Common Welding and Fabrication Mistakes: How to Avoid Costly Errors and Ensure Quality
Introduction:
Welding and fabrication are essential processes in construction, manufacturing, and many other industries. However, even experienced welders and fabricators can make mistakes that compromise the quality and strength of their work. These errors can lead to costly repairs, material waste, or even safety hazards. In this article, we’ll explore the most common mistakes in welding and fabrication, their consequences, and practical tips to avoid them.
1. Incorrect Material Selection
One of the first and most critical decisions in any welding or fabrication project is material selection. The wrong choice of materials can lead to weak joints, corrosion, or failure in the field.
Consequences of Incorrect Material Selection:
- Weak welds: Incompatible materials can result in weak welds that break under stress.
- Corrosion: Using materials prone to corrosion in certain environments leads to premature failure.
- Brittleness: Some materials are more brittle than others and may crack during or after welding.
How to Avoid:
- Understand material properties: Welders must have a solid understanding of the mechanical properties of metals like steel, aluminum, and stainless steel.
- Consult Material Specifications: Always refer to the material specifications and ensure that the correct filler metal or welding consumables are used.
- Work with Metallurgists: For specialized projects, consulting a metallurgist can prevent material compatibility issues.
2. Inadequate Preparation of Materials
Material preparation is often overlooked, but it’s a critical step in ensuring a strong weld. Contaminants like dirt, rust, oil, and mill scale can prevent proper fusion, leading to weld defects.
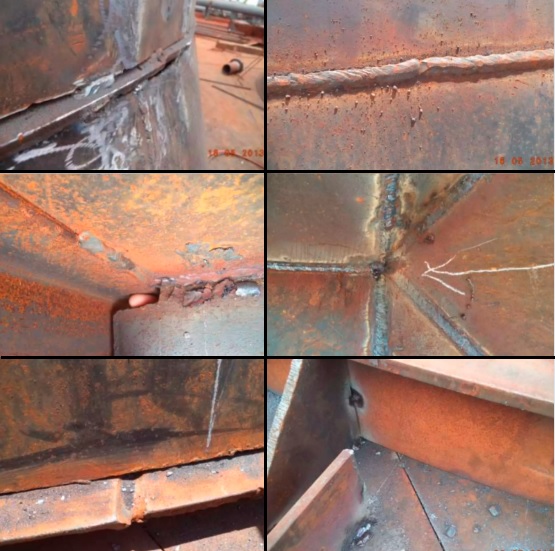
The Impact of Poor Material Preparation:
- Porosity: Contaminants trapped in the weld pool cause small holes in the weld known as porosity.
- Weak Bonds: A dirty surface prevents the filler material from bonding correctly with the base metal.
- Defective Welds: Inconsistent welds and failure to meet quality standards result from poor preparation.
How to Avoid:
- Clean thoroughly: Use wire brushes, grinders, or chemical cleaners to remove all contaminants.
- Use proper degreasers: For oily surfaces, degreasers can be applied before welding.
- Inspect surfaces: Always inspect surfaces before starting the welding process to ensure they’re ready.
3. Poor Fit-Up
Fit-up refers to how well two pieces of material fit together before welding. Poor fit-up leads to issues such as gaps, misalignment, or uneven spacing, which result in weak or inconsistent welds.
Issues Caused by Poor Fit-Up:
- Inconsistent Weld Beads: Uneven gaps or angles cause weld beads to vary in size and quality.
- Weak Joints: Misalignment results in joints that are not structurally sound.
- Excessive Grinding: Post-weld grinding and reworking are often required to fix fit-up mistakes, increasing time and costs.
How to Avoid:
- Use clamps and fixtures: These tools help hold materials in place during welding to ensure a proper fit.
- Double-check measurements: Always measure and inspect the fit-up of parts before welding.
- Tack welds: Use tack welds to hold parts in position temporarily before applying the full weld.
4. Improper Welding Technique
Welding is both an art and a science, and improper technique can lead to various defects such as spatter, undercutting, and lack of fusion. Factors like the angle of the torch, speed, and amperage settings all play a role in the quality of the weld.
Consequences of Improper Technique:
- Spatter: Small droplets of molten material can accumulate on the workpiece, reducing its aesthetic and structural quality.
- Undercutting: This occurs when too much heat is applied, resulting in grooves along the edge of the weld that weaken the joint.
- Lack of Fusion: If the arc doesn’t adequately melt the base metals and filler, the materials won’t bond properly.
How to Avoid:
- Maintain the correct torch angle: Typically, a torch angle of 10 to 15 degrees from vertical ensures good penetration and even welds.
- Control speed: Moving too fast or too slow affects bead consistency and penetration.
- Adjust settings: Make sure amperage and voltage settings are appropriate for the material thickness and type of weld being performed.
5. Lack of Penetration
Penetration refers to how deep the weld fuses into the base metal. A lack of penetration means the weld is too shallow, making it structurally unsound.
