Choosing the Right Welding Process for Any Project
When it comes to welding, selecting the right welding process is crucial to achieving the desired outcome. Different welding techniques are designed for specific applications and materials, making it essential to understand the strengths and limitations of each process. Whether you are working on a small DIY project or tackling large-scale industrial welding, choosing the correct welding method can significantly impact the quality, efficiency, and durability of your work.
In this guide, we’ll explore various welding processes, their unique characteristics, and the factors to consider when selecting the best one for your project. By understanding these details, you can make informed decisions and ensure that your welding tasks are completed with precision and professionalism.
Understanding Different Welding Processes
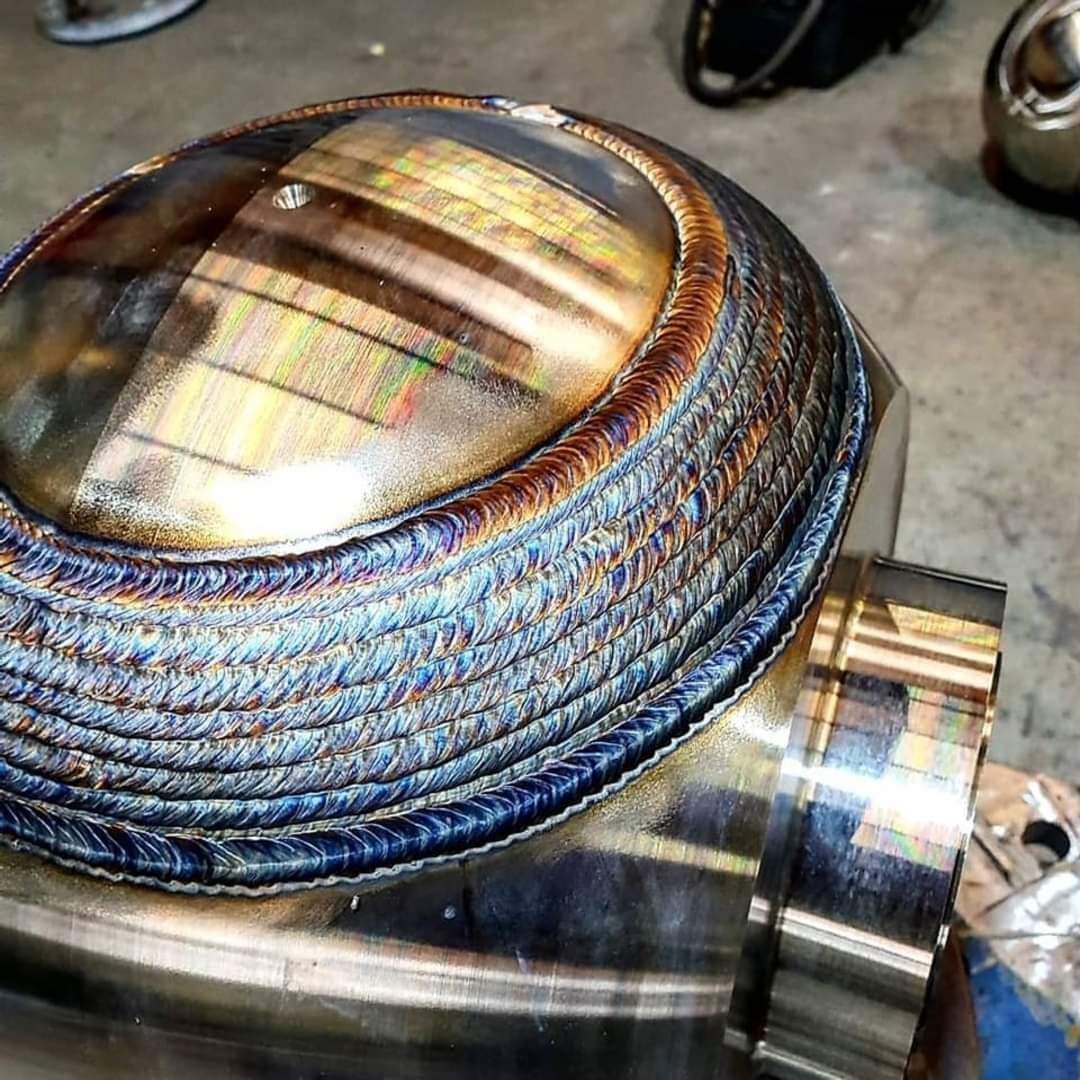
There are several common welding processes, each suited to specific types of projects and materials. Below is a detailed overview of the most widely used welding methods:
1. Metal Inert Gas (MIG) Welding
Also known as Gas Metal Arc Welding (GMAW), MIG welding uses a continuous wire electrode fed through a welding gun, creating an arc that melts the metal. The process uses an inert gas, such as argon or a mixture of argon and CO2, to shield the weld from contaminants in the air.
- Best For: Thick materials such as mild steel, stainless steel, and aluminum.
- Advantages: High welding speed, minimal cleanup, and easy to learn.
