The Most Dreaded Defects in Welding
In the world of metalworking and fabrication, welding is an indispensable process. Whether it’s building skyscrapers, constructing bridges, or crafting intricate art pieces, welding plays a vital role in joining metals. However, like any other process, welding is not without its challenges. Welders and engineers encounter various defects that can compromise the integrity and safety of welds. In this article, we will explore the most dreaded defects in welding, understand their causes, and discuss ways to prevent them.
Introduction
Welding is a complex art that demands precision and skill. While skilled welders strive for perfection, they often encounter various defects that can jeopardize the strength and durability of their work. These defects can lead to structural failures, which can be catastrophic in critical applications such as construction and aerospace.
Types of Welding Defects
Welding, despite its importance, is a complex process that can be susceptible to various defects. These defects can compromise the integrity and quality of the weld. In this section, we will explore five of the most dreaded welding defects:
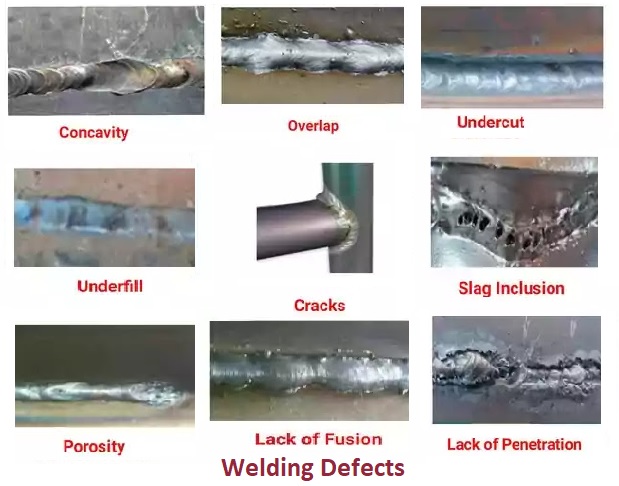
Porosity
- Definition and Causes: Porosity refers to the presence of tiny gas pockets or voids within the weld metal. It is often caused by trapped gases, such as hydrogen, nitrogen, or moisture, as the weld cools and solidifies. These gases can become trapped due to inadequate shielding gas coverage, contaminated base metal, or improper welding techniques.
- Effects on Weld Strength: Porosity weakens the weld by creating internal voids that can act as stress concentration points. This reduces the weld’s load-carrying capacity and makes it more susceptible to fracture.
- Prevention and Mitigation Techniques: To prevent porosity, it’s crucial to maintain proper shielding gas coverage, keep base materials clean and dry, and use suitable filler metals. Welders should also follow recommended welding procedures and techniques to minimize the introduction of contaminants.
Weld Cracks
- Types of Cracks (Hot Cracks, Cold Cracks, Stress Cracks): Hot cracks occur during or immediately after welding due to high temperatures and the solidification process. Cold cracks form at lower temperatures after welding, often as the weld cools. Stress cracks develop over time due to residual stresses within the weld.
- Causes and Factors Contributing to Crack Formation: Cracks result from factors like high cooling rates, impurities in the base material, and excessive welding stresses. Hot cracks are typically linked to a lack of ductility in the weld metal, while cold cracks are often caused by hydrogen embrittlement.
- Methods to Prevent Cracks: Preheating the base material, controlling cooling rates, and using low-hydrogen electrodes can help prevent cracks. Proper joint design and stress-relief heat treatments can also mitigate stress-related cracking.
Inclusions
- Definition and types (Slag Inclusions, Lack of Fusion): Inclusions refer to foreign materials trapped in the weld metal. Slag inclusions occur when welding slag is not removed properly between passes, and lack of fusion occurs when the weld metal doesn’t fuse adequately with the base material.
- Causes and Consequences: Inclusions can weaken the weld, reduce its load-bearing capacity, and act as potential stress risers. They are often caused by poor welding techniques, inadequate cleaning, or improper joint preparation.
- How to Avoid Inclusions: Proper cleaning between passes, good welding practices, and appropriate welding parameters can help prevent inclusions. Adequate fusion between the weld metal and base material should be ensured through proper joint preparation and technique.
Undercutting
- Definition and Reasons Behind Undercut Formation: Undercutting refers to the groove or depression along the edges of the weld bead. It occurs due to excessive heat, improper welding angles, or incorrect welding parameters.
- Impact on Weld Integrity: Undercutting reduces the cross-sectional area of the weld, leading to weakened joints and potentially compromising the weld’s strength.
