Metal Inert Gas (MIG) Welding
Introduction
Metal Inert Gas (MIG) welding is a highly versatile and widely used welding process in various industries. It’s known for its ease of use, speed, and adaptability, making it a popular choice for both novice and experienced welders. In this comprehensive guide, we will explore the ins and outs of MIG welding, covering everything from the basic principles to its applications, advantages, and challenges.
What is MIG Welding?
MIG welding, also known as Gas Metal Arc Welding (GMAW), is a welding process that uses a continuous solid wire electrode heated and fed into the weld pool from a welding gun. The weld pool is protected from contamination by an inert shielding gas, hence the name. This method allows for high-quality welds with minimal cleanup.
The MIG Welding Process
The MIG welding process involves several key components and steps:
Equipment and Setup:
The essential equipment for MIG welding includes a welding machine, a welding gun, a wire feeder, and a shielding gas supply. The welding machine provides the necessary power, while the wire feeder ensures a continuous supply of the electrode wire.
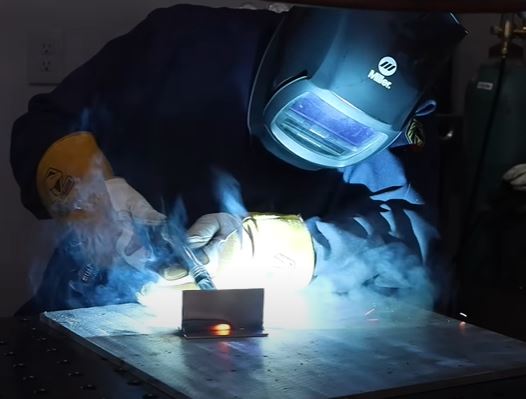
Step-by-Step Process:
- Preparation: Clean the workpiece to remove any contaminants.
- Setup: Select the appropriate wire electrode and shielding gas for the material.
- Adjust Settings: Set the welding machine to the correct voltage and wire feed speed.
- Welding: Begin welding by pulling the trigger on the welding gun, which feeds the wire and releases the shielding gas simultaneously.
- Monitor and Adjust: Continuously monitor the weld and make necessary adjustments to maintain a stable arc and good weld quality.
Characteristics of MIG Welding
MIG welding is characterized by several key features:
- High Deposition Rate: MIG welding allows for a high deposition rate, making it efficient for welding large workpieces.
- Ease of Use: The process is relatively easy to learn, making it accessible for beginners.
- Versatility: It can be used to weld a variety of metals, including aluminum, steel, and stainless steel.
- Minimal Post-Weld Cleanup: The inert shielding gas helps produce clean welds with minimal spatter and slag.
MIG vs MAG Welding
MIG (Metal Inert Gas) and MAG (Metal Active Gas) welding are both subtypes of Gas Metal Arc Welding (GMAW), but they differ primarily in the type of shielding gas used:
MIG Welding:
- Shielding Gas: Uses inert gases like argon, helium, or a mixture of the two. These gases do not react with the weld pool.
- Applications: Ideal for welding non-ferrous metals like aluminum and copper, as well as stainless steel.
- Advantages: Provides a clean weld with minimal spatter and excellent bead appearance.
MAG Welding:
- Shielding Gas: Uses active gases, typically a mixture of argon and CO2 or pure CO2. These gases can react with the weld pool to influence the properties of the weld.
- Applications: Commonly used for welding ferrous metals like mild steel.
- Advantages: More economical than MIG welding due to the lower cost of CO2 and provides deep penetration and high welding speeds.
Metal Transfer Modes in MIG Welding
The metal transfer mode in MIG welding significantly affects the quality and characteristics of the weld. There are four primary metal transfer modes:
- Short-Circuiting Transfer: This mode occurs at low voltage and amperage, making it suitable for thin materials. The wire makes contact with the workpiece, creating a short circuit that melts the wire tip.
- Globular Transfer: At higher voltages, the wire forms larger droplets that transfer across the arc. This mode is less stable and produces more spatter, but it’s useful for welding thicker materials.
- Spray Transfer: This mode uses a high voltage and current, causing the wire to melt into fine droplets that spray across the arc. It’s ideal for welding thicker materials and provides a smooth, high-quality weld.
- Pulsed-Spray Transfer: This advanced mode alternates between high and low current, allowing for better control and reduced heat input. It’s suitable for welding thin materials and out-of-position welds.
