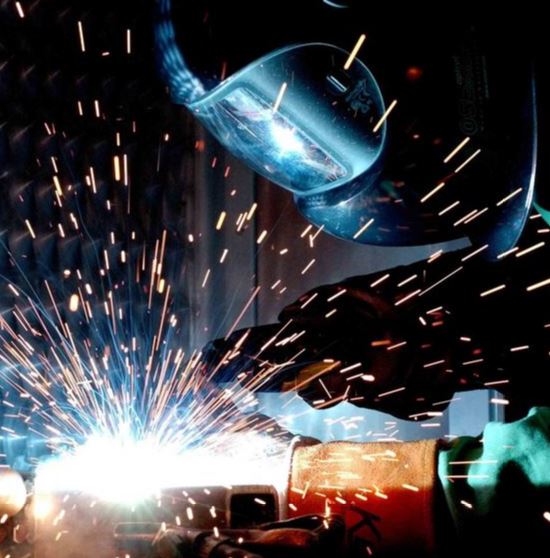
Electric Arc
Electric arc is electrical discharge between electrodes, when a sufficient voltage is applied across the gap; as a result the gas gets ionized. Gas when ionized it changes from insulator to conductor and conducts electricity. Ionization process occurs when the electrons in the gas are loosely bond and are free to move in the gas to produce an electric current. The free moving electrons get energy from electric field produced by applied voltage and collide with other gas atoms resulting in avalanche effect. When the gas is highly ionized, electrons travel easily and under standard condition electric arc is formed. Ionized gas has electrons that flow in one direction and positive charged ions move in other direction. Mostly collisions of ions with neutral atoms produce highly resistive heating of gas this makes sense that arc is a high resistor. This heat maintains the ionization. Electromagnetic (EM) radiations emitted because of extreme heat resulting characteristic glow of electrical arc produced. As a result of this, visible light, infrared (IR) and ultraviolet (UV) wavelengths are also emitted. The ionized glowing gas is called “plasma”. The arc required high current and low voltage power supply. The use of electric arc in welding process is to provide extreme heat that melts the weld pool/puddle. The arc temperature is high ranging from 5K to 30000K.
Arc Voltage
Arc voltage is the potential difference between electrode and weld pieces. It is important factor, as voltage (potential difference) varies through the arc. The arc voltages are directly related to arc lengths. The arc with longer lengths produce higher arc volt and[1]arc with shorter arc length produce lower voltages. Arc with high voltage can produce more heat than required and may lead to warping or melting of the metal. Arc with low voltage can produce less or no heat than required amount and may lead to damaging. The ideal voltage is that which creates the balance between the two extremes that will produce strong and best result welding. In most welding processes, the ideal arc voltages ranges from 10 –40 volts.
Polarity
In arc welding process, the electrical polarity applied to the arc through the power supply. The polarity does matters a lot in welding process. Choosing right polarity is important as it strengthens the quality of welding otherwise with opposite polarity there would be defects in welding like spatter, bad penetration, and a lack of control on welding arc. The positive part of welding circuit is called as anode and negative side is called as cathode. In electrical convention the current flows from positive to negative while in literature the current flows from negative end to positive end. In both cases, for a welding arc, electrons flow from cathode to anode, but it has different effects in different processes. In arc welding, when the electrode acted as cathode and the weld piece as anode, this is called DCEN (DC electrode negative) or DC straight polarity. In this way the electrons flow from welding electrode, to the weld piece through the arc. And when the electrode acted as anode relative to the weld metal, it is called DCEP (DC electrode positive) or DC reverse polarity. And in case of alternating current (AC) and variable polarity, the polarity and direction of electron flow always alternate each other. The effect of polarity affects the whole process and the characteristics of the material being welded.
Heat Input
In arc welding, heat input or energy is an important requirement. The heat input in arc welding is expressed as energy per unit length. This is a direct function of of voltage, current, and weld travel speed.
