What is Magnetic Pulse Welding?
Introduction
Magnetic Pulse Welding (MPW) is a solid-state welding process that utilizes high-velocity magnetic forces to join metal components. It involves the generation of a high-intensity magnetic field that rapidly accelerates one workpiece towards another, creating a collision and a strong metallurgical bond between them.
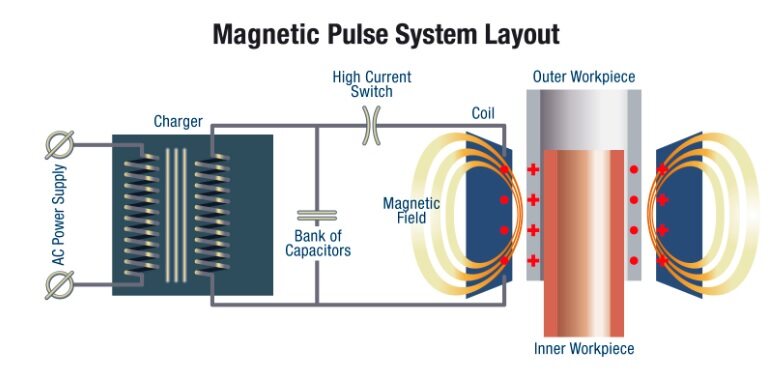
Brief overview of its applications and advantages
Magnetic Pulse Welding has gained recognition in various industries due to its unique advantages and applications. Some key points include:
- Automotive Industry: MPW is widely used in the automotive industry for joining dissimilar metals and lightweight materials. It enables the production of strong and lightweight structures, improving fuel efficiency and reducing vehicle weight.
- Aerospace and Aviation Sector: MPW finds applications in the aerospace and aviation sector for joining critical components, such as airframe structures, engine components, and turbine blades. It provides a reliable and efficient joining method without introducing heat-affected zones or compromising material properties.
- Electrical and Electronics Manufacturing: MPW is utilized in the electrical and electronics industry for joining conductive materials, such as copper and aluminum. It enables the production of high-quality electrical connections, such as busbars and electrical contacts, ensuring efficient electrical conductivity.
- Medical Device Industry: MPW is employed in the medical device industry for joining biocompatible materials, such as titanium and stainless steel. It allows for the production of strong and clean joints without the need for additional fillers or adhesives, ensuring the integrity and safety of medical devices.
The advantages of Magnetic Pulse Welding include:
- Rapid and localized heating: MPW provides fast heating through the rapid collision between workpieces, allowing for precise control of the heat-affected zone and minimizing thermal distortion.
- No need for additional heat sources: MPW does not require the use of external heat sources, reducing energy consumption and simplifying the welding process.
- Minimal heat-affected zone: MPW is a solid-state welding technique, which means it does not introduce molten phases or significant heat-affected zones, resulting in minimal material distortion and preserving material properties.
- Versatility in joining dissimilar materials: MPW can join materials with significant differences in composition, such as aluminum to steel or copper to aluminum, making it suitable for joining dissimilar metals and composites.
Principle of Magnetic Pulse Welding
Explanation of the basic principle
The basic principle of Magnetic Pulse Welding (MPW) involves the generation of a high-intensity magnetic field that accelerates one workpiece towards another at a high velocity, resulting in a collision and the formation of a metallurgical bond. The process can be summarized as follows:
- Magnetic Field Generation: An electromagnetic coil, known as a magnetic pulse generator, is positioned around one of the workpieces. When a high-voltage capacitor discharges through the coil, it creates a strong, rapidly changing magnetic field.
- Magnetic Field Interaction: The magnetic field induces electric currents, known as eddy currents, in the workpiece that is within its influence. These eddy currents interact with the magnetic field, generating Lorentz forces.
- Magnetic Forces and Impact: The Lorentz forces created by the interaction of the magnetic field and the eddy currents result in repulsion and attraction forces between the two workpieces. The repulsion forces rapidly accelerate one workpiece towards the other, leading to a high-velocity collision.
- Collision and Bond Formation: Upon collision, the kinetic energy of the colliding workpiece is converted into plastic deformation, heat, and mechanical work. The high pressure and localized heat soften and forge the materials together, forming a metallurgical bond.