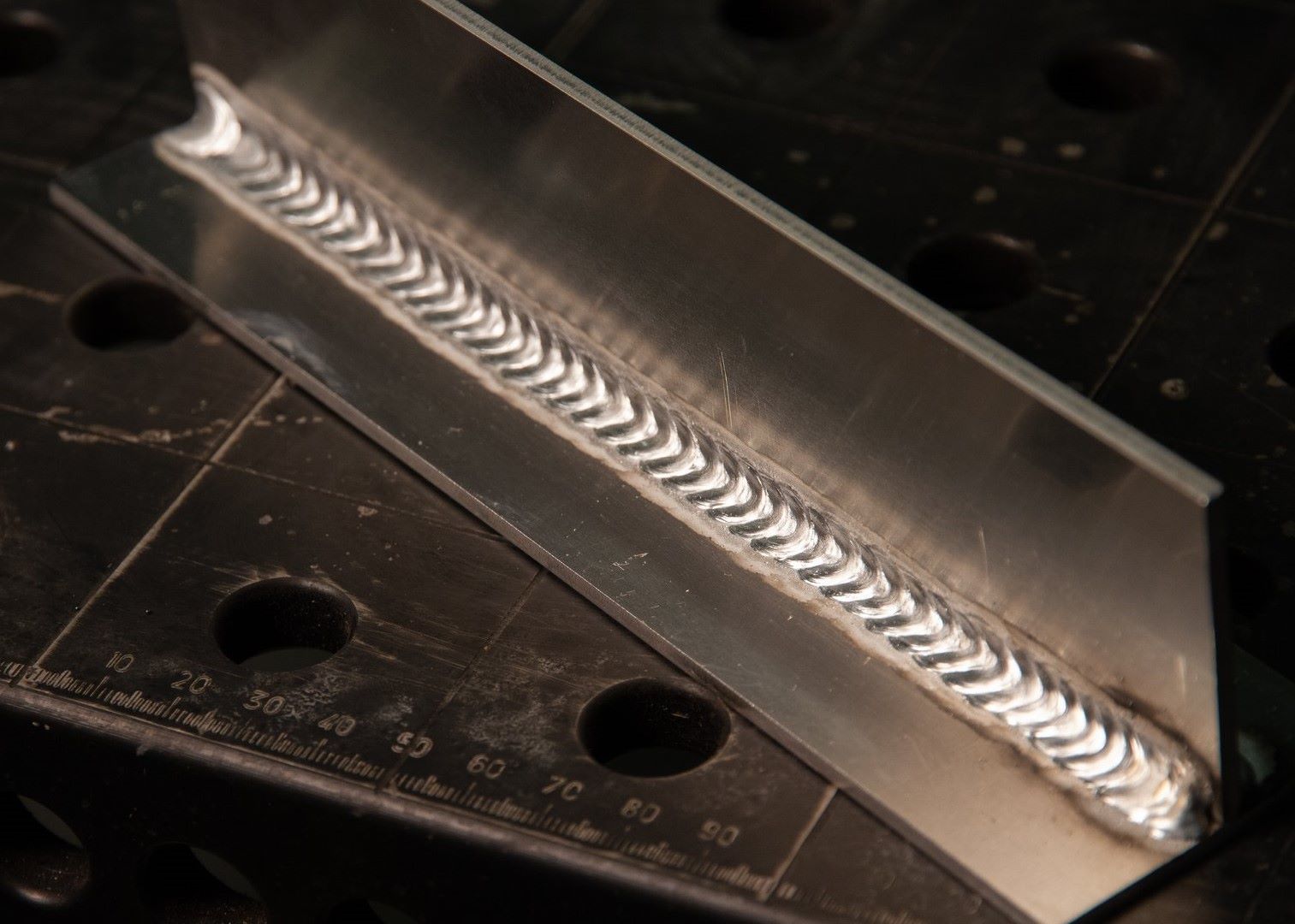
Shielding Gas in MIG Welding
Shielding gas plays a crucial role in MIG welding by protecting the weld pool from atmospheric contamination. The choice of shielding gas depends on the material being welded:
- Argon: Commonly used for non-ferrous metals like aluminum.
- Carbon Dioxide (CO2): Widely used for steel welding due to its cost-effectiveness, though it produces more spatter.