Welding Position
Welding position is an arrangement in which the weld joint is placed in space relative to the welder (one who is performing the welding task). The position may vary based on the type of welding. Most common is flat position in which the weld joint are placed flat and the molten weld pool is held in the joint by gravity. This is usually the easiest position for welding but many other positions to work, depending on the weld joints. The most difficult and opposite one is an overhead position, in which the molten metal is held solely by its surface tension. Overhead position welding is very difficult to perform and requires significant welder skill and expertise.
Electrodes and Filler Metals
There are many types of filler metals and electrodes for different materials, arc welding processes, and based on their applications. Some electrodes are consumable, as they melt from the arc and become the part of weld metal. It is called electrode because it is carrying the current to the arc. While the filler metal in case of GTAW and PAW are not considered as electrode as they don’t carry the current to the arc and the current is carried through consumable tungsten electrode.
Shielding
When metals are heated at high temperature they are more susceptible to reaction with atmospheric gases like, oxygen, nitrogen, and hydrogen. These reactions could cause contamination. Such contamination results in fusion defects, porosity, and weld metal embrittlement. In order to avoid such contamination, the metals are be shielded with some inert gases, as a result it solidifies and begins to cool. The arc welding processes are dependent on a gas or a flux for shielding from contamination. The shielding is selected based on material to be welded, joint design and weld product final appearance. Shielding is important to not only protect the molten metal, but also the surroundings of weld metal. Argon or helium (or a mixture of the two) is mostly used inert gases used in TIG welding. Argon has varying arc length that helps in prevents defects in the weld. Argon shielding produces high weld quality and good appearance of final product. Whereas helium shielding gas is used to increase the weld penetrations in a joint to increase the welding speed. Sometimes the mixture of two (helium and argon) is used to get the benefits of both. Sometimes argon-hydrogen and argon-nitrogen are used in special cases. TIG welding has become easy to produce high quality aluminum welding products for structural applications.
Weld Joints and Weld Types
The joint tells how the two weld pieces are arranged relative to each other for welding. Weld type provides information about how the weld is formed in a joint. There are two weld types; a fillet and a groove weld. While, there are many types of weld joints. The selection of a proper weld joint and weld type is an important aspect of arc welding and they are selected based on design details to be achieved.
Primary Operating Variables
The typical arc voltages for GTAW process are 10–20V. Whereas for consumable electrodes the typical arc voltages required are from 20–40V. And typical current range is between 50 and 500A (e.g., for plasma applications and GTAW). For high current types the current approaches 2000A (e.g., SAW).
Metal Transfer Mode
The selection of metal transfer mode may affect the weld shape, heat input and depth of fusion and spatter. The transfer modes depend on wire diameter, current, shielding gas and arc welding power supply. Transfer modes are spray, globular, short circuit, pulsed spray and short circuit transfer. The metal transfer mode depends on the type of welding joint to be welded.
Types of Arc Welding
There are several types of arc welding, each with its own unique characteristics and uses.
- Shielded Metal Arc Welding (SMAW): Also known as stick welding, this is the most basic and common type of arc welding. It uses a consumable electrode coated in flux to create an electric arc and create the weld. It is a manual process that is often used in outdoor or fieldwork and can be used on a variety of metal thicknesses.
- Gas Tungsten Arc Welding (GTAW): Also known as Tungsten Inert Gas (TIG) welding, this method uses a non-consumable tungsten electrode to create the arc. It is a precise method that is often used for welding thin metal sections and for creating precise and high-quality welds.
- Gas Metal Arc Welding (GMAW): Also known as Metal Inert Gas (MIG) welding, this method uses a consumable wire electrode and a shielding gas to create the arc. It is a fast and efficient method that is often used in industrial and manufacturing settings.
- Flux Cored Arc Welding (FCAW): Similar to MIG welding, this method also uses a consumable wire electrode, but it has a hollow center filled with flux. This flux creates a shielding gas when it melts, which protects the weld from contamination. It is often used for welding thicker metal sections and for welding in outdoor or windy conditions.
- Submerged Arc Welding (SAW): This method uses a consumable electrode and a flux blanket to create the arc. The weld is performed beneath the flux blanket, which protects the weld from contamination and improves its quality. It is often used in heavy industrial settings, such as shipbuilding, and is ideal for welding thick metal sections.
