Stick Welding in the Modern Era: Techniques and Innovations
Stick welding, officially known as Shielded Metal Arc Welding (SMAW), has been a cornerstone of the welding industry for decades. While it’s often considered one of the more traditional welding methods, modern technology and techniques have transformed stick welding into a highly versatile and advanced process. Today, it’s not just about striking an arc and melting metal—it’s about precision, efficiency, and adaptability.
Stick welding, is one of the oldest and most reliable welding processes used today. Though its roots trace back to the early 20th century, stick welding remains a preferred method for numerous industrial and field applications. Its versatility and ease of use make it indispensable for many professionals and hobbyists alike. But just because it’s a classic technique doesn’t mean it hasn’t evolved. In recent years, advancements in equipment, consumables, and welding techniques have propelled stick welding into the modern era, making it a cutting-edge process that blends traditional craftsmanship with state-of-the-art technology.
Table of Contents
ToggleA Brief History of Stick Welding: From Inception to Innovation
Stick welding was developed in the early 1900s, revolutionizing metal joining techniques. Before its introduction, metalworkers primarily relied on forge welding, a method that was time-consuming and required great skill. Stick welding changed the game by allowing welders to use a consumable electrode covered in flux, which not only provided a protective gas shield but also helped stabilize the arc, creating a more consistent weld.
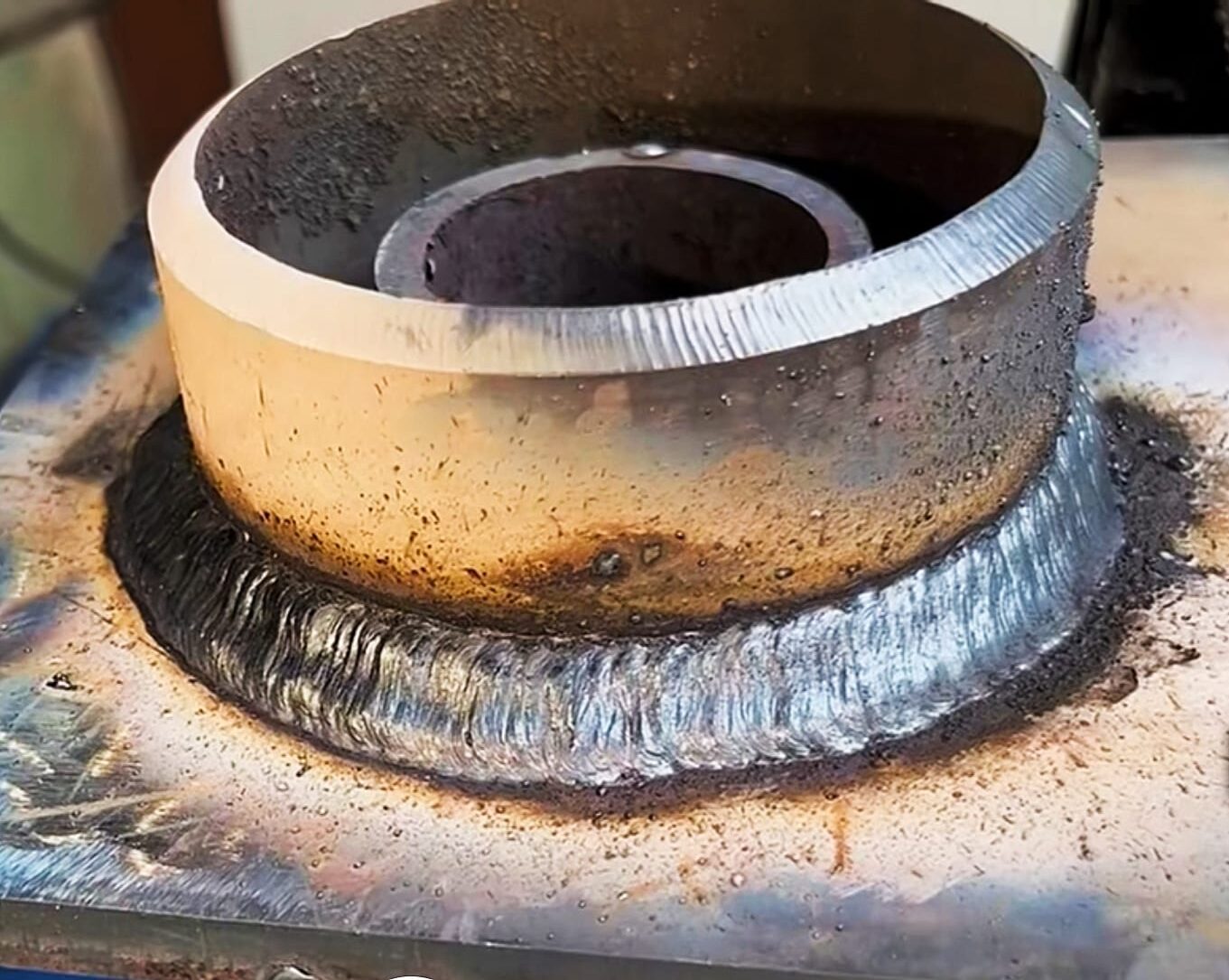
In its early days, stick welding was mainly used for industrial applications such as building bridges, ships, and skyscrapers. Over the years, as technology evolved, stick welding became more accessible, and its use spread to pipeline construction, maintenance work, and even artistic metalworking. Today, despite the rise of newer welding processes like TIG and MIG, stick welding remains widely used due to its versatility, cost-effectiveness, and ability to produce high-quality welds in adverse conditions.
Modern Applications of Stick Welding
Stick welding’s flexibility makes it suitable for a broad range of applications. Here’s where it shines today:
a. Construction and Infrastructure
