Welding in Construction Industry: A Comprehensive Overview
The construction industry stands as one of the pillars of modern society, shaping the infrastructure and buildings that we rely on daily. Welding, a vital process within this sector, plays an instrumental role in joining metals, creating robust and enduring structures. In this comprehensive article, we delve into the world of welding in the construction industry, exploring its techniques, applications, safety considerations, and the evolving trends that are shaping its future.
Introduction to Welding in Construction
Welding, often defined as the process of joining two or more pieces of metal by melting their edges together, has been an essential part of the construction industry for centuries. Its significance lies in the fact that it provides structural integrity and stability to buildings, bridges, highways, and other infrastructure projects. Whether it’s the towering skyscrapers in urban landscapes or the sturdy bridges spanning great rivers, welding plays a critical role in bringing these structures to life.
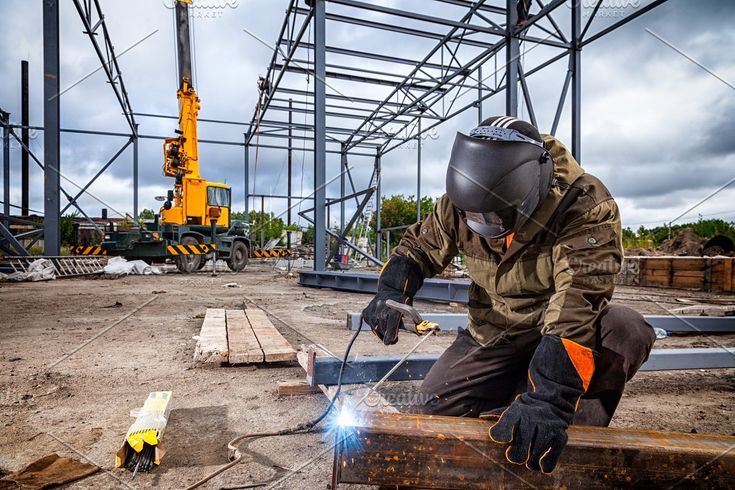
Welding Techniques in Construction
Several welding techniques are commonly employed in the construction industry, each with its own set of advantages and applications:
1. Shielded Metal Arc Welding (SMAW):
Commonly known as “stick welding,” SMAW is widely used in construction due to its versatility and ability to work in adverse conditions. It involves a consumable electrode coated with a flux that shields the weld pool from contamination.
2. Gas Metal Arc Welding (GMAW):
Also known as “MIG” (Metal Inert Gas) welding, GMAW utilizes a continuous wire electrode and a shielding gas, often argon or a mixture of gases. It’s a popular choice for welding steel and aluminum in construction.
3. Gas Tungsten Arc Welding (GTAW):
Commonly referred to as “TIG” (Tungsten Inert Gas) welding, GTAW is renowned for its precision and quality. It’s often used for welding stainless steel, aluminum, and exotic metals in applications where aesthetics and precision are crucial.
4. Flux-Cored Arc Welding (FCAW):
FCAW is similar to GMAW but uses a flux core instead of a solid wire. It’s suitable for welding thicker materials and is often used in structural steel and heavy construction.
5. Submerged Arc Welding (SAW):
SAW is ideal for welding thick steel sections. It involves the continuous feeding of a solid wire electrode under a layer of granular flux. This technique is used for high-quality welds in applications like bridge construction.
Applications of Welding in Construction
Welding finds applications throughout the construction industry, ranging from residential to heavy industrial projects. Here are some key areas where welding is indispensable:
1. Structural Steel Fabrication:
Welding is crucial in fabricating structural steel components used in buildings, bridges, and industrial facilities. These welded connections ensure the strength and stability of the structures.
2. Bridge Construction:
Bridges, whether spanning rivers or highways, rely heavily on welding for their construction. It provides the necessary strength to withstand heavy loads and environmental conditions.
3. Building Construction:
Welding is used in both residential and commercial building construction for various purposes, including attaching steel support beams, joining HVAC ductwork, and securing metal roofing.
4. Pipeline Welding:
In the oil and gas industry, welding is used extensively for the construction of pipelines that transport fluids over long distances. Proper welding ensures the integrity and safety of these pipelines.
