Laser Cutting vs Plasma Cutting
Introduction
Cutting processes play a critical role in many industries, including manufacturing, construction, and metalworking/welding. These processes involve the removal of unwanted material from a workpiece to achieve a desired shape or size. There are several cutting methods available, including laser cutting and plasma cutting, both of which are widely used in the industry. Both laser cutting and plasma cutting are commonly used methods in welding for cutting through various types of metals, but they differ in terms of their process and capabilities.
Laser cutting is a non-contact cutting method that uses a high-powered laser beam to cut through a variety of materials, such as metal, plastic, and wood. Laser cutting offers several advantages, including high precision, speed, and versatility. It is commonly used in industries that require high levels of accuracy and detail, such as aerospace, automotive, and electronics.
Plasma cutting, on the other hand, uses a high-temperature plasma arc to melt and cut through metal. It is a versatile cutting method that can cut through a range of materials, including steel, aluminum, and copper. Plasma cutting is commonly used in industries that require fast and efficient cutting, such as metal fabrication, automotive repair, and construction.
The purpose of this article is to compare laser cutting and plasma cutting, highlighting the pros and cons of each method, and helping readers decide which method is best suited for their specific needs. By understanding the differences between these two methods, readers can make informed decisions about which cutting method to use for their particular applications.
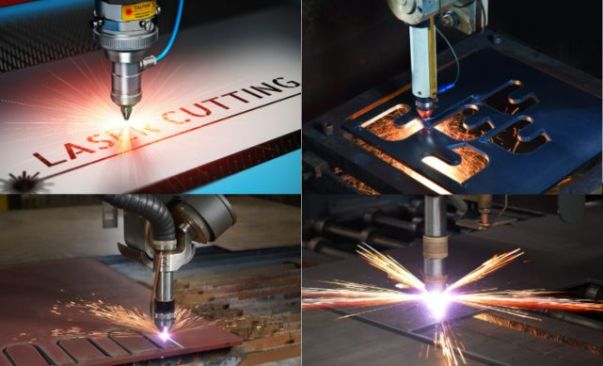
Laser Cutting
Laser cutting is a manufacturing process that uses a high-powered laser to cut materials with extreme precision. The laser is directed by a computer-controlled system that guides the laser beam along the material to be cut, vaporizing or melting the material to create a clean, precise cut.
One of the primary advantages of laser cutting is its precision. Laser cutting can achieve very small cuts with high accuracy, making it ideal for intricate designs and detailed work. Additionally, laser cutting is a very fast process, enabling quick production and turnaround times.
Another advantage of laser cutting is its versatility. Laser cutting can be used on a wide variety of materials, including metals, plastics, wood, and fabrics. This makes it a popular choice in many industries, from manufacturing to fashion.
Laser cutting is also a very clean process. The laser beam vaporizes or melts the material, leaving a clean edge with minimal debris or residue. This makes it ideal for applications where cleanliness is important, such as in the medical industry.
However, there are also limitations to laser cutting. One limitation is the cost. Laser cutting machines can be expensive to purchase and maintain, making it a less practical choice for some businesses or individuals.
Another limitation is material thickness. While laser cutting can be used on a variety of materials, the thickness of the material being cut is limited. Laser cutting is most effective on thinner materials, and may not be suitable for cutting thicker materials.
Finally, laser cutting can be a complex process that requires specialized training and knowledge. Operating a laser cutting machine requires skill and experience to ensure the desired outcome is achieved.
Plasma Cutting
Plasma cutting is a process that involves using a high-velocity jet of ionized gas, or plasma, to cut through conductive materials such as steel, aluminum, copper, and other metals. The plasma cutter creates a high-intensity electric arc that passes through a nozzle, causing the gas to ionize and form plasma. The plasma is then directed towards the material being cut, melting it and blowing away the molten metal to create a clean, precise cut.
One of the main advantages of plasma cutting is its affordability. Plasma cutters are generally less expensive than other cutting tools, such as laser cutters or water jet cutters, making it a more accessible option for small businesses and DIY enthusiasts. Another advantage of plasma cutting is its ability to cut through thicker materials, up to several inches in thickness, with relative ease. Plasma cutting is also known for its speed, allowing for quick and efficient cutting of materials.
However, plasma cutting does have some limitations. One limitation is lower precision compared to other cutting methods, such as laser cutting. The edges of the cut may also be messier, with more slag and debris left behind. Additionally, plasma cutting can create potential hazards, including exposure to high temperatures, electrical shock, and fumes. Proper safety precautions should be taken when using a plasma cutter to minimize these risks.
Safety Considerations in Laser Cutting
Here are some important safety considerations for laser cutting:
Laser Beam Hazards
The high power laser beam used in laser cutting can cause serious injury or even blindness if it comes into contact with unprotected eyes or skin. It’s essential to ensure that all personnel in the work area wear appropriate eye and skin protection, such as safety glasses or face shields, to prevent exposure to the laser beam.
Fire Hazards
The laser beam can also ignite materials that are flammable or combustible, such as paper or fabric, so it’s important to ensure that the work area is clear of any such materials.