- Argon-CO2 Mix: A blend of argon and CO2 provides a balance of good arc stability and reduced spatter, making it suitable for a variety of applications.
- Helium: Sometimes used in combination with argon for welding thicker materials due to its high thermal conductivity.
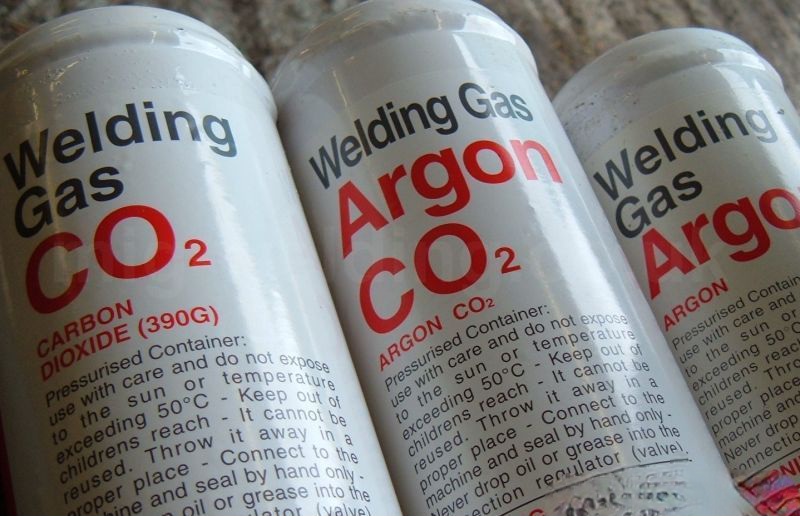
Wire Electrode in MIG Welding
The wire electrode is another critical component of the MIG welding process. The selection of the wire depends on the material and the specific requirements of the weld:
- Solid Wire Electrodes: Commonly used for general-purpose welding.
- Flux-Cored Wires: Contain a flux core that provides additional shielding and cleaning action, useful for welding in outdoor or drafty conditions.
When selecting a wire electrode, consider factors such as material compatibility, wire diameter, and the desired properties of the weld.
Advantages and Disadvantages of MIG Welding
Advantages:
- High Productivity: The continuous wire feed and high deposition rate make MIG welding a fast and efficient process.
- Ease of Automation: MIG welding can be easily automated for high-volume production.
- Versatility: Suitable for a wide range of materials and thicknesses.
Disadvantages:
- Sensitivity to Contamination: The process requires clean workpieces and proper shielding gas coverage to prevent weld defects.
- Equipment Cost: The initial investment in MIG welding equipment can be higher compared to other methods.
- Limited Out-of-Position Welding: While possible, MIG welding out-of-position can be challenging and may require specific techniques or transfer modes.
Applications of MIG Welding
MIG welding is used in various industries due to its versatility and efficiency:
- Automotive Industry: For manufacturing and repairing vehicle frames and bodies.
- Construction: In the fabrication of structural steel components.
- Shipbuilding: For welding large sections of ships and offshore structures.
- Manufacturing: Used extensively in the production of machinery, appliances, and consumer goods.
Specific applications include welding pipelines, pressure vessels, and metal furniture, highlighting the adaptability of MIG welding across different sectors.
FAQs
What materials can be welded using MIG welding?
MIG welding can weld a variety of materials, including steel, stainless steel, aluminum, and copper alloys.
How do I choose the right shielding gas for MIG welding?
The choice of shielding gas depends on the material being welded. Argon is good for non-ferrous metals, CO2 for steel, and a mix of argon and CO2 for general-purpose welding.
What is the difference between solid wire and flux-cored wire in MIG welding?
Solid wire is used for general-purpose welding, while flux-cored wire contains a flux core that provides additional shielding, making it suitable for outdoor welding or in drafty conditions.
Can MIG welding be automated?
Yes, MIG welding is easily automated and widely used in automated production lines for high-volume manufacturing.
What are the common defects in MIG welding, and how can they be prevented?
Common defects include porosity, spatter, and lack of fusion. These can be prevented by proper setup, clean workpieces, and appropriate selection of welding parameters and shielding gas.
Conclusion
MIG welding stands out as a versatile, efficient, and widely applicable welding method. From its straightforward process to its adaptability for various materials and industries, MIG welding continues to be a preferred choice for many welding applications. As technology advances, the future of MIG welding looks promising, with ongoing improvements in equipment and techniques.