How to Deal With Weld Spatter In Stick Welding
Welding can be an incredibly rewarding skill, but let’s face it—stick welding (also known as Shielded Metal Arc Welding or SMAW) can be messy. Spatter, those annoying metal droplets flying everywhere, can make an otherwise enjoyable job frustrating. But hey, don’t stress it! I’ve got you covered. Today, we’re diving deep into stick welding spatter—why it happens, how to minimize it, and how to make your welds cleaner and stronger.
Understanding Spatter in Stick Welding
What Exactly is Weld Spatter?
Simply put, spatter is those tiny droplets of molten metal that jump from the welding arc, sticking to your workpiece, equipment, and sometimes even your clothes. Not cool, right?
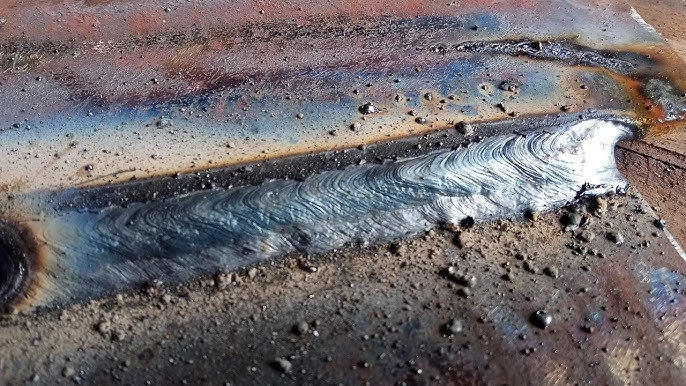
Why is Spatter a Big Deal?
Well, besides ruining your fancy welding jacket, spatter can lead to poor weld quality, weakening the structure you’re working on. Plus, it adds cleanup time and costs money—both of which nobody enjoys.
Common Causes of Spatter in Stick Welding
Incorrect Welding Current
If your amperage is too high, things get hot really quick—too quick. This overheats your electrode, resulting in excessive spatter.
Improper Arc Length
Keep your arc too long, and those droplets will fly like sparks from fireworks. Too short, and you’ll be sticking the rod constantly. It’s all about balance.
Electrode Quality and Condition
Got moisture in your electrode? You’re practically asking for spatter. Electrodes that aren’t properly stored become problematic fast.
Wrong Electrode Selection
Every job has its hero electrode. Choosing the wrong one is like wearing flip-flops in the snow—it won’t end well.
Dirty or Rusty Surface
A dirty workpiece guarantees spatter. Rust, dirt, and oil are your weld’s worst enemies.
Choosing the Right Equipment
Selecting Appropriate Electrodes
Always match your electrode type to your metal and job specifics. Low-hydrogen rods, for example, produce far less spatter than others.
Importance of a Good Welding Machine
An unstable welding machine is like trying to paint a masterpiece during an earthquake. Invest in reliable equipment, and you’ll thank yourself later.
Techniques to Minimize Spatter
Maintain Proper Arc Length
Aim for about the diameter of your electrode. Too long or too short will cause unwanted spatter.
Adjust the Welding Current Correctly
Check your electrode packaging—it’s your cheat sheet. Stay within recommended amperages for smoother welds.
Correct Electrode Angle
Hold your electrode at a consistent 15-30 degree angle. Think of it as gently brushing paint rather than stabbing your metal.
Proper Electrode Storage
Store electrodes in a dry place. Use airtight containers or special ovens to keep moisture away.
Importance of Surface Preparation
Cleaning the Metal Surface
Always clean your workpiece thoroughly. Remove rust, paint, and oils to dramatically reduce spatter.
Removing Rust and Impurities
A quick pass with a grinder or wire brush can save you a ton of headache later. Trust me, a clean weld is a happy weld.
Electrode Types and Their Impact on Spatter
Low-Hydrogen Electrodes
These electrodes, like E7018, are your best buddies when it comes to spatter reduction. They produce smoother arcs and cleaner welds.
Rutile Electrodes
Easy to use but slightly higher in spatter. They’re good, but there’s a trade-off.
Cellulosic Electrodes
Excellent penetration, but high spatter. Use these only when you truly need them.
Advanced Tips and Tricks for Stick Welders
Use of Anti-Spatter Sprays
These sprays create a barrier, preventing spatter from sticking. A quick spray beforehand can save significant cleanup time.
Practicing Consistent Travel Speed
Keep your movements steady and uniform. Speed changes equal spatter. Consistency is key here.
Troubleshooting Common Spatter Issues
Problem: Excessive Current
If your spatter looks like a meteor shower, lower the amperage. It usually solves the issue immediately.
Problem: Erratic Arc
Check your connections and machine settings. Even a slightly loose connection can wreak havoc.
Problem: Moisture in Electrode
Bake or replace damp electrodes. Moisture equals spatter—simple as that.
Benefits of Controlling Spatter in Stick Welding
Increased Weld Quality
Controlling spatter leads to stronger, cleaner welds that look professional.
Reduced Cleanup Time
Less spatter equals less grinding and sanding. Who doesn’t love saving time?
Cost Efficiency
Time is money, and less cleanup means reduced costs overall. Your boss or wallet will thank you.
FAQs
Can too low amperage cause spatter?
Yes, low amperage can cause erratic arcs, leading to increased spatter.
Is it normal to have some spatter in stick welding?
Absolutely! But excessive spatter means something’s off, and it’s time to adjust.
How often should I clean my welding surface to prevent spatter?
Always clean before every weld—it’s worth the extra minute of prep.
Do anti-spatter sprays really work?
Yes, they’re incredibly effective and worth using, especially on detailed or high-visibility jobs.
What’s the best electrode type for minimal spatter?
Low-hydrogen electrodes (E7018) usually offer the cleanest results.
Conclusion
Dealing with spatter in stick welding isn’t rocket science. By choosing the right electrodes, maintaining equipment, using correct techniques, and keeping surfaces clean, you’ll drastically reduce this common nuisance. Practice makes perfect, so keep these tips in mind and you’ll soon master cleaner, professional-quality stick welds.