- Drawbacks: Limited to indoor use due to sensitivity to wind and drafts.
2. Tungsten Inert Gas (TIG) Welding
TIG welding, or Gas Tungsten Arc Welding (GTAW), uses a non-consumable tungsten electrode and a separate filler rod. It provides exceptional control over the weld bead, making it ideal for precision work.
- Best For: Thin materials, such as stainless steel, aluminum, and copper.
- Advantages: Produces high-quality, precise welds; versatile for various positions.
- Drawbacks: Slower process, requires more skill and steady hand coordination.
3. Stick Welding
Shielded Metal Arc Welding (SMAW), commonly known as stick welding, is a versatile process that uses a consumable electrode coated in flux. The flux creates a shielding gas that protects the weld pool from atmospheric contamination.
- Best For: Heavy-duty applications such as structural welding and pipeline work.
- Advantages: Works well outdoors and on dirty or rusty metals.
- Drawbacks: More slag to clean up, and requires more post-weld finishing.
4. Flux-Cored Arc Welding (FCAW)
Similar to MIG welding, FCAW uses a wire-fed system, but instead of relying on an external gas, it uses a tubular wire filled with flux. This makes it suitable for outdoor welding.
- Best For: Heavy sections of metal and thick plate steel.
- Advantages: High deposition rate, ideal for thick materials.
- Drawbacks: More smoke and slag, which can obscure the weld area.
5. Oxy-Acetylene Welding
Oxy-acetylene welding, or gas welding, uses a mixture of oxygen and acetylene to produce a high-temperature flame. It is commonly used for brazing, cutting, and joining thin materials.
- Best For: Repairs, thin metals, and artistic applications.
- Advantages: Portable and versatile.
- Drawbacks: Slower and less precise compared to modern arc welding techniques.
Key Factors to Consider When Choosing a Welding Process
To determine the best welding process for your project, it’s essential to consider several factors, including:
1. Material Type
The type of metal you’re working with is one of the most critical factors. Each welding process is optimized for specific materials:
- MIG welding is ideal for thicker materials like carbon steel, stainless steel, and aluminum.
- TIG welding is best for thin metals and non-ferrous metals like aluminum and copper.
- Stick welding is excellent for heavy metals and structural work.
- FCAW is suited for heavy plate steel and applications requiring high deposition.
2. Material Thickness
The thickness of the metal dictates the heat input required. MIG and stick welding are better suited for thicker sections, while TIG welding is ideal for thinner materials that require precise control.
3. Position of the Weld
Different welding positions—flat, horizontal, vertical, and overhead—pose unique challenges. TIG welding provides excellent control in all positions, whereas MIG and FCAW are faster for flat and horizontal positions.
4. Environment and Accessibility
Consider whether you will be welding indoors or outdoors. MIG and TIG are sensitive to wind and drafts, making them less suitable for outdoor use. Stick and flux-cored welding are more adaptable to varying environmental conditions.
5. Welding Speed and Productivity
If speed and efficiency are priorities, MIG and FCAW are typically faster processes. For complex, intricate welds, TIG welding, although slower, offers superior control and precision.
6. Equipment Availability and Budget
Certain welding processes require specialized equipment and higher initial investments. Assess your budget and the availability of the necessary tools before committing to a particular process.
Best Practices for Selecting the Right Welding Process
Here are some best practices to guide you through the selection process:
- Define the Project Scope:
Start by defining the project requirements, including the type of materials, joint configurations, and desired aesthetics. - Consider Strength and Durability:
Choose a welding process that provides the strength and durability needed for the application. For structural projects, stick and MIG welding offer robust solutions. - Evaluate Weld Appearance:
If visual appearance is a priority, TIG welding produces the cleanest and most visually appealing welds with minimal spatter. - Factor in the Work Environment:
Assess the working environment and conditions. For outdoor projects or where portability is required, stick and FCAW are more suitable. - Match the Process to Skill Level:
Select a welding process that matches your skill level. MIG welding is beginner-friendly, while TIG welding demands more experience and steady hand coordination.
Common Mistakes When Choosing a Welding Process
- Ignoring Material Properties:
Not all metals respond well to every welding process. Failing to match the welding process to the metal type can lead to poor weld quality and potential failure. - Overlooking Environmental Factors:
Using processes like MIG or TIG in windy conditions without proper shielding can result in weak, porous welds. - Choosing Speed Over Quality:
While productivity is important, choosing a process based solely on speed can compromise weld quality. Always prioritize the integrity and strength of the weld. - Skipping Practice and Testing:
Always conduct a test weld on a scrap piece of the same material to ensure the chosen process works as expected.
Conclusion
Choosing the right welding process is a nuanced decision that requires a deep understanding of project requirements, material properties, and environmental considerations. Whether you’re a beginner or a professional welder, selecting the correct method can significantly impact the quality and success of your project. By evaluating factors such as material type, thickness, weld position, and environmental conditions, you can confidently choose a welding process that meets your specific needs. Embrace the strengths of each welding process, and leverage this guide to make informed decisions for your welding projects, ensuring high-quality results every time.