Weld Distortion – Causes and Remedies
Introduction
Weld distortion refers to the undesirable changes in the shape and dimensions of a welded structure or component that occur as a result of the welding process. During welding, the application of heat and the subsequent cooling cause localized expansion and contraction of the material, leading to the deformation of the welded joint. Weld distortion can manifest in various forms, such as longitudinal shrinkage, transverse shrinkage, and angular distortion, among others.
Understanding weld distortion is crucial for several reasons. Firstly, excessive distortion can result in dimensional inaccuracies and compromise the overall structural integrity of welded components. It can lead to fit-up issues, misalignments, and gaps, making subsequent assembly or welding operations more challenging. Moreover, distortion can cause stress concentrations, which may contribute to premature failure or fatigue of the welded structure. By comprehending the causes and remedies for weld distortion, engineers and welders can implement effective mitigation strategies to minimize its detrimental effects and ensure the quality and reliability of welded joints. This outline aims to provide a comprehensive understanding of weld distortion, its causes, and potential remedies.
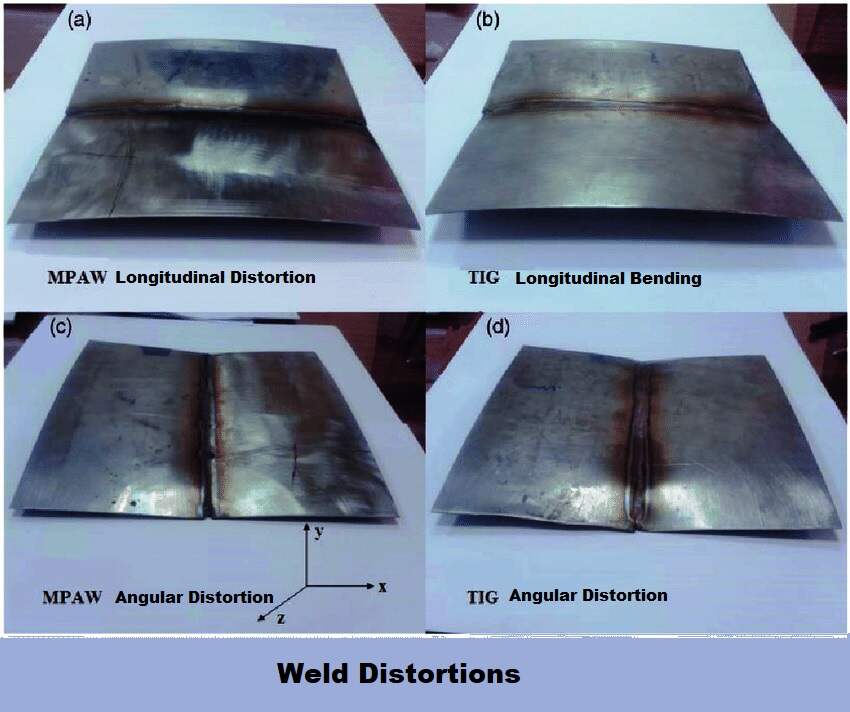
Causes of Weld Distortion
Thermal expansion and contraction
Introduction to thermal stresses during welding:
- Welding involves localized heating of the material, causing it to expand.
- Upon cooling, the heated region contracts, leading to residual stresses and distortion.
- The rate and magnitude of expansion and contraction depend on the material properties and welding conditions.
Effects of temperature gradients on metal properties:
- During welding, temperature gradients form across the welded joint.
- Non-uniform heating and cooling induce varying thermal expansion and contraction rates in different regions.
- This differential movement generates internal stresses, contributing to distortion.
- The mismatch between the coefficients of thermal expansion of base metal and filler material exacerbates distortion.
Residual stresses
Overview of residual stresses in welded joints:
- Residual stresses arise from the unequal distribution of stresses within a welded joint.
- They exist even when no external loads are applied and can significantly influence distortion.
- Residual stresses can be tensile or compressive and may accumulate in different regions of the weld.
Factors contributing to residual stresses:
- Non-uniform heating and cooling rates lead to non-uniform residual stresses.
- Welding process parameters, such as heat input and cooling rate, affect the magnitude of residual stresses.
- Joint design, material properties, and welding technique also influence the level of residual stresses.
- Inadequate weld preparation, such as poor fit-up or excessive gap, can exacerbate residual stresses and subsequent distortion.
Metallurgical changes
Phase transformations and their impact on distortion:
- High temperatures during welding can induce phase transformations in the material.
- Phase changes, such as solidification, can cause volume changes, leading to distortion.
- Martensitic transformations in certain alloys can result in significant distortion due to their volume expansion or contraction.
Microstructural changes affecting distortion:
- Welding alters the microstructure of the base metal and the heat-affected zone (HAZ).
- Changes in grain structure, grain growth, and metallurgical phase changes can influence distortion.
- Variations in material properties, such as hardness and ductility, across the weld joint can contribute to distortion.