Stick welding is ideal for heavy-duty construction projects, including structural steelwork, pipelines, and building frames. It’s commonly used for welding beams, columns, and other structural components. The process’s portability and ability to weld in various positions make it perfect for on-site work, especially in remote areas where other welding setups might be impractical.
b. Pipe Welding
One of the most critical uses of stick welding is in pipeline construction and repair. The process is particularly valued for its ability to produce sound welds in difficult positions, such as overhead or vertical, which are common in pipework. The high penetration and deep fusion characteristics of stick welding ensure strong, leak-proof joints that are crucial for pipelines carrying oil, gas, or water.
c. Maintenance and Repair
Stick welding is often used in maintenance and repair work due to its portability and minimal equipment requirements. Whether it’s fixing farm equipment, repairing a trailer, or maintaining machinery in a factory, stick welding is favored for its ruggedness and reliability.
d. Shipbuilding and Marine Applications
In shipyards, stick welding is commonly used for joining thick steel plates in shipbuilding. Its ability to produce strong, durable welds in challenging conditions, such as windy or wet environments, makes it a go-to choice for marine applications.
e. Art and Sculpture
Beyond industrial use, stick welding has also found a place in artistic metalworking. Sculptors use the process to create large-scale metal sculptures, where the aesthetic of the weld bead and the ability to join dissimilar metals play a key role.
Equipment Evolution: Stick Welding Enters the Modern Age
The core components of stick welding—power sources, electrodes, and holders—have evolved significantly over the years. Modern stick welding equipment is designed to enhance efficiency, precision, and ease of use, making it accessible to both experienced welders and novices.
a. Advanced Inverter Power Sources
Traditional stick welding machines were bulky and relied on transformer-based technology, which made them heavy and difficult to transport. Today, inverter technology has revolutionized stick welding power sources. Inverter-based machines are lightweight, compact, and offer greater control over the welding arc. They provide features such as adjustable arc force, hot start, and anti-stick functions, which help improve the quality of the weld and reduce spatter.
