Weld Overlay vs Cladding vs Hardfacing: Which Wins?
Introduction
When it comes to industrial applications, equipment is often subjected to harsh conditions that can cause wear, corrosion, and other forms of damage. To protect these components and extend their useful life, various techniques are used to add a layer of material to the surface, creating a barrier between the equipment and the environment.
Three of the most common techniques used for this purpose are Weld Overlay, Cladding, and Hardfacing. Weld Overlay involves adding a layer of material to the base metal through welding, which can improve the metal’s resistance to wear, corrosion, and other types of damage. Cladding, on the other hand, involves bonding a layer of one material to another to enhance the properties of the base material. Finally, Hardfacing is a type of weld overlay that involves adding a layer of hard, wear-resistant material to protect against abrasion, impact, and erosion.
While all three of these techniques can be effective in certain situations, each has its own strengths and weaknesses. In this article, we’ll take a closer look at Weld Overlay, Cladding, and Hardfacing, evaluating the advantages and disadvantages of each technique and discussing which one might be best for different types of applications. Whether you’re a welder, engineer, or just curious about industrial techniques, this article will provide you with a better understanding of these important processes and help you make informed decisions about which technique to use in your next project.
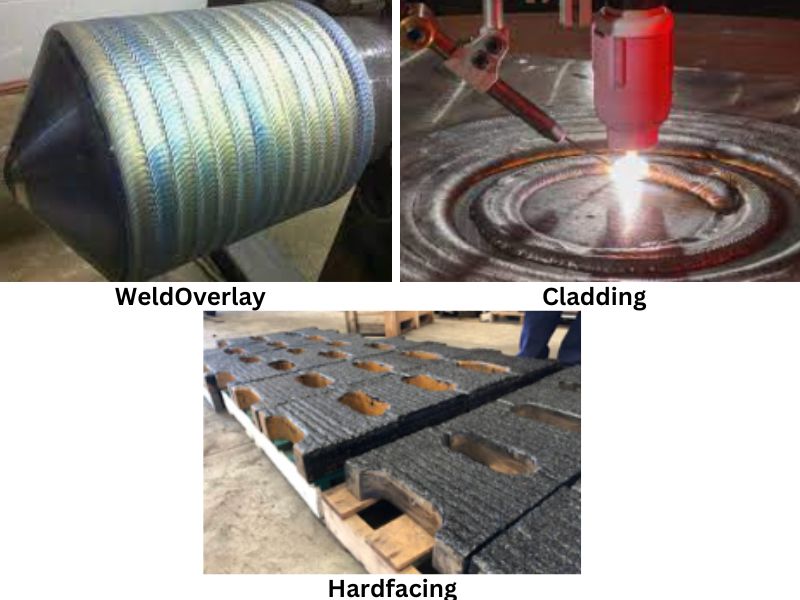
Weld Overlay: A welding technique used to add a layer of material to a base metal to improve its resistance to wear, corrosion, or other types of damage. The added layer can be made of the same material as the base metal or a different one.
Cladding: A process in which a layer of one material is bonded to another to enhance the properties of the base material. The added layer can be made of a different material with properties that are desirable for the intended application.
Hardfacing: A type of weld overlay that involves adding a layer of hard, wear-resistant material to a surface to protect it from damage caused by abrasion, impact, or erosion.
Weld Overlay
Definition and explanation of the technique
Weld Overlay is a technique used in welding and metallurgy to add a layer of material to the surface of a metal substrate. The layer can be made of the same material as the base metal or a different one, and it is applied using welding techniques such as gas tungsten arc welding (GTAW), shielded metal arc welding (SMAW), or gas metal arc welding (GMAW).
The Weld Overlay process involves melting a filler material and depositing it onto the surface of the substrate. The filler material is chosen based on the specific properties needed for the application, such as resistance to wear, corrosion, or high temperatures. Once the filler material is deposited onto the substrate, it cools and solidifies, creating a layer that is bonded to the substrate.
Advantages and disadvantages
One advantage of Weld Overlay is that it allows for the addition of a protective layer to a surface without requiring the entire component to be replaced. This can be a cost-effective solution for repairing damaged or worn parts, as it can extend the life of the component and avoid the need for expensive replacements. Weld Overlay can also be used to modify the surface properties of a component, such as increasing its hardness or improving its wear resistance.
However, Weld Overlay also has some disadvantages. One potential issue is that the layer may not bond properly to the substrate if the welding process is not carried out correctly, leading to a weak or brittle layer that can fail prematurely. In addition, Weld Overlay can add stress to the component, which may cause cracking or other forms of damage over time.