Types of Weld Distortion
Longitudinal shrinkage
Definition and causes:
- Longitudinal shrinkage refers to the contraction or shortening of the welded joint in the direction parallel to the weld axis.
- It occurs due to the non-uniform cooling and solidification of the weld metal, resulting in volume reduction.
- Longitudinal shrinkage is influenced by factors such as weld length, welding process parameters, and material properties.
Examples of longitudinal shrinkage distortion:
- Welded plates or beams may experience longitudinal shrinkage, causing them to warp or bend.
- In butt joint welds, the contraction of the weld metal can pull the base metal towards the weld, resulting in a concave or “dished” shape.
- Longitudinal shrinkage can lead to misalignment or dimensional deviations in structures with multiple welds, such as pipelines or pressure vessels.
Transverse shrinkage
Definition and causes:
- Transverse shrinkage refers to the contraction or narrowing of the welded joint perpendicular to the weld axis.
- It occurs due to the lateral or sideways movement of the weld metal during cooling and solidification.
- Transverse shrinkage is influenced by factors such as weld width, material properties, and weld pool shape.
Examples of transverse shrinkage distortion:
- In fillet welds, the transverse shrinkage can cause the weld to “pull” or move towards one side, resulting in an uneven or off-centered joint.
- Transverse shrinkage can lead to distortion in welded components such as frames, brackets, or sheet metal structures.
- Distortion in welded corners, such as box or T-joints, is often characterized by angular misalignment due to combined longitudinal and transverse shrinkage effects.
Angular distortion
Definition and causes:
- Angular distortion refers to the change in angle or rotation of the welded joint relative to its initial position.
- It occurs due to the non-uniform contraction and cooling of different regions within the weld joint.
- Angular distortion is influenced by factors such as joint configuration, welding sequence, and material properties.
Examples of angular distortion:
- Welded pipes or tubes can experience angular distortion, resulting in deviations from straightness or circularity.
- In butt joint welds, the contraction of the weld metal can cause the joint to rotate or tilt, leading to angular misalignment.
- Angular distortion can affect the fit-up and assembly of components requiring precise angular positioning, such as structural members or machinery parts.
Remedies for Weld Distortion
Welding technique and process considerations
Proper weld joint preparation:
- Ensuring proper fit-up and alignment of the joint helps minimize distortion.
- Accurate edge preparation, appropriate gap control, and joint geometry optimization are crucial.
- Beveling, chamfering, or using grooves can distribute stresses more evenly, reducing distortion.
Preheating and post-weld heat treatment:
- Preheating the base metal prior to welding reduces temperature differentials and associated distortion.
- Controlled heating helps minimize thermal gradients and promotes uniform cooling.
- Post-weld heat treatment, such as stress relief annealing, can relieve residual stresses, reducing distortion.
Fixturing and clamping techniques
Use of jigs, fixtures, and clamps:
- Employing dedicated jigs, fixtures, and clamps during welding provides proper alignment and restraint.
- These devices help maintain the desired shape and prevent excessive movement during welding and cooling.
- Accurate positioning and rigid support minimize distortion and improve dimensional control.
Mechanical restraint methods:
- External mechanical devices, such as tensioning devices, braces, or external restraints, can counteract distortion.
- Controlled application of forces can counterbalance shrinkage and minimize undesired movement.
- Mechanical restraints should be designed to allow for thermal expansion and contraction while controlling distortion.
Weld sequence and direction
Sequential welding techniques:
- Dividing a large weld into smaller, manageable sections reduces localized heating and cooling effects.
- Gradual progression along the joint minimizes distortion by allowing for uniform stress distribution.
- Strategic welding sequence selection helps control distortion in complex welded structures.
Alternating weld direction:
- Alternating the direction of the weld passes distributes thermal gradients and residual stresses.
- Back-step welding or alternating between sides of the joint can minimize distortion by balancing contraction forces.
- This technique promotes symmetrical cooling and reduces the overall distortion tendency.
Distortion control methods
Welding with the backstep technique:
- The backstep technique involves welding in the reverse direction, starting from the solidified end.
- It counteracts shrinkage forces, redistributes residual stresses, and reduces the overall distortion effect.
- This method can be particularly effective for long welds or thick sections.
Thermal stress relief techniques:
- Post-weld thermal stress relief techniques, such as local heating or controlled cooling, can reduce distortion.
- Stress relief methods aim to relax residual stresses and mitigate distortion by subjecting the weld to specific temperature cycles.
- Care must be taken to avoid inducing new distortion during the stress relief process.
Implementing these remedies and control measures can significantly reduce weld distortion and ensure the dimensional accuracy, structural integrity, and functionality of welded components. The selection and combination of these techniques depend on the specific welding application, material properties, joint configuration, and desired quality requirements.
Real-world Examples
Real-world examples of weld distortion issues:
Example 1: Shipbuilding industry
- Welding large steel plates for ship hulls often results in longitudinal shrinkage distortion.
- The plates may warp or develop a concave shape due to non-uniform cooling and solidification.
