Friction Stir Welding and Process
Introduction
Friction Stir Welding (FSW) is a solid-state welding process that was developed in the 1990s. It involves the joining of metals without melting the material, and instead uses friction and pressure to create a strong bond between the two pieces. FSW has become an increasingly popular welding technique in the manufacturing industry due to its many benefits, including high-quality welds, minimal distortions, and superior mechanical properties.
The history of FSW dates back to 1991, when it was first patented by The Welding Institute in the UK. The process was originally developed for joining aluminum alloys, but has since been successfully applied to a variety of materials, including copper, titanium, and steel. Since its development, FSW has undergone continuous improvements and has become a widely adopted technique in various industries.
FSW has become increasingly important in the manufacturing industry due to its ability to produce high-quality welds that are consistent and free of defects. It also offers several advantages over traditional welding techniques, such as reduced heat input, minimal material distortion, and the ability to weld dissimilar materials. These advantages have made FSW a popular choice for manufacturing a wide range of products, from automobiles and aircraft to ships and rail components.
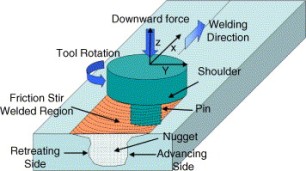
How FSW Works
Explanation of the FSW process:
FSW is a solid-state welding process that involves the joining of two metals by creating a plasticized region between them without melting the material. The process begins by clamping the two materials to be welded together. The FSW machine then uses a rotating tool made of a hard material, such as tungsten carbide, to apply pressure and friction to the joint. As the tool rotates, it moves along the joint line, creating a plasticized region between the two metals. The tool then moves through the joint, pushing the plasticized material to the back of the joint, where it cools and solidifies, creating a strong and consistent weld.
Components of the FSW machine:
The FSW machine consists of several components that are necessary for the welding process. The machine includes a clamping system to hold the two materials in place, a rotating tool to create friction and pressure, and a control system to monitor and adjust the temperature, force, and speed of the welding process. The machine also has a coolant system to maintain the temperature of the material during the welding process.
Temperature and force parameters in FSW:
The FSW process involves precise temperature and force parameters to achieve the desired weld quality. The temperature is controlled through the rotation speed of the tool, the force applied to the joint, and the cooling rate of the material. The force applied to the joint is determined by the properties of the materials being welded, and the desired quality of the weld. The speed of the tool is also a crucial factor, as it affects the amount of heat generated during the process. These parameters are monitored and controlled by the machine’s control system to ensure consistent and high-quality welds.
Advantages of FSW
High-quality and consistent welds: FSW produces high-quality welds that are consistent and repeatable. This is because FSW does not involve melting the materials, which eliminates the risk of porosity, voids, or cracks that can occur with traditional welding techniques.
Superior mechanical properties: FSW produces welds with superior mechanical properties, including higher tensile strength, better fatigue resistance, and improved toughness. This is because FSW creates a homogeneous microstructure in the weld, resulting in improved properties compared to other welding techniques.
Minimal defects and distortions: FSW produces minimal defects and distortions in the material being welded, which reduces the need for post-welding processing. This is because FSW generates less heat and causes less thermal stress on the materials being welded, resulting in minimal deformation or warping.
Ability to weld dissimilar materials: FSW has the ability to join dissimilar materials that are difficult or impossible to weld with traditional welding techniques. This is because FSW does not require melting the material, and can therefore join materials with different melting points, such as aluminum and copper.
Applications of FSW
High-quality and consistent welds:
FSW produces high-quality welds that are consistent and repeatable. This is because FSW does not involve melting the materials, which eliminates the risk of porosity, voids, or cracks that can occur with traditional welding techniques.
Superior mechanical properties:
FSW produces welds with superior mechanical properties, including higher tensile strength, better fatigue resistance, and improved toughness. This is because FSW creates a homogeneous microstructure in the weld, resulting in improved properties compared to other welding techniques.
Minimal defects and distortions:
FSW produces minimal defects and distortions in the material being welded, which reduces the need for post-welding processing. This is because FSW generates less heat and causes less thermal stress on the welded materials, resulting in minimal deformation or warping.
Ability to weld dissimilar materials:
FSW has the ability to join dissimilar materials that are difficult or impossible to weld with traditional welding techniques. This is because FSW does not require melting the material, and can therefore join materials with different melting points, such as aluminum and copper.
Challenges and Limitations of FSW
Limited joint thickness range: FSW is limited in its ability to weld materials with a large joint thickness. The thickness of the joint that can be welded is typically limited to 25mm or less, making it difficult to use for welding thicker materials.