The Risks of Insufficient Penetration:
- Weak joints: Shallow welds don’t fully join the materials, resulting in weak spots that can fail under load.
- Weld Failure: Critical failure during operation, especially under stress or vibration, can lead to accidents.
- Rework Costs: Fixing insufficiently penetrated welds requires time and additional resources.
How to Avoid:
- Increase amperage: Higher amperage settings help achieve deeper penetration.
- Proper preheat: Preheating thicker materials ensures better weld penetration.
- Use correct electrode size: Larger electrodes can carry more current and provide better penetration for thicker materials.
6. Excessive Heat Input
Too much heat during welding can warp materials, cause burn-through, or lead to excessive distortion. It’s crucial to balance heat input to maintain the integrity of the workpiece.
Negative Effects of Excessive Heat Input:
- Distortion: Materials may warp or bend out of shape due to uneven heating.
- Burn-through: Thin materials are particularly vulnerable to burn-through if too much heat is applied.
- Changes in Material Properties: Excessive heat can alter the metal’s microstructure, reducing its mechanical strength.
How to Avoid:
- Control heat: Use appropriate amperage settings and maintain a steady travel speed to control heat input.
- Use heat sinks: Heat sinks can be applied to the workpiece to absorb excess heat and prevent warping.
- Intermittent welding: Avoid overheating by using intermittent welds rather than continuous welds on larger projects.
7. Ignoring Safety Protocols
Welding is a dangerous job, and failing to follow proper safety protocols can lead to injuries or accidents. Exposure to harmful fumes, intense light, and molten materials makes safety precautions essential.
Common Safety Hazards:
- Burns and Eye Damage: The intense heat and light from welding can cause severe burns and damage to the eyes.
- Fume Inhalation: Welding fumes contain hazardous materials that can cause respiratory issues.
- Electrical Shocks: Improper grounding or contact with live electrical components can result in shocks.
How to Avoid:
- Wear PPE: Always wear protective gear, including gloves, welding helmets, flame-resistant clothing, and safety glasses.
- Ensure proper ventilation: Welding should be done in well-ventilated areas to minimize exposure to harmful fumes.
- Follow electrical safety procedures: Double-check grounding and avoid contact with live wires.
8. Neglecting Post-Weld Inspection
After welding, it’s crucial to inspect the welds for any defects such as cracks, porosity, or undercutting. Skipping this step can lead to issues later in the project.
Importance of Post-Weld Inspection:
- Ensures weld quality: Inspections identify any defects that need to be addressed before the project moves forward.
- Prevents costly repairs: Finding and fixing defects early reduces the need for expensive rework.
- Safety assurance: Inspections ensure that welds meet safety standards, reducing the risk of failure under load.
How to Avoid:
- Use visual inspection: Inspect welds for visible defects like cracks or porosity.
- Perform non-destructive testing (NDT): Methods like ultrasonic testing and X-rays can detect hidden flaws.
- Create an inspection checklist: A checklist ensures that every weld is thoroughly inspected before approval.
9. Not Accounting for Shrinkage or Warping
Welding causes metals to expand and contract due to heat. If not properly accounted for, this can lead to warping or distortion of the finished product.
Consequences of Shrinkage:
- Misaligned parts: Shrinkage can pull parts out of alignment, requiring rework.
- Warped materials: Warping can occur in thinner materials or during extended welds, making the final product unusable.
- Cracks: Uneven cooling can lead to cracks in the weld or surrounding materials.
How to Avoid:
- Plan for shrinkage: Consider the effects of heat on the materials and adjust accordingly.
- Use tack welds: Tack welding at key points can prevent excessive movement during welding.
- Control cooling: Slow, controlled cooling can minimize the risk of warping and cracking.
10. Improper Gas Flow or Shielding
For processes like MIG or TIG welding, the correct gas flow is essential to protect the weld pool from contamination. Poor shielding results in defects like porosity or oxidation.
Problems Caused by Poor Gas Shielding:
- Porosity: Gas bubbles form within the weld, weakening its structure.
- Oxidation: Without adequate shielding, the weld can oxidize, leading to weak joints and poor aesthetics.
- Inconsistent welds: Fluctuating gas flow results in uneven welds and possible contamination.
How to Avoid:
- Check gas flow settings: Make sure your shielding gas flow is set according to manufacturer recommendations.
- Use proper shielding gas: Different materials require different types of shielding gases, such as argon, CO2, or helium.
- Inspect gas hoses: Ensure there are no leaks in your hoses or regulators that could disrupt gas flow.
Conclusion:
Welding and fabrication are highly skilled processes that require attention to detail, proper technique, and careful planning. By avoiding common mistakes such as poor material preparation, incorrect fit-up, or excessive heat input, welders can produce high-quality, durable welds that meet industry standards. Understanding these common errors and taking steps to prevent them will not only improve the quality of work but also increase efficiency, safety, and overall job satisfaction.