Self-Shielded Flux Cored Welding
Introduction
Self-Shielded Flux Cored Welding is a welding process that uses a continuous, tubular electrode filled with flux to join two pieces of metal together. Unlike traditional welding methods, this process does not require an external shielding gas to protect the weld pool from atmospheric contamination. The flux inside the electrode melts and creates a protective gas that shields the weld pool from oxygen and other impurities. This process is commonly used in construction, manufacturing, and repair applications due to its efficiency and effectiveness.
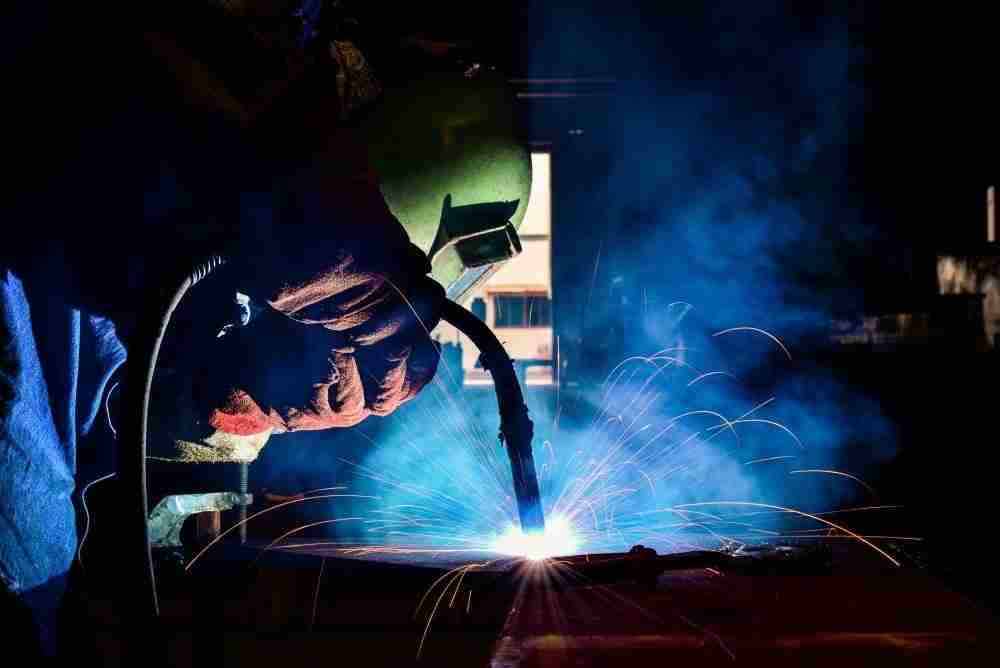
History of Self-Shielded Flux Cored Welding
Its history dates back to the early 1950s when the process was developed by the Lincoln Electric Company. At the time, the company was seeking to develop a welding process that could be used in outdoor and windy environments, where traditional welding methods were difficult to use. The process gained popularity in the 1960s when it was used to build offshore oil rigs and pipelines, as well as in shipbuilding and bridge construction.
Advantages of Self-Shielded Flux Cored Welding
Higher Deposition Rates
This process has a higher deposition rate than many other welding processes. This means that it can weld more metal in less time. This is because the flux inside the electrode creates a shielding gas that protects the weld pool from impurities, allowing the welding operator to increase the wire feed speed.
Better Penetration
This process has better penetration than many other welding processes. The flux inside the electrode creates a high-temperature environment that promotes deeper penetration into the base metal. This is particularly useful when welding thicker materials.
Less Sensitivity to Wind and Drafts
It is less sensitive to wind and drafts than many other welding processes. The flux inside the electrode creates a shielding gas that protects the weld pool from impurities, even in windy or drafty environments. This makes it an ideal process for outdoor welding applications.
Reduced Need for Shielding Gas
This process does not require an external shielding gas, which reduces the need for additional equipment and simplifies the welding process. This makes it a cost-effective alternative to other welding processes that require shielding gas.
Disadvantages of Self-Shielded Flux Cored Welding
Higher Levels of Spatter
Self-Shielded Flux Cored Welding produces higher levels of spatter than some other welding processes. Spatter is the small bits of molten metal that fly off the weld pool during the welding process. While spatter is normal in any welding process, the levels of spatter produced by Self-Shielded Flux Cored Welding can be higher than desired. This can create a safety hazard for welding operators and can also increase cleanup time.
Limited Positional Welding Capabilities
This process has limited positional welding capabilities. This means that it is more difficult to use for welding in vertical and overhead positions. This is because the slag created by the flux can run down the weld pool and create defects in the weld.
Reduced Weld Quality in Some Situations
While This process is an effective welding process for many applications, it may not produce the best weld quality in some situations. For example, it may not be the best option for welding thinner materials or for applications where a high-quality appearance is required. In these situations, other welding processes may be more suitable.
Applications of Self-Shielded Flux Cored Welding
Structural steel fabrication
Self-Shielded Flux Cored Welding is commonly used in structural steel fabrication, such as building construction, bridges, and industrial structures. The high deposition rates and better penetration make it an ideal process for welding thicker materials and completing large-scale welding projects.
Pipeline welding
Self-Shielded Flux Cored Welding is also commonly used in pipeline welding applications. This is because it is an efficient process that can weld long lengths of pipe quickly. Additionally, the reduced need for shielding gas makes it easier to weld in remote locations where access to shielding gas may be limited.