Fumes and Smoke
Laser cutting can produce fumes and smoke that can be hazardous if inhaled. It’s essential to have adequate ventilation in the work area to remove these fumes and smoke.
Laser cutting machines require a significant amount of electrical power to operate. Proper grounding and electrical safety protocols must be followed to prevent electric shock and other electrical hazards.
Safety Considerations in Plasma Cutting
Here are some important safety considerations for laser cutting:
Plasma Arc Hazards
The plasma arc used in plasma cutting can reach temperatures of up to 30,000 degrees Fahrenheit, which can cause severe burns if it comes into contact with unprotected skin. It’s essential to wear appropriate protective clothing, such as flame-resistant gloves and aprons, to prevent burns.
Ultraviolet and Infrared Radiation
The plasma cutter can also generate ultraviolet and infrared radiation, which can be harmful if not properly shielded. Proper protective eyewear and clothing must be worn to prevent exposure to these types of radiation.
Fire Hazards
Like laser cutting, plasma cutting can also ignite flammable or combustible materials, so it’s important to ensure that the work area is clear of any such materials.
Electrical Safety
Plasma cutting requires the use of high voltage electricity, which can cause electric shock if proper safety protocols are not followed. It’s essential to ensure that the equipment is properly grounded and that all safety procedures are followed to prevent electric shock.
Comparing the Two Cutting Methods
Cutting speed and efficiency
- Laser cutting is generally faster and more efficient than waterjet cutting, especially for thin materials.
- Waterjet cutting is slower but more efficient for thicker and harder materials, such as metal.
Cutting precision and accuracy
- Laser cutting has a higher level of precision and accuracy due to the narrow beam width of the laser.
- Waterjet cutting may have slightly lower precision due to the width of the waterjet stream, but it can compensate for this with its ability to make angled cuts and cut a wider range of materials.
Costs and suitable materials
- Laser cutting equipment is typically more expensive than waterjet cutting equipment, and laser cutting may require additional ventilation and safety measures.
- Waterjet cutting equipment is generally more affordable and can cut a wider range of materials, including materials that are not suitable for laser cutting, such as glass and some composites.
Maintenance requirements and safety considerations
- Both methods require regular maintenance to keep the equipment in good working condition, but waterjet cutting requires more frequent replacement of components such as nozzles and abrasive materials.
- Laser cutting poses a higher risk of fire and requires additional safety measures to prevent accidents, while waterjet cutting involves high-pressure water and abrasive materials, which require safety measures to protect operators from injury.
FAQs
What is the difference between laser and plasma?
Laser cutting uses a focused beam of light to cut materials, while plasma cutting uses a high-temperature plasma arc to melt and cut materials. Laser cutting is typically more precise, but plasma cutting can cut through thicker materials.
What is the difference between plasma and fiber laser?
A fiber laser uses a fiber-optic cable to deliver the laser beam to the cutting head, while plasma cutting uses a high-temperature plasma arc to cut materials. Fiber lasers are typically more precise and faster than plasma cutters, but plasma cutters can handle thicker materials.
What are 2 disadvantages of laser cutting?
Two disadvantages of laser cutting are that it can be expensive to operate and maintain, and it may cause thermal damage to some materials.
Which is better laser cutter or plasma cutter?
It depends on the specific application and materials being cut. Laser cutters are generally better for thinner materials that require high precision, while plasma cutters are better for thicker materials that require faster cutting speeds.
What is laser cutting process?
Laser cutting involves using a focused beam of light to melt, burn, or vaporize materials, creating a clean and precise cut. The process is controlled by a computer program and can be used on a variety of materials, including metal, wood, and plastic.
What are 3 main types of lasers?
The three main types of lasers are solid-state lasers, gas lasers, and semiconductor lasers.
Which is stronger plasma or laser?
Plasma cutters are typically better for cutting thicker materials, while laser cutters are better for thinner materials that require higher precision.
What are three types of lasers?
The three types of lasers are solid-state lasers, gas lasers, and semiconductor lasers.
What are 2 advantages of laser cutter?
Two advantages of laser cutting are that it produces a clean and precise cut, and it can be used on a variety of materials.
What are 5 advantages of using a laser cutter?
Five advantages of using a laser cutter are:
- High precision cutting
- Minimal material waste
- Versatility
- Ability to cut complex shapes
- Non-contact cutting process
What are the two types of plasma cutters?
The two types of plasma cutters are manual plasma cutters and CNC (Computer Numerical Control) plasma cutters.
Conclusion
In conclusion, the choice between laser cutting and plasma cutting methods depends on various factors such as the specific application, material type, thickness, required precision, cutting speed, equipment cost, maintenance requirements, and safety considerations. Laser cutting is typically more precise and faster, producing a clean cut on thin materials with minimal waste. However, it may cause thermal damage to some materials and can be expensive to operate and maintain. On the other hand, plasma cutting can handle thicker materials and is generally faster than laser cutting. It is also more cost-effective for larger-scale projects. However, plasma cutting may produce rougher cuts and is less precise than laser cutting. It’s important to carefully consider the advantages and disadvantages of each method to determine which one is best suited for the specific application and materials being cut. Ultimately, the choice between laser cutting and plasma cutting will depend on the specific requirements of the job and the materials involved.