High cost of equipment: The equipment required for FSW is relatively expensive compared to traditional welding equipment. This can make it difficult for smaller companies or those with limited budgets to adopt the technology.
Limited weldability of some materials: FSW is not suitable for welding all types of materials. Some materials, such as those with low melting points, may not be suitable for FSW. Additionally, some materials may not weld well due to differences in their physical and chemical properties.
Limited ability to weld complex geometries: FSW is limited in its ability to weld complex geometries or parts with intricate shapes. This is because FSW requires a straight line or a simple curve to move the tool along the joint line.
Future of FSW
Current research and development efforts: There is ongoing research and development in the field of FSW to improve its capabilities and expand its applications. Some of the areas of research include developing new FSW tools, optimizing FSW parameters for different materials and joint configurations, and exploring the use of FSW for additive manufacturing.
Potential for new applications: FSW has the potential to be used in new applications beyond its current uses in the automotive, aerospace, shipbuilding, and rail industries. For example, FSW could be used in the construction industry to weld large steel or aluminum structures. FSW could also be used to join dissimilar materials in electronic devices or medical implants.
Advancements in FSW equipment: Advancements in FSW equipment have already led to improvements in the speed, accuracy, and efficiency of the welding process. For example, new FSW machines with robotic arms and advanced sensors can perform complex welds on a variety of materials. Additionally, improvements in FSW tool materials and designs have increased the lifespan of the tools and reduced tool wear during welding.
FAQs
What is friction stir welding process?
Friction Stir Welding (FSW) is a solid-state welding process that uses a rotating tool to heat and stir the materials being joined, forming a solid-state weld without melting the materials. FSW is used to join a variety of materials, including aluminum, copper, titanium, and even some plastics.
What are the uses of friction stir welding?
FSW is used in a variety of industries, including automotive, aerospace, shipbuilding, and rail industries. It is used to join lightweight and high-strength materials that are difficult to weld with traditional welding techniques. FSW is also used in the production of heat exchangers, pressure vessels, and pipes.
What is the difference between friction and friction stir welding?
Friction welding and Friction Stir Welding (FSW) are two different welding techniques. In friction welding, the materials being joined are heated by friction and then pressed together to form a weld. In FSW, a rotating tool heats and stirs the materials being joined, forming a solid-state weld without melting the materials.
Is friction stir welding strong?
Yes, FSW produces strong and high-quality welds with superior mechanical properties. The welds produced by FSW are typically stronger and more durable than those produced by traditional welding techniques.
What are the three stages of the FSW process?
The FSW process consists of three stages: (1) plunge stage, where the tool is plunged into the materials being joined, (2) stirring stage, where the tool is moved along the joint line, and (3) exit stage, where the tool is withdrawn from the materials.
Which tool is used in friction stir welding?
A specially designed rotating tool made from a hard and durable material, such as tungsten carbide, is used in FSW. The tool has a pin that is inserted into the materials being joined and a shoulder that rides along the surface of the materials.
What speed is friction welding?
The speed of the rotating tool used in FSW depends on several factors, such as the material being welded, the joint configuration, and the desired properties of the weld. Typically, the tool speed ranges from 500 to 2000 revolutions per minute (RPM).
What is the maximum thickness of friction stir welding?
The maximum thickness of materials that can be joined by FSW depends on several factors, including the material being joined, the tool design, and the equipment being used. However, FSW can typically join materials up to 25mm thick or more.
What is the temperature of friction stir welding?
The temperature generated during FSW depends on several factors, including the material being joined, the tool design, and the equipment being used. However, the temperature typically ranges from 50% to 80% of the melting point of the material being joined.
What are the 4 variants of friction stir welding?
The four variants of FSW are
- stationary shoulder FSW
- adjustable pin tool FSW bobbin tool FSW, and double-sided FSW. These variants differ in the design of the tool and the welding process.
Conclusion
In summary, Friction Stir Welding (FSW) is a solid-state welding process that offers numerous benefits over traditional welding techniques. FSW creates high-quality and consistent welds, with superior mechanical properties, minimal defects and distortions, and the ability to weld dissimilar materials. FSW is important in modern manufacturing due to its ability to join lightweight and high-strength materials that are difficult to weld with traditional welding techniques. FSW is widely used in the automotive, aerospace, shipbuilding, and rail industries, and has the potential to be used in new applications beyond these industries. The future prospects of FSW in manufacturing look promising, with ongoing research and development efforts to improve its capabilities and expand its applications. Advancements in FSW equipment will likely lead to even more improvements in the welding process, making it an increasingly valuable technology in the manufacturing industry.