Weld Overlay has many applications in industry, including the repair of worn or damaged components in machinery, the creation of wear-resistant coatings on tools and equipment, and the modification of surface properties to improve performance in high-stress environments. It is also commonly used in the oil and gas industry to protect piping and other equipment from corrosion caused by harsh environments.
Overall, Weld Overlay is a versatile and useful technique that can be used in a wide range of applications. However, it is important to carefully consider the specific properties needed for the application and to ensure that the welding process is carried out correctly to avoid potential issues with bonding and stress.
Cladding
Definition and explanation of the technique
Cladding is a technique used in metallurgy to add a layer of material to a substrate. Unlike Weld Overlay, which involves melting a filler material and depositing it onto the surface of the substrate, Cladding involves bonding a layer of one material to another to enhance the properties of the base material. The two materials are typically chosen for their different properties, such as hardness, corrosion resistance, or thermal conductivity.
There are several ways to apply Cladding, but one common method involves using a rolling mill to bond the two materials together. The two materials are first cleaned and prepared, and then they are heated and rolled together under high pressure. The result is a strong, durable bond between the two materials.
Advantages and disadvantages
One of the advantages of Cladding is that it allows for the creation of a layer with specific properties that are different from those of the base material. This can be useful in a wide range of applications, such as improving the corrosion resistance of a metal component or enhancing its wear resistance. Cladding can also be used to create a composite material with a unique combination of properties that cannot be achieved with a single material.
However, Cladding also has some disadvantages. One potential issue is that the bond between the two materials may not be as strong as desired, which can lead to delamination or separation over time. In addition, the process of Cladding can be more complex and time-consuming than other techniques, which can increase costs and production times.
Cladding has many applications in industry, including the creation of corrosion-resistant materials for the chemical and oil and gas industries, the production of wear-resistant coatings for cutting tools and other equipment, and the manufacture of heat exchangers and other components that require specific properties. Cladding can also be used in architectural applications to create decorative or functional surfaces, such as metal façades or roofing.
Overall, Cladding is a powerful technique that can be used to enhance the properties of metal components and create new materials with unique properties. However, it is important to carefully consider the specific requirements of the application and to ensure that the Cladding process is carried out correctly to avoid potential issues with delamination or separation.
Hardfacing
Definition and explanation of the technique
Hardfacing is a technique used in metallurgy to increase the hardness and wear resistance of metal components. It involves applying a layer of hard, wear-resistant material to the surface of a substrate, typically using a welding process. The layer is chosen based on the specific requirements of the application, such as resistance to wear, abrasion, or impact.
The Hardfacing process involves melting a filler material and depositing it onto the surface of the substrate. The filler material is typically a harder, wear-resistant material than the base metal, such as tungsten carbide, chromium carbide, or a ceramic material. The Hardfacing layer is then bonded to the substrate using a welding process such as gas tungsten arc welding (GTAW), shielded metal arc welding (SMAW), or gas metal arc welding (GMAW).
Advantages and disadvantages
One of the advantages of Hardfacing is that it can significantly extend the life of metal components that are subject to wear and abrasion. By adding a layer of hard, wear-resistant material to the surface of the component, Hardfacing can reduce the rate of wear and prevent premature failure. Hardfacing can also be used to repair damaged components, such as worn or chipped gears or worn-out hydraulic components, by restoring their original dimensions and properties.
However, Hardfacing also has some disadvantages. One potential issue is that the Hardfacing layer may not bond properly to the substrate if the welding process is not carried out correctly, leading to a weak or brittle layer that can fail prematurely. In addition, the Hardfacing process can add stress to the component, which may cause cracking or other forms of damage over time.
Hardfacing has many applications in industry, including the manufacture of mining equipment, agricultural machinery, and construction equipment. It is also commonly used in the oil and gas industry to protect drilling tools and other equipment from wear caused by harsh environments. Hardfacing can also be used in the aerospace industry to improve the wear resistance of turbine blades and other components subjected to high temperatures and high stresses.
Overall, Hardfacing is a powerful technique that can significantly extend the life of metal components subject to wear and abrasion. However, it is important to carefully consider the specific requirements of the application and to ensure that the welding process is carried out correctly to avoid potential issues with bonding and stress.
Comparison of the Techniques
When it comes to improving the performance and lifespan of metal components, three common techniques are weld overlay, cladding, and hardfacing. Each technique has its own unique advantages and disadvantages, and choosing the best one for a particular application requires careful consideration of factors such as the specific requirements of the component, the environment in which it will be used, and the available resources.