The increased efficiency of inverters also means less power consumption and the ability to run on lower voltages, making them ideal for fieldwork or areas with unstable power supplies. Some of the latest models even include digital displays and programmable settings, allowing welders to fine-tune parameters for specific materials and electrode types.
b. Digital Welding Helmets
The development of digital welding helmets has significantly improved the safety and comfort of welders. Modern helmets come with auto-darkening filters that automatically adjust to changes in arc intensity, protecting the welder’s eyes while allowing for better visibility of the workpiece. These helmets also offer features like variable shade levels, sensitivity adjustments, and delay controls, making them suitable for a range of welding processes, including stick welding.
c. State-of-the-Art Electrode Technology
Electrode technology has also advanced, with manufacturers developing electrodes designed for specific materials and conditions. Low-hydrogen electrodes, for example, reduce the risk of cracking in high-strength steels, while special alloy electrodes are used for welding dissimilar metals. Modern coatings on electrodes have improved arc stability and reduced spatter, resulting in cleaner, smoother welds.
The Science Behind Modern Stick Welding
Stick welding may seem straightforward, but mastering it requires a deep understanding of arc physics, electrode selection, and proper technique. The following state-of-the-art techniques can help welders achieve high-quality results in a variety of situations.
a. Advanced Arc Control Techniques
Modern stick welders are equipped with features like adjustable arc force and hot start. Understanding how to use these controls can significantly impact weld quality:
- Arc Force (Dig Control): Arc force control adjusts the intensity of the arc when the electrode comes close to the workpiece. Increasing the arc force can prevent the electrode from sticking, especially when working in tight spaces or performing root passes in pipe welding.
- Hot Start: This function provides a brief surge of current at the start of the weld to improve arc initiation. It’s especially useful when working with difficult-to-start electrodes or on rusty or dirty surfaces.
Mastering these controls allows welders to achieve stable arcs, reduce spatter, and produce consistent weld beads.
b. Electrode Manipulation: Stringers vs. Weaves
The way an electrode is manipulated can have a significant impact on the final weld. Modern welders are experimenting with various techniques to optimize bead appearance, penetration, and heat input:
- Stringer Beads: Stringer beads are narrow and typically used for root passes or when welding thinner materials. They produce less heat, minimizing distortion.
- Weave Patterns: Weave beads, which involve moving the electrode side to side, are used for wider joints or when more metal needs to be deposited. However, modern practice often discourages excessive weaving, as it can lead to overheating and a weaker weld.
c. Using Pulse Stick Welding
While pulse welding is more commonly associated with TIG or MIG processes, some modern stick welding machines offer pulse features. Pulsing allows the welder to control heat input more effectively, resulting in deeper penetration with less risk of burn-through. This technique is particularly useful for thin materials or for achieving a smoother bead profile in aesthetic applications.
d. Weld Positioning and Techniques
Stick welding can be performed in various positions: flat, horizontal, vertical, and overhead. Each position requires different techniques to control the weld puddle and prevent defects:
- Flat Position: This is the easiest position for stick welding, allowing gravity to assist in forming a smooth, even bead.
- Vertical Position: Welding vertically, either up or down, requires more skill. Vertical-up welding is preferred for thicker materials as it provides better penetration, while vertical-down is faster and suitable for thin materials.
- Overhead Position: Overhead welding is challenging due to the risk of molten metal dripping. Modern anti-spatter electrodes and low-splash techniques have made overhead stick welding more manageable.
Innovations in Stick Welding Consumables and Filler Materials
Modern stick welding electrodes are engineered for specific applications, allowing welders to tackle a broader range of projects with greater precision and reliability. Let’s look at some of the latest innovations:
a. Low-Hydrogen Electrodes
Low-hydrogen electrodes (classified as “H4” or “H8” in AWS standards) are designed to minimize the risk of hydrogen-induced cracking. They are especially valuable when welding high-strength steels or in applications where weld integrity is critical, such as pressure vessels and pipelines.
These electrodes have moisture-resistant coatings that prevent hydrogen absorption, making them more stable and reliable, even in humid conditions.
b. Specialized Alloy Electrodes
For applications involving dissimilar metals or specific alloys, manufacturers have developed electrodes with tailored compositions. For example, nickel-based electrodes are used for welding stainless steel to carbon steel, while cobalt-based electrodes are used in high-temperature applications.
Specialized electrodes like these have enabled stick welding to be used in areas traditionally dominated by TIG or MIG welding, such as high-precision aerospace components.
c. Flux Improvements for Cleaner Welds
Modern flux formulations have been optimized to produce cleaner welds with less slag. Some electrodes are designed with fast-freezing flux, which solidifies quickly, making them ideal for vertical or overhead positions. Others have slow-freezing flux that allows for better control and bead shaping, particularly in flat and horizontal positions.