- Techniques to Minimize Undercut: Proper electrode angles, control of heat input, and selecting suitable welding techniques can help minimize undercut. Maintaining a consistent travel speed and electrode manipulation are also essential for preventing undercut.
Distortion
- What is Distortion in Welding? Distortion in welding refers to the deformation or misalignment of the welded components due to thermal expansion and contraction during welding.
- Factors Influencing Distortion: Factors like heat input, material thickness, and joint design influence distortion. Thicker materials are more prone to distortion, and the way the weld is placed can affect the extent of distortion.
- Strategies to Control and Manage Distortion: To control distortion, techniques such as pre-welding fixturing, tack welding, and controlled heating/cooling cycles can be employed. Proper sequencing of weld passes and careful monitoring of welding parameters are essential in managing distortion effectively.
Excessive Spatter
- Definition and Causes: Excessive spatter refers to the tiny droplets of molten metal that are expelled from the welding arc during the welding process. It occurs due to factors like improper shielding gas, incorrect voltage settings, or the presence of impurities on the workpiece.
- Effects on Weld Quality: Excessive spatter can lead to an untidy and uneven weld surface. It may also result in reduced weld strength and integrity.
- Prevention and Mitigation Techniques: To minimize spatter, welders should use the appropriate shielding gas, adjust voltage settings correctly, and ensure that the workpiece is clean and free from contaminants. Proper electrode and wire selection can also help reduce spatter.
Tungsten Inclusion
- Definition and Causes: Tungsten inclusion occurs when tungsten from the electrode becomes trapped in the weld metal. This can happen when the electrode is not properly shielded or when the electrode is contaminated.
- Effects on Weld Quality: Tungsten inclusion weakens the weld and can create stress concentration points. It may also lead to poor electrical conductivity in the weld.
- Prevention and Mitigation Techniques: To prevent tungsten inclusion, welders should ensure that the electrode is properly shielded with the appropriate gas, maintain a clean electrode tip, and use suitable electrode materials. Proper welding techniques and electrode manipulation can also help avoid this defect.
Burn-Through
- Definition and Causes: Burn-through occurs when excessive heat input causes the weld to penetrate completely through the base material, creating a hole. This can happen if the welding parameters are not appropriately adjusted for the material thickness.
- Effects on Weld Quality: Burn-through can severely weaken the weld and compromise the structural integrity of the joint.
- Prevention and Mitigation Techniques: To prevent burn-through, welders should select suitable welding parameters, such as the right heat input and travel speed, based on the material thickness. They should also use appropriate filler materials and welding techniques to control the heat.
Weld Overlap
- Definition and Causes: Weld overlap occurs when successive weld passes overlap each other, creating an uneven and undesirable weld surface. This can happen due to improper welding techniques or inadequate joint preparation.
- Effects on Weld Quality: Weld overlap can weaken the weld and lead to uneven distribution of stresses. It may also result in an unsightly weld appearance.
- Prevention and Mitigation Techniques: Welders should follow proper welding techniques, maintain a consistent travel speed, and ensure that each pass slightly overlaps the previous one to achieve a smooth and even weld. Adequate joint preparation is also essential to prevent this defect.
Arc Strikes
- Definition and Causes: Arc strikes occur when the welding arc inadvertently strikes a surface other than the intended weld joint. This can happen due to incorrect electrode positioning or poor workpiece grounding.
- Effects on Weld Quality: Arc strikes can create defects, such as surface cracks or heat-affected zones, on unintended areas of the workpiece.
- Prevention and Mitigation Techniques: To prevent arc strikes, welders should ensure proper electrode positioning and maintain good workpiece grounding. Welding curtains or shields can also be used to protect adjacent surfaces from accidental contact with the arc.
Case Studies and Examples
Welding defects can have far-reaching consequences in various industries, affecting structural integrity, safety, and economic costs. Let’s explore real-world case studies and examples of welding defects to understand the gravity of these issues and the lessons learned.
Real-World Examples of Welding Defects
- The Hyatt Regency Walkway Collapse (1981):
- In this tragic case, the collapse of two walkways at the Hyatt Regency Hotel in Kansas City resulted in 114 fatalities and numerous injuries. The primary cause was the improper welding of the walkway supports, leading to a catastrophic failure. This disaster underscores the importance of strict adherence to welding standards and quality control.
- Space Shuttle Challenger Disaster (1986):
- The Space Shuttle Challenger disaster was caused by the failure of an O-ring seal in one of the solid rocket boosters. While not directly related to welding, this event highlights the importance of materials integrity and the rigorous testing and inspection of critical components in aerospace, where welding defects can be equally detrimental.