Repair and Maintenance Welding
Self-Shielded Flux Cored Welding is often used for repair and maintenance welding applications. This is because it is a versatile process that can be used to weld a wide range of materials, including carbon steel, low-alloy steel, and stainless steel. The high deposition rates and better penetration also make it an efficient process for completing repairs quickly.
Techniques for Self-Shielded Flux Cored Welding
Preparation of base metal
Proper preparation of the base metal is critical for achieving high-quality welds. The base metal must be clean and free from contaminants such as rust, oil, and grease. Any surface contaminants can result in porosity, reduced weld quality, and weld defects. Additionally, the base metal must be properly fit-up and aligned to ensure proper weld penetration and prevent weld defects.
Selection of Welding Parameters
The selection of welding parameters such as voltage, amperage, and wire feed speed is critical for achieving a high-quality weld. The appropriate welding parameters will depend on the thickness and type of material being welded, the joint design, and the welding position. Welding parameters must be set correctly to ensure proper penetration and fusion between the base metal and the filler material.
Joint Design
The joint design is also important in Self-Shielded Flux Cored Welding. The joint must be properly designed to ensure proper penetration and fusion between the base metal and the filler material. The joint design will depend on the application and the thickness of the base metal. Butt joints, lap joints, and T-joints are some of the common joint designs used in this process.
Welding Techniques
There are different welding techniques that can be used in Self-Shielded Flux Cored Welding. One of the most common techniques is the drag technique, where the welding gun is dragged along the joint in a straight line. Another technique is the weave technique, where the welding gun is moved back and forth across the joint. The appropriate welding technique will depend on the application, the thickness of the base metal, and the joint design.
Equipment and Materials for Self-Shielded Flux Cored Welding
Welding machines
The welding machine is the primary equipment needed for Self-Shielded Flux Cored Welding. The machine must be capable of providing the appropriate voltage, amperage, and wire feed speed to achieve high-quality welds.
Wire Feeders
Wire feeders are used to feed the self-shielded flux cored wire through the welding gun. The wire feeder must be compatible with the welding machine and capable of providing consistent wire feed to ensure consistent weld quality.
Welding Guns
Welding guns are used to direct the self-shielded flux cored wire to the weld joint. The welding gun must be compatible with the wire feeder and the welding machine and be able to withstand the high temperatures and pressures involved in welding.
Self-Shielded Flux Cored Wires
Self-shielded flux cored wires are the primary consumable material used in Self-Shielded Flux Cored Welding. These wires have a flux core that provides shielding gas and flux to the weld puddle, eliminating the need for external shielding gas. The wires are available in a range of sizes and compositions to suit different welding applications.
Personal Protective Equipment (PPE)
Welding operators must wear appropriate personal protective equipment to protect themselves from the hazards associated with welding. This includes welding helmets, gloves, aprons, and boots. Additionally, welding operators must ensure that they work in a well-ventilated area to avoid inhaling welding fumes.
FAQs
Is flux core the same as self-shielded?
Flux core welding is a type of welding that uses a continuous hollow wire electrode that is filled with flux. The flux serves as a shielding gas to protect the weld from atmospheric contamination. Self-shielded welding is a type of flux core welding where the flux core of the wire produces its own shielding gas, eliminating the need for an external shielding gas.
What are self-shielded FCAW electrodes used for?
Self-shielded FCAW (Flux Cored Arc Welding) electrodes are commonly used for welding in outdoor and windy conditions where the use of an external shielding gas is not practical. They are also used in welding thicker materials and in applications where high deposition rates are required.
What is one advantage of the self-shielded FCAW process?
One advantage of the self-shielded FCAW process is that it eliminates the need for an external shielding gas, which can save time and money in terms of setup and operating costs.
What is SMAW vs FCAW welding?
SMAW (Shielded Metal Arc Welding), also known as stick welding, uses a consumable electrode coated in flux to create a shielded arc between the electrode and the base metal. FCAW (Flux Cored Arc Welding) is a type of welding that uses a continuous hollow wire electrode filled with flux to protect the weld from atmospheric contamination. FCAW can be either self-shielded or dual-shielded (with external shielding gas).
What is self-shielded flux core?
Self-shielded flux core is a type of welding wire that is used in self-shielded FCAW welding. The wire has a hollow core that is filled with flux materials that produce a shielding gas to protect the weld from atmospheric contamination. Self-shielded flux core eliminates the need for an external shielding gas.
What is self-shielded?
Self-shielded refers to a welding process or welding wire that produces its own shielding gas, eliminating the need for an external shielding gas.
Does flux core need gas?
Some types of flux core welding require an external shielding gas to protect the weld from atmospheric contamination. However, self-shielded flux core welding produces its own shielding gas, eliminating the need for an external shielding gas.
What is the difference between self-shielded and dual shielded FCAW wire?
Self-shielded FCAW wire produces its own shielding gas, eliminating the need for an external shielding gas. Dual-shielded FCAW wire uses both a flux core and an external shielding gas to protect the weld from atmospheric contamination. Dual-shielded wire generally produces higher quality welds but requires more setup and operating costs.
What polarity for flux core welding?
Flux core welding can be done with either DC (direct current) electrode positive (DCEP) or DC electrode negative (DCEN) polarity. However, DCEN polarity is generally preferred for flux core welding because it produces deeper penetration and better fusion.
Conclusion
Self-Shielded Flux Cored Welding is a popular welding process that offers a range of advantages over other welding processes. These advantages include higher deposition rates, better penetration, less sensitivity to wind and drafts, and reduced need for shielding gas. However, the process also has some disadvantages, such as higher levels of spatter, limited positional welding capabilities, and reduced weld quality in some situations.