Safety Considerations in Modern Stick Welding
Safety remains a top priority in any welding environment, but modern technology and best practices have made stick welding safer and more comfortable than ever before. Advances in personal protective equipment (PPE), ventilation systems, and safety protocols ensure that welders are protected from common hazards like electric shock, fumes, and burns. In this section, we’ll explore state-of-the-art safety equipment and techniques that have become essential for professional and hobbyist welders alike.
a. Personal Protective Equipment (PPE) Innovations
The right PPE is crucial for protecting welders from a variety of hazards, including ultraviolet (UV) and infrared radiation, flying sparks, and fumes. Modern PPE has evolved significantly, offering enhanced protection and comfort:
- Auto-Darkening Helmets: Today’s auto-darkening helmets feature high-definition lenses, digital controls, and multiple shade settings. These helmets respond almost instantly to changes in light intensity, protecting the welder’s eyes while allowing for better visibility of the workpiece during setup. Some models even include Bluetooth connectivity, enabling welders to adjust settings without removing the helmet.
- Breathable Flame-Resistant Clothing: Modern flame-resistant (FR) clothing is made from lightweight, breathable fabrics that provide excellent protection without sacrificing comfort. Some advanced materials include built-in moisture-wicking properties to keep welders cool in hot environments.
- Powered Air-Purifying Respirators (PAPRs): Welders are exposed to potentially harmful fumes, especially when welding certain materials like galvanized steel or stainless steel. PAPRs, which provide a constant supply of filtered air, have become a standard for protecting welders’ respiratory health. They often integrate with welding helmets, offering comprehensive protection.
b. Improved Ventilation and Fume Extraction
In enclosed or poorly ventilated spaces, welding fumes can pose a serious health risk. Modern fume extraction systems are designed to capture and filter fumes at the source, significantly reducing exposure. Some advanced systems use high-efficiency particulate air (HEPA) filters to capture even the smallest particles, while portable units allow for flexibility in various welding environments.
For large-scale industrial settings, centralized ventilation systems are equipped with intelligent controls that monitor air quality in real time and adjust airflow accordingly, ensuring a safe and comfortable work environment.
c. Electric Shock Prevention
Electric shock is a major risk in stick welding, as the process involves high currents and direct contact with live circuits. To mitigate this risk, modern welding machines are equipped with features like:
- Voltage Reduction Devices (VRD): VRD reduces the open-circuit voltage when the welder is not actively welding, minimizing the risk of electric shock.
- Insulated Electrode Holders: High-quality electrode holders now come with insulated grips and ergonomic designs that improve safety and reduce fatigue.
Modern Stick Welding Techniques: Achieving Perfection
Mastering stick welding requires a combination of skill, knowledge, and experience. In this section, we’ll delve into advanced techniques that help welders achieve high-quality results consistently. Whether you’re welding in challenging positions or dealing with complex joint geometries, these techniques will elevate your craft.
a. Mastering the Start and Stop: Reducing Crater Cracks
One of the common challenges in stick welding is dealing with crater cracks at the end of a weld. When the arc is broken abruptly, the weld puddle can shrink too quickly, leading to a small crack at the end of the bead. Modern welders use a technique known as the “backstep method” to prevent this:
- Backstep Method: As you finish the weld, briefly move the electrode back into the weld bead before lifting it away. This reduces the size of the molten puddle gradually, allowing it to solidify evenly and preventing cracking.
Additionally, some advanced stick welding machines have a “crater fill” function that automatically reduces current at the end of the weld, minimizing the risk of defects.
b. Controlling Distortion: Tack Welds and Sequencing
Distortion is a common issue in stick welding, especially when working with thin materials or long joints. Modern welders use a combination of tack welds and controlled weld sequencing to manage heat input and minimize warping:
- Tack Welds: Place small tack welds along the joint before performing the full weld. These tacks help hold the pieces in place and reduce movement due to heat expansion.