Highlighting the Consequences of Defects in Different Industries
- Construction Industry:
- In the construction industry, welding defects can lead to building collapses, endangering lives and causing massive financial losses. For instance, the collapse of the Quebec Bridge in 1907 resulted from welding defects in crucial components, leading to a significant loss of life.
- Automotive Industry:
- Welding defects in the automotive sector can compromise vehicle safety. For example, faulty welds in the Ford Pinto’s fuel tank contributed to explosions and deaths during rear-end collisions in the 1970s. This incident emphasizes the need for stringent quality control in automotive manufacturing.
- Aerospace Industry:
- The aerospace industry demands the highest level of quality and precision. In 2003, the Space Shuttle Columbia disintegrated upon re-entry into Earth’s atmosphere due to damage to the shuttle’s thermal protection system caused by foam insulation. While not a welding defect per se, this tragedy highlights the catastrophic consequences of any manufacturing defect in aerospace.
Lessons Learned from These Cases
- Adherence to Standards:
- These case studies emphasize the critical importance of adhering to industry standards and best practices. Deviating from established procedures can have dire consequences.
- Quality Control and Inspection:
- Rigorous quality control and inspection procedures are paramount to detect and prevent welding defects. Regular inspections and testing can identify potential issues before they become catastrophic.
- Materials Integrity:
- The integrity of materials, including the base metals and welding consumables, is fundamental. Ensuring the quality and compatibility of materials is essential in preventing defects.
- Continuous Improvement:
- These cases underscore the need for continuous improvement in welding techniques, materials, and quality control processes. Lessons learned from past failures drive innovation and enhance safety.
Inspection and Quality Control
In the world of welding, ensuring the quality of welds is of paramount importance. Inspection and quality control measures are essential to detect welding defects early, ensure structural integrity, and maintain safety standards. This section discusses non-destructive testing methods, the importance of quality control in welding, and the role of welding codes and standards.
Non-Destructive Testing Methods
- X-ray Inspection:
- X-ray testing involves passing X-rays through a weld to create an image that reveals internal defects like cracks and porosity. It is highly effective for detecting subsurface defects and assessing weld quality in critical applications, such as aerospace and nuclear industries.
- Ultrasonic Testing:
- Ultrasonic testing uses high-frequency sound waves to detect internal defects in welds. It is particularly useful for identifying cracks, voids, and inclusions. Ultrasonic testing is versatile and widely used in various industries, including oil and gas, construction, and manufacturing.
- Magnetic Particle Testing:
- Magnetic particle testing is employed to find surface and near-surface defects. It involves applying magnetic particles to the surface of the weld, and any discontinuities or defects create visible indications when the particles are attracted to them. This method is commonly used in the automotive and construction industries.
- Dye Penetrant Inspection:
- Dye penetrant testing is suitable for identifying surface defects. A colored liquid penetrant is applied to the weld surface, and it seeps into any surface cracks or discontinuities. After excess dye is removed, a developer is applied, making the defects visible. This method is cost-effective and used in various applications.
Importance of Quality Control in Welding
Quality control in welding is essential for several reasons:
- Safety: Ensuring the structural integrity of welded components is crucial for safety, especially in industries like aerospace, automotive, and construction. Quality control helps identify potential defects that could compromise safety.
- Cost Efficiency: Welding defects can be costly to rectify. Detecting and addressing defects early in the welding process saves time and resources.
- Regulatory Compliance: Many industries are subject to strict regulations and standards. Quality control helps companies comply with these standards and avoid legal issues.
- Customer Satisfaction: Providing high-quality welds enhances the reputation of manufacturers and contractors. Satisfied customers are more likely to return for future projects.
Role of Welding Codes and Standards
Welding codes and standards play a pivotal role in ensuring quality and safety in welding. These codes are established by organizations like the American Welding Society (AWS) and the International Organization for Standardization (ISO). Their roles include:
- Setting Standards: Welding codes define the standards and requirements for welding processes, materials, and inspections. They provide guidelines for welder qualifications and procedures.
- Safety Assurance: Codes and standards prioritize safety by specifying acceptable welding practices and materials that meet minimum safety requirements.
- Quality Control: These documents promote quality control through procedures, inspections, and testing methods that ensure the integrity of welds.
- Interoperability: Welding codes ensure that welding processes and materials are compatible across different manufacturers and industries.
- Continuous Improvement: Codes are updated periodically to incorporate new technologies and best practices, promoting continuous improvement in welding processes.
Welder Training and Certification
Welding is a highly skilled profession that demands precision, knowledge, and expertise. In this section, we will explore the significance of proper training and certification for welders, provide an overview of welding certification programs, and emphasize the importance of continuous education and skill development in the field.
