Weld Decay: Cause and Cure
Weld decay is a critical issue in the welding world, especially for materials like stainless steel. This phenomenon occurs when welded areas lose their corrosion resistance, leading to potential structural failures. But why is this problem so significant? Weld decay isn’t just an occasional nuisance; it can cause catastrophic failures in industries where safety and durability are paramount, such as chemical processing and food production. Understanding what weld decay is and how to manage it can save you from costly repairs and potential hazards.
What is Weld Decay?
Weld decay refers to the corrosion and weakening of a welded joint or heat-affected zone (HAZ) due to the formation of chromium carbides along the grain boundaries. Chromium is the key element that provides stainless steel with its corrosion-resistant properties. However, during welding, the heat can cause chromium to react with carbon in the steel, forming chromium carbides.
This reaction depletes the amount of chromium available to form a protective oxide layer on the steel surface, leaving the material susceptible to corrosion. Factors like prolonged exposure to high temperatures, improper cooling, and welding techniques contribute to this issue.
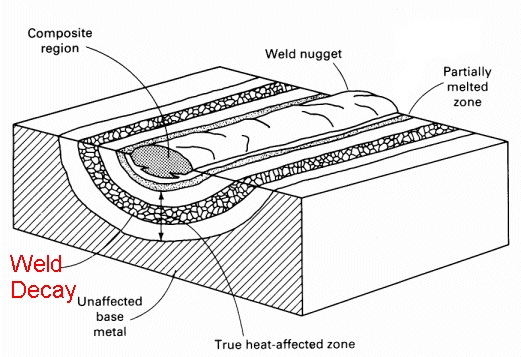
Types of Weld Decay
Sensitization Weld Decay
This type of weld decay occurs when stainless steel is exposed to temperatures between 425°C and 815°C during welding. At this temperature range, chromium combines with carbon to form chromium carbides at the grain boundaries. The affected material becomes “sensitized,” meaning it’s more vulnerable to corrosive environments. You’ll often see this in environments where the metal is exposed to corrosive chemicals or water.
Intergranular Corrosion
Intergranular corrosion specifically targets the grain boundaries of the metal while leaving the grains themselves relatively unaffected. This selective corrosion can severely weaken the metal’s internal structure, leading to cracks and eventual failure. Unlike general corrosion, intergranular corrosion can be hard to detect until it’s too late, as it doesn’t always manifest visibly on the surface.
Materials Susceptible to Weld Decay
Not all metals are equally prone to weld decay.
Stainless Steels
Stainless steels, particularly the 300 series (like 304 and 316), are most vulnerable. These grades contain high levels of chromium, which, while excellent for corrosion resistance, also makes them susceptible to chromium carbide formation during welding.
Nickel-based Alloys
Nickel-based alloys, although more resistant to corrosion than stainless steels, can also experience weld decay under certain conditions. The presence of chromium in these alloys means they too are at risk when exposed to high welding temperatures without proper precautions.
The Science Behind Weld Decay
Role of Chromium Carbides
Chromium, when exposed to carbon at high temperatures, forms chromium carbides. These carbides tend to precipitate at grain boundaries, effectively “stealing” chromium from the surrounding metal. This depletes the chromium content needed to form a protective oxide layer, leaving the metal vulnerable to corrosion.
Grain Boundary Weakening
The formation of carbides at grain boundaries weakens the metal’s structural integrity. These grain boundaries become the metal’s weak points, making it prone to cracking under mechanical stress. This is particularly dangerous in applications like pressure vessels, where even minor weaknesses can lead to catastrophic failure.
Effects of Weld Decay on Welded Structures
Loss of Corrosion Resistance
The primary effect of weld decay is a significant reduction in corrosion resistance. This can lead to localized corrosion at the grain boundaries, which, over time, compromises the entire structure.
Mechanical Failures
Weakened grain boundaries can result in cracking, especially when the material is subjected to stress, vibration, or pressure. This is why weld decay is a major concern in industries like oil and gas, where structural integrity is non-negotiable.
How to Detect Weld Decay
Visual Inspection Techniques
While visual inspection is the simplest method, it’s not always reliable. Signs like discoloration, pitting, or cracking may indicate weld decay, but these are often late-stage symptoms.
Advanced Testing Methods
For a more accurate diagnosis, advanced methods like ultrasonic testing, X-ray analysis, and chemical testing are used. These techniques can detect chromium depletion and intergranular corrosion, even if there are no visible signs.
Preventing Weld Decay
Proper Material Selection
One of the best ways to prevent weld decay is to choose the right materials. Low-carbon stainless steels (e.g., 304L or 316L) or stabilized grades (e.g., 321 or 347) are less prone to carbide formation.
Post-Weld Heat Treatments
Heat treatments such as annealing can dissolve chromium carbides, restoring the material’s corrosion resistance. This is especially important for parts exposed to corrosive environments.
Welding Techniques and Practices
Using controlled welding techniques, such as minimizing heat input and rapid cooling, can reduce the risk of sensitization. Additionally, ensuring proper shielding gas coverage prevents contamination during welding.
Repairing Weld Decay
When to Repair vs. Replace
Deciding whether to repair or replace a weld affected by decay depends on the extent of the damage. Minor cases can often be repaired, while severe decay may require complete replacement of the affected section.
Common Repair Methods
Grinding out the affected area and re-welding it using proper techniques is a common repair strategy. Heat treatments post-repair can further improve the material’s integrity and resistance.
FAQs
What is the primary cause of weld decay?
The main cause is the formation of chromium carbides during welding, which depletes chromium from grain boundaries and reduces corrosion resistance.
Can weld decay occur in non-stainless steels?
While it’s less common, certain high-carbon steels and nickel-based alloys can also experience weld decay.
How do you test for weld decay?
Methods like ultrasonic testing, X-ray analysis, and chemical tests can detect weld decay effectively.
Is it possible to reverse weld decay?
In some cases, post-weld heat treatments can dissolve chromium carbides and restore the metal’s properties.
What industries are most affected by weld decay?
Industries such as chemical processing, oil and gas, and food production are most impacted due to their reliance on stainless steel.
Conclusion
Weld decay is a hidden but serious threat to the durability and safety of welded structures. By understanding its causes, effects, and prevention methods, welders can take proactive measures to protect their projects. Whether you’re working on industrial pipelines or smaller-scale applications, managing weld decay is crucial for ensuring long-term reliability and safety.