Description of the equipment and components used
The equipment and components used in Magnetic Pulse Welding typically include:
- Magnetic Pulse Generator: The magnetic pulse generator is a high-voltage capacitor discharge system that generates a powerful, rapidly changing magnetic field. It consists of an electromagnetic coil and associated circuitry to produce the necessary magnetic pulse.
- Workpiece Fixturing: Fixturing components, such as clamps or jigs, are used to securely hold the workpieces in place during the welding process. They ensure proper alignment and positioning for effective collision and bonding.
- Energy Storage System: An energy storage system, such as a high-voltage capacitor bank, is used to store and discharge the electrical energy into the magnetic pulse generator. It provides the necessary energy for creating the intense magnetic field.
Role of magnetic forces and impact velocity in the process
In Magnetic Pulse Welding, the magnetic forces and impact velocity play crucial roles in the welding process:
- Magnetic Forces: The rapidly changing magnetic field induces eddy currents in the workpieces, creating repulsion and attraction forces. These magnetic forces accelerate one workpiece towards the other, allowing for a high-velocity collision and subsequent deformation and bonding.
- Impact Velocity: The high-velocity collision between the workpieces generates heat and plastic deformation. The impact velocity influences the energy transfer, heat generation, and material flow during the collision, impacting the quality and characteristics of the resulting weld.
Process Steps
Pre-welding Preparation
- Selection of suitable materials for magnetic pulse welding: The selection of materials is crucial for successful magnetic pulse welding. The chosen materials should exhibit good electrical conductivity and be compatible for metallurgical bonding. Commonly welded materials include various metals and alloys such as aluminum, copper, steel, and their combinations.
- Surface preparation and cleaning of workpieces: Prior to welding, the surfaces of the workpieces need to be prepared and cleaned. Any contaminants, such as dirt, grease, or oxide layers, should be removed to ensure proper bonding. Surface preparation methods may include grinding, sanding, or chemical cleaning.
- Fixturing and alignment of the components: The workpieces are securely fixtured and aligned using clamps, jigs, or other means. Proper alignment ensures that the collision occurs at the desired joint interface, facilitating effective bonding. Fixturing also helps maintain stability and alignment during the welding process.
Welding Phase
- Activation of the equipment and setup of welding parameters: The magnetic pulse welding equipment is activated, and the necessary parameters are set. This includes adjusting the energy storage system, charging voltage, discharge time, and other relevant parameters based on the material properties and desired weld characteristics.
- Generation of a high-intensity magnetic field: The energy storage system discharges the stored energy into the magnetic pulse generator, creating a strong and rapidly changing magnetic field. The electromagnetic coil induces eddy currents in the workpieces, initiating the welding process.
- Application of a high-velocity magnetic pulse to the workpieces: The intense magnetic field generates attractive and repulsive forces between the workpieces, leading to a high-velocity collision. The impact velocity and pressure cause plastic deformation, localized heating, and material flow, facilitating the formation of a metallurgical bond.
Solidification and Bonding
- Controlled deformation and solid-state bonding: After the collision, the workpieces experience controlled deformation and plastic flow, allowing the materials to intimately contact each other. The combination of pressure, heat, and mechanical work promotes diffusion and intermixing of atoms, resulting in a solid-state bond formation.
- Cooling and solidification of the welded joint: Upon completion of the welding phase, the joint is allowed to cool and solidify. The workpieces naturally cool down, and the metallurgical bond solidifies, resulting in a strong and durable welded joint.
Post-welding
- Inspection and testing of the weld quality: The welded joint undergoes inspection and testing to evaluate its quality and integrity. Visual inspection, non-destructive testing methods, and mechanical tests may be performed to assess the strength, integrity, and dimensional accuracy of the weld.
- Post-weld processing or finishing: Depending on the specific application or desired aesthetics, post-weld processing or finishing may be carried out. This can include processes such as grinding, polishing, or surface treatment to achieve the desired final appearance and functionality of the welded components.
Advantages and Limitations
Advantages of Magnetic Pulse Welding
- Rapid and localized heating: Magnetic Pulse Welding (MPW) offers rapid heating capabilities due to the high-velocity collision between workpieces. The intense collision generates localized heat, allowing for precise control over the heat-affected zone and minimizing thermal distortion.
