What is Weld Purging?
Weld purging is the process of removing oxygen and other gases from the weld zone in order to create a high-quality, defect-free weld. This is done by introducing an inert gas, such as argon or helium, into the welding environment to displace any atmospheric gases that might otherwise contaminate the weld. Weld purging is a critical step in many welding applications, particularly those that involve stainless steel, titanium, or other exotic materials that are sensitive to oxidation.
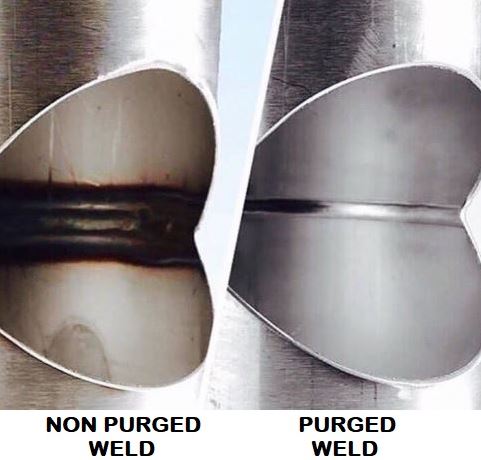
Basic Concepts of Weld Purging
Weld purging is a critical process in welding that involves removing oxygen and other contaminants from the weld zone to prevent oxidation, reduce weld defects, and improve the quality of the weld. Weld purging is essential for welding reactive metals such as stainless steel, titanium, and zirconium, where the presence of oxygen and other contaminants can lead to severe weld defects and reduce the mechanical properties of the joint.
Purging works by replacing the oxygen in the weld zone with an inert gas such as argon or helium, which does not react with the metal being welded. The inert gas is introduced into the weld zone through a nozzle or diffuser, and the flow rate is controlled to ensure adequate coverage of the weld zone. The oxygen and other contaminants are then displaced and forced out of the weld zone by the inert gas.
There are several types of weld purging techniques, including:
- Gas purging: This is the most common technique, where an inert gas such as argon or helium is used to displace oxygen and other contaminants from the weld zone. Gas purging is often used for TIG welding and is effective for both internal and external welds.
- Back purging: This technique involves introducing the inert gas through the backside of the weld, which helps to remove oxygen and other contaminants from the root of the weld. Back purging is often used for pipe welding and can be combined with gas purging for improved effectiveness.
- Mechanical purging: This technique involves using a mechanical device such as a bladder or inflatable dam to seal off the weld zone and prevent the ingress of oxygen and other contaminants. Mechanical purging is often used for welding large components and can be combined with gas purging for improved effectiveness.
Techniques for Weld Purging
Weld purging is a critical process in welding that involves removing oxygen and other contaminants from the weld zone to prevent oxidation, reduce weld defects, and improve the quality of the weld. Purging can be achieved using various techniques depending on the type of welding process used. In this section, we will discuss some of the most common techniques for weld purging in different welding processes.
- Gas Tungsten Arc Welding (GTAW): GTAW is a commonly used process for welding reactive metals, and it requires high-quality welds with minimal defects. In GTAW welding, the weld zone is purged using an inert gas such as argon or helium. The gas is delivered through a nozzle or diffuser, and the flow rate is controlled to ensure adequate coverage of the weld zone. GTAW welding often uses a back-purging technique to remove oxygen from the backside of the weld to prevent oxidation.
- Gas Metal Arc Welding (GMAW): GMAW is a welding process that uses a consumable electrode and a shielding gas to protect the weld zone. In GMAW welding, the shielding gas is used to purge the weld zone, and it can be delivered through a nozzle or diffuser. The gas used for purging depends on the type of material being welded, but argon or a mixture of argon and CO2 are commonly used.
- Flux-Cored Arc Welding (FCAW): FCAW is a welding process that uses a flux-cored wire instead of a solid wire to shield the weld zone. In FCAW welding, the shielding gas is delivered through the flux core, which acts as a purging agent. The gas used for purging depends on the type of flux-cored wire used, but CO2 and argon are commonly used.
- Shielded Metal Arc Welding (SMAW): SMAW is a welding process that uses a coated electrode to shield the weld zone. In SMAW welding, the electrode coating releases a gas that purges the weld zone. The gas released depends on the type of electrode used, but CO2 and argon are commonly used.
- Plasma Arc Welding (PAW): PAW is a welding process that uses a plasma arc to melt the base material and a filler material, if required. In PAW welding, the weld zone is purged using an inert gas such as argon or helium, which is delivered through a nozzle or diffuser.
- Electron Beam Welding (EBW): EBW is a welding process that uses a beam of high-velocity electrons to melt and join two materials. In EBW welding, the weld zone is purged using a high vacuum to remove any contaminants that may interfere with the welding process.
- Laser Beam Welding (LBW): LBW is a welding process that uses a high-energy laser beam to melt and join two materials. In LBW welding, the weld zone is purged using an inert gas such as argon or helium, which is delivered through a nozzle or diffuser.
Materials Used for Weld Purging:
- Purging Gases: Purging gases are used to displace oxygen and other contaminants from the weld zone. The most commonly used purging gases are argon and helium, which are inert and do not react with most metals. The choice of purging gas depends on the type of material being welded, the welding process, and other factors.
- Purge Dams: Purge dams are used to create a barrier around the weld zone to contain the purging gas and prevent it from escaping. Purge dams can be made of various materials, including rubber, silicone, and plastic. They come in different shapes and sizes, depending on the size and shape of the weld.