Weld Overlay Weld overlay involves depositing a layer of metal onto the surface of a substrate to improve its resistance to wear, corrosion, or other forms of damage. The advantages of weld overlay include its versatility, which allows it to be used on a wide range of components and applications, and its ability to provide a relatively thick layer of protection. However, weld overlay can be difficult to apply accurately, which can lead to inconsistencies in the thickness and quality of the overlay. It also requires significant expertise and experience to perform properly.
Cladding Cladding involves adding a layer of material to the surface of a substrate to provide protection and insulation. Common cladding materials include brick, stone, metal, and glass. The advantages of cladding include its ability to provide excellent protection against weather and other environmental factors, as well as its versatility and aesthetic appeal. However, cladding can be expensive and time-consuming to install, and it may not be suitable for applications where weight or thickness are concerns.
Hardfacing Hardfacing involves applying a layer of hard, wear-resistant material onto the surface of a metal component to increase its resistance to wear, abrasion, or impact. The advantages of hardfacing include its ability to provide excellent protection against wear and tear, as well as its versatility and relatively low cost. However, hardfacing can be difficult to apply accurately, which can lead to inconsistencies in the thickness and quality of the overlay. It also requires significant expertise and experience to perform properly.
Choosing the Best Technique for Your Application The choice of welding technique depends on the specific requirements of the application, including the type of metal component, the environment in which it will be used, and the available resources. For example, if the component is subject to heavy wear and tear, hardfacing may be the best choice.
FAQs
Is cladding the same as welding?
No, cladding is not the same as welding. Welding is a process of joining two or more pieces of metal by melting them together. Cladding, on the other hand, is a process of bonding a layer of material to the surface of another material.
What is a weld overlay?
Weld overlay is a welding technique that involves depositing a layer of metal onto the surface of a substrate, typically to improve its resistance to wear, corrosion, or other forms of damage.
What is hard surfacing in welding?
Hard surfacing is a welding technique that involves applying a layer of hard, wear-resistant material onto the surface of a metal component to increase its resistance to wear, abrasion, or impact.
What are the advantages of hardfacing in welding?
The advantages of hardfacing in welding include increased resistance to wear, abrasion, or impact, extended life of metal components, and the ability to repair damaged components.
Is weld overlay the same as hard facing?
No, weld overlay and hard facing are not the same. Weld overlay involves depositing a layer of metal onto the surface of a substrate, while hard facing involves applying a layer of hard, wear-resistant material onto the surface of a metal component.
What is hardfacing used for?
Hardfacing is used to increase the resistance to wear, abrasion, or impact of metal components that are subject to harsh environments, such as mining equipment, agricultural machinery, and construction equipment. It is also used to repair damaged components.
Is facade and cladding the same?
Facade and cladding are not exactly the same, but they are related. Facade refers to the exterior of a building, including walls, windows, and doors, while cladding refers to the process of adding a layer of material to the exterior of a building to provide protection and insulation.
What is weld cladding?
Weld cladding is a welding technique that involves depositing a layer of metal onto the surface of a substrate to improve its resistance to corrosion or other forms of damage.
What are the three types of welds?
The three types of welds are butt weld, lap weld, and fillet weld.
What are the three installation systems used for cladding?
The three installation systems used for cladding are rain screen, face-sealed, and barrier wall systems.
What is the best type of cladding?
The best type of cladding depends on the specific requirements of the application, such as the desired level of insulation, weather resistance, and aesthetic appearance. Some common types of cladding include brick, stone, metal, and glass.
How many types of cladding are there?
There are many types of cladding, including brick, stone, metal, glass, wood, vinyl, and composite materials. The choice of cladding depends on the specific requirements of the application, as well as factors such as cost, durability, and aesthetic appearance.
Conclusion
In conclusion, Weld Overlay, Cladding, and Hardfacing are all effective methods for improving the surface properties of materials. Weld Overlay involves depositing a layer of material onto the surface of a base metal, while Cladding involves bonding a thin layer of material onto the base metal. Hardfacing involves depositing a layer of hard and wear-resistant material onto a base metal. Each method has its own advantages and disadvantages, and the choice of method will depend on the specific application and the desired properties of the surface. Weld Overlay and Cladding are often used to provide corrosion resistance, while Hardfacing is used to increase wear resistance. Ultimately, the choice of method will depend on the specific requirements of the application and the available resources.