Advantages and Disadvantages of Arc Welding
Arc welding is a versatile and widely used method of welding, but it also has some limitations and drawbacks.
Advantages
- High strength and durability of the weld: Arc welding creates strong and durable welds that can withstand high stress and pressure.
- Versatility: There are different types of arc welding, each with its own advantages and disadvantages, that can be used to weld a wide range of metal types and thicknesses.
- High precision: Some types of arc welding, such as TIG welding, allow for high precision and control, making it ideal for creating precise and high-quality welds.
- Fast and efficient: Methods such as MIG welding are fast and efficient, making it ideal for industrial and manufacturing settings.
Disadvantages
- Requires skill and training: Arc welding requires a high level of skill and training, and it is not easy to learn.
- High heat input: Arc welding generates high heat, which can cause warping, cracking, or distortion of the metal.
- Health and safety risks: Arc welding generates UV radiation, which can be harmful to the eyes and skin, and it also produces hazardous fumes and gases.
- Limited in certain application: Some types of arc welding are not suitable for certain applications, such as welding in tight spaces or in the presence of wind.
- Quality of weld depends on the skill of the welder: If the welder is not skilled enough the quality of weld may not be as good as it should be.
Applications of Arc Welding
Some common applications of arc welding include:
- Arc welding is often used in the construction industry to weld steel beams, pipes, and other structural components.
- Arc welding is used in manufacturing to join metal parts in the production of vehicles, machinery, and other equipment.
- Arc welding is used to repair and maintain a wide range of equipment and structures, including bridges, ships, and pipelines.
- Some artists use arc welding to create sculptures and other works of art.
- Arc welding is used in the aerospace and defense industries to manufacture and repair aircraft and spacecraft components.
- Arc welding is also used in shipbuilding and repair, as well as in the construction of offshore oil platforms and other marine structures.
- Arc welding is used in the medical industry to manufacture surgical instruments and implants.
- Arc welding is used extensively in the automotive industry, such as in the production of cars, trucks, and buses.
FAQs
What are the limitations of arc welding?
Some of the limitations of arc welding include the need for skilled operators, the potential for welding defects such as incomplete fusion and porosity, and the need for proper joint preparation and fit-up. Additionally, arc welding can produce harmful fumes and radiation, so appropriate safety measures must be taken.
What should not be done during arc welding?
During arc welding, it is important to avoid contamination of the joint area, such as from rust or oil, as well as to avoid creating an arc in the presence of flammable materials. It is also important to avoid over-welding and to use the correct welding technique and equipment for the specific application.
What controls the size of an arc?
The size of an arc is controlled by the voltage and current settings on the welding power source.
What is the maximum safe voltage for arc welding?
The maximum safe voltage for arc welding is typically considered to be around 50 volts.
Which current is used for arc welding?
Direct current (DC) is typically used for arc welding.
What is the maximum temperature of arc welding?
The maximum temperature of arc welding can reach around 6,500 degrees Fahrenheit (3,600 degrees Celsius).
What is the minimum voltage for an arc?
The minimum voltage for an arc is typically around 10 volts.
Why is arc very hot?
The arc is very hot because it is created by an electric current passing through a gas, which heats the gas to extremely high temperatures.
How bright is a welding arc?
The brightness of a welding arc can be very intense and can cause damage to the eyes, so proper eye protection is essential when welding.
Conclusion
In conclusion, arc welding is a widely used welding technique that is capable of producing strong and durable welds. However, it also requires skilled operators and proper equipment and joint preparation to avoid defects such as incomplete fusion and porosity. Additionally, arc welding can produce harmful fumes and radiation, so appropriate safety measures must be taken. The size of the arc is controlled by the voltage and current settings on the welding power source, direct current (DC) is typically used for arc welding, and the maximum safe voltage for arc welding is typically considered to be around 50 volts. The maximum temperature of arc welding can reach around 6,500 degrees Fahrenheit. It’s important to follow the manufacturer’s specifications and safety guidelines, and consult with a professional before welding.