Example 2: Automotive manufacturing
- Welding automotive chassis or frame components can lead to angular distortion.
- Misalignment or rotation of the welded joints can occur due to unequal contraction of different sections.
- Analysis of the causes and remedies applied:
Example 1:
- Cause: The high heat input during welding causes rapid cooling and contraction, resulting in longitudinal shrinkage.
- Remedies applied:
- Proper joint preparation: Accurate fit-up and minimized gap help reduce distortion.
- Fixturing and clamping techniques: Use of jigs and fixtures to maintain alignment during welding.
- Sequential welding: Dividing the weld into smaller sections to manage shrinkage forces.
- Analysis: These measures aim to control thermal gradients, minimize residual stresses, and provide restraint.
Example 2:
- Cause: Unequal cooling rates and non-uniform contraction lead to angular distortion.
- Remedies applied:
- Preheating: Uniformly heating the components before welding reduces thermal gradients.
- Welding direction: Alternating the weld direction to balance contraction forces.
- Mechanical restraints: Using braces or tensioning devices to counteract angular misalignment.
- Analysis: These solutions focus on reducing thermal differentials, promoting symmetrical cooling, and providing external support to mitigate distortion.
- Evaluation of the effectiveness of the chosen solutions:
Example 1:
- The combination of proper joint preparation, fixturing techniques, and sequential welding helps minimize longitudinal shrinkage distortion.
- By controlling shrinkage forces and maintaining proper alignment, the distortion can be significantly reduced.
- Evaluation: The chosen solutions effectively address the causes of distortion, resulting in improved weld quality and reduced deformation.
Example 2:
- Preheating, alternating welding direction, and mechanical restraints aim to counteract angular distortion.
- These measures promote uniform cooling, minimize differential contraction, and provide external support.
- Evaluation: The selected remedies help mitigate angular distortion, leading to improved joint alignment and reduced misalignment.
- The evaluation of the chosen solutions in real-world examples demonstrates the effectiveness of implementing appropriate remedies for weld distortion. By understanding the causes and applying the right techniques, engineers and welders can successfully minimize distortion, improve weld quality, and ensure the integrity of welded structures.
FAQs
Which defect in welding is called thermal distortion?
Thermal distortion is not considered a defect in welding but rather a phenomenon that refers to the deformation or changes in shape that occur during welding due to thermal effects.
How many types of distortion are there in welding?
There are three main types of distortion in welding: longitudinal shrinkage, transverse shrinkage, and angular distortion.
What is the meaning of thermal distortion?
Thermal distortion refers to the deformation or changes in shape that occur in a welded joint or structure due to the non-uniform heating and cooling during the welding process.
What is the thermal effect of welding?
The thermal effect of welding refers to the heat generated during the welding process that causes changes in the material, including thermal expansion, phase transformations, and the development of residual stresses.
What are two causes of distortion?
Two causes of distortion in welding are thermal expansion and contraction of the material due to the heat input during welding and the formation of residual stresses in the welded joint.
What are the two types of distortion?
The two main types of distortion in welding are longitudinal shrinkage and transverse shrinkage. Additionally, there is a third type known as angular distortion.
What are the stages of distortion?
Distortion in welding typically occurs in three stages: the initial deformation during the welding process, the intermediate distortion as the joint cools, and the final distortion after the welding process is completed.
What is the thermal effect?
The thermal effect refers to the influence of heat on the material during welding, including changes in temperature, expansion and contraction, and metallurgical transformations.
What is distortion called?
Distortion in welding is the term used to describe the deformation or changes in shape that occur in a welded joint or structure as a result of thermal effects, residual stresses, or other factors.
What is the purpose of distortion?
Distortion in welding is an undesirable effect, and the purpose is to minimize or control it. The goal is to ensure that the welded joint or structure retains its desired shape and dimensional accuracy, thereby maintaining the integrity and functionality of the weld.
Conclusion
In conclusion, weld distortion is a common challenge faced in welding operations. Understanding the causes and implementing effective remedies is crucial for minimizing distortion and ensuring the integrity of welded structures. Throughout this outline, we have explored the various aspects of weld distortion, including its definition, importance, causes, types, and remedies.
Thermal expansion and contraction, residual stresses, and metallurgical changes were identified as primary causes of weld distortion. Longitudinal shrinkage, transverse shrinkage, and angular distortion were discussed as the main types of distortion that can occur during welding.
To address weld distortion, several remedies were outlined. Welding technique and process considerations, such as proper joint preparation, preheating, and post-weld heat treatment, can help control distortion. Fixturing and clamping techniques, as well as careful consideration of weld sequence and direction, contribute to minimizing distortion effects. Distortion control methods, including the backstep technique and thermal stress relief techniques, were also presented as effective measures.
Real-world examples highlighted the occurrence of weld distortion in industries such as shipbuilding and automotive manufacturing. The analysis of causes and remedies applied in these cases demonstrated the practical application of mitigation strategies.