Significance of Proper Training and Certification
- Safety: Proper training ensures that welders understand the safety protocols and precautions necessary to protect themselves and others during the welding process. Untrained welders are more likely to engage in unsafe practices.
- Quality: Certified welders are trained to produce high-quality welds that meet industry standards. This is crucial for maintaining the structural integrity and reliability of welded components.
- Efficiency: Properly trained welders are more efficient, leading to reduced production costs and faster project completion. They waste fewer materials and spend less time correcting mistakes.
- Compliance: Many industries and regulatory bodies require certified welders to ensure that welding work adheres to specific codes and standards. Compliance is essential for industries such as aerospace, construction, and manufacturing.
- Career Opportunities: Certification can open doors to better job opportunities and higher earning potential for welders. Employers often prefer or require certified welders due to the assurance of their skills and knowledge.
- Professionalism: Certification reflects a commitment to professionalism and a dedication to the craft of welding. It instills a sense of pride in welders and enhances their reputation in the industry.
Overview of Welding Certification Programs
Welding certification programs are designed to assess a welder’s skills and knowledge, ensuring they meet specific industry standards. Here’s an overview of how these programs typically work:
- Training: Welders undergo formal training programs, often offered by technical schools, vocational institutions, or apprenticeship programs. These programs cover welding techniques, safety procedures, and relevant theory.
- Hands-On Welding Tests: Welders must pass hands-on welding tests that simulate real-world welding scenarios. These tests evaluate their ability to produce quality welds using different welding processes (e.g., MIG, TIG, Stick) and materials.
- Written Examinations: In addition to practical tests, welders may be required to pass written exams to demonstrate their knowledge of welding theory, safety practices, and relevant codes and standards.
- Certification Bodies: Welding certification is typically issued by recognized organizations such as the American Welding Society (AWS) or the International Organization for Standardization (ISO). These organizations set the criteria for certification and conduct assessments.
- Renewal: Welding certifications are usually valid for a specific period (e.g., 2 to 5 years) and may require renewal through retesting or continuing education to ensure that welders stay current with industry developments.
Continuous Education and Skill Development
The welding industry is continually evolving with new technologies, materials, and techniques. Therefore, continuous education and skill development are crucial for welders:
- Advanced Training: Welders can pursue advanced training in specialized welding processes, such as robotic welding or underwater welding, to expand their skill set.
- Technology Adaptation: Staying updated with the latest welding technologies, such as digital welding systems and automation, is essential to remain competitive in the field.
- Professional Development: Engaging in professional organizations, attending conferences, and participating in workshops can provide opportunities for networking and learning from industry experts.
- Code and Standard Updates: As welding codes and standards evolve, welders must stay informed and adapt their practices accordingly to ensure compliance.
- Cross-Training: Learning about related fields like metallurgy, materials science, and engineering can enhance a welder’s understanding of the welding process and improve problem-solving skills.
FAQs
What is the main cause of welding defects?
Welding defects are primarily caused by factors like improper welding technique, contaminated materials, incorrect settings, and inadequate pre-weld preparation.
How can I prevent welding defects?
Preventing welding defects involves maintaining cleanliness, using proper welding techniques, controlling welding parameters, and ensuring the right equipment and materials are used.
Can welding defects be repaired?
In some cases, welding defects can be repaired by removing the flawed weld and re-welding the joint correctly. However, prevention is always preferable to repairs.
Are welding defects a safety concern?
Yes, welding defects can compromise the structural integrity of welded components, potentially leading to accidents and injuries. Ensuring defect-free welds is essential for safety.
What are the visual signs of welding defects?
Visual signs of welding defects include irregularities in the weld bead, cracks, porosity, spatter, and uneven fusion between the weld metal and base metal.
How can I improve my welding skills to reduce defects?
Improving your welding skills requires practice, training, and a thorough understanding of welding processes. Consider taking welding courses and seeking guidance from experienced welders.
Conclusion
In the world of welding, defects can be the Achilles’ heel of even the most skilled welders. However, with the right knowledge, techniques, and equipment, these dreaded defects can be prevented and rectified. Porosity, cracking, incomplete fusion, undercutting, and lack of penetration are challenges that can be overcome through diligence and expertise.
Welding is not merely a technical skill; it’s an art that requires precision and attention to detail. By staying vigilant and continually honing their craft, welders can ensure that their welds are not plagued by these defects. As the saying goes, “A well-welded joint is a strong joint,” and mastering the art of welding is the key to success in the world of fabrication and construction.