- No need for additional heat sources: MPW eliminates the need for additional heat sources such as flames, lasers, or arcs. The welding process relies on the intense magnetic forces and impact generated by the high-velocity collision, making it a self-contained welding method.
- Minimal heat-affected zone: MPW is a solid-state welding process, meaning it does not involve the complete melting of the workpieces. As a result, there is minimal heat input and a limited heat-affected zone, preserving the material properties and reducing the risk of distortion.
- Versatility in joining dissimilar materials: MPW has the ability to join dissimilar materials, including metals with significant differences in composition or melting points. This versatility allows for the combination of different materials, expanding design possibilities and enabling the creation of lightweight structures.
Limitations and Considerations
- Limited thickness of workpieces: Magnetic Pulse Welding is most suitable for joining thin to moderately thick materials. Very thick workpieces may require multiple welding passes or alternative welding methods due to the limitations of the collision forces and energy transfer.
- Surface finish and cleanliness requirements: Proper surface preparation and cleanliness are crucial for achieving strong and reliable welds in MPW. The surfaces of the workpieces must be free from contaminants such as dirt, grease, or oxide layers, as they can hinder bonding and compromise weld quality.
- Equipment cost and complexity: The equipment required for MPW can be relatively costly and complex. It typically involves specialized electromagnetic coils, high-voltage capacitors, energy storage systems, and associated control systems. The setup and operation of the equipment may require skilled personnel and adequate safety measures.
Applications of Magnetic Pulse Welding
Automotive Industry
MPW finds extensive application in the automotive industry for joining various components. Some notable applications include:
- Lightweight structures: MPW is used to join dissimilar materials, such as aluminum to steel, for lightweight vehicle structures, resulting in improved fuel efficiency and reduced emissions.
- Battery manufacturing: MPW is employed in the assembly of battery packs for electric vehicles, ensuring secure connections between battery cells and enhancing overall performance.
- Engine components: MPW is used for joining engine components, such as valves, pistons, and connecting rods, ensuring reliable and high-strength assemblies.
Aerospace and Aviation Sector
The aerospace and aviation sector benefits from MPW due to its ability to join critical components without introducing heat-affected zones. Some applications include:
- Airframe structures: MPW is used to join various structural components, such as fuselage sections, wings, and brackets, providing strong and lightweight structures.
- Engine components: MPW is employed in joining turbine blades, compressor components, and other critical engine parts, ensuring secure and high-integrity assemblies.
- Fuel systems: MPW finds application in joining fuel system components, such as fuel lines and tanks, ensuring reliable and leak-free connections.
Electrical and Electronics Manufacturing
MPW is utilized in the electrical and electronics manufacturing industry for precise and efficient joining of conductive components. Examples of applications include:
- Electrical connectors: MPW is used to join electrical connectors, ensuring low-resistance electrical pathways and reliable connections in various electronic devices.
- Power electronics: MPW finds application in the assembly of power electronic components, such as inverters and converters, ensuring high-quality electrical connections and thermal management.
Medical Device Industry
MPW is employed in the medical device industry for joining biocompatible materials and achieving clean and reliable connections. Some applications include:
- Implantable devices: MPW is used to join components of implantable medical devices, such as orthopedic implants and cardiovascular devices, ensuring secure and biocompatible assemblies.
- Surgical instruments: MPW finds application in joining components of surgical instruments, such as forceps, scissors, and trocars, ensuring strong and precise connections.
Other Industrial Sectors
MPW has potential applications in various other industrial sectors, including:
- Consumer goods: MPW can be used in the assembly of consumer goods such as appliances, electronics, and sporting equipment, providing efficient and reliable joining of components.
- Oil and gas: MPW finds application in the assembly of oil and gas equipment, such as valves, connectors, and pipelines, ensuring durable and leak-free connections.
- Metal fabrication: MPW can be used in metal fabrication processes for joining components, such as panels, frames, and brackets, ensuring strong and efficient assemblies.
FAQs
What is magnetic pulse welding used for?