- Weld Sequencing: Instead of welding the entire joint in one go, break it up into smaller sections and alternate between different areas. This allows the metal to cool between passes, reducing overall heat input.
c. Advanced Electrode Manipulation Techniques
Controlling the movement of the electrode is key to producing a high-quality weld. Modern stick welders use a variety of manipulation patterns to control the shape and penetration of the weld:
- Circular Pattern: Move the electrode in small circles to increase penetration and reduce spatter. This pattern is ideal for root passes in pipe welding.
- Zig-Zag Weave: Use a side-to-side zig-zag motion to produce a wider bead. This pattern is useful for filling larger gaps or welding in vertical positions.
- Whip and Pause: For thin materials, quickly whip the electrode forward and then pause briefly before moving again. This technique reduces heat input, preventing burn-through and warping.
Digital Transformation: Smart Welding Systems
The integration of digital technology has transformed stick welding into a highly controllable and efficient process. Smart welding systems are equipped with sensors, software, and connectivity features that enable welders to monitor and optimize their performance in real-time.
a. Intelligent Arc Control
Modern welding machines use microprocessors to analyze and adjust arc characteristics on the fly. This results in a more stable arc, reduced spatter, and improved penetration. Some systems even have adaptive controls that automatically adjust parameters based on the welder’s technique and material properties.
b. Data Logging and Performance Analysis
Smart welders can record detailed information about each weld, including arc length, voltage, and heat input. This data can be reviewed later to identify areas for improvement and ensure consistency across multiple welds. In industrial settings, data logging is used to verify weld quality and compliance with industry standards.
c. Remote Monitoring and Control
Some advanced stick welding systems can be controlled remotely via mobile apps or computer software. This allows supervisors to monitor weld quality, adjust parameters, and troubleshoot issues from a distance. In large-scale projects, remote monitoring can significantly improve productivity and reduce downtime.
9. Stick Welding in Harsh Environments: Modern Solutions
One of the main advantages of stick welding is its ability to perform well in challenging environments, such as windy, wet, or dirty conditions. Modern solutions have enhanced this capability, making stick welding more reliable than ever.
a. Wind-Resistant Techniques
Wind can blow away the protective shielding gases used in other welding processes, leading to porosity and weak welds. However, stick welding uses a flux coating that generates its own shielding gas, making it more resistant to wind. Modern electrodes have improved flux compositions that produce a denser shielding gas, offering even greater protection in windy conditions.
b. Moisture-Resistant Electrodes
Moisture is the enemy of stick welding, as it can lead to hydrogen-induced cracking. Today’s low-hydrogen electrodes are designed with moisture-resistant coatings that prevent water absorption, even in humid or rainy environments. Some electrodes are vacuum-packed to maintain their low-hydrogen properties until they are ready to use.
The Future of Stick Welding: Trends and Predictions
As technology continues to advance, the future of stick welding looks bright. Here are some trends and innovations that are set to shape the next generation of stick welding:
a. Automation and Robotics
While stick welding has traditionally been a manual process, advancements in robotics and automation are making it possible to automate certain aspects of stick welding. Robotic arms equipped with intelligent sensors can perform complex welds with high precision, reducing human error and increasing productivity.
b. Integration with Augmented Reality (AR)
AR is being used to train new welders and assist experienced welders in complex tasks. AR welding helmets can overlay digital information onto the real-world view, showing welders exactly where to place the electrode and how to move it for optimal results.
c. Sustainable Welding Practices
As the industry focuses on sustainability, modern stick welding is incorporating greener practices. Low-emission electrodes, energy-efficient inverters, and improved fume extraction systems are helping reduce the environmental impact of welding.
Conclusion
Stick welding has come a long way since its inception, evolving from a rudimentary process into a sophisticated, high-tech technique that blends tradition with innovation. From state-of-the-art equipment to advanced welding techniques, the modern welder has a wealth of tools and knowledge at their disposal. As technology continues to advance, stick welding will remain a vital part of the welding landscape, offering unparalleled versatility and reliability for the next generation of metalworkers.
Whether you’re a seasoned professional or just starting out, embracing the modern advancements in stick welding will not only improve your weld quality but also open up new possibilities in your welding journey.