5. Sheet Metal Work:
In HVAC (Heating, Ventilation, and Air Conditioning) systems and architectural applications, welding is used to join sheet metal components to create ductwork and decorative features.
6. Repair and Maintenance:
Beyond initial construction, welding is vital for the repair and maintenance of structures. Welders are often called upon to fix damaged steel components or reinforce weakened areas.
Safety Considerations in Construction Welding
Safety is paramount in the construction industry, and welding presents its own set of hazards. To ensure the well-being of workers and the quality of the work, several safety considerations must be addressed:
1. Personal Protective Equipment (PPE):
Welders must wear appropriate PPE, including helmets with auto-darkening filters, flame-resistant clothing, gloves, and safety glasses, to protect against sparks, UV radiation, and hot metal.
2. Ventilation and Fume Extraction:
Proper ventilation and fume extraction systems are essential to remove harmful welding fumes and gases, such as ozone and hexavalent chromium, which can lead to respiratory issues.
3. Fire Prevention:
Welding generates sparks and heat, increasing the risk of fires. Adequate fire prevention measures, such as fire extinguishers and fire-resistant barriers, must be in place.
4. Training and Certification:
Welders should undergo comprehensive training and obtain relevant certifications to ensure they have the necessary skills and knowledge to perform welding tasks safely and effectively.
5. Inspecting Equipment:
Regular inspections of welding equipment, including power sources, cables, and welding guns, help prevent equipment failures that could lead to accidents.
6. Fall Protection:
When working at heights, such as on scaffolding or elevated platforms, welders must use fall protection equipment to prevent falls and injuries.
Evolving Trends in Construction Welding
The construction industry, like any other, evolves over time, and welding is no exception. Several emerging trends are reshaping the way welding is applied in construction:
1. Automation and Robotics:
Automation and robotics are increasingly used in welding processes. Robotic welding systems enhance precision and productivity, reducing the reliance on manual labor.
2. Digitalization and Data Integration:
Digital tools and software are being integrated into welding processes, allowing for real-time monitoring and data analysis. This enhances quality control and provides insights for process improvement.
3. Advanced Materials and Alloys:
The development of advanced materials and alloys, such as high-strength steels and aluminum alloys, is driving innovation in welding techniques and equipment to accommodate these materials.
4. Environmentally Friendly Practices:
Sustainability is a growing concern in construction. Welding methods that reduce energy consumption and emissions, such as laser welding, are gaining traction.
5. Welding in 3D Printing:
The integration of welding with 3D printing technology, known as additive manufacturing, is opening up new possibilities for creating complex metal structures with precision.
6. Remote Welding and Augmented Reality (AR):
Remote welding and AR technologies allow experts to oversee and guide welding processes from a distance, improving efficiency and reducing the need for on-site personnel.
FAQs
What are the common welding techniques used in the construction industry?
Common welding techniques in construction include SMAW (stick welding), GMAW (MIG welding), GTAW (TIG welding), FCAW (flux-cored welding), and SAW (submerged arc welding).
What is the primary application of welding in construction?
Welding is primarily used in construction for structural steel fabrication, including buildings, bridges, and industrial facilities.
What safety precautions should welders take on construction sites?
Welders should wear appropriate PPE, ensure proper ventilation, have fire prevention measures in place, undergo training and certification, inspect equipment regularly, and use fall protection when working at heights.
How is automation changing welding in construction?
Automation, including robotics, is enhancing precision and productivity in welding processes, reducing reliance on manual labor and improving overall efficiency.
What are some emerging trends in construction welding?
Emerging trends include digitalization and data integration, the use of advanced materials, a focus on sustainability, the integration of welding with 3D printing, and the adoption of remote welding and augmented reality technologies.
Why is welding important for the sustainability of construction projects?
Welding methods that reduce energy consumption and emissions contribute to the sustainability of construction projects, aligning with environmental goals and reducing the industry’s carbon footprint.
Conclusion
Welding is an indispensable element of the construction industry, providing the strength and durability necessary for building the structures that shape our world. With various welding techniques and applications, safety measures, and evolving trends, the role of welding in construction continues to evolve and adapt to meet the demands of a changing industry. As technology advances and sustainability becomes increasingly important, we can expect further innovations in welding methods and materials, further enhancing the construction industry’s ability to create safe, efficient, and sustainable structures for the future.