Magnetic Pulse Welding is used for joining metal components in various industries such as automotive, aerospace, electronics, and medical devices. It is particularly beneficial for joining dissimilar materials and creating strong, lightweight structures.
What is pulse welding process?
Pulse welding is a welding process that involves alternating the current between high and low levels during the welding operation. This pulsing action helps control the heat input, reduce spatter, and improve weld quality.
What is the difference between MIG and pulse welding?
MIG welding is a continuous process where a continuous wire electrode is fed into the welding puddle, while pulse welding refers to a welding process where the current is alternated between high and low levels. Pulse welding allows for better control over heat input and reduces the risk of overheating or distortion compared to continuous MIG welding.
What is magnetic pulse forming?
Magnetic Pulse Forming is a manufacturing process that uses electromagnetic forces to shape and form metal components. It involves subjecting the workpiece to a high-intensity magnetic field that induces controlled deformation, allowing for precise shaping of the metal.
What is the advantage of pulse MIG?
The advantage of pulse MIG welding is that it offers better control over heat input, reduces distortion, minimizes spatter, and improves weld quality compared to continuous MIG welding. It allows for a higher welding speed while maintaining a stable arc and better control over the weld pool.
What are the types of pulse welding?
There are various types of pulse welding techniques, including pulse MIG welding, pulse TIG welding, and pulse laser welding. Each technique utilizes pulsing action to control the heat input and improve the welding process.
Which welding is faster?
The speed of welding depends on various factors such as the welding technique, joint design, and material thickness. In general, processes like laser welding and electron beam welding are known for their high welding speeds. However, the specific welding speed can vary based on the application and the equipment used.
Does pulse welding need gas?
Yes, pulse welding typically requires the use of shielding gas to protect the welding area from atmospheric contamination. The type of gas used depends on the specific welding process and the material being welded.
What gas is used for pulse MIG welding?
For pulse MIG welding, commonly used shielding gases include argon, helium, and mixtures of argon with carbon dioxide (CO2) or oxygen. The specific gas or gas mixture used depends on the material being welded and the desired welding characteristics.
What are the two types of MIG?
The two main types of MIG welding are:
- Gas Metal Arc Welding (GMAW): This is the most common type of MIG welding, where a continuous wire electrode is fed through a welding gun, and an externally supplied shielding gas protects the weld pool.
- Flux-Cored Arc Welding (FCAW): Similar to MIG welding, but instead of using a solid wire electrode, it uses a flux-cored wire that contains flux inside. The flux provides the shielding gas and acts as a deoxidizer and arc stabilizer.
What are the 3 disadvantages of MIG welding?
Some disadvantages of MIG welding include:
- Higher equipment cost compared to other welding processes.
- Limited effectiveness on thick or heavy materials.
- Sensitivity to wind or drafts, requiring proper shielding gas coverage and positioning.
Why is CO2 used in MIG?
CO2 (carbon dioxide) is commonly used as a shielding gas in MIG welding because it is readily available, cost-effective, and provides good penetration and arc stability. It is especially suitable for welding carbon steels and low-alloy steels.
Conclusion
Magnetic Pulse Welding is a solid-state welding process that utilizes high-velocity magnetic forces to join metal components. It involves the generation of a high-intensity magnetic field, which accelerates one workpiece towards another, resulting in a collision and the formation of a metallurgical bond. Key points about MPW include its rapid and localized heating, minimal heat-affected zone, versatility in joining dissimilar materials, and its applications in various industries.
Magnetic Pulse Welding offers several benefits that make it a preferred joining method in different industries. These benefits include rapid and localized heating, no need for additional heat sources, minimal heat-affected zone, and the ability to join dissimilar materials. The potential applications of MPW are vast and include the automotive industry, aerospace and aviation sector, electrical and electronics manufacturing, medical device industry, and other industrial sectors.
The field of Magnetic Pulse Welding continues to evolve, driven by advancements in technology and industry demands. The field of MPW continues to evolve, with ongoing advancements aimed at process optimization, material expansion, automation, process monitoring, and sustainability. These advancements will contribute to the further growth and utilization of Magnetic Pulse Welding as a reliable and efficient joining method in the field of metal fabrication and manufacturing.