- Purge Plugs: Purge plugs are used to seal off openings in the weld joint, such as holes or gaps, to prevent the purging gas from escaping. Purge plugs can be made of various materials, including rubber, silicone, and metal. They come in different shapes and sizes, depending on the size and shape of the opening.
- Oxygen Monitors: Oxygen monitors are used to measure the level of oxygen in the purging gas or in the weld zone. They provide real-time feedback on the effectiveness of the purging process and alert the welder if oxygen levels exceed the acceptable limit.
Best Practices for Weld Purging:
- Pre-weld Preparation: Before starting the welding process, it is essential to properly clean the weld joint and remove any contaminants, such as oil, grease, or rust. The weld joint should also be properly aligned and fit together tightly to minimize gaps and openings.
- Weld Purging Sequence: The weld purging sequence should be carefully planned to ensure that the purging gas effectively displaces oxygen and other contaminants from the weld zone. The sequence should start from the bottom of the weld joint and work upwards, and back-purging should be used to remove oxygen from the backside of the weld.
- Weld Purge Monitoring: During the welding process, it is essential to monitor the purging gas flow rate and the oxygen levels in the weld zone using oxygen monitors. The gas flow rate should be adjusted as needed to ensure adequate coverage of the weld zone, and the oxygen level should be kept below the acceptable limit.
- Post-weld Cleanup: After the welding process is complete, it is essential to properly clean and inspect the weld joint to ensure that it meets the required quality standards. Any purge dams or plugs used should be removed, and the weld joint should be cleaned of any residue or debris.
Weld Purging Challenges and Solutions:
Low-Pressure Purging
When welding thin-walled or small-diameter pipes, low-pressure purging may be required to prevent distortion or collapse. In such cases, specialized low-pressure purge systems, such as inflatable purge dams or flexible silicone dams, can be used to maintain a low-pressure environment.
Large-Diameter Pipe Purging
When welding large-diameter pipes, it can be challenging to achieve a consistent purge gas flow rate throughout the entire pipe. One solution is to use multiple purge points along the length of the pipe to ensure even distribution of the purging gas.
Welding Stainless Steel
When welding stainless steel, it is essential to use a purging gas with a low oxygen content, such as argon or helium, to prevent oxidation and discoloration of the weld. Back-purging can also be used to remove oxygen from the backside of the weld.
Welding Titanium
Welding titanium requires a highly controlled purging environment to prevent oxidation and contamination of the weld. A high-purity argon gas with a low moisture content should be used, and the welding zone should be protected with a titanium purge dam or cover.
FAQs
What is purging a weld?
Purging a weld refers to the process of removing oxygen and other gases from the area surrounding a weld joint before, during, and after the welding process. The goal of purging is to create an oxygen-free environment to prevent oxidation and other forms of contamination that can weaken the weld joint and compromise its integrity.
Why is purging done?
Purging is done to create an oxygen-free environment around the weld joint, which prevents oxidation and other types of contamination that can weaken the joint and compromise its strength and durability. Purging is essential when welding materials like stainless steel, titanium, and other alloys that are prone to oxidation and other types of contamination.
What are the benefits of purging welding?
The benefits of purging welding include:
- Improved weld quality
- Increased strength and durability of the weld joint
- Reduced risk of defects like porosity and cracking
- Prevention of oxidation and other types of contamination
- Enhanced corrosion resistance
- Improved aesthetics of the weld joint
How is purging done?
Purging is done by flushing the area around the weld joint with an inert gas, such as argon, nitrogen, or carbon dioxide. The gas displaces the air in the vicinity of the joint and creates an oxygen-free environment. The gas is usually introduced through a small tube or nozzle that is positioned close to the weld joint.
Which material is used for purging?
Inert gases like argon, nitrogen, and carbon dioxide are commonly used for purging.
What are the three methods of purging?
The three methods of purging are:
- Flow purging
- Mechanical purging
- Chamber purging
Why argon is used in purging?
Argon is used in purging because it is an inert gas that does not react with other materials or contaminate the weld joint. Argon is also heavier than air, so it is effective in displacing the air around the weld joint.
What is purging in flow?
Purging in flow refers to the process of removing any undesirable gases or contaminants from a system or container by flushing it with a gas such as nitrogen or argon. This is typically done to ensure the system or container is free from any impurities before being filled with a specific gas or substance.
What is purging in mechanical?
Purging in mechanical engineering refers to the process of removing any residual gases or liquids from a system or component before it is put into service. This is typically done to prevent any damage or malfunction that may be caused by the presence of contaminants in the system.
Why is co2 used for purging?
CO2 is commonly used for purging because it is readily available and inexpensive. Additionally, CO2 is non-reactive with most materials and does not leave any residue or contaminants behind.
Why n2 is used for purging?
Nitrogen (N2) is also commonly used for purging because it is an inert gas and does not react with most materials. Additionally, it is widely available and relatively inexpensive.
Conclusion
Weld purging is an essential process for achieving high-quality welds, particularly in materials that are sensitive to oxidation and contamination. Here are some key points to remember:
- Weld purging involves removing oxygen and other contaminants from the weld zone to prevent oxidation and porosity in the weld.
- The purging process can be achieved through a variety of methods, including inert gas purging, backing gas, and vacuum purging.
- Weld purging is particularly important for welding materials such as stainless steel, titanium, and other high-performance alloys that are susceptible to oxidation and contamination.
- Failure to properly purge the weld zone can result in poor quality welds, which can compromise the integrity of the joint and lead to premature failure.
- Proper training and equipment are critical to ensuring a successful weld purging process.