Planar Defects in Welding: Ensuring Strong, Flawless Joints
Welding is a critical process in the fabrication of various structures, and while it provides strength and durability, it’s not immune to imperfections. Planar defects in welding can compromise the integrity of joints, leading to structural issues and reduced service life. In this article, we’ll delve into the intricacies of planar defects, their types, causes, and most importantly, how to prevent them.
Introduction
Welding is the art of fusing materials together to create a strong, unified structure. However, even in the skilled hands of a welder, imperfections can arise, and among them, planar defects are a significant concern. Understanding these defects is crucial for ensuring the longevity and reliability of welded joints.
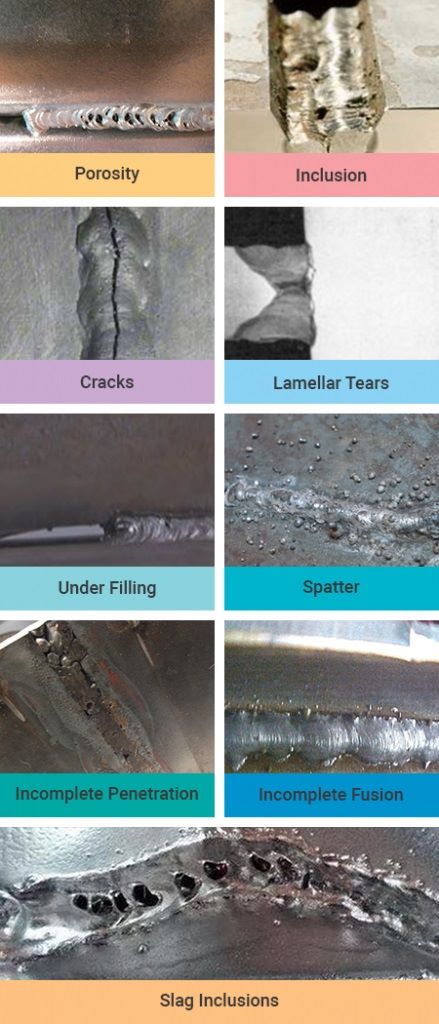
Understanding Planar Defects in Welding
Definition and Types
Planar defects, as the name suggests, are defects that occur along a plane within the welded material. The most common types include lack of fusion, incomplete penetration, and cracks. Each presents unique challenges in terms of detection and correction.
Causes of Planar Defects
Planar defects can result from a variety of factors, including improper welding techniques, material issues, and environmental conditions. Identifying the root causes is essential for effective prevention.
Common Planar Defects
Lack of Fusion
Lack of fusion occurs when the weld metal fails to fuse adequately with the base material or previous weld pass. This can lead to weak joints and a higher susceptibility to fractures.
Incomplete Penetration
Incomplete penetration happens when the weld metal doesn’t penetrate the entire thickness of the joint, leaving a void that compromises structural integrity.
Cracks
Cracks are one of the most detrimental planar defects. They can occur during welding or post-welding due to factors like stress, temperature variations, or poor material quality.
Impact of Planar Defects on Welded Joints
Structural Weakness
Planar defects create weak points in welded joints, reducing their load-bearing capacity and overall strength.
Corrosion Vulnerability
Defects often expose the interior of the weld to the environment, increasing the risk of corrosion and deterioration.
Reduced Service Life
Structures with planar defects are prone to premature failure, limiting their operational lifespan.
Detection and Inspection Methods
Visual Inspection
Visual inspection is the first line of defense against planar defects. Skilled inspectors can identify surface irregularities that may indicate underlying issues.
Non-Destructive Testing (NDT)
NDT methods, such as ultrasonic testing and magnetic particle inspection, provide in-depth analysis without compromising the integrity of the weld.
Radiographic Testing
X-ray and gamma-ray radiographic testing can reveal internal defects, offering a comprehensive view of the weld’s quality.
Prevention and Control Measures
Proper Welding Techniques
Adopting correct welding procedures, including appropriate heat levels and travel speeds, significantly reduces the risk of planar defects.
Quality Control Protocols
Implementing stringent quality control measures ensures that each weld meets specified standards and minimizes the chances of defects.
Welder Training and Certification
Well-trained and certified welders are less likely to introduce defects during the welding process.
Case Studies
Real-life examples of planar defects
Exploring actual cases where planar defects led to structural issues highlights the importance of vigilance and adherence to quality standards.
Importance of Quality Assurance in Welding
Industry Standards
Following established industry standards is paramount for producing welds that meet the required specifications.
Regulatory Compliance
Adhering to regulatory requirements ensures that welded structures are safe and reliable, meeting legal standards.
Future Trends in Welding Quality Assurance
Technological Advancements
Incorporating advanced technologies, such as robotic welding and artificial intelligence, is shaping the future of welding quality assurance.
Automation in Welding
Automated welding processes reduce the likelihood of human error, enhancing the overall quality of welds.
FAQs
Can planar defects be completely eliminated in welding?
While complete elimination is challenging, proper techniques and quality control measures can significantly minimize the occurrence of planar defects.
Are all planar defects visible through visual inspection?
No, some defects may require more advanced testing methods, such as radiographic testing, for accurate detection.
How often should welding equipment be inspected for potential defects?
Regular inspections, at least annually, are recommended to identify and address any potential issues promptly.
What role does material quality play in preventing planar defects?
High-quality materials reduce the likelihood of defects and contribute to the overall strength of the weld.
Is there ongoing research to further enhance welding quality assurance?
Yes, ongoing research and technological advancements continue to improve welding processes and quality assurance measures.
Conclusion
In the world of welding, understanding and addressing planar defects is crucial for building robust structures that stand the test of time. Through proper detection, prevention, and continuous improvement, we can ensure that welded joints meet and exceed expectations for strength and durability.